《年产22.7520万吨的乙烯车间工艺设计》化学工艺学课程设计
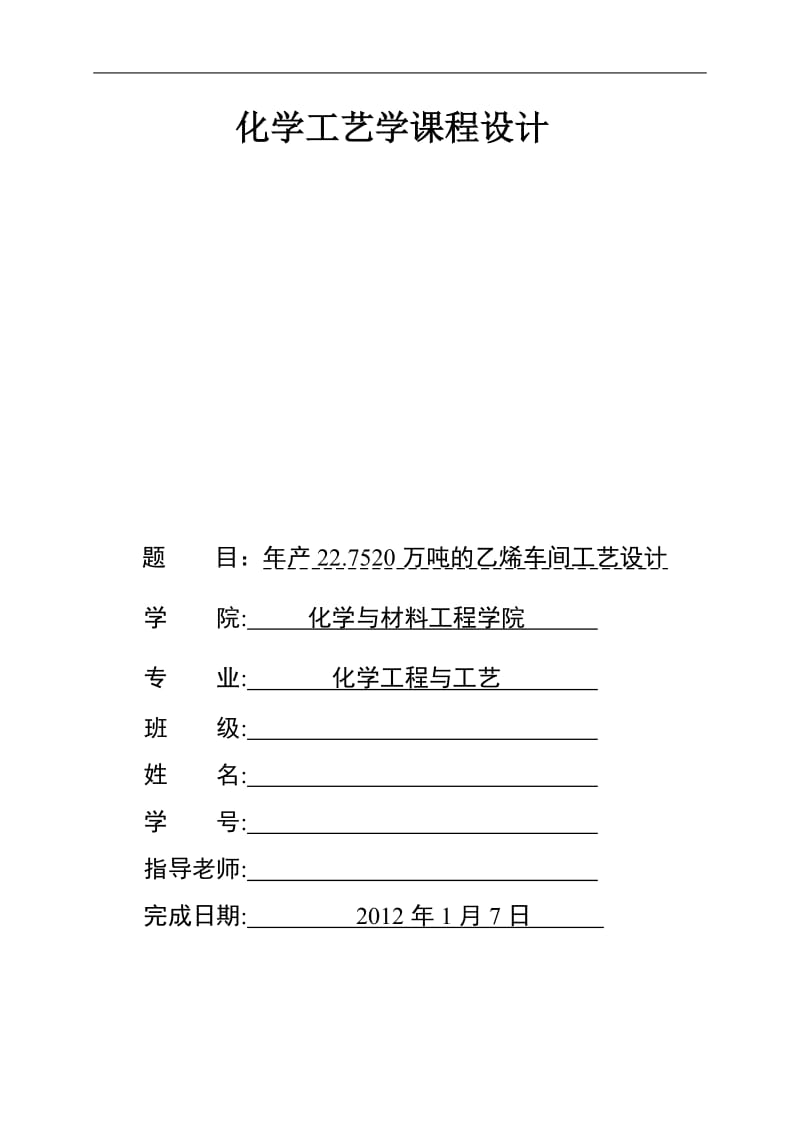


《《年产22.7520万吨的乙烯车间工艺设计》化学工艺学课程设计》由会员分享,可在线阅读,更多相关《《年产22.7520万吨的乙烯车间工艺设计》化学工艺学课程设计(44页珍藏版)》请在装配图网上搜索。
1、温州大学 化学与材料工程学院 化工工艺学课程设计 化学工艺学课程设计 题 目:年产22.7520万吨的乙烯车间工艺设计 学 院: 化学与材料工程学院 专 业: 化学工程与工艺 班 级: 姓 名: 学 号:
2、 指导老师: 完成日期: 2012年1月7日 目录 1、 总论 2 1.1 概述 2 1.2 设计依据及规模 2 1.3 工艺方案 2 2、 工艺设计方案 3 2.1 概述 3 2.2 石脑油裂解工艺现状 3 2.2.1 日本共同研究集团裂解工艺 3 2.2.2 韩国LG石化公司裂解工艺 4 2.2.3 国内传统石脑油蒸汽裂解工艺 4 2.3 石脑油裂解工艺设计确定 8
3、 2.3.1 原料及产品指标 8 2.3.2 催化裂解及预分馏工艺 8 2.3.3 裂解气分离精制工艺 11 3、 物料衡算 12 3.1 概述 12 3.2 物料衡算的原理和基准 12 3.3 物料衡算 12 3.3.1 石脑油裂解预处理物料 12 3.3.2 预处理后裂解气物料 12 4、 热量衡算 14 4.1 工艺流程和热量衡算说明 14 5、 设备选型 15 5.1 反应器设计 15 5.1.1 裂解过程对管式炉的要求 15 5.2 换热器的设计选型 16 5.2.1 概述 16 5.2.2 选型范例 16 5.3 塔设备设计 20 5.3.1 概
4、述 20 5.3.2 塔型选用原则 20 5.3.3 分离塔的设计 21 5.3.4 塔设计结果 34 第一章 总论 1.1概述 随着社会的发展,我国乙烯丙烯的市场需求急剧增加,乙烯丙烯及其下游产品的进口量逐年增加,国内产品市场占有率还不到一半。目前全世界乙烯主要以石脑油(或乙烷)为原料,采用蒸汽热裂解技术(在800℃左右的温度下)生产,其产量超过总产量的90%。 乙烯工业是石油化工的龙头,其发展水平已成为衡量一个国家经济实力的重要标志之一,在石化工业乃至国民经济发展中占有重要地位。聚乙烯得到了广泛应用,如粘合剂、农膜、电线和电缆、包装(食品软包装、
5、拉伸膜、收缩膜、垃圾袋、手提袋、重型包装袋、挤出涂覆)、聚合物加工(旋转成型、注射成型、吹塑成型)。 丙烯是仅次于乙烯的一种重要有机石油化工基本原料,主要用于生产聚丙烯、苯酚、丙酮、丁醇、辛醇、丙烯腈、环氧丙烷、丙二醇、环氧氯丙烷、合成甘油、丙烯酸以及异丙醇等,其他用途还包括烷基化油、高辛烷值汽油调合料等。 (1)丙烯制成聚丙烯,聚丙烯应用在塑制品、薄膜制品、纤维制品; (2)丙烯制成苯酚,苯酚制成木材防腐剂、皮肤科常用的治疗药物、面部美容治疗药物。 1.2设计依据及规模 本设计主要以中国石油化工新建四所石脑油裂解厂为现实基础,根据设计要求石脑油31600kg/h的进料,年产22.7
6、4万吨聚合级乙烯产品。 1.3工艺方案 本设计借鉴中国石油化工股份有限公司的石脑油裂解方式,选用Kellogg公司和日本出光石油化学公司共同开发的一种新型裂解炉——毫秒炉或超短时间炉(USRT炉),蒸汽裂解反应之后对得到的裂解气进行预分馏,最后选用前脱乙烷后加氢的方法进行分离精制得到乙烯、丙烯。 裂解气的分离精制工段现工业应用上也已经非常成熟、高效。裂解气进入分离工段的主要是C1~C5混合气体,混合气体在水洗塔进行水洗,除去有机杂质;再流入碱洗塔中洗去酸性杂质气体;为避免水对之后分离过程的影响,需将气体干燥;干燥后的气体经过压缩、制冷流入脱乙烷塔系统,分离出C3~C5和C2以下产品;C2
7、及以下产品进入脱甲烷塔分离出甲烷和C2产品;C2产品脱炔后进入乙烯精馏塔,分离出聚合级乙烯;C3~C5产品进入脱丙烷塔分离出C3和C4及以上产品,C4及以上产品进入脱丁烷塔得到C4,C3脱炔后进入丙烯精馏塔分离出聚合级丙烯产品。 第二章 工艺设计方案 2.1概述 石脑油制乙烯丙烯主要分为石脑油裂解及预分离工段和裂解气分离工段。 目前全世界乙烯主要以石脑油(或乙烷)为原料,采用蒸汽热裂解技术(在800℃左右的温度下)生产,其产量超过总产量的90%。催化裂解同蒸汽裂解相比,该过程反应温度比标准裂解反应约低50~200℃,因此比普通蒸汽裂解能耗少,裂解炉管内壁结焦速率将会降低,从而可延长
8、操作周期,增加炉管寿命;二氧化碳排放也会降低,并可灵活调整产品结构,可增加乙烯和丙烯的总收率,乙烯生产成本大幅度降低。 2.2石脑油裂解工艺现状 (一)日本共同研究集团裂解工艺 日本通产省工业技术院推进新阳光计划,其中经5年官民集中共同研究的“下世纪化学工艺技术开发”项目中,由日本化学工业协会与工业技术院物质工学工业技术研究所组成的共同研究集团,开发成功了生产乙烯、丙烯的石脑油催化裂解工艺,可实现大幅度节能和降低环境负荷,并可按乙烯、丙烯供需变化灵活控制烯烃生成比例。 共同研究集团(日本化学工业协会方面参加的企业有出光石油化学、东燃化学、日本石油化学、丸善石油化学等)为了证实催化裂解工
9、艺的竞争力,进行了石脑油日处理能力3000t 规模的可行性研究。该工艺采用固定床,因裂解温度下降,可大幅节能,乙烯和丙烯收率60%,大大超过目标值57%。采用这种固定床型催化裂解工艺,不仅可节能20%,减少CO2排放20%,而且由于与现行蒸汽转化炉的结构类似,现行工艺经改造和后续工序作若干改造即可使用, 证实有助于石化产业强化竞争能力,可望实现新工艺的工业化。 石脑油经蒸汽热解生产乙烯、丙烯,其设备大型化和节能工艺开发有一定限度,但为了提高石化产业的国际竞争能力和实现削减CO2排放的中长期目标,能耗占石化工业40%的石脑油裂解炉的节能和削减CO2排放的工艺开发又是最重要的课题。共同研究集团的
10、催化裂解工艺,裂解温度比现行蒸汽裂解的820℃约低100℃。同时,对以沸石为中心的固体酸等催化剂以及烃的催化裂解反应进行了广泛研究。 结果显示,沸石系统负载稀土金属的催化剂,除活性没有降低、烯烃收率高外,还抑制副产芳烃,特别是负载镧的沸石(ZSM-25)催化剂,反应温度650℃(开发目标为750℃),乙烯和丙烯收率61%(开发目标57%),显示良好的裂解特性。另外,乙烯和丙烯组成比0.7,比现行热裂解的丙烯收率高。共同研究集团的催化剂添加10%镧可抑制芳烃生成,从而增加乙烯、丙烯收率。这种催化剂再添加2%的磷,由于担体中氧化铝与磷的相互作用抑制了脱铝,因此反复使用性能不衰减,活性高,寿命长。
11、 (二)韩国LG石化公司裂解工艺 LG石化公司(Seoul)开发了石脑油催化裂解新工艺,与传统的蒸汽裂解工艺相比,该工艺可大大提高烯烃产率。采用该技术可提高乙烯产率20%,提高丙烯产率10%。现有裂解装置稍加改进就可使用这一工艺。 该工艺使用含特定金属氧化物的专用催化剂,工艺过程在比标准的反应温度低50~100℃下操作,因此与常规蒸气裂解相比,耗能大大减少,裂解炉管内结焦速率也将下降,可延长连续运行时间和炉管寿命,同时,CO2排放也较少。 LG公司正在韩国丽川一套30万美元的中型装置上进行试验。该公司在丽川的乙烯生产能力为75万t/a,在2003年使丽川一台裂解炉采用该技术。烯烃产能增
12、加和运行费用的降低,将使年现金流通费用增加约1500万美元。长期以来,人们期望开发工业化催化工艺过程用于石油原料裂解为轻烯烃,并用于甲烷氧化偶联以生产乙烯。 (三)国内传统石脑油蒸汽裂解工艺 早期的管式裂解炉是沿用石油炼制工业的加热炉的结构采用横置裂解炉管的方箱炉。反应管放置在靠墙内壁处,采用长火焰烧嘴加热,炉管表面热强度低,约为85~125MJ/(m2h)。20世纪50年代,裂解炉结构有较大改进,炉管位置由墙壁处移至辐射室中央,并采用短焰侧壁烧嘴加热,提高了炉管表面热强度和受热均匀性。热强度可达210MJ/(m2h)。至60年代,反应管开始由横置式改为直立吊装式,这是管式炉的一次重大技术
13、改进。它采用单排管双面辐射加热,进一步把炉管表面热强度提高到约250MJ/(m2h),并采用多排短焰侧壁烧嘴,以提高反应的径向和轴向温度分布的均匀性。美国鲁姆斯公司短停留时间裂解炉(简称SRT炉)是初期立管式裂解炉的典型装置。现在世界上大型乙烯装置多采用立式裂解反应管。 1、反应炉炉型 目前国际上应用较广的管式裂解炉有短停留时间炉、超选择性炉、林德-西拉斯炉、超短停留时间炉。 (1)短停留时间炉 鲁姆斯公司在60和70年代开发的炉型(SRT),有三种:即SRT-Ⅰ、SRT-1Ⅱ及SRT-Ⅲ型,其中SRT-Ⅱ又可分为高选择性(HS)和高生产能力(HC)两种。SRT-Ⅰ型由等径管组成;SR
14、T-Ⅱ及SRT-Ⅲ则为前细后粗的变径管,四股平行进料以强化前期加热,缩短停留时间和后期降低烃分压,从而提高选择性,增加乙烯产率。由于三种反应管采用了不同的管径及排列方式,其工艺特性差异较大。 SRT型炉是目前世界上大型乙烯装置中应用最多的炉型。中国的燕山石油化工公司,扬子石油化工公司和齐鲁石油化工公司的300kt乙烯生产装置均采用此种裂解炉。 (2)超选择性裂解炉 简称USC炉。它是美国斯通-韦伯斯特公司在70年代开发的一种炉型,炉子的基本结构与SRT炉大体相同,但反应管由多组W型变径管组成,每组四根管,前两根材质为HK-40,后两根为HP-40,全部离心浇铸和内部机械加工平整,管径由小
15、到大,一般为50~83mm,长为10~20m。按照生产能力的要求,每台炉可装16、24或32个管组,裂解产物离开反应管后迅速进入一种专用急冷锅炉(USX),每两组反应管配备一个急冷锅炉。 USC炉的主要技术特性为:①采用多组小口径管并双面辐射加热,炉管比表面较大,加热均匀且热强度高,从而实现了0.3s以下的短停留时间。②采用变径管以降低过程的烃分压。短的停留时间和低的烃分压使裂解反应具有良好的选择性。 USC炉单台炉子乙烯年生产能力可达40kt。中国大庆石油化工总厂以及世界上很多石油化工厂都采用它来生产乙烯及其联产品。 (3)林德-西拉斯裂解炉 简称LSCC炉。是林德公司和西拉斯公司在
16、70年代初合作研制而成的一种炉型。炉子的基本结构与SRT炉相似。炉膛中央吊装构形特殊的反应管,每组反应管是由12根小口径管(前8根组成4对平列管,后4根组成两对平列管)以及4根中口径管(由4根管组成两对平列管)和一根大口径管组成,管径为6~15cm,管总长45~60m。裂解产物离开反应管后立即进入急冷锅炉骤冷。 LSCC炉反应器的特点是原料入口处为小口径管双排双面辐射加热,物料能迅速升温,缩短停留时间,后继的反应管则为单排双面辐射,管径采取逐管增大方式以达到降低烃分压的目的。物料在反应管中的停留时间为0.2~0.4s。短停留时间和低烃分压使裂解反应具有较高的选择性,乙烯产率高。 LSCC裂
17、解炉在工业上得到一定的应用,单台炉的乙烯年产量可达70kt。 (4)超短停留时间裂解炉 简称USRT炉,或称毫秒裂解炉。是美国凯洛格公司和日本出光石油化学公司在70年代末共同开发成功的新型管式裂解炉。炉子由十多根直径约为2.54cm,长约10m的单根直管并联组成。反应管吊在辐射室中央,由底部烧嘴进行双面辐射加热。物料由下部进入上部离开并迅速进入专用的USX型急冷锅炉,每两根反应管合用一个USX,多个USX合接一个二次急冷锅炉。裂解过程停留时间可低于100ms,从而显著提高了反应的选择性。同传统的管式裂解炉相比,乙烯相对收率约可提高10%,甲烷和燃料油则有所减少。 USRT炉单台炉的乙烯年
18、产量为50~60kt。此种炉首次应用于日本出光石油化学公司所属千叶化工厂的年产300kt乙烯的生产装置上。中国兰州石油化学公司也将采用这种裂解炉生产乙烯。 2、反应炉比较 表2.5裂解石脑油时毫秒炉(USRT炉)与传统炉产品分布比较 产品 传统管式炉高深度裂解 毫秒炉中深度裂解 H2 1.0 1.0 CH4 17.0 12.8 C2H2 0.7 0.7 C2H4 28.5 29.0 C2H6 3.8 3.2 C3H4 0.6 1.0 C3H6 11.6 15.0 C3H8 0.3 0.4 C4H6 3.7 5.4 C4H8 2
19、.7 4.5 C4H10 0.2 0.2 C5+ 29.9 26.8 合计 100.0 100.0 H/C比(C5+) 1.0 1.16 H2+ CH4 / C2H4 0.631 0.476 C3H6/ C2H4 0.407 0.517 C4H6/ C2H4 0.130 0.186 C2H4+ C3H6+ C4H6 43.8 49.4 乙烯总效率(乙烷循环) 32.2% 32.2% (四)中国石化股份有限公司催化裂解工艺 一种石脑油催化裂解制乙烯丙烯的方法,以C4-C10烃的石脑油为原料,在反应温度600-700℃,反应压力为0.
20、001Mpa~0.5Mpa,反应重量空速为0.1-4小时-1,水/石脑油重量比为1~4:1的条件下,原料通过催化剂床层,反应生成乙烯丙烯,其中所用催化剂为选自ZSM-5和β沸石的共生分子筛、ZSM-5和Y沸石的共生分子筛或其混合物。 中国石化集团公司投资100亿美元新建四座1000kt/a石脑油裂解厂,在2007~2010年完成。这些项目分别由上海石化公司在上海漕泾、天津石化在天津、武汉石化在武汉和镇海炼化公司在宁波建设。据称,肯能寻找合作伙伴合资建设,中国石化也可以自己独立投资建设,除建设乙烯装置外,每座乙烯厂还建设一系列下游生产装置。建设这些大型乙烯项目将使天津石化、武汉石化和镇海炼化公
21、司进入烯烃产品生产行列。 2.3石脑油裂解工艺设计确定 本设计选用的是石脑油蒸汽裂解技术,生成的裂解气按照前脱乙烷后加氢的分离顺序进行分离精制得到产品聚合级乙烯、丙烯。 2.3.1原料及产品指标 表2.1 石脑油原料指标 项目 数据 密度(20℃)千克/米 704.6 馏程 初馏程℃ 40 终馏程℃ 160 饱和蒸汽压(20℃)千帕 50.2 烷烃%(重量%) 65.18 烷烃中正构烷烃%(重量%) >32.5 环烷烃%(重量%) 28.44 烯烃%(重量%) 0.17 芳烃%(重量%) 6.21 表2.2产品
22、质量指标 产品 含量(mol百分比) 甲烷乙烷含量 丙烯 杂质 聚合级乙烯 99.9%以上 1000ppm以下 250ppm以下 10ppm以下 产品 含量(mol百分比) 丙烷含量 乙烯含量 CO,CO2含量 S含量 聚合级丙烯 99.9%以上 5000ppm以下 50ppm以下 5ppm以下 1ppm以下 2.3.2催化裂解及预分馏工艺 石脑油以31600kg/h进料,裂解温度达到800℃,管壁温度达到1000℃。添加水蒸汽为稀释剂,与石脑油共同进料。 图2.1石脑油裂解装置裂解气预分馏过程示意图 如图所示
23、,石脑油裂解装置中裂解炉出口高温裂解气,经急冷换热器回收热量后,再经急冷器用急冷油喷淋降温至220~300℃左右。冷却后的裂解气进入油洗塔(或称预分馏塔),塔顶用裂解汽油喷淋,塔顶温度控制在100~110℃之间,保证裂解气中水分从塔顶带出油洗塔。塔釜温度则随裂解原料的不同而控制在不同水平。石脑油裂解时,塔釜温度大约180~190℃,轻柴油裂解时则可控制在190~200℃左右。塔釜所得燃料油产品,部分经汽提并冷却后作为裂解燃料油产品。另外部分(成为急冷油)送至稀释蒸汽系统作为稀释蒸汽的热源,回收裂解气的热量。经稀释蒸汽发生系统冷却的急冷油,大部分送至急冷器以喷淋高温裂解气,少部分急冷油进一步冷却
24、后作为油洗塔中段回流。 油洗塔塔顶裂解气进入水洗塔,塔顶用急冷水喷淋,塔顶裂解气降至40℃左右送入裂解气压缩机。塔釜约80℃,在此,可分馏出裂解气中大部分水分和裂解汽油。塔釜油水混合物经油水分离后,部分水(称为急冷水)经冷却后送入水洗塔作为塔顶喷淋,另一部分则送至稀释蒸汽发生器发生蒸汽,供裂解炉使用。油水分离所得裂解汽油馏分,部分送至油洗塔作为塔顶喷淋,另一部分则作为产品采出。 裂解气中含有CO,CO2,H2S,H2O,C2H2等气体杂质,来源主要有三方面:一是原料中带来;二是裂解反应过程生产;三是裂解气处理过程引入。根据《化学工艺学》中石脑油裂解气组成的分析,如下表所示: 表2.3石脑
25、油裂解气组成 裂解原料 石脑油 转化率 中深度 组成(体积分数)/% H2 14.09 CO+ CO2+ H2S 0.32 CH4 26.78 C2H2 0.41 C2H4 26.10 C2H6 5.78 C3H4 0.48 C3H6 10.30 C3H8 0.34 C4 4.85 C5 1.04 C6~204℃馏分 4.53 H2O 4.98 平均相对分子质量 26.83 在裂解和急冷过程中不可避免地会发生二次反应,最终会结焦,积附在裂解炉管的内壁上和急冷锅炉换热管的内壁上。所以需要及时给裂解炉和急冷锅炉进行清焦。 2.3
26、.3裂解气分离精制工艺 裂解气的分离和提纯工艺,是以精馏分离的方法完成的。精馏方法要求将组分冷凝为液态。甲烷和氢气不容易液化,碳二以上的馏分相对地比较容易液化。因此,裂解气在除去甲烷、氢气以后,其它组分的分离就比较容易。所以分离过程的主要矛盾是如何将裂解气中的甲烷和氢气先行分离。解决这对矛盾的不同措施,便构成了不同的分离方法。 工业生产上采用的裂解气分离方法,主要有深冷分离和油吸收精馏分离两种。油吸收精制分离的技术经济指标和产品纯度差,现已被淘汰。本设计选用的是深冷分离。深冷分离是在-100℃左右的低温下,将裂解气中除了氢和甲烷以外的其它烃类全部冷凝下来。然后利用裂解气中各种烃类的相对挥发
27、度不同,在合适的温度和压力下,以精馏的方法将各组分分离开来,达到分离的目的。其经济技术指标先进,产品纯度高,分离效果好,但投资较大,流程复杂,动力设备较多,需要大量的耐低温合金钢。 图2.2裂解气分离精制流程图 第三章 物料衡算 3.1概述 石脑油裂解年产22.7520万吨乙烯设计项目,采用毫秒裂解炉反应器反应生成裂解气、裂解汽油和燃料油。预处理后分离出裂解气,再对混合裂解气进行分离,得到产物乙烯和丙烯。整个低碳烯烃生产工艺流程主要由催化裂解预处理过程和烯烃精制两部分组成,物料的平衡计算侧重质量守恒。 3.2物料衡算的原理和基准 物料衡算的理论基础是质量守恒定理。它是研究
28、某一体系内进出物料量及组成的变化。进行物料衡算时,首先必须确定衡算的体系。对一般体系,均可表示为: (物料的积聚率)=(物料进入率)-(物料流出率)+(反应生成率)-(反应消耗率) 当系统没有化学反应时,则:(物料的积聚率)=(物料进入率)-(物料流出率) 在稳定状态下有:(物料进入率)=(物料流出率) 3.3物料衡算 3.3.1石脑油裂解预处理物料 形式 物料 百分含量(质量计%) 物料量kg/h 进料 石脑油 31600kg/h 出料 裂解气 73.2 23223.88 裂解汽油 15.76 4978.58 燃料油 11.04 3397.54
29、 3.3.2预处理后裂解气物料 裂解原料 石脑油 转化率 中深度 裂解气量 23223.88kg/h或861866.57mol/h 平均相对分子质量 26.83 裂解气组成(体积分数)/% 物料量(摩尔质量) H2 14.09 121437 CO+ CO2+ H2S 0.32 2757.97 CH4 26.78 23080.76 C2H2 0.41 3533.63 C2H4 26.10 224947.17 C2H6 5.78 49815.89 C3H4 0.48 4136.96 C3H6 10.30 88772.26
30、C3H8 0.34 2930.35 C4 4.85 41800.53 C5 1.04 8963.41 C6~204℃馏分 4.53 39042.56 H2O 4.98 42920.96 物料流入:31600kg/h 物料流出:23223.88 kg/h+4978.58 kg/h +3397.54kg/h=31600kg/h (物料进入率)=(物料流出率),所以物料守恒。 第四章 热量衡算 4.1工艺流程和热量衡算说明 根据能量守恒定律,进出系统的能量衡算式为: 输入系统中的能量-从系统输出的能量=系统中积累的能量 即: Q-过程的换热之和,
31、包括与环境的换热和与加热剂或冷却剂的换热。 W-输入系统的总的机械能。 ∑Hout-离开设备的各物料焓之和。 ∑Hin-进入设备的各物料焓之和。 在稳定流动中,系统内积累的能量为零。在无机械形式能量的交换时过程所需吸收或放出的热量等于其焓变。热量衡算就是对过程进行焓衡算,即: 本热量平衡计算书以单元设备为衡算对象,考虑下面三种形式的热量变化过程: (1)有机械能输入的能量转化过程,如压缩机; (2)有化学反应的化学能释放过程,如甲醇催化裂解反应; (3)只有物理变化的单纯的焓变过程,如汽化、冷凝和闪蒸等。 通过对主要单元设备进行衡算之后,再对全系统进行热量衡算,以便说明整
32、个工艺流程中热量的变化和利用情况,为公用工程的配置提供设计依据。 第五章 设备选型 5.1反应器设计 管式炉裂解技术的反应设备是裂解炉,它既是乙烯装置的核心,又是挖掘节能潜力的关键设备。 5.1.1裂解过程对管式炉的要求 对一个性能良好的管式炉来说,主要有以下几方面的要求: 1、适应多种原料的灵活性 所谓灵活性是指同一台裂解炉可以裂解多种石油烃原料。 2、炉管热强度高,炉子热效率高 由于原料升温,转化率增长快,需要大量吸热,所以要求热强度大,管径小可使比表面积增大,可满足要求;燃料燃烧除提供裂解反应所需的有效总热负荷外,还有散热损失、化学不完全燃烧
33、损失、排烟损失等,损失越少,则炉子热效率越高。 3、炉膛温度分布均匀 其目的是消除炉管局部过热所导致的局部结焦,达到操作可靠、运转连续、延长炉管寿命。 4、生产能力大 裂解炉的生产能力一般以每台裂解炉每年生产的乙烯量来表示。为了适应乙烯装置向大型化发展的趋势,各乙烯技术专利商纷纷推出大型裂解炉。裂解炉大型化减少了各裂解装置所需的炉子数量,一方面降低了单位乙烯投资费用,减少了占地面积;另一方面,裂解炉台数减少,使散热损失下降,节约了能量,方便了设备操作、管理,降低了乙烯的生产成本、维修等费用。目前运行的单台气体裂解炉最大生产能力已达到21万吨,单台液体裂解炉最大生产能力达到18~20万吨
34、。 5、运转周期长 裂解反应不可避免地总有一定数量的焦炭沉积在炉管管壁和急冷设备管壁上。当炉内管壁温度和压力降达到允许的极限范围值时,必须停炉进行清焦。裂解炉投料后,其连续运转操作时间,称为运转周期,一般以天数表示。所以,减缓结焦速度,延长炉子运转周期,同样是考核一台裂解炉性能的主要指标。 5.2换热器的设计选型 5.2.1概述 换热器的种类很多,按热量交换原理和方式,可以分为混合式、蓄热式和间壁式三种。本设计使用间壁式换热器。而间壁式换热器又包括管壳式、管式、板式、液模式等换热器。我们主要选用管壳式换热器。 5.2.2选型范例 下面本设计组以反应工段的换热器为例做一详细的选型说
35、明。下面本设计组以反应工段的换热器为例做一详细的选型说明。 (1)计算定性温度、确定物理常数 表5.2.1 物性表 项目 管程 壳程 定性温度 物理常数 (在定性温度) 注:, 表中物料的物性数据通过热量守恒处理以及《化工工艺设计手册》中得到; (2)初设总传热系数 (3)计算对数平均温差 热流体 536.7℃477.8℃ 冷流体 100℃180℃ (4)计算所需传热面积A,确定换热器参数 参考化工原理(天津大学出版)确定换热器的参数: 管子为正方形排列 管长,管程数N=2,管数为Nt=160,
36、传热面积,公称直径DN=480mm。 (5)对总传热系数进行校核 a. 计算传热膜系数 对于管程: 对壳程: 取换热器列管中心距t=32mm 当量直径 流体通过管间最大截面积为: 假定 b. 计算总传热系数K 从换热器设计手册(钱颂文 主编)查得污垢系数: 冷却管子为钢管其导热系数,而其壁厚 所以总传热系数: 所以选取的值符合设计要求。 (6)压力降的计算(参考化工工艺设计手册 第三版上册) 对于管程: 管程压强降 管程
37、流通面积 管内流速为: 设管壁的粗糙度为0.1mm,则,则查得 所以 对于壳程: 管子为正方形错列,取F=0.4 取折流板间距h=0.15m 挡板数 所以 管程和壳程压强降均符合题设要求 表5.2.2 换热器计算结果 项目 参数 壳程 单壳程 管程 双管程 壳内径 480 mm 管数 160根 排布方式 正三角形 管间距 32
38、 mm 管内径 20 mm 管外径 25 mm 热负荷 10.9913 MMcal/h 需换热面积 51.2966 m2 实际换热面积 42.1327 m2 平均传热系数 194.7 kcal/h .m2. K 对数平均温差 367.1552 ℃ 壳压降 789.6 Pa 管压降 1203.9 Pa 传质单元数 0.2178 裕量 21.75% 根据以上数据,查阅《化工工艺手册》,选取换热器,经过调试,满足压降要求和15~30%的裕量及冷却水出口温度规则,最后选用浮头式换热器,型号FA450-52-25-2。 5.3塔设备设计 5.3.1概述
39、 塔有板式塔和填料塔两大类,两者均可以用作蒸馏、吸收等气液传质过程,但各有优缺点,要根据具体情况进行选择。 5.3.2塔型选用原则 (1)填料塔的优势 a. 小直径塔费用低,便于安装; b. 压降较小,适合于要求压降较小的场合; c. 在难分离的场合可以降低塔高; d. 用于腐蚀严重的场合; e. 适合于发泡物系; f. 用于间歇精馏,因为填料塔的持液量低。 (2)板式塔的优势 a. 对于大直径塔设备费用低; b. 不易堵塞,且易清理; c. 适合大液量操作,因为板式塔气流为错流,流量增大对气体负荷影响小; d. 适合于中间内部换热,侧线出料多的场合。 5.3.4
40、分离塔的设计 塔的设计主要以脱甲烷塔为计算范例进行设计。 脱甲烷塔的作用是通过混合液挥发度的不同将甲烷与C2、C3分离开来。设计此塔时,希望它能满足如下设计要求: a. 生产能力大,即气液处理量大; b. 分离效率高,气液接触充分; c. 操作稳定,保持高的分离效率; d. 流体流动阻力小,及气液通过每层塔板的压降小; e. 结构简单可靠,制造安装容易,设备投资小。 (1)塔板选型 a. 板式塔塔板种类 根据塔板上气、液两相的相对流动状态,板式塔分为穿流式和溢流式。目前板式塔大多采用溢流式塔板。穿流式塔板操作不稳定,很少使用。 b. 各种塔板性能比较 工业上需分离的
41、物料及其操作条件多种多样,为了适应各种不同的操作要求,迄今已开发和使用的塔板类型繁多。这些塔板各有各的特点和使用体系,我们将几种主要塔板的性能比较列表如下: 表5.3.1 几种主要塔板的性能比较 塔板类型 优点 缺点 适用场合 泡罩板 较成熟、操作稳定 结构复杂、造价高、塔板阻力大、处理能力小 特别容易堵塞的物系 浮阀板 效率高、操作范围宽 浮阀易脱落 分离要求高、负荷 变化大 筛板 结构简单、造价低、塔板效率高 易堵塞、操作弹性较小 分离要求高、塔板数较多 舌型板 结构简单、塔板阻力小 操作弹性窄、效率低 分离要求较低的 闪蒸塔 浮动喷射板
42、 压降小、处理量大 浮板易脱落、效率较低 浮板易脱落、效率较低 下表给出了几种主要塔板性能的量化比较: 表5.3.2 几种主要塔板性能的量化比较 塔板类型 塔板效率 处理能力 操作弹性 压降 结构 泡罩板 1.0 1.0 5 1 复杂 浮阀板 1.2~1.4 1.4 3 0.5 简单 筛板 1.2~1.3 1.5 9 0.6 一般 舌型板 1.1~1.2 1.5 3 0.8 简单 (2)基本数据 表5.3.3 数据表 塔板 编号 气相体积流量cum/h 液相体积流流cum/h 气相密度kg/cum 液相密度
43、kg/cum 液相表面张力dyne/cm 液相粘度cp 1 482.4715 26.0962 30.0282 554.9378 17.1117 0.1206 2 518.5388 25.694 31.7322 478.3581 10.1991 0.07261 3 545.1864 29.2124 32.2437 459.2358 8.7543 0.06834 4 549.2259 29.7655 32.3393 456.842 8.5529 0.06831 5 549.9129 29.8365 32.3421 456.550
44、8 8.5196 0.06836 6 550.2073 29.7576 32.275 456.8406 8.5147 0.06844 7 550.9003 29.3434 31.9775 458.4664 8.519 0.06875 8 551.516 27.8539 31.0486 465.2981 8.521 0.0701 9 2077.446 379.0409 31.9201 484.5984 8.749 0.07458 10 2218.81 395.8869 32.3234 477.6359 8.2931 0.0
45、7311 11 2263.467 401.4327 32.5012 475.6356 8.1467 0.07296 12 2279.657 403.4955 32.5801 474.9542 8.0919 0.07298 13 2286.219 404.3395 32.6152 474.6895 8.0693 0.073 14 2289.024 404.6902 32.6291 474.5832 8.0595 0.07302 15 2290.174 404.7536 32.6239 474.572 8.0546 0.0730
46、4 16 2289.492 404.1587 32.5506 474.8004 8.0495 0.0731 17 2284.526 400.7282 32.1819 476.3593 8.0659 0.0735 18 2284.526 242.4697 32.1819 484.0618 7.9148 0.07567 由于各塔板的数据有一定的差异,故求出其平均值。 表5.3.4 计算结果 气相体积流量cum/h 液相体积流流cum/h 气相密度kg/cum 液相密度kg/cum 液相表面张力dyne/cm 液相粘度cp 平均值 1
47、492.294 226.0309 32.11633 475.4678 8.899256 0.074471 (3)塔径 令HT=0.55m,hL=0.07m,则 HT - hL=0.48m 查《化工工艺设计手册》泛点关联图得:C20=0.055 则C=C20=0.055 取安全系数为0.7,则空塔气速为 所以塔径 圆整后取D=2.0m。 (4)塔径的初步核算 ①降液管及流型选择 降液管主要有弓形、圆形和矩形三种。目前多采用弓形,因其结构简单,特别适合于塔径较大的场合。 液体在塔板上的流动路径是由降液管的布置方式决定的。常用的布置方式有以下几种形式:U
48、型流、单溢流、双溢流、多溢流。下表列出了溢流类型、塔径、液体负荷之间的经验数据。 表5.3.5 液体负荷与溢流类型的关系 塔径 cum/h 液体流量 cum/h U型流 单溢流 双溢流 1000 <7 <45 1400 <9 <70 1600 <9 <80 2000 <11 <90 90-160 3000 <11 <110 110-200 由于脱丙烷塔的液相负荷为1538.23cum/h,已超出相应塔径双溢流型塔板的液相负荷,为此我们在双溢流的基础上对塔板结构作了进一步改进: a. 加大了外堰长,取(一般而言双溢流型); b. 选
49、用凹型受液盘。 (注:这里及下面的所提到堰均指偶数板的堰,即降液管在两侧的堰) ②雾沫夹带 查手册得, ③停留时间 s>5s, 综上,塔径D=2.0m是合适的。 (5)溢流装置设计 a. 溢流堰长 b. 溢流堰高度 hw 选用平直堰,近似取,则 堰上液层高度 取板上清液层高度 故,圆整后取 所以板上清液层高度 c. 弓形降液管宽度与降液管面积 有=0.75查手册得 故两侧弓形降液管管宽 两侧降液管的面积 为使中间降液管的面积’等于两侧降液管面积之和, 经计算中间降液管的管宽 故降液管设计合理 d. 降液管底隙高度
50、 e. 液面梯度 平均溢流宽度 液体流道长度 鼓泡层高度 液面梯度 (6)塔板布置 a. 塔板的分块 因,故塔板采用分块式。查表得,塔板分为三块 (2)边缘区宽确定 取 b. 孔布置 筛孔按正三角形排列,取筛孔直径 ,,则t=17.5m 查图得开孔率 根据双溢流型开孔区面积计算公式 所以开孔面积 所以筛孔数 (7)塔板压降 a. 干板阻力hc计算 取板厚 ,则 ,查得C0=0.85,所以 取,,可忽略不计。 所以气体通过塔板的总压降 气体通过每层塔板的压降 (8)雾沫夹带 (合格) (9)液泛液校核
51、 取,<,故不会发生液泛。 (10)塔板负荷性能图 a. 液漏线 由,,,, 得 b. 雾沫夹带线 以kg液/kg气为限,求关系如下: 由 , 故 整理得 c. 液相负荷下限 根据平直堰,取堰上液层高度作为最小液体负荷标准。 取,则 d. 液相负荷上限 以作为液体在降液管中停留时间的下限,由式 得 e. 液泛线 令 由 ,,, 联立得 忽略,将与,与,与的关系式代入上式,并整理得 式中 , , 将有关数据代入,得
52、故 或 图5.1塔板负荷性能图 (11)塔高 a. 塔顶空间高度 b. 最后一块板到塔底高度 进气管顶部到最后一块板的距离 进气管管径 进气管底部到塔釜液面的距离 为保证塔底有1min的液体储量 所以 c. 群座高度 d. 封头高度 e. 开人孔处增加的高度 每四块板开一人孔,共需开4个人孔,开人孔处塔板间距为0.8m。 故需增加高度 所以 塔高H= (12)脱甲烷塔的机械设计 ① 塔体选材 脱甲烷塔的操作压力为1.8MPa,操作温度在-90℃左右,介质的腐蚀性不是很强,故综合考虑决定选用低合金钢板16MnR。 ② 塔体壁厚计算 a
53、. 塔筒体壁厚计算 查得低合金钢板16MnR 在 -90℃的许用应力: 焊缝系数 设计压力 取 则 考虑到塔的质量载荷、风载荷及地震载荷,圆整取塔筒体壁厚 b. 封头壁厚计算 采用标准椭圆形封头,则 圆整取与筒体相同的厚度即 c. 确定裙座壁厚 裙座取与筒体、封头相同的厚度即 (13)接管设计 a. 气流管 塔顶出料上升气体及塔釜进料气体速度均取20m/s 塔顶上升气流管 选取φ1007的焊接碳钢管,实际流速为17.07m/s。 塔釜进料气管 选取φ2007的焊接碳钢管,实际流速为13.20m/s。 b. 液流管 进出料流速均取2.5
54、m/s。 进料管 选取φ2005的无缝碳钢管,实际流速为2.00m/s。 塔釜出料管 选取φ1005的无缝碳钢管,实际流速为0.9233m/s。 5.3.5塔设计结果 a. 脱甲烷塔设计 通过脱丙烷系统分离出来的C3及以下产品进入脱甲烷塔。通过混合物系挥发度的不同从甲烷和C2、C3的混合物中分离开出C2、C3产品。塔参数设计如下: 表5.3.6 脱甲烷塔参数设计 项目 规格 塔径D 2000mm 塔高H 17.55m 塔截面积A T 3.14m2 塔板间距H T 550mm 塔板厚度δ 4mm 浮阀型式 F-1型浮阀 开孔率 14.1
55、% 阀孔直径d0 5mm 阀孔数目 6872 阀孔总面积A0 0.1349m2 阀孔动能因子F0 10kg0.5.m0.5.s-1 孔中心距t 17.5mm 塔板形式 双溢流型 堰长l w 1560mm 堰高h w 54mm 管宽W d1 338mm 管宽W d2 352mm 降液管面积A f 0.7034 m2 受液盘型式 凹型受液盘 外堰前安定区W s 100mm 内堰前安定区 60mm 边缘区W c 60mm 堰上液流高度h ow 54mm 板上清液层高度h L 70mm 板上清液层阻力h l 36.5mm 单板压
56、降h p 37.28mm 干板压降h c 0.83mmm 降液管内清液层高度H d 178.5mm 液体在降液管内的停留时间θ 6.17s 雾沫夹带e v 0.000023kg/kg 负荷上限L max 0.0774 m3/s 负荷下限L min 0.00266 m3/s b. 脱乙烷塔设计 经过脱甲烷塔分离出来的C2、C3产品进入脱乙烷塔将C2和C3产品分离开。塔参数设计如下: 表5.3.7 脱乙烷塔参数设计 项目 规格 塔径D 2800mm 塔高H 20.50m 塔截面积A T 6.15m2 塔板间距H T 600mm 塔板厚度δ
57、 4mm 开孔率 14.1% 阀孔直径d0 5mm 阀孔数目 16506 阀孔总面积A0 0.3239 m2 阀孔动能因子F0 10kg0.5.m0.5.s-1 孔中心距t 17.5mm 塔板形式 双溢流型 堰长l w 2100mm 堰高h w 60mm 管宽W d1 473mm 管宽W d2 492mm 降液管面积A f 1.3776m2 受液盘型式 凹型受液盘 外堰前安定区W s 100mm 内堰前安定区 60mm 边缘区W c 60mm 堰上液流高度h ow 10.53mm 板上清液层高度h L 70mm 板上清液
58、层阻力h l 31.74mm 单板压降h p 51.70mm 干板压降h c 19.96mmm 降液管内清液层高度H d 144.91mm 液体在降液管内的停留时间θ 12.54s 雾沫夹带e v 0.000022kg/kg 负荷上限L max 0.02268 m3/s 负荷下限L min 0.001791 m3/s c. 脱丙烷塔设计 反应产物通过水洗干燥后,进入脱丙烷系统,根据混合物系挥发度的不同将C4、C5和C2、C3产品分离开。塔参数设计如下: 表5.3.8 低压脱丙烷塔设计 项目 规格 塔径D 1000mm 塔高H 16.86m 塔
59、截面积A T 0.785m2 塔板间距H T 400mm 塔板厚度δ 4mm 浮阀型式 筛板 开孔率 14.1% 阀孔直径d0 5mm 阀孔数目 3164 阀孔总面积A0 0.06209 m2 阀孔动能因子F0 10kg0.5.m0.5.s-1 孔中心距t 17.5mm 塔板形式 单溢流型 堰长l w 700mm 堰高h w 40mm 管宽W d1 165mm 管宽W d2 70.65mm 降液管面积A f 0.07065m2 受液盘型式 凹型受液盘 外堰前安定区W s 75mm 内堰前安定区W s’ 50mm 边缘区
60、W c 50mm 堰上液流高度h ow 24.12mm 板上清液层高度h L 60mm 板上清液层阻力h l 34.15mm 单板压降h p 38.01mm 干板压降h c 3.86mm 降液管内清液层高度H d 124.2mm 液体在降液管内的停留时间θ 5.87s 雾沫夹带e v 0.0002252kg/kg 负荷上限L max 0.05653 m3/s 负荷下限L min 0.0005071 m3/s 表5.3.9高压脱丙烷塔设计 项目 规格 塔径D 2400mm 塔高H 29.70m 塔截面积A T 4.52m2 塔板间距H
61、 T 550mm 塔板厚度δ 4mm 浮阀型式 筛板 开孔率 14.1% 阀孔直径d0 5mm 阀孔数目 21495 阀孔总面积A0 0.4218 m2 阀孔动能因子F0 10kg0.5.m0.5.s-1 孔中心距t 17.5mm 塔板形式 单溢流型 堰长l w 1680mm 堰高h w 40mm 管宽W d1 396mm 管宽W d2 170mm 降液管面积A f 0.4068 m2 受液盘型式 凹型受液盘 外堰前安定区W s 100mm 内堰前安定区W s’ 60mm 边缘区W c 60mm 堰上液流高度h ow
62、 34.54mm 板上清液层高度h L 70mm 板上清液层阻力h l 33.54mm 单板压降h p 39.71mm 干板压降h c 6.165mm 降液管内清液层高度H d 132.6mm 液体在降液管内的停留时间θ 11.30s 雾沫夹带e v 0.0000897kg/kg 负荷上限L max 0.04475 m3/s 负荷下限L min 0.001433 m3/s d. 乙烯精馏塔 经过脱乙烷塔分离出来的产品(主要为乙烯和乙烷)进入乙烯精馏塔,根据混合物系的不同挥发度,分离出聚合级乙烯产品。塔参数设计如下: 表5.3.10乙烯精馏塔塔设计 项
63、目 规格 塔径D 3200mm 塔高H 37.20m 塔截面积A T 8.04m2 塔板间距H T 650mm 塔板厚度δ 5mm 浮阀型式 筛板 开孔率 14.1% 阀孔直径d0 6mm 阀孔数目 86202 阀孔总面积A0 0.542 m2 阀孔动能因子F0 10kg0.5.m0.5.s-1 孔中心距t 17.5mm 塔板形式 双溢流型 堰长l w 2400mm 堰高h w 54mm 管宽W d1 554mm 管宽W d2 532mm 降液管面积A f 1.801 m2 受液盘型式 凹型受液盘 外堰前安定区W
64、s 100mm 内堰前安定区 60mm 边缘区W c 60mm 堰上液流高度h ow 58mm 板上清液层高度h L 70mm 板上清液层阻力h l 36.5mm 单板压降h p 37.28mm 干板压降h c 0.83mm 降液管内清液层高度H d 178.5mm 液体在降液管内的停留时间θ 11.3s 雾沫夹带e v 0.000056kg/kg 负荷上限L max 0.0774 m3/s 负荷下限L min 0.00266 m3/s e. 丙烯精馏塔 经过脱乙烷塔分离出来的产品(主要为丙烯和丙烷)进入丙烯精馏塔,根据混合物系的不同挥发度
65、,分离出聚合级丙烯产品。塔参数设计如下: 表5.3.11丙烯精馏塔I设计 项目 规格 塔径D 2200mm 塔高H 34.10m 塔截面积A T 3.80m2 塔板间距H T 550mm 塔板厚度δ 5mm 浮阀型式 筛板 开孔率 14.1% 阀孔直径d0 5mm 阀孔数目 16697 阀孔总面积A0 0.3277 m2 阀孔动能因子F0 10kg0.5.m0.5.s-1 孔中心距t 17.5mm 塔板形式 双溢流型 堰长l w 1320mm 堰高h w 13.16mm 管宽W d1 125.4mm 管宽W d2 196
66、.9mm 降液管面积A f 0.4331 m2 受液盘型式 凹型受液盘 外堰前安定区W s 100mm 内堰前安定区 60mm 边缘区W c 60mm 堰上液流高度h ow 46.84mm 板上清液层高度h L 60mm 板上清液层阻力h l 27mm 单板压降h p 34.66mm 干板压降h c 7.66mm 降液管内清液层高度H d 118.8mm 液体在降液管内的停留时间θ 5.85s 雾沫夹带e v 0.001126kg/kg 负荷上限L max 0.04764m3/s 负荷下限L min 0.00266 m3/s 表5.3.12丙烯精馏塔II设计 项目 规格 塔径D 4400mm 塔高H 84.60m 塔截面积A T 15.19m2 塔板间距H T 600mm 塔板厚度δ 5mm 浮阀型式 筛板 开孔率 14.1% 阀孔直径d0 5mm 阀孔数目 77837 阀孔总面积A0 1.53 m2 阀孔动能因子F0 10kg0.5.m0.5.s-1 孔中心
- 温馨提示:
1: 本站所有资源如无特殊说明,都需要本地电脑安装OFFICE2007和PDF阅读器。图纸软件为CAD,CAXA,PROE,UG,SolidWorks等.压缩文件请下载最新的WinRAR软件解压。
2: 本站的文档不包含任何第三方提供的附件图纸等,如果需要附件,请联系上传者。文件的所有权益归上传用户所有。
3.本站RAR压缩包中若带图纸,网页内容里面会有图纸预览,若没有图纸预览就没有图纸。
4. 未经权益所有人同意不得将文件中的内容挪作商业或盈利用途。
5. 装配图网仅提供信息存储空间,仅对用户上传内容的表现方式做保护处理,对用户上传分享的文档内容本身不做任何修改或编辑,并不能对任何下载内容负责。
6. 下载文件中如有侵权或不适当内容,请与我们联系,我们立即纠正。
7. 本站不保证下载资源的准确性、安全性和完整性, 同时也不承担用户因使用这些下载资源对自己和他人造成任何形式的伤害或损失。
最新文档
- 36个关键词详解2025政府工作报告
- 学习2025年政府工作报告中的八大科技关键词
- 2025年政府工作报告要点速览接续奋斗共谱新篇
- 学习2025政府工作报告里的加减乘除
- 深化农村改革党课ppt课件(20250305)
- 弘扬雷锋精神凝聚奋进力量学习雷锋精神的丰富内涵和时代价值
- 深化农村改革推进乡村全面振兴心得体会范文(三篇)
- 2025年民营企业座谈会深度解读PPT课件
- 领导干部2024年述职述廉述责述学述法个人报告范文(四篇)
- 读懂2025中央一号党课ppt课件
- 2025年道路运输企业主要负责人安全考试练习题[含答案]
- 2024四川省雅安市中考英语真题[含答案]
- 2024湖南省中考英语真题[含答案]
- 2024宁夏中考英语真题[含答案]
- 2024四川省内江市中考英语真题[含答案]