兰州工业学院机设专业ca6140机床主轴箱的设计12级变速解读
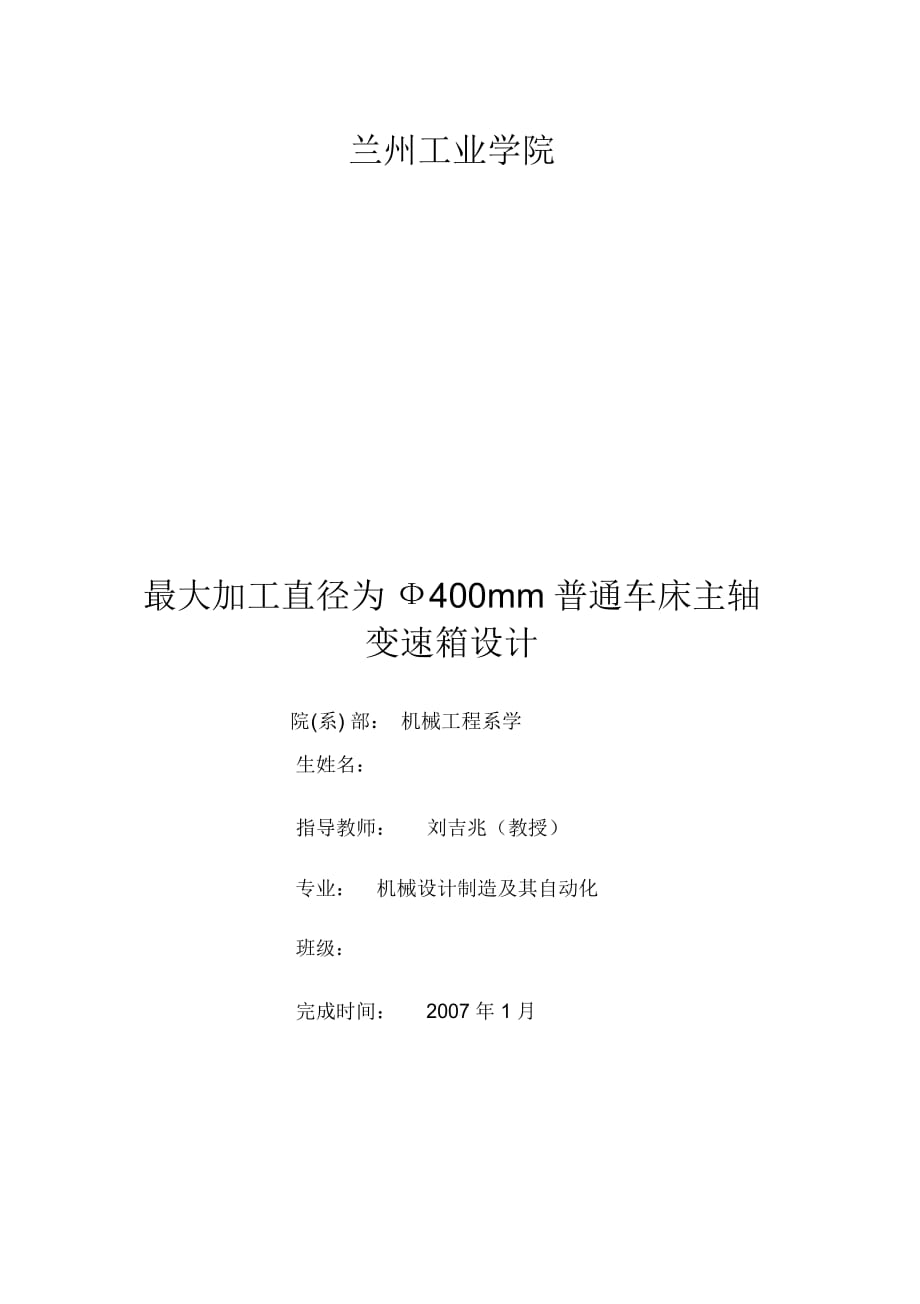


《兰州工业学院机设专业ca6140机床主轴箱的设计12级变速解读》由会员分享,可在线阅读,更多相关《兰州工业学院机设专业ca6140机床主轴箱的设计12级变速解读(40页珍藏版)》请在装配图网上搜索。
1、 兰州工业学院 最大加工直径为 Ф400mm普通车床主轴变速箱设计 院 (系) 部: 机械工程系学生姓名: 指导教师: 刘吉兆(教授) 专业: 机械设计制造及其自动化 班级: 完成时间: 2007 年 1 月 目录
2、 1. 车床参数的拟定 - ------------------------------------------------------2 1.1 车床主参数和基本参数 ------------------------------------------------ 2 1.1.1 拟定参数的步骤和方法 ---------------------------------------------- 2 2. 运动设计 - ------------------------------------------------------------4 2.1 传动结构式
3、、结构网的选择确定 ----------------------------------------- 4 2.1.1 传动组及各传动组中传动副的数目 ------------------------------------ 4 2.1.2 传动系统扩大顺序的安排 ------------------------------------------- 4 2.1.3 绘制结构网 -------------------------------------------------------- 4 2.1.4 传动组的变速范围的极限值 ----------------
4、-------------------------- 5 2.1.5 最大扩大组的选择 -------------------------------------------------- 5 2.2 转速图的拟定 -------------------------------------------------------- 6 2.2.1 主电机的选定 ------------------------------------------------------ 6 2.3 齿轮齿数的确定及传动系统图的绘制 ----------------------------
5、-------- 7 2.3.1 齿轮齿数的确定的要求 ---------------------------------------------- 7 2.3.2 变速传动组中齿轮齿数的确定 ---------------------------------------- 8 3. 强度计算和结构草图设计 -- --------------------------------------------11 3.1 确定计算转速 ------------------------------------------------------- 11 3.1.1 主轴的
6、计算转速 --------------------------------------------------- 11 3.1.2 中间传动件的计算转速 --------------------------------------------- 11 3.1.3 齿轮的计算转速 --------------------------------------------------- 12 3.2 传动轴的估算和验算 ------------------------------------------------- 12 3.2.1 传动轴直径的估算 ---------
7、---------------------------------------- 12 3.2.2 主轴的设计与计算 ------------------------------------------------- 13 3.2.3 主轴材料与热处理 ------------------------------------------------- 16 3.3 齿轮模数的估算和计算 ----------------------------------------------- 16 3.3.1 齿轮模数的估算 ---------------------------
8、------------------------ 16 3.3.2 齿轮模数的验算 --------------------------------------------------- 19 3.4 轴承的选择与校核 --------------------------------------------------- 21 3.4.1 一般传动轴上的轴承选择 ------------------------------------------- 21 3.4.2 主轴轴承的类型 -------------------------------------------
9、-------- 22 3.4.3 轴承间隙调整 ----------------------------------------------------- 22 3.4.4 轴承的校核 ------------------------------------------------------- 23 3.5 摩擦离合器的选择与验算 --------------------------------------------- 23 1 3.5.1 按扭矩选择 ----------------------------------
10、---------------------24 3.5 摩擦离合器的选择与验算 ---------------------------------------------24 3.5.1 按扭矩选择 -------------------------------------------------------24 3.5.2 外摩擦片的内径 d- ------------------------------------------------25 3.5.3 选择摩擦片尺寸 ( 自行设计 )-------------------------------------
11、----25 3.5.4 计算摩擦面的对数 Z------------------------------------------------25 3.5.5 摩擦片片数 ------------------------------------------------------25 参考文献 - -------------------------------------------------------------26 1. 车床参数的拟定 1.1 车床主参数和基本参数 1.1.1 拟定参数的步骤和方法 1)极限切削速度 Vmax、V
12、min 根据典型的和可能的工艺选取极限切削速度要考虑: 允许的切速极限参考值如下: 表 1.1 加 工 条 件 Vmax(m/min) Vmin(m/min) 硬质合金刀具粗加工铸铁工件 30 ~ 50 硬质合金刀具半精或精加工碳 150~ 300 钢工件 螺纹加工和铰孔 3~8 根据给出条件,取 Vmax=150 m/min 螺纹加工和铰孔时取 Vmin=4 m/min 2)主轴的极限转速 计算车床主轴极限转速时的加工直径,按经验分别取 K=0.5,Rn
13、=0.25 。则主轴极 限转速应为: 1000vmaz 1000v maz 1000 180 1146r / min nmax DkRn 3.1415 400 0.5 0.25 dmin 取标准数列数值,即 nmax =1250r/min 在 nmin 中考虑车螺纹和铰孔时, 其加工的最大直径应根据实际加工情况选取 50mm 左右。 1000vmin 1000 4 nmin = d max 3.14 31.8 r/min
14、 40 取标准数列数值,即 nmin =28r/min 2 转速范围 Rn=n max n min 转速范围 Rn=n max = 1250 =44.64r/min n min 28 取 1.41 Z= 1 lg Rn 1 lg 44.64 lg =12 lg 1.41 考虑到设计的结构复杂程度要适中, 故采用常规的扩大传动。 并选级数 Z=12,各级转速数列可直接从标准的数列表中查出,按标准转速数列为: 28, 40,56,80, 112,160
15、,224,315, 450,630,900, 1250 3)主轴转速级数 Z 和公比 已知 Rn=n max n min Rn= Z-1 且 Z= 2a x3b a、b 为正整数,即 Z 应可以分解为 2 和 3 的因子,以便用 2、 3 联滑移齿轮实现变速。 取 Z=12 级 则 Z=22 3 Rn Z 1nmax 1.4112 1 Rn 43.8 nmin nmax =1250 nmin =28 Rn= n max =44.64 n min 综合上述可得:主传动部件的运动参数 nmax 1250
16、nmin =28 Z=12 =1.41 4)主电机功率——动力参数的确定 合理地确定电机功率 N,使机床既能充分发挥其性能,满足生产需要,又不致使电机经常轻载而降低功率因素。 中型普通车床典型重切削条件下的用量 刀具材料: YT15 工件材料 45 号钢,切削方式:车削外圆 查表可知:切深 ap =3.5mm 进给量 f(s)=0.35mm/r 切削速度 V=90m/min 功率估算法用的计算公式 a 主切削力: Fz=1900apf0.75 =1900 3.5 0.35 0.75 =3026N b 切削功率: 3
17、 N 切 = FZV 3026 90 KW= KW=4.45KW 61200 61200 c 估算主 机功率: N=N切 = 4.45 =5.5KW 总 0.8 可 取 机 : Y132S-4 定功率 5.5KW , 速 1440r/min. 2.运动设计 2.1 传动结构式、结构网的选择确定 2.1.1 传动组及各传动组中传动副的数目 数 Z 的 系 由若干个 序的 成, 各 分 有 Z1、Z2、Z3、⋯个 副 . 即
18、 Z=ZZ Z ⋯ 1 2 3 副数由于 构的限制以 2 或 3 适合,即 速 数 Z 应为 2 和 3 的因子: 即 a 3b Z=2 实现 12 主 速 化的 系 可以写成多种 副的 合 : 1) 12=3 4 2) 12=4 3 3 12=3 2 2 4) 12=2 3 2 ) 5) 12=2 2 3 按照 副“前多后少
19、”的原 Z=3 2 2 一方案,但主 向采用双向片式摩擦离合器 构,致使Ⅰ 的 向尺寸 大,所以此方案不宜采用,而 先 12=232。 方案 4)是比 合理的 12=2 32 2.1.2 传动系统扩大顺序的安排 12=232 的 副 合,其 的 大 序又可以有 6 种形式: 1) 12=2 132 26 2) 12=2 1 3422 ) 6 3123 312=233126 4) 12=2 5) 12=2 234 21 6) 12=2 632 21 根据 比指数分配要“前密后疏”的原 ,
20、 用 Z=21 32 26 一方案,然 而 于我 所 的 构将会出 两个 : 第一 速 采用降速 ,由于摩擦离合器径向 构尺寸限制,使得Ⅰ 上 4 的齿轮直径不能太小,Ⅱ轴上的齿轮则会成倍增大。这样,不仅使Ⅰ - Ⅱ轴间中心距加大,而且Ⅰ - Ⅱ轴间的中心距也会辊大,从而使整个传动系统结构尺寸增大。这种传动不宜采用。 如果第一变速组采用升速传动,则Ⅰ轴至主轴间的降速传动只能同后两个变速组承担。为了避免出现降速比小于允许的杉限值,常常需要增加一个定比降速传动组,使系统结构复杂。这种传动也不是理想的。 如果采用 Z
21、=23 31 26 这一方案则可解决上述存在的问题。 2.1.3 绘制结构网 图 2.1 结构网 2.1.4 传动组的变速范围的极限值 齿轮传动最小传动比 Umin 1/4, 最大传动比 Umax 2 , 决定了一个传动组的最大 变速范围 rmax=umax/umin 8 。 因此,要按照下表,淘汰传动组变速范围超过极限值的所有传动方案。 极限传动比及指数 X,X, 值为: 表 2.1
22、 公比 极限传动比指数 1.41 X 值: Umin= 1 =1/4 x 4 X, 值: Umax= x, =2 2 5 (X+ X, ) 值: rmin= x+x` =8 6 2.1.5 最大扩大组的选择 正常连续的顺序扩大组的传动的传动结构式为: Z=Z1[1] Z2[Z1] Z3[Z1 Z2] 最后扩大组的变速范围 按照 r 8 原则,导出系统的最大级数 Z 和变速范围 Rn 为: 表 2.2
23、 Z3 2 3 1.41 Z=12 R n=44 Z=9 R n=15.6 最后扩大组的传动副数目 Z3=2 时的转速范围远比 Z3=3 时大 因此,在机床设计中,因要求的 R 较大,最后扩大组应取 2 更为合适。 同时,最后传动组与最后扩大组往往是一致的。安装在主轴与主轴前一传动轴的具有极限或 接近传动比的齿轮副承受最大扭距, 在结构上可获得较为满意的处理, 这也就是最后传动组的传 动副经常为 2 的另一原因。 2.2 转速图的拟定 运动参数确定以后,主轴各级转速就已知,切削耗能确定了电机功率。在此基础上,选择电机
24、型号,确定各中间传动轴的转速,这样就拟定主运动的转速图,使主运动逐步具体化。 2.2.1 主电机的选定 1)电机功率 N: 中型机床上,一般都采用三相交流异步电动机作为动力源。 根据机床切削能力的要求确定电机功率: N=5.5KW 2) 电机转速 n d : 选用时,要使电机转速 nd 与主轴最高转速 nmax 和 I 轴转速相近或相宜, 以免采用过大的升速或过小的降速传动。 nd =1440r/min 3)分配降速比 : 该车床主轴传动系统共设有四个传动组其中有一个是带传动。根据降速比分配应“前慢后快”的原则以及摩擦离合器
25、的工作速度要求,确定各传动组最小传动比。 u 总 = nmin / nE =28/1440=1/51.4 分配总降速传动比时,要考虑是否增加定比传动副,以使转速数列符合标准和有 6 利于减小齿数和减小径向与轴向尺寸,必须按“前慢后快”的原则给串联的各变速器分配最小传动比。 a 决定轴Ⅲ - Ⅳ的最小降速传动比主轴上的齿轮希望大一些,能起到飞轮的作用, 所以最后一个变速组的最小降速传动比取极限 1/4 ,公比 ψ=1.41 ,1.41 4=4,因此从 Ⅳ轴的最下点向上 4 格,找到Ⅲ上对应的点,连接对应的两点即为Ⅲ -
26、Ⅳ轴的最小传 动比。 b 决定其余变速组的最小传动比根据“前慢后快”的原则,轴Ⅱ - Ⅲ间变速组取 umin=1/ ψ3,即从Ⅲ轴向上 3 格,同理,轴Ⅰ - Ⅱ间取 u=1/ ψ3,连接各线。 c 根据个变速组的传动比连线按基本组的级比指数 x0=3,第一扩大组的级比指数 x1=1,第二扩大组的级比指数 x3=6, 画出传动系统图如 2.2 所示 图 2.2 转速图 2.3 齿轮齿数的确定及传动系统图的绘制
27、 2.3.1 齿轮齿数的确定的要求 可用计算法或查表确定齿轮齿数,后者更为简便,根据要求的传动比 u 和初步定 出的传动副齿数和 SZ ,查表即可求出小齿轮齿数。 选择时应考虑: 1.传动组小齿轮应保证不产生根切。对于标准齿轮,其最小齿数 Zmin Zmin =17 2.齿轮的齿数和 SZ 不能太大,以免齿轮尺寸过大而引起机床结构增大,一般推荐齿 数和 SZ ≤ 100-120,常选用在 100 之内。 3.同一变速组中的各对齿轮,其中心距必须保证 相等。 4.保证强度和防止热处理变形过大,齿轮齿根圆 到键
28、槽的壁厚 7 5. 保证主轴的转速误差在规定的范围之内。 图 2.3 齿轮的壁厚 2.3.2 变速传动组中齿轮齿数的确定 1)确定齿轮齿数 1. 用计算法确定第一个变速组中各齿轮的齿数 Z j +Z ’= SZ j Zj /Z j’ =uj 其中 Zj ——主动齿轮的齿数 Zj ’——被动齿轮的齿数 uj——一对齿轮的传动比 SZ ——一对齿轮的齿数和 为了保证不产生根切以及保证最小齿轮装到轴上或套筒上具有
29、足够的强度,最小齿轮必然是在降速比最大的传动副上出现。 把 Z1 的齿数取大些:取 Z1=Zmin =20 则 2 Z1 20 Z = u2 =58 1 / 2.85 齿数和 SZ =Z1+Z2=20+58=78 同样根据公式 Z3= Z 4 =39 2. 用查表法确定第二变速组的齿数 a 首先在 u1、 u2、u3 中找出最小齿数的传动比 u1 b 为了避免根切和结构需要,取 Zmin =24 c 查表找到 u1=1/1.413 的倒数 2.82 的行找到 Zmin=24 查表最小齿数和为 92 d 找
30、出可能的齿数和 SZ 的各种数值,这些数值必须同时满足各传动比要求的齿轮齿 数 能同时满足三个传动比要求的齿数和有 SZ =92 96 99 102 e 确定合理的齿数和 8 SZ =102 依次可以查得 Z5=27 Z6=75 Z7=34 Z8=68 Z9=42 Z10=60 同理可得其它的齿轮如下表所示: 表 2.3 变速组 第一变速组 第二变速组 第三变速组 齿数和 78 102 114
31、 齿轮 Z1 Z2 Z3 Z4 Z5 Z6 Z7 Z8 Z9 Z10 Z11 Z12 Z13 Z14 齿数 20 58 39 39 24 78 34 68 42 60 23 91 76 38 2)验算主轴转速误差 由于确定的齿轮齿数所得的实际转速与传动设计的理论转速难以完全相符,需要验算主轴各级转速,最大误差不得超过 10(ψ -1)%。 主轴各级实际转速值用下式计算 n 实=nE (1-ε ) ua ubucud 其中 ε——滑移系数 ε=0.2 a b c d 分别为各级的传动
32、比 12/45 u u u u 转速误差用主轴实际转速与标准转速相对误差的绝对值表示 ⊿n=| n实际 n标准 ∣≤ 10(ψ -1)% n实际 n 实 1=14400.6250.980.350.350.25 =27.8 ⊿n=∣(27.8-28)/28 ∣=0.7% 同样其他的实际转速及转速误差如下 : 表 2.4
33、 主 轴 n1 n2 n3 n4 n5 n6 n7 n8 n9 n10 n11 n12 转速 标 准 28 40 56 80 112 160 224 315 450 630 900 1250 转速 实 际 27.8 39.8 55.7 79.6 111.2 159.3 223.6 314.5 445.6 628.4 897.8 1244.9 转速 转 速 0
34、.7 0.5 0.5 0.5 0.7 0.4 0.1 0.2 0.9 0.3 0.2 0.4 误差 转速误差满足要求。 3) 齿轮的布置 为了使变速箱结构紧凑以及考虑主轴适当的支承距离和散热条件,其齿轮的布置如下图 2.4 所示。 9 4)绘制主传动系统图 按照主传动转速图以及齿轮齿数绘制主传动系统图如下 2.5 所示 图 2.4 齿轮结构的布置
35、 图 2.5 主传动系统图 3 . 强度计算和结构草图设计 3.1 确定计算转速 3.1.1 主轴的计算转速 nj =nminψz/3-1 10 z=12 nj =nminψ3 =28 2.82=79r/min 3.1.2 中间传动件的计算转速 Ⅲ轴上的 6 级转速分
36、别为: 112、160、224、315、450、630r/min. 主轴在 79r/min 以上都可以传递全部功率。 Ⅲ轴经 Z13-Z 14 传递到主轴,这时从 112r/min 以上的转速全部功率, 所以确定最低转速 112r/min 为Ⅲ轴的计算转速。按上述的方法从转速图中分别可找到计算转速:Ⅱ轴为 315r/min, Ⅰ轴为 900r/min, 电动机轴为 1440r/min. 3.1.3 齿轮的计算转速 Z10 安装在Ⅲ轴上,从转速图可见 Z10 齿轮本身有 6 种转速,其要传递全部的功率的计算转速为 112r/min 。 同样可以确定其余齿轮的转速如下表
37、3.1 所示: 表 3.1 齿轮 Z1 Z2 Z3 Z4 Z5 Z6 Z7 Z8 Z9 Z10 Z11 Z12 Z1 3 计算转速 900 315 900 900 315 112 315 112 315 112 150 160 112 3.2 传动轴的估算和验算 3.2.1 传动轴直径的估算 传动轴直径按扭转刚度用下列公式估算传动轴直径: d 944 N mm n j [ ] 其中: N—该传动轴的输入功率 N
38、 N d KW Nd—电机额定功率; —从电机到该传动轴之间传动件的传动效率的乘积 n j —该传动轴的计算转速 r/min [ ] —每米长度上允许的扭转角 (deg/m), 可根据传动轴的要求选取如表 3.2 所示 表 3.2 刚度要 主 轴 一般的传动轴 较低的传动轴 求 允许的扭转角 Z14 112
39、 11 [ ] 0.5 — 1 1— 1.5 1.5 —2 对于一般的传动轴,取 [ ] =1.5 N N d 5.5 0.96 5.28 KW n j =900 r/min d1 91 5.28 28.5 mm 400 4 1.5 900 1000 取 d1 32 mm N2 N d 5.5 0.96 0.995 5.25KW n j =425 r/
40、min d2 91 5.25 =37 mm 400 4 1.5 315 1000 取 d2 36 N3 N d 5.5 0.96 0.995 0.99 5.20 KW n j =150 d3 91 5.20 42.2 mm 400 4 150 1.5 1000 d3 46 采用花键轴结构, 即将估算
41、的传动轴直径 d 减小 7%为花键轴的直径, 在选相近的 标准花键。 d1’=29.3 0.93=27.0 d2’=34.5 0.93=32.0 d3’=42.2 0.93=40.0 查表可以选取花键的型号其尺寸 Z D d b(GB1144 74) 分别为 d1 轴取 6-28 32 7 d2 轴取 8-32 36 6 d3 轴取 8-42 46 80 3.2.2 主轴的设计与计算 主轴组件结构复杂,技术要求高。安装工件的主轴参与切削成形运动,此,它的 精度和性能性能直接影响加工质量(加工精度与表面粗糙
42、度) 。 12 1)主轴直径的选择 查表可以选取前支承轴颈直径 D1=90 mm 后支承轴颈直径 D2=(0.7 ~ 0.85)D 1=63~77 mm 选取 D2=70 mm 2)主轴内径的选择 车床主轴由于要通过棒料, 安装自动卡盘的操纵机构及通过卸顶尖的顶杆必须是空心轴。 确定孔径的原则是在满足对空心主轴孔径要求和最小壁厚要求以及不削弱主轴刚度的要求尽可能取大些。 推荐:普通车床 d/D( 或 d1/D1 )=0.55 ~ 0.6 其中 D ——主轴的平均直径, D= (D
43、1+D2)/2 d 1——前轴颈处内孔直径 d=(0.55 ~0.6)D=44 ~ 48 mm 所以,内孔直径取 45mm 3)前锥孔尺寸 前锥孔用来装顶尖或其它工具锥柄, 要求能自锁,目前采用莫氏锥孔。 选择如下: 莫氏锥度号取 5 号 标准莫氏锥度尺寸 大端直径 D=44.399 4)主轴前端悬伸量的选择 确定主轴悬伸量 a 的原则是在满足结构要求的前提下,尽可能取小值。 主轴悬伸量与前轴颈直径之比 a/D=0.6 ~1.5 a=(0.6 ~1.5)D 1 =54~135 mm 所以,悬伸量取 100mm 5)
44、主轴合理跨距和最佳跨距选择 根据表 3-14 见《金属切削机床设计》计算前支承刚度 K A 。 前后轴承均用 3182100 系列轴承,并采用前端定位的方式。 查表 K A 1700 D11.4 K A =1700901.4 =9.26 105 N/mm 13 K A 因为后轴承直径小于前轴承,取 1.4 K B KB = 6.61 105N/mm L0 ) 3 1 ( L0 K A a 1) 6( K B a
45、 其中 K A 为参变量 K B 综合变量 EI K A a 3 其中 5 2 E ——弹性模量,取 E=2.0 10 N/mm I 4 4 4 4 6 4 ——转动惯量, I= π(D -d )/64=3.14
46、 (80 -45 )=1.81 10 mm EI 2.0 105 1.81 106 K A a 3 = 5 100 3 9.26 10 =0.3909 由图 3-34 中,在横坐标上找出 η=0.3909 的点向上作垂线与 K A 1.4 的斜线相交, K B 由交点向左作水平线与纵坐标轴相交,得 L0/a=2.5 。
47、 所以最佳跨距 L0 L0=2.5a=2.5 100=250 mm 又因为合理跨距的范围 L 合理 =(0.75 ~1.5)L 0=187.5 ~375 mm 所以取 L=260 mm 6)主轴刚度的验算 对于一般机床主轴,主要进行刚度验算,通常能满足刚度要求的主轴也能满足强度要求。 对于一般受弯矩作用的主轴,需要进行弯矩刚度验算。主要验算主轴轴端的位移 y 和前轴承处的转角 θA。 14 图 3.1
48、主轴支承的简化 切削力 Fz=3026N 2 挠度 y A= Fza (L a) 3EI = 3026 1002 (260 100) 3 2.0 10 5 1.81 10 6 =0.01 [y]=0.0002L=0.0002 260=0.052 y A<[y] 倾角 θ A= Fa( 2L 3a) 6EI = 3026 100 (2 260 3 100) 6 2.0 105 181 10 6 =0.00011 前
49、端装有圆柱滚子轴承,查表 [ θA]=0.001rad θ A<[ θA] 符合刚度要求。 3.2.3 主轴材料与热处理 材料为 45 钢,调质到 220~250HBS ,主轴端部锥孔、定心轴颈或定心圆锥面等部位局部淬 硬至 HRC50 ~ 55,轴径应淬硬。 3.3 齿轮模数的估算和计算 3.3.1 齿轮模数的估算 根据齿轮弯曲疲劳的估算: m 323 N mm znj 齿面点蚀的估算: A 3703 N mm n j 其中 n j 为大齿轮的计算转速, A 为齿轮中心距。 由中心距 A
50、及齿数 z1 、 z2 求出模数: m j 2A mm z1 z2 根据估算所得 m 和 mj 中较大的值,选取相近的标准模数。 1)齿数为 32 与 64 的齿轮 N=5.28KW 15 m 5.28 323 1.85 mm 32 425 A N 3703 n j = 3703 5.2885.5 mm 425 m j 2 A 2 85.5 z2 32 1.78 mm z1 64 取模数为 2
51、 2)齿数为 56 与 40 的齿轮 m 323 5.28 1.54 mm 56 850 A 3703 N n j =3703 5.28 68 mm 1850 m j 2 A 2 68 z1 z2 56 1.42 mm 40 取模数为 2 3)齿数为 27 与 75 的齿轮 N=5.25KW m 323 5.25 2.48 mm
52、 75 150 A 3703 N nj =3703 5.25 121mm 150 m j 2 A 2 121 z1 z2 27 2.37 mm 75 16 取模数为 2.5 4)齿数为 34 与 68 的齿轮 N=525KW m 323 5.25 2.29mm 68 212 A 3
53、70 N 3 nj =3703 5.25 107.8 mm 212 m j 2 A 2 107.8 2.11 mm z1 z2 34 68 取模数为 2.5 5)齿数为 42 与 60 的齿轮 N=5.25KW m 323 5.25 2.12 mm 60 300 A 3703 N =3703 5.25 96.1 mm n j 300
54、 m j 2 A 2 96.1 z1 z2 42 1.88 mm 60 取模数为 2.5 6)齿数为 23 与 91 的齿轮 N=5.20KW 5.20 m 323 2.32 mm 91 150 A 3703 N n j =3703 5.20 121.0 mm 150 17 2 A 2 121.0 m j 2.12 mm z1 z2 23 91 取模数为 2.5
55、 7)齿数为 76 与 38 的齿轮 N=5.20KW m 323 5.20 2.46 mm 76 150 A 3703 N n j =3703 5.20 120.6 mm 150 m j 2 A 2 120.6 z2 76 2.12 mm z1 38 取模数为 2.5 3.3.2 齿轮模数的验算 结构确定以后,齿轮的工作条件、空间安排 、材料和精度等级等都已确定,才可 能
56、核验齿轮的接触疲劳和弯曲疲劳强度值是否满足要求。 根据齿轮的接触疲劳计算齿轮模数公式为: (i 1)K 1K 2 K 3 K S N m j 163003 mm m z1 2i [ j ]2 n j 根据齿轮的弯曲疲劳强度计算齿轮模数公式为: m K 1K 2 K 3K s N 275 mm z1Y mn j [ ] 式中: N--- 计算齿轮传递的额定功率 N J -- 计算齿轮(小齿轮)的计算转速 r/min m --- 齿
57、宽系数 m b , m 常取 6~10; m z1 --- 计算齿轮的齿数,一般取传动中最小齿轮的齿数; i --- 大齿轮与小齿轮的齿数比, i z2 1;“ +”用于外啮合,“- ”号用于内啮 z1 18 合; Ks --- 寿命系数, Ks K r K n K N K q ;⋯⋯⋯⋯⋯⋯⋯⋯⋯⋯⋯⋯⋯⋯⋯ 3.5 K T --- 工作期限系数, K T m 60nT ;⋯⋯⋯⋯⋯⋯⋯⋯⋯⋯⋯⋯⋯⋯⋯ 3.6 C 0
58、 等 件在接触和弯曲交 荷下的疲 曲 指数 m和基准循 次数 Co n--- 的最低 速 r/min; T--- 定的 工作期限,中型机床推荐: T=15000~ 20000h; K n --- 速 化系数 K N --- 功率利用系数 K q --- 材料 化系数。幅 低的交 我荷可使金属材料的晶粒 界 化,起着阻止疲 展的作用; K S (寿命系数)的极限 K S max , K S min 当 K S K max , 取 K S K S min ,取 K S K S min ; K 1
59、 --- 工作情况系数。中等冲 的主运 : K 1 =1.2 ~1.6 ; K 2 --- 荷系数 K 3 --- 向 荷分布系数 Y---- 形系数; [ ] 、 [ j ] --- 用弯曲、接触 力 MPa 1) 数 32 与 64 的 N 5.28 KW d mz 2 32 64mm 速度 V d n 64 850 2.85 m/s 60000 60000 由表 8 可得:取精度等
60、 7 级 。 K 2 =1.2K 1 1.2 m 1 m 1 7 0.21 z 32 由表 9 得: K 3 =1 Ks K r K n K N K q K T 60nT 3 60 850 17000 4.43 m K T 107 C 0 K n =0.71 K w 0.60 K q 0.78 Ks 4.43
61、 0.71 0.60 0.78 1.47 19 由表可知 K S K max 所以 取 Ks=0.6 由表 11 许用应力知,可取齿轮材料为 45 整淬 [ ] =1100MPa [ j ] =320MPa 由表 10 可知 可查得 Y=0.45 m j 16300 3 (i 1) K1 K 2 K 3 K S N m
62、 z1 2i[ j ] 2 n j ( 64 1) 1.2 1.2 1 0.6 5.28 m j 16300 3 32 64 1.89 32 2 1100 2 7 850 32 m K 1K 2 K 3K s N 275 mn j [ ] z1Y m 275 1.2
63、 1.2 1 0.6 5.28 1.51 32 0.45 7 850 320 所以 模数取 2 适合要求。 同样可以校核其它齿轮的模数也符合要求。 3.4 轴承的选择与校核 机床传动轴常用的滚动轴承有球轴承和滚锥轴承。在温升。空载功率和噪音等方 面,球轴承都比滚锥轴承优越。而且滚锥轴承对轴的刚度、支承孔的加工精度要求 都比较高,异常球轴承用得更多。但滚锥轴承的内外圈可以公开。装配方便,间隙 容易调整。所以有时在没有轴向力时,也常采用这种轴承。选择轴承的型式和尺寸, 首先取
64、决于承载能力,但也要考虑其它结构条件。即要满足承载能力要求,又要符 合孔的加工工艺,可以用轻、中、或重系列的轴承来达到支承孔直径的安排要求。 花键轴两端装轴承的轴颈尺寸至少有一个应小于花键的内径,一般传动轴承选用 G 级精度。 3.4.1 一般传动轴上的轴承选择 在传动轴上选择 6200 系列的深沟球轴承,其具体的型号和尺寸如下表 3.3 所示 表 3.3 传动轴 Ⅰ Ⅱ Ⅲ 轴承型号 6205 7206 7207 轴承尺寸 25 52 3055 3572 20 3.4.2
65、 主轴轴承的类型 主轴的前轴承选取 3182100 系列双列向心短圆柱滚子轴承。这种轴承承载能力大,内孔有 1:12 锥度,磨擦系数小,温升低,但不能承受轴向力,必须和能承受轴向力的轴承配合使用,因此整个部件支承结构比较复杂。 图 3.1 3.4.3 轴承间隙调整 为了提高主轴回转精度和刚度,主轴轴承的间隙应能调整。把轴承调到合适的 负间隙,形成一定的预负载,回转精度和刚度都能提高,寿命、噪声和
66、抗振性也有 改善。预负载使轴承内产生接触变形,过大的预负载对提高刚度没有明显效果,而磨损发热量和噪声都会增大,轴承寿命将因此而降低。 调整结构形式如下图所示: 21 图 3.2 调整说明: 转动调整螺母,使内圈向大端移动。 特点:结构简单。移动量完全靠经验,一旦调整过紧,难以把内圈退回。 3.4.4 轴承的较核 1) 滚动轴承的疲劳寿命验算 Lh Cf n T h 500 K A K Hp K Hn K
- 温馨提示:
1: 本站所有资源如无特殊说明,都需要本地电脑安装OFFICE2007和PDF阅读器。图纸软件为CAD,CAXA,PROE,UG,SolidWorks等.压缩文件请下载最新的WinRAR软件解压。
2: 本站的文档不包含任何第三方提供的附件图纸等,如果需要附件,请联系上传者。文件的所有权益归上传用户所有。
3.本站RAR压缩包中若带图纸,网页内容里面会有图纸预览,若没有图纸预览就没有图纸。
4. 未经权益所有人同意不得将文件中的内容挪作商业或盈利用途。
5. 装配图网仅提供信息存储空间,仅对用户上传内容的表现方式做保护处理,对用户上传分享的文档内容本身不做任何修改或编辑,并不能对任何下载内容负责。
6. 下载文件中如有侵权或不适当内容,请与我们联系,我们立即纠正。
7. 本站不保证下载资源的准确性、安全性和完整性, 同时也不承担用户因使用这些下载资源对自己和他人造成任何形式的伤害或损失。
最新文档
- 36个关键词详解2025政府工作报告
- 学习2025年政府工作报告中的八大科技关键词
- 2025年政府工作报告要点速览接续奋斗共谱新篇
- 学习2025政府工作报告里的加减乘除
- 深化农村改革党课ppt课件(20250305)
- 弘扬雷锋精神凝聚奋进力量学习雷锋精神的丰富内涵和时代价值
- 深化农村改革推进乡村全面振兴心得体会范文(三篇)
- 2025年民营企业座谈会深度解读PPT课件
- 领导干部2024年述职述廉述责述学述法个人报告范文(四篇)
- 读懂2025中央一号党课ppt课件
- 2025年道路运输企业主要负责人安全考试练习题[含答案]
- 2024四川省雅安市中考英语真题[含答案]
- 2024湖南省中考英语真题[含答案]
- 2024宁夏中考英语真题[含答案]
- 2024四川省内江市中考英语真题[含答案]