机械制造技术基础--第5章
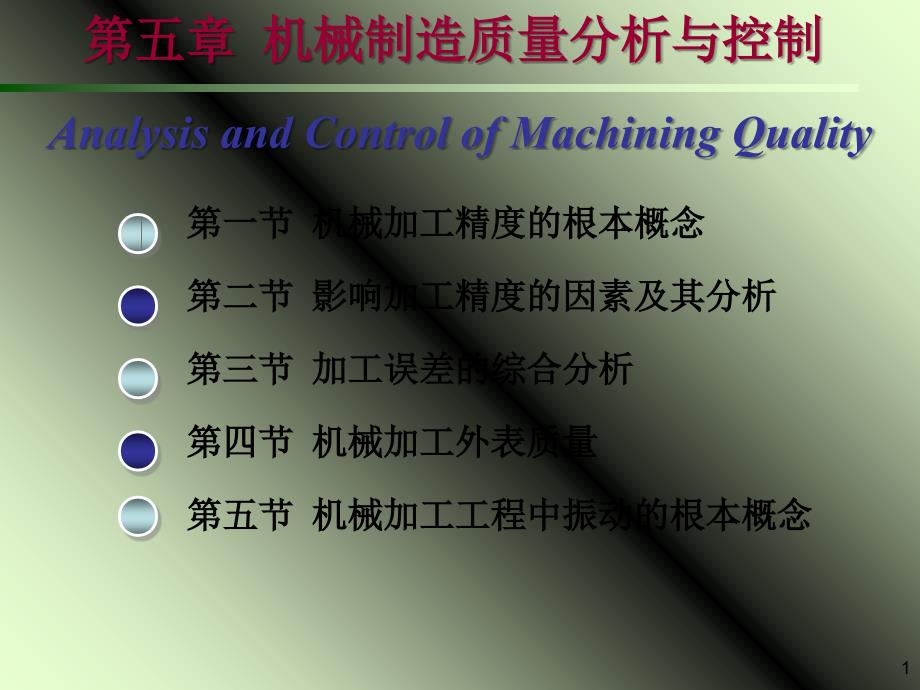


《机械制造技术基础--第5章》由会员分享,可在线阅读,更多相关《机械制造技术基础--第5章(106页珍藏版)》请在装配图网上搜索。
1、*,第五章 机械制造质量分析与控制,,,,第一节 机械加工精度的根本概念,,第二节 影响加工精度的因素及其分析,,第三节 加工误差的综合分析,,第四节 机械加工外表质量,,第五节 机械加工工程中振动的根本概念,,,Analysis and Control of Machining Quality,,1,尺寸精度,,形状精度,,位置精度,〔通常形状误差限制在位置公差内,位置公差限制在尺寸公差内〕,外表粗糙度,,波度,,纹理方向,,伤痕,加工精度,外表质量,外表几何形状精度,,,,,外表缺陷层,表层加工硬化,,表层金相组织变化,,表层残余应力,加工质量,,加工质量,2,一、加工精度与加工误差,加工
2、精度是指零件加工后的实际几何参数〔尺寸、形状及各外表相互位置等参数〕与图样规定的理想零件的几何参数的符合程度。符合程度越高,加工精度就越高。反之,越低。,第一节 机械加工精度的根本概念,零件的形状公差和位置公差一般应为相应尺寸公差的1/3~1/2左右,在同一要素上给出的形状公差值应小于位置公差值。,加工误差是指零件加工后的实际几何参数对理想几何参数的偏离程度。所以,加工误差的大小反映了加工精度的上下。,3,二、加工经济精度,加工本钱与加工误差之间的关系,加工经济精度是指在正常生产条件下〔采用符合质量标准的设备、工艺装备和标准技术等级的工人,不延长加工时间〕所能保证的加工精度,如图中之AB范围。
3、,4,定尺寸刀具加工,试切法切削轴,三、零件获得加工精度的方法,获得尺寸精度的方法,试切法,定尺寸刀具法,调整法,自动控制法,5,,获得形状精度的方法,轨迹法,成形刀具法,展成法,,获得位置精度的方法,直接装夹法,找正装夹法,夹具装夹法,6,第二节 影响加工精度的因素及其分析,在机械加工时,机床、夹具、刀具和工件就构成一个完整的系统。工艺系统中的误差是造成零件加工误差的根源,故称为原始误差。,原始误差,,例:活塞加工中以止口定位、顶部夹紧的精镗销孔工序的加工过程,分析影响工件和刀具间相互位置的种种因素。,1-对刀误差;2-夹紧误差;3-定位误差;4-导轨误差,7,原始误差分类,,工艺系统原始误
4、差,工艺系统原始状态有关的原始误差(工艺系统静误差),与工艺过程有关的原始误差(工艺系统动误差),原理误差,,定位误差,,调整误差,,刀具误差,,夹具误差,,,机床误差,,工艺系统受力变形,,工艺系统受热变形,,刀具磨损,,测量误差,,工件剩余应力引起的变形,主轴回转误差,,导轨导向误差,,传动误差,8,一、原理误差,,原理误差是指由于采用了近似的加工方法、近似的成形运动或近似的刀具轮廓而产生的误差。,例如滚齿用的齿轮滚刀,就有两种误差,一是为了制造方便,采用阿基米德蜗杆代替渐开线根本蜗杆而产生的刀刃齿廓近似造形误差;二是由于滚刀切削刃数有限,切削是不连续的,因而滚切出的齿轮齿形不是光滑的渐开
5、线,而是折线。,,成形车刀、成形铣刀也采用了近似的刀具轮廓。,,采用近似的成形运动和刀具刃形,不但可以简化机床或刀具的结构,而且能提高生产效率和加工的经济效益。,9,,机床导轨误差,机床导轨是机床中确定某些主要部件相对位置的基准,也是某些主要部件的运动基准。,,机床导轨误差的基本形式,垂直面内的直线度,,水平面内的直线度,,前后导轨的平行度〔扭曲〕,现以卧式车床为例,说明导轨误差是怎样影响工件的加工精度的。,二、机床几何误差,10,,床身导轨在垂直面内有直线度误差如图示,会引起刀尖产生切向位移,δ,z,,造成工件在半径方向产生的误差△R为:,导轨在垂直面内直线度误差的影响,11,导轨在水平面内
6、直线度误差的影响,当导轨在水平面内的直线度误差为△y时,引起工件在半径方向的误差为:△R,′,=,δ,y,假设:,那么:,12,对平面磨床,龙门刨床及铣床等,导轨在垂直面内的直线度误差会引起工件相对于砂轮〔刀具〕产生法向位移,其误差将直接反映到被加工工件上,造成形状误差〔图〕。,,,原始误差引起工件相对于刀具产生相对位移,假设产生在加工外表法向方向Y〔误差敏感方向〕,对加工精度有直接影响;产生在加工外表切向方向Z〔误差非敏感方向〕 ,可忽略不计。,龙门刨床导轨垂直面内直线度误差,,1-刨刀 2-工件 3-工作台 4-床身导轨,13,前后导轨平行度误差的影响,从图可知,车床前后导轨扭曲的最
7、终结果反映在工件上,于是产生了加工误差△y。从几何关系中可得出:,,△y:H≈△:A,,即 △y≈H△/A,,一般车床H≈2A/3,外圆磨床H≈A,因此该项原始误差对加工精度的影响很大。,14,机床主轴回转误差,主轴回转误差的根本形式,15,,工件回转类,刀具回转类,误差敏感,,方向不变,镗床,,,车床,加工时误差敏感,,方向和切削力方,,向随主轴回转而,,不断变化,,下面以在镗床上镗孔、车床上车外圆为例来说明主轴回转误差对加工精度的影响。,机床,16,车削时纯径向跳动对加工精度的影响,车床加工:工件回转,刀具移动。假设主轴轴线沿y轴作简谐运动,在工件的1处〔主轴中心偏移最大之处〕切出的
8、半径比在工件的2、4处切出的半径小一个幅值A;在工件的3处切出的半径比在工件的2、4处切出的半径大一个幅值A。这样上述四点工件的直径都相等,其它各点直径误差也很小,所以车削出的工件外表接近于一个真圆。,由此可见,主轴纯径向跳动对车削加工工件的圆度影响很小。,主轴的纯径向跳动对车削和镗削加工精度的影响,17,镗孔时纯径向跳动对加工精度的影响,Y=Acosφ+Rcosφ=(A+R)cosφ; Z=Rsinφ;,,将上两式平方相加得:Y2/(A+R)2+Z2/R2=1,,说明此时镗出的孔为椭圆形。,镗削加工:镗刀回转,工件不转。假设由于主轴纯径向跳动而使轴线在y坐标方向作简谐运动,其频率与主轴转速
9、相同,简谐幅值为A; 那么:Y = Acosφ(φ=ωt)当镗刀转过一个φ角时〔位置1’〕,刀尖轨迹的水平分量和垂直分量分别计算得:,18,产生径向圆跳动误差的主要原因有:主轴支承轴颈的圆度误差、轴承工作外表的圆度误差等、轴承孔之间的同轴度误差。假设机床主轴采用滑动轴承结构如图a所示,此时主轴支承轴颈的圆度误差将直接反映为主轴径向圆跳动δd,而轴承内径的圆度误差那么影响不大;在镗床上镗孔时如图b所示,轴承内外表的圆度误差将直接反映为主轴径向圆跳动δd,而主轴支承轴颈的圆度误差那么影响不大。,假设机床主轴采用滚动轴承结构,在车床上车外圆时,滚动轴承内环外滚道的圆度误差对主轴
10、径向圆跳动影响较大;在镗床上镗孔时,轴承外环内滚道的圆度误差对主轴径向圆跳动影响较大。滚动体的尺寸误差将直接影响主轴径向圆跳动误差的大小。,19,轴向窜动对车、镗削加工精度的影响,主轴的轴向窜动对内、外圆的加工精度没有影响,但加工端面时,会使加工的端面与内外圆轴线产生垂直度误差。,,主轴每转一周,要沿轴向窜动一次,使得切出的端面产生平面度误差,如图示。当加工螺纹时,会产生螺距误差。,轴向窜动对车削端面的影响,20,车外圆:得到圆形工件,但产生圆柱度误差〔锥体〕,,车端面:产生平面度误差,,镗孔时,由于主轴的纯角度摆动 使得主轴回转轴线与工作台导轨不平行,使镗出的孔呈椭圆形,如下图。,角度摆动对
11、车、镗削加工精度的影响,主轴纯角度摆动对镗孔精度的影响,21,,机床传动链误差,22,三、调整误差,调 整 误 差,机床的调整,夹具的调整,刀具的调整,23,工艺系统:,,机床、夹具、工件、刀具,外力:,切削力、传动力、惯性力、夹紧力、重力,破坏刀具、工件间相对位置,现场加工中工艺系统受力变形的现象,四、工艺系统受力变形对加工精度的影响,现象一:车细长轴时的腰鼓形误差,,现象二:旧机床的“让刀〞,,现象三:“无进给磨削〞,24,受力变形对工件精度的影响,,a) 车细长轴 b〕 磨内孔,由此看来,工艺系统的受力变形是机械加工精度中一项很重要的原始误差,为了保证和提高工件的加工精度,
12、就必须深入研究并控制以至消除工艺系统及其有关组成局部的变形。,25,机床部件刚度及其特点,工艺系统的刚度表示工艺系统整体抵抗其变形的能力。其大小为:垂直作用于工件加工外表的径向切削分力Fy与工艺系统在该方向上的变形y的比值,即k=Fy/y,工艺系统的刚度是由组成工艺系统各部件的刚度决定的。工艺系统的总变形量为: y,系统,= y,机床,+y,刀具,+y,夹具,+y,工件,,,而,,,所以,假设工艺系统各组成局部的刚度,就可以求出工艺系统的刚度。工艺系统刚度主要取决于薄弱环节的刚度。,工艺系统的刚度,26,例如装夹在卡盘中的棒料以及压紧在车床方刀架上的车刀,可以按照悬臂梁公式把它们的刚度计算出来
13、〔刀在工件最右端时变形最大〕,又如,支承在两顶尖间加工,的棒料,切削位置在中间点时,工件变形最大,可以用两支点梁的公式求出它的刚度:,式中 l--工件(刀具)长度(mm); E--材料的弹性模量(N/mm,2,),; I--工件(刀具)的截面惯性矩(mm,4,); y,1max,--外力作用在梁端点的最大位移(mm); y,2max,--外力作用在梁中点的最大位移(mm)。,27,静刚度测量,机床部件刚度的测定,车床刀架部件静刚度曲线,28,非线形关系,不完全是弹性变形,部件实测刚度远比按实体结构估算值小。图中第一次加载时刀架的平均刚度值约为,4.6×10,3,N/mm,,这只相当于一
14、个截面积为,30mm×30mm,、悬伸长度为,200mm,的铸铁悬臂梁的刚度,而刀架的实体结构尺寸要比此尺寸大得多。,存在剩余变形,反复加载卸载后剩余变形→0,加载和卸载曲线不重合,所围面积表示克服摩擦和接触塑性变形所作功,29,连接外表的接触变形,,薄弱零件本身的变形,,间隙的影响,,摩擦的影响,,施力方向的影响,影响机床部件刚度的因素,接触刚度 粗糙度 材料硬度,机床刚度的薄弱环节,外表的接触情况,30,工艺系统的变形随施力点位置的变化情况,切削力作用点位置变化引起工件形状误差,工艺系统受力变形对加工精度的影响,;,;,;,;,;,;,;,;,;,31,例:卧式车床的k头座=30
15、0000N/mm,k尾座=56600N/mm,k刀架=30000N/mm,径向切削分力Fy=4000N,设工件刚度、刀具刚度、夹具刚度相对较大,试计算加工一长为l的光轴由于工艺系统刚度发生变化引起的圆柱度误差。,解:工艺系统最小变形y,min,和最大变形y,max,:,,由于工艺系统刚度变化引起的工件圆柱度误差:,32,根据材料力学的计算公式,在切削点处的位移为:,综合以上两例的分析,可以推广到一般的情况,即工艺系统的总位移为以上两种情况的位移的叠加:,33,车削时毛坯形状的误差复映,由于毛坯存在的圆度误差△m=ap1-ap2 ,引起了工件产生圆度误差△w=y1 -y2 ,且△m越大,△w越大
16、,这种由于工艺系统受力变形的变化而使毛坯椭圆形状误差复映到加工后工件外表的现象称为“误差复映〞。,车削一具有椭圆形状误差的毛坯件A,让刀具预先调整到图上双点划线的位置, 毛坯椭圆长轴方向的背吃刀量为,a,p1,,短轴方向的背吃刀量为,a,p2,。由于背吃刀量不同,切削力不同,工艺系统的变形也不同,切削力大时,变形大。,,切削力大小变化引起的加工误差〔误差复映〕,34,式中为F,y,径向切削力,根据切削原理,切削分力可表示为:,,令,, C为常数,在车削加工中,x,Fy,≈1,,故有,,那么,35,例:在车床上用硬质合金刀具半精镗大直径短孔,加工前内孔的圆度误差为0.5mm,要求加工后圆度
17、误差小于0.01mm;主轴箱刚度k主轴=40000N/mm,k刀架=3000N/mm,走刀量f=0.05mm/r,工件材料硬度为190HBS;如只考虑机床刚度对加工精度的影响,问此镗孔工序能否到达预定的加工要求?,解:,查表2-2得:,计算结果说明,该镗孔工序能够到达预定的加工要求。,36,夹紧力影响,套筒夹紧变形后误差,图所示用三爪卡盘夹持薄壁套筒,在车床上车内孔。为减小此类误差,可用开口环夹紧薄壁环〔如图d〕或圆弧面卡爪夹紧〔如图e〕。由于夹紧力在薄壁环内均匀分布,故可减小由于工件夹紧变形引起的加工误差。,其他作用力引起的加工误差,37,薄片工件的磨削,,a) 毛坯翘曲
18、 b) 电磁工件台吸紧 c) 磨后松开,工件翘曲,,d) 磨削凸面 e) 磨削凹面 f) 磨后松开,工件平直,38,龙门铣横梁变形,【例】,龙门铣横梁,在横梁上再安装一根附加横梁,使横梁承受的重量转移到附加梁上,龙门铣横梁变形补偿,机床部件和工件本身质量质量的影响,解决1:,重量转移,,解决2:,变形补偿,39,,,,常用的提高接触刚度方法:,改善工艺系统主要零件接触面的配合质量;在接触面间预加载荷。,减小工艺系统受力变形的措施,提高工艺系统中零件间的配合外表质量,以提高接触刚度,设置辅助支承提高部件刚度,
19、采用辅助支承提高机床部件的刚度,40,,,提高工件的刚度,增加支承提高工件的刚度,,a〕采用中心架 b〕采用跟刀架,41,,,合理装夹工件,减小夹紧变形,铣角铁时的两种装夹,42,工艺系统在各种热源作用下,会产生相应的热变形,从而破坏工件与刀具间正确的相对位置,造成加工误差。,五、工艺系统热变形引起的加工误差,工艺系统的热变形及其热源,电机、轴承、齿轮、油泵等,工件、刀具、切屑、切削液,气温、室温变化、热、冷风等,热源,切削热,摩擦热,外部热源,内部热源,环境温度,热辐射,日光、照明、暖气、体温等,43,工艺系统的热平衡,工艺系统受各种热源的影响,其温度会逐渐升高。同时,它们也通过各种传热方
20、式向周围散发热量。,,热 平 衡,当单位时间内传入和散发的热量相等时,工艺系统到达了热平衡状态。,,而工艺系统的热变形也就到达某种程度的稳定。,44,机床的热变形及其对加工精度影响,车床受热变形,a〕 车床受热变形使床身及导轨向上凸起,b〕 温升与变形曲线,车床、铣床和钻、镗类机床的主要热源来自主轴箱。车床主轴箱的温升将使主轴中心升高,,45,立铣〔图a〕,立式铣床、外圆磨床、导轨磨床受热变形,a〕铣床受热变形形态,b〕外圆磨床受热变形形态,c〕导轨磨床受热变形形态,外圆磨〔图b〕,导轨磨〔图c〕,其他机床热变形,,46,图c〕支承距影响热变形,热对称结构〔图a〕,图b〕主轴箱的两种装配结构的
21、热位移,合理选择装配基准〔图c〕,避开加工误差的敏感方向〔图b〕,结构措施,减小机床热变形对加工精度影响的措施,图a〕立柱热对称结构,47,图a〕均衡立柱前后壁温度场,和隔离热源,均衡温度场,充分冷却和强制冷却,改善散热条件 。,图b〕采用隔热罩减少热变形,工艺措施,48,体积小,热容量小,到达热平衡时间较短,,温升高,变形不容无视〔达0.03 ~0.05mm〕,1、刀具热变形特点,2、刀具热变形变形曲线,车刀热变形曲线,曲线A—车刀连续工作时的热伸长曲线;,,曲线B—切削停止后,车刀温度下降曲线;,,曲线C—车刀作间断切削的热变形切削。,车外圆时,车刀热变形会使工件产生圆柱度误差〔喇叭口〕。
22、加工内孔又如何?,刀具热变形对加工精度的影响,49,工件均匀受热,△L=αL△T,,式中 α——工件材料的热膨胀系数,单位为1/℃;,,L——工件在热变形方向的尺寸,单位为mm;,,△T——工件温升,单位为℃。,工件热变形对加工精度的影响,例如:在磨削3m长的丝杠时,每磨一次温度升高3℃,那么被磨丝杠将伸长:,,△L=〔1.2×10-5×3000×3〕mm=0.1mm,,而6级丝杠的螺距累积误差在3m长度上不允许超过0.02mm左右。因此,热变形对工件加工精度影响很大。,50,为了减少工件热变形,可以采取以下措施:,,在切削区域施加充分的冷却液。,,提高切削速度或进给量。,,工件在精加工前得到
23、足够的冷却。,,刀具和砂轮不能过分磨钝。,,使工件在夹紧状态下有伸缩的自由。,在刨削、铣削、磨削加工平面时,工件单面受热,上下平面间产生温差,导致工件向上凸起,凸起局部被工具切去,加工完毕冷却后,加工外表就产生了中凹,造成了几何形状误差。,工件不均匀受热,51,六、工件内应力引起的变形,内应力是指在没有外部载荷的情况下,存在于工件内部的应力,又称剩余应力。剩余应力是由金属内部的相邻宏观或微观组织发生了不均匀的体积变化而产生的,促使这种变化的因素主要来自热加工或冷加工。,存在剩余应力的零件,始终处于一种不稳定状态,其内部组织有要恢复到一种没有内应力的状态倾向。,,在内应力变化的过程中,零件产生相
24、应的变形,原有的加工精度受到破坏。,,用这些零件装配成机器,在机器使用中也会逐渐产生变形,从而影响整台机器的质量。,52,铸件剩余应力引起的变形,毛坯制造中产生的剩余应力,在铸造、锻造、焊接及热处理过程中,由于工件各局部冷却收缩不均匀以及金相组织转变时的体积变化,在毛坯内部就会产生剩余应力。,53,冷校直引起的内应力,在外力F的作用下,工件内部的应力重新分布,在轴心线以上的局部产生压应力〔用负号表示〕,在轴心线以下的局部产生拉应力〔用正号表示〕。在轴心线和两条虚线之间,是弹性变形区域,在虚线以外是塑性变形区域。,冷校直工艺方法是在一些长棒料或细长零件弯曲的反方向施加外力F以到达校直目的.,当外
25、力F去除后,弹性变形本可完全恢复,但因塑性变形局部的阻止而恢复不了,使剩余应力重新分布而到达平衡。,冷校直带来的内应力,54,切削带来的内应力,工件在切削加工时,其外表层在切削力和切削热的作用下,会产生不同程度的塑性变形,引起体积改变,从而产生剩余应力。这种剩余应力的分布情况由加工时的工艺因素决定。,内部有剩余应力的工件在切去外表的一层金属后,剩余应力要重新分布,从而引起工件的变形。,,在拟定工艺规程时,要将加工划分为粗、精等不同阶段进行,防止在粗加工后内应力重新分布所产生的变形发生在精加工阶段或精加工之后。,,对质量和体积均很大的笨重零件,即使在同一台重型机床进行粗精加工也应该在粗加工后将被
26、夹紧的工作松开,使之有充足时间重新分布内应力,在使其充分变形后,然后重新夹紧进行精加工。,55,细长轴车削时的受力情况和变形状况,轴向力→压弯,,工件一端被夹紧,→,切削轴向力,→,弯曲,高速回转,→,离心力,→,加剧变形,导致振动,切削热,两端固定,→,热身长,→,轴向力,→,加剧,七、保证和提高加工精度的途径,直接消除或减少原始误差,56,大进给量反向切削法加工细长轴,进给方向由卡盘向尾座方向,后面采用浮动活顶尖,,采用大进给量和大主偏角车刀,:,消除径向振动,,采用浮动活顶尖缓解工件热伸长,;,减小弯曲变形,,将工件的卡盘端车出一缩颈,消除轴心线歪斜影响,57,补偿或抵消原始误差的方法,
27、人为的造成一种新原始误差去抵消原来的误差,正误差用人为的负误差去抵消,负误差用人为的正误差去抵消,两者大小相等,方向相反。,,用人为误差抵消装配后因自重产生变形,,精加工磨床床身导轨时预加载荷抵消装配后部件自重变形,,前后双刀架对刀,:,使切削力抵消,对刀切削示意图,龙门铣床横梁的变形与刮研,58,分组调整或均分误差的方法,例如,在V型块上铣削一个轴类工件的小平面,如图示,要求保证尺寸h的公差为0.02mm。工件采用经锻工艺,其尺寸分散范围ΔD=0.05mm,怎样才能满足要求?,解:,即毛坯的定位误差已经超出公差要求。,现采用分组调整的方法,将毛坯分为4组,那么各组毛坯误差ΔD=0.0125m
28、m,计算得其毛坯定位误差为0.0088mm,占工件公差的44%,比较适宜。,这个方法的实质就是:把毛坯按误差的大小分为n组,每组毛坯误差的范围就缩小为原来的1/n。然后按各组分别调整刀具相对于工件的位置,使各组工件的尺寸分散范围中心根本上一致。,59,转位误差在垂直面内,影响非常小,变形转移或误差转移的方法,横梁变形的转移,转塔车床的“立刀〞安装法,立轴转塔车床刀架转位误差的转移,,a)水平 b)垂直,六角转塔的转位误差△就处于Z方向,而非误差的敏感方向,由△而产生的加工误差△y就小到可以忽略不计。,60,“就地加工〞到达最终精度的方法,如转塔车床的转塔刀架上有6个安装刀杆的大孔,采用自
29、己加工自己保证与机床主轴回转件同轴。,六角车床转塔上六个孔和平面的加工与检验,61,在现场中,经常看到一些几何精度要求很高的轴和孔采用研磨方法来到达。研具本身并不要求具有很高的精度,但它却能在和工件作相对的运动中对工件进行微量的切削。最初是工件和研具的外表粗糙中最高点相接触,在一定的压力下,高点先磨损,然后接触面扩大,上下不平处逐渐接近,几何形状的精度也逐渐提高。这种外表间相对研擦和磨损的过程,也就是误差不断地减少的过程,称之为误差平均的方法。,,误差平均法的实质是:利用有密切联系的外表相互比较,相互检查,从比照中找出差距以后,或是相互纠正(如偶件的对研)或是互为基准进行加工。,误差平均的方法
30、,实时检测,动态补偿的方法,62,常值误差,变值误差,误差的大小和方向保持不变。如原理误差,机床、刀具、夹具、量具的制造误差,一次调整误差以及工艺系统的静力变形。,误差的大小和方向按一定规律变化。如机床和刀具的热变形和刀具磨损。,加工误差,随机,,误差,系统,,误差,在顺序加工一批工件时,误差的大小和方向都是随机变化的。如毛坯误差的复映,夹紧误差,屡次调整误差,剩余应力引起的变形误差等都属于随机性误差。,一、加工误差的性质,第三节 加工误差的综合分析,63,检查一批精镗后的活塞销孔直径,抽查件数为100,测量的结果如表所示。图纸规定的尺寸及公差为 。,分布曲线法,二、加工误差的
31、统计分析方法,表中n是测量的工件数。如果用每组件数的频率作为纵坐标,以尺寸范围的中点x为横坐标,就可以作成如下图的折线图。,64,活塞销孔实际直径尺寸分布折线图,分散范围=最大孔径-最小孔径=(28.004-27.992)mm=0.012mm;,问题:,分散范围0.012mm比公差范围0.015mm小,但还是有18%的工件超出了公差上限。,解决方法:消除常值系统性误差,即镗孔时将镗刀伸出量调整得短一些。,65,再如在无心磨床上用贯穿法磨削活塞销,其公差为 ,,,公差范围为0.009mm。设加工后量得的工件尺寸分布如图。,活塞销实际直径尺寸分布折线图,尺寸分散范围0.016大于公差范
32、围0.009,常值系统误差27.9980-27.9945=0.0035mm,即使把分散范围中心调整到与公差范围中心重合,也还是要产生不合格品。,要解决这类精度问题,不但要把系统误差减小,而且还要设法减小随机性误差。,,66,式中,n—工件的数目〔应足够多〕。,—工件的平均尺寸〔分散中心〕,,σ—,均方根差,,正态分布曲线方程:,正态分布曲线下面所包含的全部面积代表了全部工件,即100%。,图中阴影局部的面积F为尺寸从 到X间的工件的频率:,67,68,均方根误差σ决定了分布曲线的形状和分散范围。σ值越小那么曲线形状越陡,尺寸分散范围越小,加工精度越高;,算术平均值,正态分布曲线的特征参数,正
33、态分布曲线的特征参数有两个,即,和σ,是确定曲线位置的参数,。它决定一批工,件尺寸分散中心的坐标位置,如图a所示。使 产生变化,的主要原因是常值系统误差的影响。,69,正态分布曲线的特点,表中可以查出, 时,F=49.865%,2F=99.73%,。,即工件尺寸在±3σ以外的频率只占0.27%,可以忽略不计。因此,一般都取正态分布曲线的分散范围为±3σ。,±3σ (或6σ)的的大小代表了某一种加工方法在规定的条件下所能到达的加工精度。所以在一般情况下我们应该使公差带的宽度T 和均方根误差σ之间具有以下关系:,,T≥ 6σ,,考虑到变值系统性误差(如刀具磨损)及其他因素的影
34、响,总是使公差带的宽度大于6σ。,70,通常就以0.0134作为在正常生产条件下〔一次调整、同一机床、同一切削用等〕整批活塞销孔的尺寸分散范围。试比较一下上面所抽查100件测量的结果,尺寸分散范围为,可见是颇为接近的。,在上述检查活塞销孔的例子中,由所测量的数值来计算σ:,71,正态分布曲线除了用来进行加工误差性质的判断外,还常常用来进行工艺能力(工序能力)的计算。所谓工艺能力是用工艺能力系数Cp来表示的,它是公差范围T和实际加工误差之比〔分散范围6σ〕,即:,,Cp=T/6σ,根据工艺能力系数Cp的大小,可以将工艺分为5个等级:,,Cp>1.67,为特级,工艺力过高,不一定经济;,,1.67
35、≥Cp>1.33,为一级,工艺能力足够,可以允许一定的波动;,,1.33≥Cp>1.00,为二级,工艺能力勉强,必须密切注意;,,1.00≥Cp>0.67,为三级,工艺能力缺乏,可能出少量不合格品;,,0.67≥Cp,为四级,说明工艺能力不行,必须加以改进。,,一般情况下,工艺能力不应低于二级。,72,(a)两次调整下加工的零 (b)砂轮磨损下加工的 (c)形位误差分布曲线,,件的尺寸分布曲线 零件分布曲线,在机械加工中,工件实际尺寸的分布情况,有时也出现并不近似于正态的分布。,非正态分布曲线,73,非正态分布的分散范围,应将6σ除以相对分布系数K,即等于6σ/K。
36、K值的大小与分布曲线的形状有关。表中列出了几种典型分布曲线的K值和σ值,,α,称为相对不对称系数。,74,如果尺寸分散范围超出零件的公差带,那么肯定有废品产生,如下图的阴影局部。,,假设尺寸落在Lmin、Lmax范围内,工件的概率即空白局部的面积就是加工工件的合格率。,估算工序加工的合格率及废品率,75,例:在卧式镗床上镗削一批箱体零件的内孔,孔径尺寸要求为 ,孔径尺寸按正态分布, , ,试计算这批加工件的合格品率和不合格品率。,解:,那么合格率,那么这批工件合格率:P=0.49865+0.4772=97.585%,不合格率为1-97.585%=2
37、.415%。,76,例:无心磨床加工销轴,外径 ,抽样后测 ,,,=0.005mm,尺寸分布符合正态分布,试分析该工序的加工质量。,解:,1)判断加工能力,结论:工艺能力缺乏,产生废品不可防止。,2)计算废品率,77,由图知,,,因此没有不可修复的尺寸偏小的废品。,因此尺寸偏大废品率为0.5-0.4772=2.28%。因为,d,max,< X,max,,所以产生的废品可修复。,3)工艺分析,使,尺寸偏大废品率为0.5-0.4965=0.35%,总的废品率为2×0.35%=0.7%。,78,点图法,要点:按加工的先后顺序作出尺寸的变化图,以暴露整个加工过
38、程中误差变化的全貌。,,具体方法:按工件的加工顺序定期测量工件的尺寸,以其序号为横坐标,以量得的尺寸为纵坐标,那么可得到如下图的点图。,自动车床加工的点图,79,点图的用法有多种,下面主要阐述点图在工艺稳定性的判定和工序质量控制方面的应用。,,所谓工艺的稳定,从数理统计的原理来说,一个工序的质量参数的总体分布,其平均值 和均方根差 在整个工序中假设能保持不变,那么工艺是稳定的。为了验证工艺的稳定性,需要应用 和 两张点图。 是将一批工件依照加工顺序分成m个为一组、第i组的平均值,共K组; 是第i组数值的极差 。两张图常常合在一起应用,通称为 图,
39、如图示。,80,精镗活塞销孔和磨轴承内环孔的 图,81,在 图上分别画出中心线和控制线,控制线就是用来判断工艺是否稳定的界限线。,图的中心线为,图的中心线为,图的上控制界限为,图的下控制界限为,图的上控制界限为,图的下控制界限为,82,零件外表质量,表面粗糙度,表面波度,外表物理、力学性能的变化,外表层的几何形状特征,表面层冷作硬化,表面层残余应力,表面层金相组织的变化,第四节 机械加工外表质量,一、概述,83,表面粗糙度与初期磨损量的关系,零件外表质量,粗糙度太大、太小都不耐磨,适度冷硬能提高耐磨性,对疲劳强度的影响,对耐磨性影响,对耐腐蚀性的影响,对配合质量的影响,粗糙
40、度越大,疲劳强度越差,适度冷硬、剩余压应力能提高疲劳强度,有配合要求的外表、Ra小。,粗糙度越小,接触刚度越高,粗糙度越大,耐腐蚀性越差,冷作硬化、剩余应力降低耐腐蚀性,对配合质量的影响,其他影响,剩余应力降低机器工作质量,二、外表质量对零件使用性能的影响,84,三、机械加工外表的粗糙度及其影响因素,切削加工后的外表粗糙度,切削加工外表粗糙度的形成,主偏角Kr、副偏角Kr′、进给量f越小,刀尖圆弧半径rε越大,加工外表的粗糙度越小。,几何因素,85,物理因素,加工后外表的实际轮廓和理论轮廓,由于存在着与被加工材料的性能及切削机理有关的物理因素,切削加工后外表的实际粗糙度与理论粗糙度有着较大差异
41、。,在切削过程中出现的刀瘤与鳞刺,会使外表粗糙度严重地恶化,在加工塑性材料时,常是影响粗糙度的主要因素。,86,影响切削加工外表粗糙度的因素,刀具几何形状,刀具材料、刃磨质量,切削用量,工件材料,f,、,K,r,、,K’,r,↓,、,r,ε,→R,a,↓,,前角↑→,R,a,↓,,后角↑→摩擦↓→,R,a,↓,,v↑→ R,a,↓,,f↑→ R,a,↑,,a,p,不宜太小,材料塑性↑→,R,a,↑,,晶粒组织大↑→,R,a,↑,,,常用正火、调质处理,,脆性材料接近理论,R,a,刀具材料强度↑→,R,a,↓,,前后刀面,Ra↑→R,a,↓,,冷却、润滑↑→,R,a,↓,87,影响磨削加工外表粗
42、糙度的因素,粒度↓→,R,a,↓,砂轮越光滑↑,→,R,a,↓,,磨粒等高性↑→,R,a,↓,砂轮粒度,砂轮修正,磨削用量,砂轮,V↑→ R,a,↓,,a,p,、,工件,V↑→,塑变,↑→,R,a,↑,,粗磨,a,p,↑→,生产率↑,,精磨,a,p,↓→ R,a,↓,磨削加工外表是由砂轮上大量的磨粒刻画出的无数极细的沟槽形成的。每单位面积上刻痕越多已经刻痕的等高度越好,那么粗糙度越小。,磨削加工后的外表粗糙度,88,外表物理力学性能变化,影响金相组织,,变化因素,影响显微硬度,,因素,影响剩余应力,,因素,塑变引起的冷硬,,金相组织变化引起的硬度变化,冷塑性变形,,热塑性变形,,金相组织变化,
43、切削热,四、机械加工后外表物理力学的性能,切削力,,切削热,89,加工外表的冷作硬化,切削过程中产生的塑性变形,会使表层金属的晶格发生扭曲、畸变,晶粒间产生剪切滑移,晶粒拉长、破碎和纤维化,这些都会使表层金属的硬度和强度提高,这种现象称作冷作硬化。,冷作硬化的程度取决于塑性变形的程度,塑性变形越大,硬化程度越大。,切削加工后外表层的冷作硬化,N—硬化程度,,H—外表层的显微硬度,,H0—基体材料的硬度,,h—硬化层深度,式中,90,,刀具的影响,前角↓、切削刃 rε↑、后面磨损量VB↑→塑变变形,↑,,→冷硬↑,切削用量,,的影响,切削速度v↑→塑变↓→冷硬↓,,f↑→切削力↑→塑变↑→冷硬↑
44、,工件材料,,性能的影响,,材料塑性↑→冷硬↑,的主要因素,,影响冷作硬化,91,磨削加工时,磨削外表层温度一般高于500~600℃,某些情况甚至更高,,当温度到达相变临界点时,表层金属就发生金相组织变化,强度和硬度降低、产生剩余应力、甚至出现微观裂纹。这种现象称为磨削烧伤。,,淬火钢在磨削时,由于磨削条件不同,产生的磨削烧伤有三种形式。,加工外表层的金相组织变化,当加工外表温度超过相变温度时,表层金属的金相组织将会发生相变。切削加工时,切削热大局部被切屑带走,因此影响较小,多数情况下,表层金属的金相组织没有质的变化。,92,回火烧伤,退火烧伤,如果磨削区温度超过马氏体转变温度〔中碳钢250~
45、300℃〕,这时工件表层金属的金相组织,由原来的马氏体转变为硬度较低的回火组织〔索氏体或托氏体〕,这种烧伤称为回火烧伤,假设工件表层温度超过相变温度,而磨削区又没有冷却液进入,表层金属产生退火组织,硬度急剧下降,称之为退火烧伤。,淬火烧伤,如果磨削区温度超过了相变临界温度〔碳钢的相变温度为723℃〕,马氏体转变成奥氏体,在切削液急冷作用下,使表层金属发生二次淬火,硬度高于原来的回火马氏体,这种烧伤称为淬火烧伤,93,磨削用量,合理选择砂轮,砂轮转速,↑ →,,磨削烧伤↑,,径向进给量,f,p,↑→,,磨削烧伤↑,,轴向进给量,f,a,↑→,磨削烧伤↓,,工件速度,v,w,↑→,磨削烧伤↓,磨削
46、时,砂轮外表上磨粒的切削刃口锋利↑→磨削力↓→磨削区的温度↓,,合理选择砂轮硬度、结合剂和组织→磨削烧伤↓,影响磨削烧伤的因素及改善途径,增大磨削刃间距,间断磨削→受热↓→磨削烧伤↓,改善冷却条件,采用内冷却法→烧伤↓,94,冷塑性变形的影响,切削后,表层产生残余压应力,而在里层产生残余拉伸应力。,热塑性变行的影响,,表层产生残余拉应力,里层产生产生残余压应力。,金相组织变化的影响,,比重小的组织→比重大的组织→体积收缩,产生拉应力,反之,产生压应力,加工外表层的剩余应力,r,马,≈7.75 g/cm³,,r,奥,≈7.96 g/cm³,,r,残,≈7.78 g/cm³。,,试分析,在磨削淬火
47、钢时产生的三种不同类型的烧伤,其外表层的剩余应力状态。,95,机械加工后工件外表层的剩余应力是冷塑性变形、热塑性变形和金相组织变化的综合结果。切削加工时起主要作用的往往是冷态塑性变形,外表层常产生剩余压缩应力。磨削加工时起主要作用的通常是热态塑性变形或金相组织变化引起的体积变化,外表层常产生剩余拉伸应力。,磨削裂纹和剩余应力有着十分密切的关系。在磨削过程中,当工件外表层产生的剩余应力超过工件材料的强度极限时,工件外表就会产生裂纹。由于磨削热是产生剩余拉应力的根本原因,因此防止裂纹的途径也在于降低磨削热以及改善其散热条件。磨削裂纹常与烧伤同时出现。,96,喷丸强化,,喷丸强化是利用大量快速运动的
48、珠丸打击被加工工件外表,使工件外表产生冷硬层和压缩剩余应力,可显著提高零件的疲劳强度。,,珠丸的直径一般为0.2~4mm,对于尺寸较小、外表粗糙度值较小的工件,采用直径较小的珠丸。,,喷丸强化主要用于强化形状复杂或不宜用其它方法强化的工件,如弹簧、连杆、齿轮、焊缝等。经喷丸加工后的外表,硬化层深度可达0.7mm,零件外表粗糙度值可由Ra5~2.5μm 减小到Ra0.63~0.32μm,可几倍甚至几十倍地提高零件的使用寿命。,五、控制加工外表质量的途径,97,滚压加工是利用经过淬火和精细研磨过的滚轮或滚珠,在常温状态下对金属外表进行挤压,使受压点产生弹性和塑性变形,表层的凸起局部向下压,凹下局部
49、向上挤,逐渐将前工序留下的波峰压平,降低了外表粗糙度;如图为典型的滚压加工示意图。同时它还能使工件外表产生硬化层和剩余压应力。因此提高了零件的承载能力和疲劳强度。,,滚压加工可以加工外圆、孔、平面及成型外表,通常在普通车床、转塔车床或自动车床上进行。,滚压加工,滚压加工原理,98,机械加工振动,自激振动,自由振动,强迫振动,当系统受到初始干扰力鼓励破坏了其平衡状态后,系统仅靠弹性恢复力来维持的振动称为自由振动。由于总存在阻尼,自由振动将逐渐衰减。(占5%),系统在周期性激振力(干扰力)持续作用下产生的振动,称为强迫振动。 (占35%),在没有周期性干扰力作用的情况下,由振动系统本身产生的交变力
50、所激发和维持的振动,称为自激振动。(占65%),第三节 机械加工过程中的震动,99,强迫振动的特征,机外振源,,旋转零件的质量偏心,,传动机构的缺陷,,断续切削引起的振动,1〕强迫振动是由周期性激振力引起的,不会被阻尼衰减掉,振动本身也不能使激振力变化。,,2〕强迫振动的振动频率与外界激振力的频率相同,而与系统的固有频率无关。,,3〕强迫振动的幅值既与激振力的幅值有关,又与工艺系统的特性有关。,一、机械加工过程中的强迫振动,强迫振动,100,机械加工中的自激振动是指在没有周期性外力干扰下产生的振动运动。在实际加工过程中,由于偶然的外界干扰〔如工件材料硬度、加工余量的变化等〕,会使切削力发生变化
51、,从而使工艺系统产生自由振动。通常将自激振动看成是由振动系统〔工艺系统〕和调节系统〔切削过程〕两个环节组成的一个闭环系统,如下图。,机械加工过程中的自激振动,二、机械加工过程中的自激振动〔颤振〕,自激振动系统的组成,101,自激振动的特征,自,,激,,振,,动,,特,,点,,不衰减的振动,由振动过程本身引起切削力周期性变化,无阻尼存在。,自激振动的频率接近于系统薄弱环节的固有频率,这与强迫振动根本不同。,,能量E,,A B,,C 振幅A,E,-,E,+,f,自,=,f,固,取决于一周期,,获得的能量,取决于切削,,过程本身,102,自激振动的激振机理,再生颤振,重叠系数μ=(B-f)/B。切
52、断时,μ=1;车螺纹时,μ=0;大多数情况下0<μ<1。重叠切削是再生颤振的必要条件,非充分条件。,切削时再生颤振的产生,103,当纵车方牙螺纹的外圆外表如下图,刀具并未发生重叠切削,假设按再生颤振原理,那么不应该产生颤振。但在实际加工中,当切削深度到达一定值时,仍会发生颤振,这可以用振型耦合原理来解释。,刀具等效质量为 m;相互垂直的等效刚度系数分别为k1、k2〔设k1< k2〕刚度低的方向振型为x1,刚度高的方向振型为x2。,振型耦合,纵车方牙螺纹外外表,两个自由度振型耦合颤振动力学模型,104,产生自激振动的条件,单自由度机械加工振动模型,,a〕 振动模型 b〕 力与位移的关系图,W振
53、出=W振入+ W摩阻〔振入〕时,系统有稳幅的自激振动;,,W振出>W振入+ W摩阻〔振入〕时,系统为振幅递增的自激振动,至一定程度,系统有稳幅的自激振动;,,W振出< W振入+ W摩阻〔振入〕时,系统为振幅递减的自激振动,至一定程度,系统有稳幅的自激振动;,振动系统产生自激振动的根本条件是:,W,振出,>W,振入,E,吸收,>E,消耗,,即,105,冲击式减振镗杆和镗刀,动力减振装置,三、控制机械加工振动的途径,减小内部振源,,调整振源频率,,采取隔振措施,f,、,K,r,↑→μ,↓→,自振↓,,γ,、,K,r,,、,f↑→,切削刚度↑→自振,↑,消除振动途径,消除产生振动的条件,改善工艺系统动态特性,采用各种消振减振装置,强迫振动,自激振动,提高工艺系统刚度,,增大工艺系统阻尼,动力式减振器,阻尼减振器,冲击式减振器,动力减振装置,固体摩擦式减振器结构简图,,1 -飞轮 2 -毂盘 3 -扭转轴 4-螺帽 5 -弹簧 6 -摩擦盘,106,
- 温馨提示:
1: 本站所有资源如无特殊说明,都需要本地电脑安装OFFICE2007和PDF阅读器。图纸软件为CAD,CAXA,PROE,UG,SolidWorks等.压缩文件请下载最新的WinRAR软件解压。
2: 本站的文档不包含任何第三方提供的附件图纸等,如果需要附件,请联系上传者。文件的所有权益归上传用户所有。
3.本站RAR压缩包中若带图纸,网页内容里面会有图纸预览,若没有图纸预览就没有图纸。
4. 未经权益所有人同意不得将文件中的内容挪作商业或盈利用途。
5. 装配图网仅提供信息存储空间,仅对用户上传内容的表现方式做保护处理,对用户上传分享的文档内容本身不做任何修改或编辑,并不能对任何下载内容负责。
6. 下载文件中如有侵权或不适当内容,请与我们联系,我们立即纠正。
7. 本站不保证下载资源的准确性、安全性和完整性, 同时也不承担用户因使用这些下载资源对自己和他人造成任何形式的伤害或损失。