影响表层金属力学物理性能的工艺因素及其改善措施
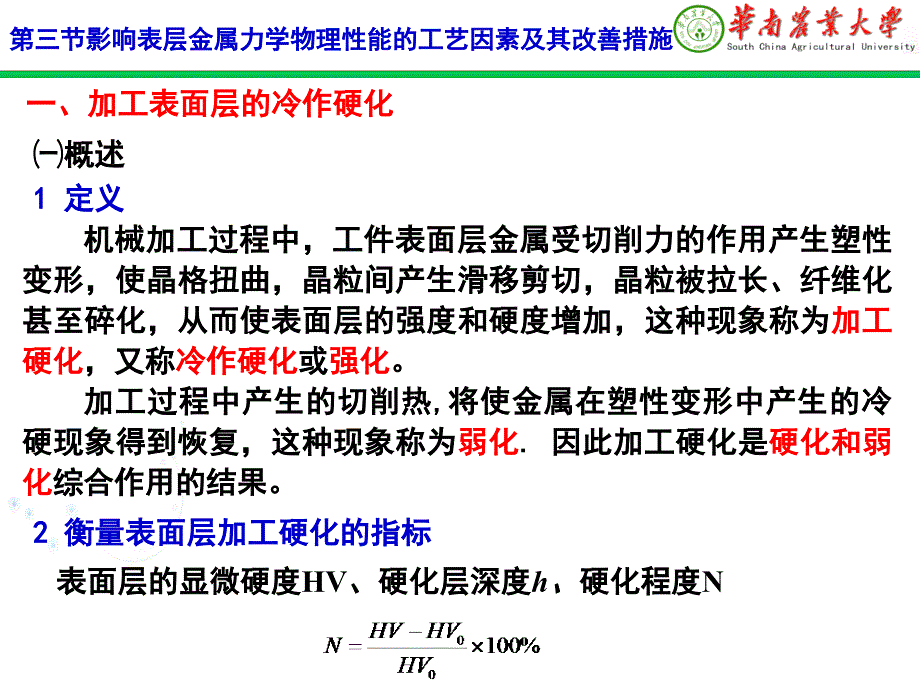


《影响表层金属力学物理性能的工艺因素及其改善措施》由会员分享,可在线阅读,更多相关《影响表层金属力学物理性能的工艺因素及其改善措施(15页珍藏版)》请在装配图网上搜索。
1、单击此处编辑母版标题样式,,单击此处编辑母版文本样式,,第二级,,第三级,,第四级,,第五级,,,*,第三节影响表层金属力学物理性能的工艺因素及其改善措施,一、加工表面层的冷作硬化,,㈠概述,,1,定义,机械加工过程中,工件表面层金属受,切削力,的作用产生塑性变形,使晶格扭曲,晶粒间产生滑移剪切,晶粒被拉长、纤维化甚至碎化,从而使表面层的强度和硬度增加,这种现象称为,加工硬化,,又称,冷作硬化,或,强化,。,,加工过程中产生的切削热,,,将使金属在塑性变形中产生的冷硬现象得到,恢复,这种现象称为,弱化,.,因此加工硬化是,硬化和弱化,综合作用的结果。,,2,衡量表面层加工硬化的指标,表面层的显
2、微硬度,HV、,硬化层深度,h、,硬化程度,N,,一、加工表面层的冷作硬化,㈡影响切削加工表面冷作硬化的因素,主要取决于产生塑性变形的力、变形速度和变形时的温度。塑性变形越大,则硬化越严重;切削温度升高,弱化作用加强。,,1,切削用量影响,,1,),f↑→,切削力↑→塑性变形↑→冷硬程度↑,,2,)切削速度影响复杂(力与热综合作用结果),,3,)切削深度影响不大,2,刀具几何形状的影响,,1,)切削刃钝圆半径,rε,↑,,冷硬程度↑;,,2,)其他几何参数影响不明显;,,3,)刀具磨损影响显著(力和热互相作用),,3,工件材料,,碳钢,塑性愈大的材料,切削后的冷硬现象愈严重(材料塑性↑,→,冷
3、硬倾向↑)。有色金属,熔点低,容易弱化,其冷作硬化现象比钢材轻得多。,,,一、加工表面层的冷作硬化,㈢影响磨削加工表面冷作硬化的因素,1,工件材料,,1,)材料塑性↑→ 冷硬倾向↑;,,2,)材料导热性↑→ 弱化倾向↓ → 冷硬倾向↑,,2,磨削用量,,1,)磨削深度↑→冷硬程度↑;,,2,)磨削速度↑→冷硬程度↓;,,3,)工件转速↑→冷硬程度↑:,,4,)纵向进给量影响复杂。,,3,砂轮,,1,)砂轮粒度↑→冷硬程度↓;,,2,)砂轮硬度、组织影响不显著。,,一、加工表面层的冷作硬化,1,表面层显微硬度,HV,测量,:用显微硬度计,,㈣冷作硬化的测量方法,2,加工硬化层深度,h,测量,:,
4、,1,)金相法,,2,),X,光法,,3,)测量显微硬度法,,4,)再结晶法,,5,)脆性涂料法,,6,)激光全息摄影法,,二、表面金属的金相组织变化,,㈠机械加工表面金相组织的变化,,,机械加工过程中,工件的加工区及其邻近的区域,温度会急剧升高,当温度超过工件材料金相组织变化的临界点,会发生金相组织变化。,,磨削加工中,由于磨削比压大,磨削速度高,磨削热大部分传给工件,使工件表面达到很高的温度。高温使表层的金相组织产生变化,造成表层金属硬度下降,工件表面呈现氧化膜颜色,这种现象称为,磨削烧伤,。,,1,回火烧伤,,磨削时,如果工件表面温度未超过相变温度(碳钢的相变温度为,720,),但超过了
5、马氏体的转变温度(中碳钢为,300,),则表层原来的马氏体组织将产生回火现象而转变为硬度较低的回火组织(索氏体或托氏体),这种现象称为,回火烧伤,。,,第三节 影响表层金属力学物理性能的工艺因素及其改善措施,,2 淬火烧伤,磨削时,如果工件表面层温度超过相变温度,,,马氏体转变为奥氏体。如果这时有充分的冷却液,则表层将急冷形成二次淬火马氏体,硬度比回火马氏体高,但很薄,只有几个微米厚,其下为硬度较低的回火索氏体和屈氏体。由于二次淬火层极薄,表面层总的硬度是降低的,这种现象称为,淬火烧伤,。,二、表面金属的金相组织变化,㈠机械加工表面金相组织的变化,,3,退火烧伤,磨削时,如果工件表面层温度超过
6、相变温度,马氏体转变为奥氏体。若此时无冷却液,表层金属在空气冷却比较缓慢而形成退火组织,硬度和强度均大幅度下降,这种现象称为,退火烧伤,。,,,二、表面金属的金相组织变化,㈡改善磨削烧伤的工艺途径,,1,正确选择砂轮,,硬度太高的砂轮,容易产生烧伤,因此采用软砂轮且有弹性的粘接剂。,,,2,合理选择磨削用量,,1,)砂轮转速↑→ 磨削烧伤↑,,2,)磨削背吃刀量,ap,↑→,磨削烧伤↑,,3,)进给量,f,↑→,磨削烧伤↓,,4,)工件速度,↑→,磨削烧伤↓,3,改善冷却条件,,采用内冷却法→磨削烧伤↓,,,4,开槽砂轮,,在砂轮上开槽,使砂轮间断磨削,工件受热时间短,金相组织来不及转变,且改
7、善了散热条件,可防止烧伤和裂纹。,,,,三、表层金属的残余应力,,在机械加工过程中,当表层金属组织发生,形状,变化、,体积,变化或,金相组织,变化时,将在表面层的金属与其基体间产生相互平衡的残余应力。,㈠表层金属产生残余应力的原因,,1,冷态塑性变形引起的残余应力,------,表层产生残余压应力,,切削或磨削过程中,工件表面层受到后刀面或砂轮磨粒的挤压和摩擦及受前刀面的撕裂作用,表面层产生伸长塑性变形,此时基体金属仍处于弹性变形。切削或磨削过后,基体金属趋于恢复,但受到已产生塑性变形的表面层金属的牵制,从而在表面层产生残余压应力,里层则产生与其平衡的残余拉应力。,,,冷态塑性变形主要是力的作
8、用,它使表层产生残余压应力。,,第三节 影响表层金属力学物理性能的工艺因素及其改善措施,,1,冷态塑性变形引起的残余应力,滚压、喷丸等表层强化工艺时,也是冷态塑性变形。表面几何形状上的波峰被压平并挤到两边的波谷中,晶格被拉伸扭曲,晶粒被拉长,表层产生,残余压应力,。,㈠表层金属产生残余应力的原因,,切削时表面残余应力分布,磨削时表面残余应力的分布,,,三、表层金属的残余应力,㈠,表层金属产生残余应力的原因,,2,热态塑性变形引起的残余应力,-----,表层产生残余拉应力,切削或磨削过程中,工件加工表面在切削或磨削作用下产生热膨胀,此时基本金属温度较低,因此,表面层产生压应力。,,当切削或磨削结
9、束时,工件表面温度下降发生收缩,由于表层已产生热态塑性变形并受到基体的限制,故而产生,残余拉应力,。,热态塑性变形主要是热的作用,它使表层产生残余拉应力。,磨削时表面残余应力的分布,,,三、表层金属的残余应力,㈠表层金属产生残余应力的原因,,3,金相组织变化引起的残余应力,,切削或磨削过程中,若工件加工表面温度高于材料的相变温度,则会引起表面层的金相组织变化。,,不同的金相组织有不同的密度,马氏体的密度,7.75,,奥氏体的密度,7.96,,在各种金相组织中,马氏体密度最小(比容最大),奥氏体最大(比容最小)。,,当金相组织发生变化时,由于密度不同,体积就要变化,如果体积膨胀,则受到里层的限制
10、,而产生残余压应力;反之,如果体积缩小,则产生残余拉应力。,,机械加工后表面层的残余应力是力引起的冷态塑性变形、热引起的热态塑性变形和金相组织变化这三者的综合结果,在一定条件下,某种或两种因素起主导作用,决定了工件表层残余应力的状态,.,,三、表层金属的残余应力,㈡影响车削表层残余应力的工艺因素,1,切削用量,,1,)低速,-,残余拉应力,高速,→,残余压应力(,45#,钢,热应力起主导作用),,2,),f↑→,塑性变形和切削热↑→残余压应力↑,,3,)切削深度影响不显著,,2,刀具,,1,)前角,+→,-,残余拉应力↓;用很大负前角时,会产生残,,余压应力,采用正前角刀具,产生残余拉应力。,
11、,2,)刀具磨损↑→残余压应力↑。,,3,工件材料,,材料塑性↑→残余压应力↑,,,三、表层金属的残余应力,㈢影响磨削残余应力的因素,1,磨削用量,,1,)砂轮速度↑→残余拉应力↑;,,2,)工件速度和进给量↑:砂轮和工件热作用时间缩短,塑性变形起主导作用,表面产生残余压应力;,,3,)磨削深度,ap,↓→,残余拉应力↓,减小到一定程度,得到低残余应力。,,㈡影响磨削残余应力的工艺因素,2,工件材料,,工件材料强度越高,导热性越差,塑性越低,磨削时易产生残余拉应力。,,㈣工件最终工序加工方法的选择,,工件表面的残余应力将直接影响机器零件的使用性能,一般工件表面残余应力的数值和性质主要取决于工件
12、最终加工工序的加工方法。,,选择工件最终工序的加工方法,要考虑该零件的具体工作条件及零件可能产生的破坏形式。,,零件在,交变载荷,的作用,最终工序选择能产生,压应力,的加工方法。,,两,相对滑动,的零件,从提高零件抵抗滑动摩擦引起的磨损考虑,最终工序应选择产生,拉应力,的加工方法。,,两,相对滚动,的零件,从提高零件抵抗滚动摩擦引起的磨损考虑,最终工序应选择能在表面层下深处产生,压应力,的加工方法。,,四、表面强化工艺,,,表面强化,工艺中几种最重要的加工方法有化学热处理(渗碳、渗氮和渗铬)、电镀和表面机械强化。,,,表面机械强化,是通过冷压加工方法使表面层金属产生冷态塑性变形,以降低表面粗糙度值,提高表面硬度,并在表面层产生,残余压应力,的表面强化工艺。,1.喷丸,2.滚压加工,3.挤孔(胀孔),第三节 影响表层金属力学物理性能的工艺因素及其改善措施,,
- 温馨提示:
1: 本站所有资源如无特殊说明,都需要本地电脑安装OFFICE2007和PDF阅读器。图纸软件为CAD,CAXA,PROE,UG,SolidWorks等.压缩文件请下载最新的WinRAR软件解压。
2: 本站的文档不包含任何第三方提供的附件图纸等,如果需要附件,请联系上传者。文件的所有权益归上传用户所有。
3.本站RAR压缩包中若带图纸,网页内容里面会有图纸预览,若没有图纸预览就没有图纸。
4. 未经权益所有人同意不得将文件中的内容挪作商业或盈利用途。
5. 装配图网仅提供信息存储空间,仅对用户上传内容的表现方式做保护处理,对用户上传分享的文档内容本身不做任何修改或编辑,并不能对任何下载内容负责。
6. 下载文件中如有侵权或不适当内容,请与我们联系,我们立即纠正。
7. 本站不保证下载资源的准确性、安全性和完整性, 同时也不承担用户因使用这些下载资源对自己和他人造成任何形式的伤害或损失。