车削中心热误差实时补偿应用实例
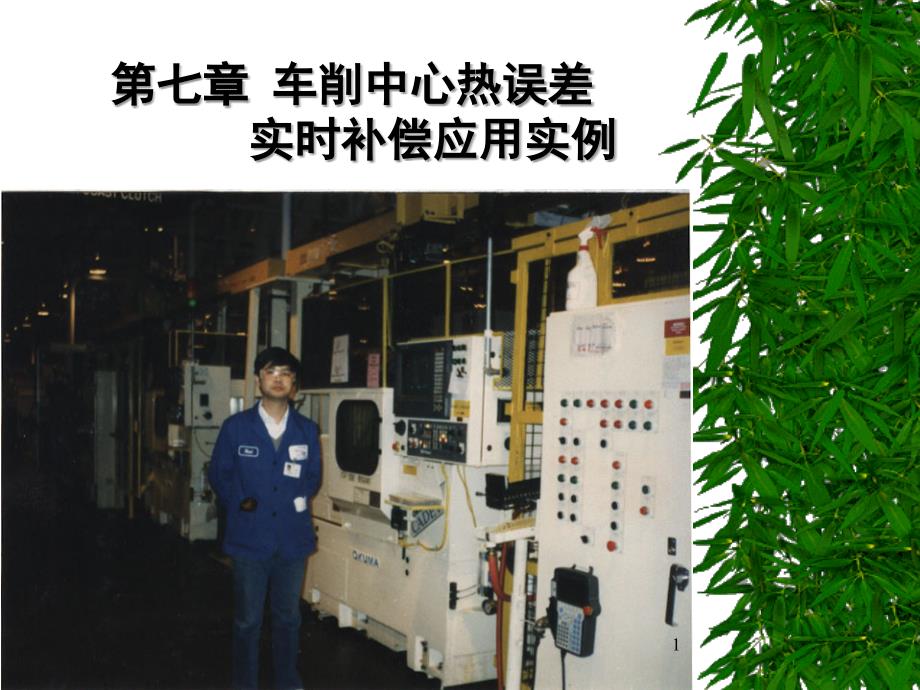


《车削中心热误差实时补偿应用实例》由会员分享,可在线阅读,更多相关《车削中心热误差实时补偿应用实例(34页珍藏版)》请在装配图网上搜索。
1、单击此处编辑母版标题样式,单击此处编辑母版文本样式,第二级,第三级,第四级,第五级,*,*,*,第七章 车削中心热误差 实时补偿应用实例,1,7.1 问题的提出,7.2 温度场、热误差的检测和分析,7.2.1 温度传感器布置及试验系统的建立,7.2.2 热误差测量试验,7.2.3 一系列影响热误差的单因素试验,7.3 热误差模态分析,7.4 热误差建模,7.5 补偿控制系统及补偿效果检验,7.6 多台同类车削中心热误差实时补偿,7.6.1,适合于多台同类车削中心的热误差鲁棒建模,7.6.2,适合于多台同类车削中心的热误差补偿系统,7.6.,3 多台同类车削中心的热误差补偿结果,2,7.1 问题
2、的提出,提出课题的工厂有150台车削中心,,在应用补偿技术前,,由于机床热变形而产生以下三个主要问题:(1)随着加工的进行,工件直径尺寸越来越小,每加工大约10个工件需调整机床一次,特别在加工初期工件尺寸变化得更快,使得操作工劳动强度增大,且一有疏忽就会造成废品;(2)每次停机后加工的第一个工件尺寸有个跳跃,绝大多数成为废品;(3)每班在机床切削加工前需预热即空转(包括主轴运转、,拖板运动、冷却液流动等)半小时以上,以达到机床初步热平衡,这样既浪费了电力、损耗了机床,又降低了机床利用率。,以150多台车削中心计算,由机床热变形造成的损失是相当大的。故极有必要开发能满足工厂实际生产要求的高精度、
3、低成本热误差补偿系统来修正主轴(或工件)与切削刀具之间的热漂误差,以提高机床加工精度、降低废品、增加生产效率和经济效益。,3,7.2 温度场、热误差的检测和分析,7.2.1 温度传感器布置及试验系统的建立,为了检测机床的温度场,按下图所示在车削中心上安装了16个温度传感器。依其在车削中心上的位置可分为5组。,(1)两个传感器(编号0和1)用于测量主轴箱的温度;,(2)四个传感器(25)用于测量丝杆螺母的温度;,(3)两个传感器(6、7)用于测量冷却液温度;,(4)一个传感器(8)用于测量室温;,(5)七个传感器(915)用于测量床身温度。,上图为热误差测量示意图。固定在刀架上的两个位移传感器用
4、来测量,X,向(#17)和,Z,向(#16)的主轴相对于刀架的热漂误差。由于工件较短,忽略偏角误差。,4,7.2.2 热误差测量试验,首先进行模拟切削加工循环过程的试验,但只是机床主轴旋转、拖板移动和冷却液流动而无切削加工,亦即空切削。机床先运行3.25小时,接着模拟中午休息停机1小时,然后再运行3.5小时后停机1小时。机床热误差和温度变化如下图所示。,观察试验数据在一般意义下很难解释图中热误差曲线的一些变化过程。当机床温度升高时,主轴和位移传感器之间的间隙在减小。3.25小时后,当机床停机冷却时,一般认为间隙应作相反的变化。但是,误差曲线显示间隙仍以相当大的速度减小。午休后,开机使机床温度再
5、次升高。一般认为间隙应象开始时一样减小,然而,曲线以很快的速度向正方向变动。这种现象同样发生在3.5小时后的第二次冷却中。因此,很有必要对机床热源进行更深入的分析和研究。,5,7.2.,3 一系列影响热误差的单因素试验,根据机床结构及工作情况分析可得,该车削中心的热误差主要受3个因素的影响:冷却液温度变化、主轴旋转发热和拖板运动造成丝杆和螺母发热。单因素试验研究是为了了解各单个因素对机床热误差的不同影响。为此,进行了以下三个试验:,(1),冷却液循环单因素试验,在这个试验里,机床温升只由冷却液流动引起。下图表示了热误差的变化过程。结果显示,当冷却液温度升高时,工件半径(#17,X,方向)减小,
6、误差约为21,m。,工件长度(#16,Z,方向)也减小,误差约为15,m。,从图中还可看出达到热稳定状态约需2小时。,冷却液流动单因素试验的热误差,6,(2)主轴旋转单因素试验,在这个试验里,机床温升只由主轴先以600,r/min,旋转2小时,再以1800,r/min,旋转2小时引起。下图表示了热误差的变化过程。结果显示,当主轴箱温度升高时,工件半径(#17,X,方向)减小,误差约为23,m。,工件长度(#16,Z,方向)也减小,误差约为40,m。,从图中还可看出达到热稳定状态约需3.5小时。,主轴旋转单因素试验的热误差,7,(3),拖板移动单因素试验,下图表示了只由拖板在,Z,和,X,二个方
7、向以3,m/min,进给速度运动引起机床温升的热误差变化过程。结果表明,当丝杆螺母温度升高时,工件半径(#17,X,方向)增大,误差约为7,m。,工件长度(#16,Z,方向)也增大,误差约为12,m,,达到,X,方向丝杆螺母热稳定状态只需1小时。,拖板移动单因素试验的热误差,8,热特性分析结果,在热特性分析的基础上,机床热误差测量试验图的曲线就比较容易解释了。以半径(,X,方向)误差为例。当机床开始工作时,冷却液、主轴箱和丝杆螺母温升对误差的影响彼此基本抵消。因此,前60分钟曲线几乎是平的。当丝杆螺母达到热稳定状态后,冷却液和主轴箱温升引起半径误差朝负向变化。当机床开动3.25小时后冷却时,丝
8、杆收缩,但由于冷却液和主轴箱的热容量较大故其温度变化不大。因此,半径误差继续朝负向变化。当机床温度重新升高时,丝杆螺母膨胀导致半径误差朝正向变化达到稳定状态。因此,热源分析很好地解释了这些热现象。,但是,为什么当冷却液温度升高、主轴箱温度升高和丝杆螺母温度降低时半径误差减小?为了更好地估计由这些热源引起的热误差,温度传感器应如何布置?下节介绍的热误差模态分析是解决这些问题的一个有效方法。,9,7.3 热误差模态分析,经过对工厂的该车削中心的机械结构、工作情况、热源及热变形的研究和分析得出关于影响被加工工件径向尺寸(,X,轴方向),有四个方面的主要热变形误差模态。,(1)基座弯曲模态,由于机床基
9、座被用作为冷却液储存箱,故冷却液温度变化将直接造成机床床身上下温度不均匀变化而引起床身弯曲变形。当机床工作时,床身温度(包括冷却液温度)升高、床身上下温度差值增大且测得上部温度低于下部温度,所以产生如图所示的向上热弯曲模态,使得刀具和被加工工件的径向距离减小最终导致被加工工件的径向尺寸变小。这个现象和试验数据相吻合。从冷却液流动单因素试验的热误差图中可得到这热误差模态的时间常数(此时间常数定义为达到稳定热误差63.2%的时间)大约为40,min。,根据床身上部温度(测床身温度的温度传感器#15)和下部温度(测冷却液温度的温度传感器#6)的差值可有效地估计这一基座弯曲模态。,10,(2)基座膨胀
10、模态,由于热传递的作用,在机床工作后,床身上部温度和下部温度会一起逐渐地提高而使基座(床身)膨胀。其基座横向膨胀模态如图所示。床身横向膨胀使被加工工件径向尺寸变大。基座膨胀模态的时间常数和弯曲模态的时间常数基本相同。根据床身上部温度(温度传感器#15)和下部温度(温度传感器#6)的平均值可有效地估计这一基座膨胀模态。,11,(3),X,轴丝杆膨胀模态,由于,X,轴拖板移动,使得,X,轴丝杆螺母的温度上升而产生丝杆热伸长。如图所示,因为推力轴承安装在丝杆的前(右)端,故丝杆热伸长时推动螺母往后(左)移动使得刀具和被加工工件的径向距离变大最终导致被加工工件的径向尺寸也变大。从拖板移动单因素试验的热
11、误差图中可得这热误差模态的时间常数大约为20,min。,由于螺母上容易安装温度传感器,故可用螺母(温度传感器#4)代替丝杆温度来估计这一热误差。,12,(4)主轴箱体膨胀模态,如图所示,来自主轴旋转的热将引起主轴箱体朝着垂直向上的方向膨胀。因为刀架拖板的导轨面是倾斜的(角度为,),故主轴箱体膨胀量,L,将会造成被加工工件径向尺寸误差,r=,L*Sin,(,此,为40,o,)。,从主轴旋转单因素试验的热误差图中可得主轴箱体膨胀模态的时间常数大约为40,min。,对于这一热误差模态,最好的温度传感器安置点是主轴箱提上接近主轴点,如图中温度传感器#1。,13,通过热误差模态的分析,更进一步认识了机床
12、热变形对加工精度的影响程度并且比较清楚地可得出在原先的16个温度传感器中有4个很关键,用它们可较简便地但精度也可满足地估计所研究机床的热误差(具体应用还得通过温度传感器布置策略来论证和选用,见下节)。它们是:,(1)温度传感器 6#测量冷却液温度(床身下部温度);,(2)温度传感器 15#测量床身温度(床身上部温度);,(3)温度传感器 4#测量,X,轴螺母温度;,(4)温度传感器 1#测量主轴(箱)温度。,14,7.4 热误差建模,经检测和分析,对于所研究的车削中心,与机床运动位置有关的几何误差不大于10,m,,而与机床温度有关的热误差(大约40,m),占了总误差的75%,故本研究只考虑热误
13、差的建模和补偿。,热误差最主要应为机床温度分布的函数,故机床类型、大小、结构,加工工件材料、形状、大小,刀具材料、形状,等等因素都间接通过机床温度分布来影响机床热变形。故热误差模型的一般形式可为:,其中:,T,为热误差;,c,0,c,i,c,ij,为模型的温度系数;,T,i,,,T,j,为温度变量。,热误差建模一般过程为:(1)采集机床各关键点温度数据和相应时间的热误差数据;(2)选择热误差模型的阶数;(3)使用最小二乘拟合法确定参数;(4)计算拟合残差。如精度不够,提高模型阶数重新拟合直至符合要求。,本研究考虑到工厂实际使用方便,热误差模型估计式设定为线性模型。另外,为使建模条件接近实际加工
14、条件及在建模过程中不影响工厂生产,实际加工后的工件尺寸误差被用为建模数据。,在机床关键温度点的优化选择中,根据优化布置策略,先后使用了主因素策略、互不相关策略、最近线性策略、最少布点策略等,获得了与上节所述的热变形模态分析中得出一致的在车削中心上的四个关键温度点,并用于热误差建模。最终从16个温度传感器减少到仅使用4个。,T,15,右上图为机床四个关键点温度变化。右下图为机床热误差变化和用最小二乘拟合法进行的建模分析图,从图中看出估计模型拟合得较好,残差小于10,m,,可满足被加工工件尺寸公差24,m,m,的精度要求。,16,求得的热误差估计模型为(本例仅考虑尺寸敏感方向,其它同理可得):,T
15、x,=28.2-4.2T,c,-2.7T,n,-1.5T,s,+7.9T,b,其中:,T,c,、,T,n,、,T,s,和,T,b,分别为冷却液温度、,X,轴丝杆螺母、主轴,温度和床身温度。故误差数学模型为:,W,x,=,st,x,=,Tx,=28.2-4.2T,c,-2.7T,n,-1.5T,s,+7.9T,b,17,7.5 补偿控制系统及补偿效果检验,7.5.,1 热误差补偿系统,本研究补偿系统使用原点平移法,因为这种补偿系统既不影响坐标值,也不影响,CNC,控制器上执行的工作程序。补偿系统由微机结合机床控制器构成,流程框图见下图。工作过程和功能如下。首先通过布置在机床上的温度传感器实时采集
16、机床温度信号,经放大等预处理后再通过,A/D,板进入微机。微机根据预先建立的热误差数学模型结合实时采集的机床温度值运算出补偿值并把补偿值送入机床控制器。控制器根据补偿值实时控制刀架的附加进给运动来修正误差、提高机床加工精度。位移传感器(在实际生产补偿加工过程中不用)用于在空切削中检测机床热误差(由机床热变形引起的主轴相对于刀具的漂移),并将热误差数据结合相对应的机床温度数据进行建模。,18,7.5.,2 补偿效果检验,关于补偿效果检验,先使用位移传感器测量主轴热漂误差,然后再进行实际切削检验。,(1)主轴热漂测量,与前述主轴热误差的检测一样的设置,检验补偿效果的主轴热漂测量是在空切削中,使用位移传感器测量主轴和刀具之间的热漂误差。下图为主轴热漂测量结果。从图中可得,经补偿,半径方向热漂从25,m,以上降低到大约7,m,,降低热误差72%;轴向热漂从36,m,以上降低到8,m,,降低热误差78%。主轴热漂测量结果表明经补偿机床加工精度大大提高。,19,(2)实际切削加工结果,下图表示了使用本误差补偿系统所得的实际切削补偿结果。从图中可见,经过补偿,工件直径尺寸误差从大于35,m,以上降低
- 温馨提示:
1: 本站所有资源如无特殊说明,都需要本地电脑安装OFFICE2007和PDF阅读器。图纸软件为CAD,CAXA,PROE,UG,SolidWorks等.压缩文件请下载最新的WinRAR软件解压。
2: 本站的文档不包含任何第三方提供的附件图纸等,如果需要附件,请联系上传者。文件的所有权益归上传用户所有。
3.本站RAR压缩包中若带图纸,网页内容里面会有图纸预览,若没有图纸预览就没有图纸。
4. 未经权益所有人同意不得将文件中的内容挪作商业或盈利用途。
5. 装配图网仅提供信息存储空间,仅对用户上传内容的表现方式做保护处理,对用户上传分享的文档内容本身不做任何修改或编辑,并不能对任何下载内容负责。
6. 下载文件中如有侵权或不适当内容,请与我们联系,我们立即纠正。
7. 本站不保证下载资源的准确性、安全性和完整性, 同时也不承担用户因使用这些下载资源对自己和他人造成任何形式的伤害或损失。
最新文档
- 踏春寻趣 乐享时光——春季旅游踏春出游活动
- 清明假期至安全不缺席风起正清明安全需守护
- 全国党员教育培训工作规划
- XX中小学公共卫生培训树立文明卫生意识养成良好卫生习惯
- 小学生常见传染病预防知识培训传染病的预防措施
- 3月18日全国爱肝日中西医结合逆转肝硬化
- 肝病健康宣教守护您的肝脏健康如何预防肝炎
- 垃圾分类小课堂教育绿色小卫士分类大行动
- 中小学班主任经验交流从胜任到优秀身为世范为人师表 立责于心履责于行
- 教师数字化转型理解与感悟教师数字化转型的策略与建议
- 团建小游戏团建破冰小游戏团队协作破冰游戏多人互动
- 教师使用deepseek使用攻略让备课效能提升
- 办公室会议纪要培训会议内容会议整理公文攥写
- 党员要注重培塑忠诚奋斗奉献的人格力量
- 橙色卡通风儿童春季趣味运动会