双耳止动垫圈倒装复合模设计说明书要点
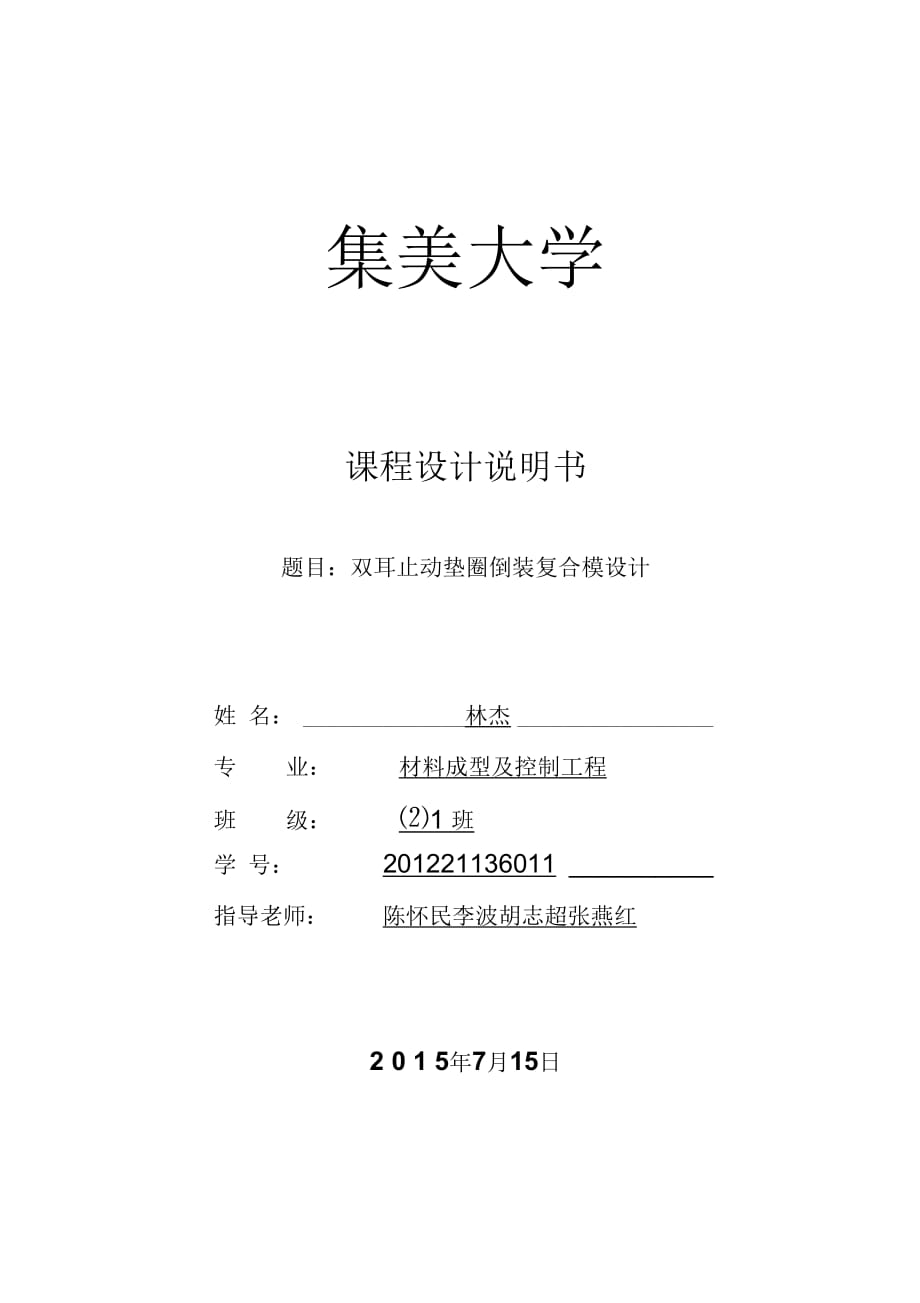


《双耳止动垫圈倒装复合模设计说明书要点》由会员分享,可在线阅读,更多相关《双耳止动垫圈倒装复合模设计说明书要点(37页珍藏版)》请在装配图网上搜索。
1、集美大学 课程设计说明书 题目:双耳止动垫圈倒装复合模设计 姓 名: 林杰 专 业: 材料成型及控制工程 班 级: ⑵1 班 学 号: 201221136011 指导老师: 陈怀民李波胡志超张燕红 2 0 1 5年7月15日 双耳止动垫圈倒装复合模设计 集美大学 专业课程设计任务书 ——材料成型及控制工程专业一一 设计题目: 双耳止动垫圈倒装复合模 设计任务:设计一简单冲压零件,并根据该零件设计一副冲压模具。 制件年产量:50万件 完成的任务: 1 .冲压工艺过程卡一份; 2 .产品零件图一份; 3 .冲压模具装配及模具成形零件工程图各一份; 4
2、 .设计说明书一份。 时间安排: 1 .借资料、产品的结构设计及绘制零件图;( 1天) 2 .确定零件冲压工艺方案,填写冲压工艺过程卡;( 1天) 3 .零件工艺性分析及冲压工艺方案的确定;毛坯排样方案设计及材料利用率计算;冲裁力 及压力中心计算;选择压力设备;模具总体结构设计,包括送料方式、卸料和出件方式、 凹模板外形尺寸的计算、其它模板尺寸的确定和模架的选择;凸、凹模零件设计,包括 刃口尺寸计算、凸模结构及凹模型腔结构设计;卸料和顶件装置设计;模具结构三维设 计。(3天) 4 .绘制模具结构装配图、模具成型零件工程图;( 2天) 5 .编写设计说明书;(2天) 6 .答辩。(
3、1天) 参考书目: [1]翁其金.冲压工艺及冲模设计[M].北京:机械工业出版社, 2004 [2]黄毅宏.模具制造工艺[M].北京:机械工业出版社, 2004 [3]王新华.冲模结构图册[M].北京:机械工业出版社, 2004 [4]陈锡栋.实用模具设计简明手册[M].北京:机械工业出版社,2001 [5]郑家贤.冲压工艺与模具设计实用技术 [M].北京:机械工业出版社, 2005 [6]杨玉英.实用冲压工艺模具设计手册 [M].北京:机械工业出版社, 2005 指导教师: 2015年07月15日 材料成型及控制工程 2012 级 1211 班 学生: 学号: 201
4、221136011 2015年 07月15日 双耳止动垫圈倒装复合模设计 [摘要]本设计是对双耳止动垫圈的冲孔一落料复合模的设计, 完成的内容为:对模具 在工业生产中的作用,模具发展历史与现状,未来模具的发展前景做了概述。进行零件 的形状、尺寸、精度工艺分析,确定合理的工艺方案。确定毛坯尺寸,合理排样,计算 材料利用率,绘制排样图,并计算冲裁力、推件力、卸料力,确定压力中心。确定凸、 凹模间隙,计算落料、冲孔的刃口尺寸。确定凸模、凹模和凸凹模的结构,并绘制零件 图,设计定位,压料、卸料、出件零部件,选择模架标注紧固件。最后绘制模具非标准 零件图,用Solidworks画出三维装配图,并在
5、 AutoCAD对装配图进行修改。本设计运 用模具使钢料产生塑性变形,获得最终需要的零件,这是一种少切削、无切削、多工序 重合的生产方法,并且利用复合模生产零件,提高了生产效率,对相似工件的大批量生 产具有参考的作用。 [关键词]双耳止动垫圈;倒装复合模;凸凹模;弹性卸料 目录 引言 1 1 .零件工艺性分析及冲压工艺方案的确定 2 1.1 冲裁件造型 2 1.2 冲裁件工艺分析 2 1.3 冲压工艺方案的确定 3 2 .毛坯排样方案设计及材料利用率计算 4 2.1 排样方法的确定 4 2.2 布置方式的确定 4 3 .冲裁力及压力中心计算 6 3
6、.1 冲裁力的计算 6 3.2 其他冲压力计算 6 3.3 压力中心计算 6 4 .选择压力设备 8 5 .模具总体结构设计 9 5.1 送料方式 9 5.2 卸料和出件方式 9 5.3 凹模板外形尺寸的计算 1 0 5.4 其他模板尺寸的确定 1 0 5.5 模架的选择 1 1 6 .凸、凹模零件设计 13 6.1 刃口尺寸计算 1 3 6.2 凸凹模结构设计 14 6.3 凸模结构设计 1 6 6.4 凹模型腔结构设计 1 7 7 .卸料和顶件装置设计 1 7 7.1 卸料装置设计 1 8 7.2 推件装置设计
7、 1 9 8 .其他零件设计 2 1 8.1 模柄的设计 2 1 8.2 螺钉的选择 2 1 8.3 圆柱销的选择 2 1 9 .校核模具高度 2 2 10 .模具结构三维设计 2 3 工艺卡 2 5 结论 2 6 致谢 2 8 参考文献 2 9 双耳止动垫圈倒装复合模设计 引言 冷冲压式利用安装在压力机上的冲模对材料施加压力,使其产生分离或塑形变形, 从而获得所需要零件(俗称冲压件或冲件)的一种压力加工方法。因为它通常是在室 温下进行加工,所以称为冷冲压。 冲模是将材料加工成所需冲件的一种工艺装备。冲模在冷冲压中至关重要,一般 来说,不
8、具备符合要求的冲模,冷冲压就无法进行;先进的冲压工艺也必须依靠相应 的冲模来实现。由于冷冲压所用原材料多是表面质量好的板料或带料,冲件的尺寸公 差由冲模来保证,所以产品尺寸稳定、互换性好。 在工业生产中,尤其在大批量生产中应用十分广泛。相当多的工业部门都越来越 多地采用冷冲压加工产品零部件,如机械制造、车辆生产、航天航空、电子、电气、 轻工、仪表及日用品等行业。在这些工业部门中,冲压件所占的比重都相当大,不少 过去用铸造、锻造、切削加工方法制造的零件,现在已被质量轻,刚度好的冲压件所 代替。可以说,如果在生产中不广泛采用冲压工艺,,许多工业部门的产品要提高生 产率、提高质量、降低成本,进行产
9、品的更新换代是难以实现的。 我国经济的高速发展对模具行业提出了越来越多的要求,也为其发展提供了巨大 的动力。近十年来,我国模具工业已知以每年 15%右的增长速度快速发展。目前,我 国有3.5万余家冲压模具生产企业,100万〜120万冲压生产从业人员,全年产值达700 亿元人民币。随着我国经济的持续发展,我国模具产业必然将在良好的市场环境下得 到高速发展。 9 1 .零件工艺性分析及冲压工艺方案的确定 1.1 冲裁件造型 冲裁件为双耳止动垫圈 根据GB/T 855-1988,得到规格24mmi勺双耳止动垫圈尺寸。具体尺寸如图 1-1所 技术要求 L未注圆角R0
10、. 5; 2 .未注公差按照IT14制 造; 3 .去除断面毛刺,进行 平整处理口 图1-1双耳止动垫圈 1.2 冲裁件工艺分析 (1)材料 选用20号钢。20号刚属于优质碳素结构钢,具有较好的塑形,因此冲压成形性能 好。并且选用钢板时,应保证其表面质量与厚度公差。 由《实用冲压工艺及模具设计手册》表 1-9可得,牌号为SM400A勺20号钢 屈服强度 J =245Mpa,抗拉强度 % =410Mpa,屈强比;,/二b =0.598 (2)结构与尺寸 零件形状规则,但不对称。 零件孔边距5.5mm大于冲裁钢板要求的最小孔边距(2〜2.3mm);最小圆角 R=0.5mm大于
11、规定值(0.35t=0.35mm);凸出悬臂的宽度为20mm大于规定值(2t=2mn)。 适合冲裁加工。 (3)精度 零件精度按照GB/T 855-1988所规定的双耳垫圈尺寸,未注尺寸的公差根据 IT14 制定。小于普通冲裁所能达到的最大精度(IT11)。 综上,该零件具有良好的冲裁工艺性。 1.3 冲压工艺方案的确定 该零件包括落料、冲孔两个基本工序,可以采用以下三种工艺方案: (1)单工序模:先落料,再冲孔,分布冲压 (2)级进模:冲孔-落料连续冲压 (3)复合模:落料一冲孔同时冲压 其中方案一模具制造容易,且价格低,但生产效率低,难以完成 50万件的生产要 求;方案
12、二对条料宽度有严格要求,而本工件尺寸较小,一定情况下,为了能使用边 角料进行生产,不推荐方案二;若采用方案三,需校核凸凹模的最小壁厚要求。零件 最小壁厚为5.5mm大于凸凹模要求的最小壁厚值 (c> (1.5〜2) t ,即c>1.5〜2mm。 零件符合采用复合模进行生产的要求,最终确定冲压工艺方案为采用复合模进行生产。 2.毛坯排样方案设计及材料利用率计算 2.1 排样方法的确定 排样方法大致可以分为: (1)有废料排样(2)少废料排样(3)无废料排样 考虑到零件形状的特殊性,无法采用无废料排样。由于采用手工送料,无法精确 控制步距,出于保证冲裁件精度与模具寿命,确定排样方
13、法为有废料排样。 由《冲模设计速查手册》表3-28可得,板厚为1mm勺低碳钢材料的最小搭边值: 圆形件及 r>2t : a圆 1=0.8mm;丽=1.0mm 矩形件及边长L<50: a次g1= 1.2mm; a矩=1.5mm 2.2 布置方式的确定 . _ 2 冲裁件的实际面积 A = 1187.29mm 2 无法避免的结构废料A5 = 490.87mm 1.直排的排样方式 图2-1直排样图 8 = 80+2圆十2矩=(43+1 +1.5) mm = 45.5mm S = L0 +a 矢巨 1 =(60 + 1.2)mm =61.2mm
14、A BS 1187.29 45.5 61.2 100% =42.64% 即一个步距内的材料利用率为42.64%,材料利用率较低,由于工件呈L型,考虑 进行对排 2.对排的排样方式 图2-2对排样图 B = B0 +2父丽 +a矢g1 = (56+2m1+1.2)mm = 59.2mm S = L0 + (Do + a圆)sin45口 = 62.58+ (36+08 sin45nmm =88.6mm 2 A 2 1187.29 入 100% =45.27% BS 59.2 88.6 2 A 2 490.87 s=-A^=—90-8- 100% = 18.
15、72% BS 59.2 88.6 即一个步距内的材料利用率为45.27%,材料利用率已有提高,考虑到其中不可避 免的结构废料占18.72%,工艺废料仅为36.01%,总体上已满足要求。 故确定排样布置方式为直对排,条料宽度 B=60mm步距S=88.6mm材料利用率 为 45.27% 3 .冲裁力及压力中心计算 3.1 冲裁力的计算 落料周边长度L1 = 183.905mm;冲孔周边长度L2 = 78.540mm; 材料厚度t=imm 20号钢的抗拉强度0b=410Mpa 落料的冲裁力 F1 = L1kb =183.905 1 410N = 75401.05N : 75.4k
16、N 冲孔的冲裁力 F2 =L2t %=78.540 1 410N =32201.4N : 32.2kN 总冲裁力 F =F1 F2 = (75401.5 32201.4 N =107602.9N 107.6kN 3.2 其他冲压力计算 由《冲压工艺及冲模设计》表3-9可得,板厚为1mm的钢板, 卸料力系数Kx =0.04;推件力系数Kt =0.055 h 5 _ 洛料凹板内的工件数 Q =1;冲孔凹板内的工件数 n2 5 t 1 隹口料力 Fx =KxF[ =0.04 75401.05N =3016.04N : 3kN 推出落料件的推件力 FT1=n1KTF1=1 0.05
17、5 75401.05N =4147.06N : 4.1kN 推出冲孔废料的推件力 ^2=n2KtF2 =5 0.055 32201.4 =8855.39 N 8.9kN 由于本模具是采用弹性卸料装置和下出料方式的冲裁模 总冲裁力 FZ = F FX FT1 FT2 = (107602.9 3016.04 4147.06 8855.39)N 二 123621.39N : 123.6kN 3.3 压力中心计算 (单位:mm 线段 长度Li 压力中心点 (xi , yi ) L1 27.03 (-28.48 , 10) L2 20 (-42, 0) L3
18、 27.03 (-28.48 , -10) L4 7.07 (-13.32 , -13.32 ) L5 10.03 (-10 , -19.98 ) L6 20 (0,-20) L7 10.03 (10, -19.98 ) L8 78.54 (0, 0) L9 63.62 (7.06, 7.06) Xo n “ LiXi i :1 n 、Li i=1 27.03 x(-28.48)+20 父(-42)+ +63.62 >7.06 27,03 20 ……63.62 =-12.418mm 由上表可得 n 、Ly i m
19、n v L i 1 =-2.824mm 27,03 10 20 0 一……--63.62 7.06 10 0 ……7.06 即压力中心为(-12.418 , -2.824 ) 4 .选择压力设备 已知总冲压力FzT23.6kN 由于P之1.耳=1.2123. 6k=148.2tk,所以所选压力机的公称压力需大于 148.21kN 考虑到开式可倾压力机机身为可倾式结构,倾斜时便于冲压件或废料从模具上滑 下,可免去取件的步骤,有利于提高生产效率。并且开式的结构便于工人进行手动送 料等操作,故选择可倾压力机。 由《冲模设计速查手册》表7-10查得J23-16开式可倾压力机
20、的公称压力160k/N, 满足使用要求。故选择J23-16开式可倾压力计机,主要参数如下: 表4-1 J23-16压力机参数 项目 参数 公称压力 160KN 滑块行程 55mm 滑块行程次数 120 次/min 最大封闭高度 220mm 封闭高度调节量 45mm 滑块中心线至床身跑离 160mm 立柱距离 220mm 工作台尺寸 前后 300mm 左4 450mm 工作台孔尺寸 前后160mm左右240mm直径210mm 模柄孔尺寸 直径40mm深度60mm 5 .模具总体结构设计 复合模主要分为(1)正装复合模 (2)倒装复合模 其中
21、正装复合模适合用于冲制材料较软或板料较薄的平面度要求较高的冲裁,还 可以冲制孔边距较小的冲裁件,但冲孔废料被推出后落在凹模表面,生产的连续性较 低。而倒装复合模结构简单,又可以直接利用压力机的打杆装置进行推件,并且冲孔 废料可直接顺冲裁方向推出,效率较高。 考虑到所冲压白^零件厚度为1mm非薄板件,孔边距较大,平直度上也没有严格的 规定,并且要生产50万件,要求较高的生产效率,故确定采用倒装复合模进行生产。 5.1送料方式 由于零件形状简单,价格低廉,并且生产批量仅为 50万件,而进行自动送料的成 本较高,不符合生产实际的要求,故选定送料方式为手工送料。 1.1.1 导料方式的选择 导
22、料方式主要分为导料板与导料销,考虑到采用倒装复合模进行冲裁,并且要进 行弹性卸料,所以导料板不符合要求。导料销分为固定式和弹顶式,由于导料销的布 置位置离凹模刃口位置较远,所以选择导料方式为固定式导料销,并在凹模上开设避 让孔。 1.1.2 挡料方式的选择 挡料方式主要有固定挡料销、活动挡料销、回带式挡料销、侧刃,考虑到采用倒 装复合模进行冲裁,侧刃定距的方式不符合要求。由于导料方式采用导料销,为了便 于加工,挡料方式选择固定挡料销。 5.2 卸料和出件方式 5.2.1 卸料方式选择 卸料装置主要可以分为(1)固定卸料装置 (2)弹压卸料装置 其中固定卸料装置的卸料力大,卸料可靠,
23、适用于冲裁板料较厚 (t>0.5mm),平面 度要求不高的场合;弹压卸料装置的卸料力小,但它既起卸料作用,又起压料作用, 所得冲裁零件质量较好,平面度较高,适用于板料较薄的场合( t<1.5mm)。 双耳止动垫圈倒装复合模设计 综合考虑冲裁零件的要求,冲裁件尺寸较小,卸料力较小,弹压卸料装置完全能 够满足卸料力的要求,并且由于选择倒装复合模进行生产,提高生产效率的同时,导 致冲裁件的平直度受影响,故应选择弹压卸料装置,弥补其平直度。 确定卸料装置为弹压卸料装置。 5.2.2 出件方式选择 成型后冲孔废料卡在凸凹模的内孔中,成型件卡在凹模中 由于采用倒装复合模,卡在凸凹模内孔中
24、的冲孔废料由下次冲裁时的凸模推出, 不用布置推件装置。而对于卡在凹模内的成型件,必须布置推出装置进行推出。 为了保证成型件的平整与推件可靠,建议采用弹性推出与刚性推出相结合的方法, 一方面在推板上布置弹簧,冲裁时起到压料作用,保证从冲裁件的平整,并且在成型 后及时将冲裁件推出,避免用打杆推出时冲裁件从高处掉落在凹模上,影响冲裁件质 量与模具寿命,另一方面为了防止有时弹簧未能有效推出,冲裁件卡在凹模内,也要 在推板上布置打杆,以确保推件的可靠。 5.3 凹模板外形尺寸的计算 (1)由排样可知,垂直送料方向的凹模刃壁间最大距离 s=43mm 由《冲压工艺及冲模设计》表 3-13可得,材料厚
25、度t=1mm s=43mnW,凹模厚 度系数k=0.35 凹模厚度 H =ks =0.35 43mm = 15.05mm 所得凹模厚度较小,考虑到凹模强度与压力机的最小封闭高度,取凹模厚度 H=21mm (2)垂直于送料方向的凹模 宽度B=s + 3.5H =(43+3.5M21)mm=116.5mm (3)由《冲压工艺及冲模设计》表 3-12可得,材料宽度为60mm厚度为1mnW,凹 模孔壁至边缘的距离S2 =30mm 送料方向凹模长度L -S1 - 2s2 = (60 2 30) mm-120mm 初定凹模外形尺寸为 HX BX L=21X 116.5 X 120mm 5.4
26、 其他模板尺寸的确定 1 o 双耳止动垫圈倒装复合模设计 由于采用复合模进行生产,主要工作部分模板大致包括:凸模固定板、限位板、 凹模版、卸料板、凸凹模固定板。 根据凹模板的厚度H=21mmt致确定凸模固定板厚度为16mm限位板厚度为16mm 卸料板厚度为14mm凸凹模固定板厚度为16mm 5.5 模架的选择 根据国家标准,导柱模模架主要分为(1)中间导柱模架;(2)后侧导柱模架; (3)对角导柱模架;(4)四导柱模架 考虑到复合模对刚性与工作平稳度有较高要求,故后侧导柱模架不符合要求;冲 裁件形状规则简单,精度要求相对较低,四导柱模架精度远大于所要求的精度,并且 成本较
27、高,故也不符合要求。中间导柱模架与对角导柱模架都符合生产的要求,从中 选择中间导柱模架。 根据《中国模具设计大典》表 22.4-5中GB/T 2851-2008规定的中间导柱模架规 格。由凹模外形尺寸为 HX BX L=21X 116.5 X 120mm压力机最大封闭高度 220mm封 闭高度调节量45mm选定凹印S周界为125X 125mm参考闭合高度150— 190mm勺中间 导柱模架。 查得: 上模座规格 125X 125X35 (GB/T 2855.1-2008 ) 下模座规格 125 X125X45 (GB/T 2855.2-2008 ) 导柱规格 22 X180; 25X
28、180 (GB/T 2861.1-2008 ) 导套规格 22 X80X 33; 25 X80X 33 (GB/T 2861.3-2008) 由此,所有模板的规格尺寸与材料选用如下: 表5-1各模板尺寸表 (单位:mrm 模板 规格(LXBXH) 材料 上模座 125X125X35 HT200 垫板 125X125X20 T10 推杆固定板 125X 125X5 Q235 凸模固定板 125X125X 16 Q235 限位板 125X125X 16 45 凹模 125X125X21 Cr12Mov 卸料板 125X125X 14 45
29、 凸凹模固定板 125X125X 16 Q235 垫板 125X125X 16 Q235 下模座 125X125X45 HT200 推板 D80 45 1 10 6.凸、凹模零件设计 6.1 刃口尺寸计算 6.1.1 刃口加工方式选择 根据凸、凹模加工方式的不同,刃口尺寸的计算方法主要分为 (1)分开加工法 (2)配做法 考虑到分开加工法主要针对圆形或简单规则形状的冲裁件,并且模具的制造公差 小,模具制造困难,成本高,而配做法工艺简单,制造容易,模具的间隙由配制保证, 可适当放大基准件的制造公差,目前应用较为广泛。故确定加工方法为配做法。 6.1
30、.2 刃口尺寸计算 落料以凹模尺寸为基准,冲孔以凸模尺寸为基准。因模具为复合模,要同时进行 冲孔与落料。因此要分别进行落料凹模与冲孔凸模的尺寸计算。 由《冲模设计速查手册》表 3-35可得,厚度为1mmi勺20号钢的初始双面间隙取 值范围为 Zmin -0.100mm; Zmax -0.140mm (1)落料凹模与凸凹模外轮廓计算 磨损图 凹模尺寸图 凸凹模外轮廓尺寸图 图6-1凹模刃口计算图 由《冲压工艺及冲模设计》表3-5可得,尺寸20、42、25、36、R3的磨损系数x=0.5 由磨损图可知,磨损后变大的尺寸: % =(人1皿7与沪=(20-0.5 . 0.52)尸
31、=19.74胪 max 人2 =(儿2 - XA)节 max =(42.5-0.5x1) t/4 =42片 Ad3 =(Ad3max -XA)泸 =(25.42-0.5x0.84)f4 =25421 Ad4 = (Ad4max - X&)出 二(36-0.5 0.62)0.62/4 =35.69 0,6 磨损后变小的尺寸: Bd1 = (Bd1min +X&)-44 =(2.75 + 0.5x0.25)-0.25/4 =2.88;0.06 凸凹模外轮廓的尺寸, 按照凹模的实际尺寸配制,保证双面间隙为 0.100mm- 0.140mm (2)冲孔凸模与凸凹模
32、内轮廓计算 工件尺寸图 凸模尺寸图 凸巴模内轮,用尺寸图 磨损图 图6-2凸模刃口计算图 由磨损图可知,磨损后变小的尺寸: 0.100mm- Bp1 = (B*in +xA)-& = (25 + 0.5^0.52)-0.52/4 =25.260.13 凸凹模内轮廓的尺寸,按照凸模的实际尺寸配制,保证双面间隙为 0.140mm 6.2 凸凹模结构设计 (1)凸凹模最小壁厚校核 已知冲裁件的最小壁厚为5.5mm 根据《冲压工艺及冲模设计》表 3-14可得,冲裁材料厚度为1mm勺板料的凸凹模 的最小壁厚为2.7mm,故凸凹模的最小壁厚满足要求。 (2)凸凹
33、模结构形式与固定方式 考虑到凸凹模的轮廓非圆形,故选用凸缘式凸凹模,凸缘部分设计为矩形。由凸 凹模固定板进行定位于固定,凸凹模固定板与下模座间采用螺钉锁紧,销钉定位。 (3)凸凹模的长度计算 根据模具结构,凸凹模长度等于凸凹模固定板、卸料板厚度之和,在加上一定的 增加长度(凸模进入凹模的深度 0.5mm凸凹模固定板与卸料板之间的安全距离 11mm 即凸凹模的长度 h= (16+14+0.5+11) mm=41.5mm (4)凸凹模孔口结构形式 孔口结构形式主要分为:(1)全直壁型孔;(2)阶梯形直刃壁型孔;(3)斜刃 壁凹模 考虑到采用倒装复合模,冲孔废料要从凸凹模中向下推出,
34、故全直壁型孔不符合 要求;考虑到凸凹模使用一段时间后要进行刃磨,为了保证刃磨之后凸凹模孔口尺寸 不变,能继续进行生产,因此选定凸凹模孔口的结构形式为阶梯形直刃壁型孔。 根据《冲模设计速查手册》表 3-57,由材料厚度1mm得到刃口高度h=5〜10mm 取刃口高度h=5mm 4L.5 生 技术要求 L上下表市先毛林 2 .台肩部分圆角R0.2; 3 .凸凹模刃口尺寸按冲孔凸模 与凹模实际尺寸配制,保证双 面间隙值 0. 100mm—0. 140mm; 4 .建窗蘸火处理中 图6-3凸凹模结构图 6.3 凸模结构设计 (1)凸模结构形式 圆凸模的结
35、构形式主要分为标准圆凸模,凸缘式圆凸模,直通式凸模,由于冲裁 件内孔为圆形,形状简单,冲裁力不大,故凸缘式圆凸模与直通式凸模不符合要求。 考虑到标准圆凸模的配合段占据整个凸模长度的一半,将导致凸模固定板过厚,于是 决定不采用标准件,自行加工。凸模的固定采用凸模固定板配合段定位,凸模固定板 压紧的方式。 (2)凸模长度计算 根据模具结构,凸模长度等于凸模固定板、限位板、凹模厚度之和 由于凸凹模将会进入凹模板一段距离, 再加上一定的增加长度(凸模进入凹模的深度 0.5mn^ 即凸模长度 h= (16+16+21) mm=53.5mm (3)凸模强度与刚度校核 由于凸模直径为25mm冲
36、裁的板厚为1mm凸模的截面尺寸相对于板料厚度大了 很多,故不需要进行强度和刚度的校核。 其余竽 技术要求 L表面光滑无毛刺; 2.除刃耳部分外的圆角R0.2; 3.HRC60-64; 4,表面淬硬。 图6-4冲孔凸模结构图 6.4凹模型腔结构设计 1 .凹模结构形式与固定方式 凹模的结构主要分为整体式和镶拼式,由于冲裁件形状简单,尺寸较小,冲裁所 用的凹模选定为整体式。 由于采用整体式的凹模版,凹模板与上模座之间采用螺钉锁紧,销钉定位。 2 .凹模孔口的结构形式 凹模孔口的结构形式主要分为:(1)全直壁型孔;(2)阶梯形直刃壁型孔;(3) 斜刃壁凹模 考虑到采用倒
37、装复合模,凹模在上模,要从凹模内进行推件,故斜刃壁凹模、阶 梯形直刃壁型孔不符合要求,凹模孔口的结构形式选定为全直壁型孔。 其余序 技术要求 1.表面光滑无毛丸; 2.HRCSD-64. 图6-5凹模结构图 7 .卸料和顶件装置设计 7.1 卸料装置设计 7.1.1 弹性元件的选用 1)初定弹簧数量n 为确保卸料平稳,拟选n=4 2)计算每个弹簧的预压力Fy 已知卸料力Fx =3016.04N Fx 3016.04 z Fy = — = N = 754.01 N 755N n 4 3)由2Fy估算弹簧的极限工作载荷Fj Fj =2Fy =2 755N -151
38、0N 由《国际标准模具弹簧ISO10243》,初选SJM3216X44,其规格为: DH =3 2 m m Dd =1 6 m m h0 =4 4 m m h=1 6.3 四百=17118, bMh = 6.84mm n = 7 .5 4)计算弹簧预压缩量hy hj 755 16.3 hv = F mm = 7.16mm y y Fj 1718 5)校核 h = hy hx hm = (7.16 T 1 5)mm = 14.16mm :: 16.3mm 因此,弹簧SJM32X16必4是合适的 7.1.2 卸料螺钉的选用 卸料螺钉选用圆柱头内六角卸料螺钉 已知与弹簧配合
39、的芯轴的直径为 16mm根据JB/T 7650.6-1994 ,选用规格为M12 的卸料螺钉。 已知下模座厚度为45mm垫板厚度为16mm凸凹模固定板厚度为16mm安全距离 为10mm卸料板厚度14mm 故卸料螺钉长度 L>(16+16+10+14)mm=56mm, L<(45+16+16+10+14)mm=101mm 根据JB/T 7650.6-1994 ,选用长度为65mm勺卸料螺钉。 综上,卸料螺钉的规格为 M12X 65 JB/T 7650.6-1994 7.2 推件装置设计 7.2.1 推件块的设计 推件块的外轮廓与冲裁件的外轮廓一致, 与凹模之间按照H9的配合公差制造
40、,为 f8 了保证推件块的推出可靠,推件块与凹模配合的部分要比凹模略长1mm即 = h 1 = (211) mm = 2 2 m m 设计推件块的凸缘部分时,要保证板料分离时,推件块离凸模固定板仍有 10mm勺 安全距离,已知限位板厚度为16mm推件块已比凹模厚度略长1mm材料板厚1mm因 此凸缘的长度 L2 =(16-10-1-1)mm=4mm。 要完全包络推件块外轮廓,于是将凸缘的表面尺寸设计为 55x 72mm勺矩形。同时, 为保证推出平稳,无偏心载荷,矩形的几何中心位于工件的压力中心。 7.2.2 推杆的设计 为确保推出的平稳,选用四根推杆,分别布置在推件块的四周。
41、为了推出可靠,推杆的长度要略大于推杆固定板、凸模固定板、限位板的厚度之 和。再减去推件块的凸缘厚度。 即 L (16 16 5 -4)mm = 33mm 根据《中国模具设计大典》表 22.5-61中JB/T 7650-1994,确定推杆的规格为 6X35。 7.2.3 推板的设计 考虑到推件块的大小与推杆的布置情况,推板选择直径为 80mm厚度为6mm勺圆 板 7.2.4 弹性元件的选择 1)初定弹簧数量n 为确保推件平稳,拟选n=6 2)计算每个弹簧的预压力Fy 双耳止动垫圈倒装复合模设计 已知推件力FT1 = 4147.06 N =员 =4147.06 n =6
42、91.17N : 692N n 6 3)由1.5Fy估算弹簧的极限工作载荷Fj Fj =1.5Fy =1.5 692N =1038N 由《国际标准模具弹簧ISO10243〉,选定SJM2CK 10X25,其规格为: DH =20mm, Dd =10mm, h0=25mm, hj =12.0mm, Fj=1292N, b h=3 2.5mm, n=2.5圈 由于是进行推件的弹簧,则不需要进行校核。 2 10 8 .其他零件设计 8.1 模柄的设计 模柄主要分为旋入式、压入式、凸缘式。考虑到上模座的尺寸较小,而凸缘式的 面积较大,故不符合要求;并且模柄下的垫板开有推板孔,故压
43、入式也不符合要求, 所以选定模柄为旋入式模柄。 根据《最新冲压模具标准及应用手册》表 8-3.4中JB/T 2862.2-2008 ,由压力机 J23-16的模柄孔尺寸(直径为40mmfflg为60mm与上模座的厚度35mm选定规格为 40 >95的旋入式模柄。 由于需要设置打杆,故选择 B型模柄。其模柄孔尺寸为直径13mm ,模柄高度为 95mm ,所以选定打杆直径为12mm ,长度为120mm的打杆, 8.2 螺钉的选择 考虑到最小孔边距与螺钉长度,上模选择内六角螺钉 M10X100 ,下模选择内六角 螺钉M6X60。 8.3 圆柱销的选择 考虑到最小孔边距与螺钉长度,上模选
44、择圆柱销 M10X100 ,下模选择圆柱销 M6X60 0 9 .校核模具高度 为确保设计的模具能正确地安装到压力机上,需对模具进行高度校核。 模具高度等于各板的厚度加上留出的安全距离 10mm板厚1mm H总=(35 + 20+5+16+16 + 21+14+1+10 + 16 + 16+45) mm = 215mm 压力机最大闭合高度220mm闭合高度调节量45mm 由于(220-45) mmEH总E220mm,故模具高度满足要求。 10 .模具结构三维设计 B-B 1X* 图10-1模具装配图 1-内六角卸料螺钉 2-滑动导柱3-弹簧4-凸凹模5-凹模
45、6-推件块7-凸模 8-滑动导套9-内六角螺钉10-模柄11-上模座12-销13-滑动导套14-垫板 15-推杆固定板16-凸模固定板17-限位板18-卸料板19-凸凹模固定板 20-垫板21-下模座22-滑动导柱23-内六角螺钉 24-固定挡料销 25-推板26-弹簧27-打杆28-销29-推杆30-固定导料销 31-销 工作原理: 图中为倒装复合模,凸凹模装在下模,落料凹模和冲孔凸模装在上模。模具工作 时,由手工送料,条料沿两个固定导料销送至固定挡料销处定位。冲裁时,上模向下 运动,因弹压卸料板与安装在凹模型孔内的推件板分别高出凸凹模和落料凹模的工作 面约1mm,故首先将条料压
46、紧。上模继续下压,同时完成冲孔和落料。冲孔废料直接 由冲孔凸模从凸凹模内孔中推下,无顶件装置,结构简单,操作方便。卡在凹模中的 冲件由弹性推件装置推出,打杆来确保推出的可靠性。 工艺卡 序 工序 工序 号 名称 内容 加工简图 工艺 设备 1 下料 60 M 200 mm 2 冲孔 落料 冲内孔与 落外形 J23-16 开式可 倾压力 机 冲孔落 料倒装 复合模 凸凹模按 3 检验零件图纸 检验 检具
47、 结论 这次冲压模具课程设计给了我一个完全独立自主地进行模具设计的机会,在这过 程中,在进一步掌握了模具设计的标准与方法的同时,更是对之前所学的机械制图、 AutoCAD Solidworks等进行了复习与巩固。从中不仅收获了成功设计出模具时的那种 成就感,对模具设计也有了更加深入的认识。其主要在于以下几个方面: (1)更深入地了解了模具设计制造的思维方式。因为模具的作用就在于生产,所 以模具设计就一定要和生产的实际情况结合在一起,书本上的案例大多都由于过于典 型而脱离生产实际,所以我们设计时不能完全照搬
48、书本上的设计结构与布置,只能从 书本中体会设计的思路和解决问题的方法。就以模柄中的打杆为例,书本中为了让推 出更加平稳,在打杆与推板接触的地方做了宽大的平面,虽然这可以达到增大接触面 积,使运动平稳的目的,但这提高了加工打杆的难度,导致材料浪费,同时也限制了 打杆的安装方向,使打杆只能从模柄的下方装入。若将打杆做成直杆就可以在整个模 具装配完成后,从模柄上方装入,使整个装配过程更加高效。 (2)在遵循标准和寻求创新之间找到平衡。设计模具时虽然要遵守各种行业标 准,但不能被行业标准限制了思维。某些必要的时候,为了制造的便捷和生产的高效, 可以和标准有一定出入。如果永远盲目遵守标准,那么技术就永
49、远不会得到革新,新 的生产方式就永远不会出现。在技术发展的历史洪流中,每次新的发展都伴随着对旧 规则的突破。作为一个机械工程师,我们在遵守标准的同时,一定要怀着一颗敢于开 拓探索的心。 (3)设计时应当本着以人为本的理念。在设计不仅要考虑到生产效益,同时也要 考虑到操作工人的安全与便利,尤其是在选择送料方式为手工送料时,尽量能让工人 站在远离刃口的位置进行操作。并且最好选择可倾式压力机,让从上模落下的工件自 动从板上滑下,省去了取件的过程,提高生产效率的同时也保证了工人的安全。 但同时,我也发现了自身的许多不足。 (1)选取参数时,考虑问题时不够周全。在选取参数时,往往仅是根据标准给定
50、的数值极限取中间值,而忽视了其对后续设计的影响。给我印象最深的就是在对凹模 的周界的选择时,由于未考虑到排样方式,直对排时步距较大,导致送料方向的距离 和步距不匹配,影响了定位元件的布置。 (2)在工程图的表达上还有待提高。在工程图的表达上过于繁琐,表达不够简洁, 不能很好地传达出自己的设计思路。在工程图上应该少用局部剖的方式,因为这让人 不好判断出截面的位置,不如阶梯剖的说明性强。 这是我第一次完整地设计出一套模具,虽然还存在着一些问题,不能符合生产中 的要求,但我相信在不久的将来,在我的认真学习积累之下,一定能做出真正实用的 模具。 致谢 在这次课程设计的尾声,我想衷心感谢一下各位
51、给我悉心指导的老师和同学。 在课程设计的过程中,遇到了很多突如其来的问题,而书本并不总能给我最有效 的解决方案,这时周围的同学们总能热情地加入到问题的讨论中,大家一起想办法, 出主意,解决问题。通过这个过程,不仅使问题得到了解决,还让我有机会掌握到许 多平时被忽视的知识点,对书本的掌握又更近了一步。 然而当遇到同学们也无法解决的问题时,老师们总能悉心给我指导。在老师的指 导中,我真正跳出了书本,了解到更多生产实际中的问题。例如陈怀民老师向我们介 绍的弹性推件与打杆共同使用的倒装复合模在实际生产中的优势、打杆常用的安装方 法、避让孔的加工方式,李波老师介绍的生产中倒装复合模导料、定位的一般方
52、式、 关键零部件的配合要求,以及胡志超老师指导了我们装配图的简洁表达方式和张燕红 老师传授的AutoCAD绘图技巧。在各位老师的指导下,我才能圆满地完成这次课程设 计,并且让我学到了许多在课堂上难以涉及的知识。 最后,再次向陈怀民老师、李波老师、胡志超老师以及张燕红老师致以诚挚的谢 参考文献 [1]翁其金.《冲压工艺及冲模设计》[M].北京:机械工业出版社, 2012.1 [2]魏峥.《solidwords 2004 冷冲模设计实训教程》[M].北京:电子工业出版社, 2005.1 [3]李奇.《模具材料及热处理》[M].北京:北京理工大学出版社, 2012.8 [4]俞汉清.《金
53、属塑性成型原理》[M].北京:机械工业出版社, 2002 [5]胡世光.《板料冷压成形原理》[M].北京:国防工业出版社,1997 [6]肖景容.《冲压工艺学》[M].北京:机械工业出版社, 2000 [7] 丁松聚.《冷充模设计》[M].北京:机械工业出版社, 2002 [8]刘心治.《冷冲压工艺及模具设计》 [M].重庆:重庆大学出版社,1998 [9]张毅.《现代冲压技术》[M].北京:国防工业出版社, 1994 [10]王芳.《冷冲压模具设计指导》[M].北京:机械工业出版社,1998 [11]杨玉英.《实用冲压工艺及模具设计手册》 [M].北京:机械工业出版社, 2004 [12]肖祥芷.《中国模具设计大典:第三卷》 [M].南昌:江西科学技术出版社, 2003 [13]洪慎章.《冲模设计速查手册》[M].北京:机械工业出版社, 2012 [14]王树勋.《冷冲压模具结构图册大全》 [M].广州:华南理工大学出版社, 1994
- 温馨提示:
1: 本站所有资源如无特殊说明,都需要本地电脑安装OFFICE2007和PDF阅读器。图纸软件为CAD,CAXA,PROE,UG,SolidWorks等.压缩文件请下载最新的WinRAR软件解压。
2: 本站的文档不包含任何第三方提供的附件图纸等,如果需要附件,请联系上传者。文件的所有权益归上传用户所有。
3.本站RAR压缩包中若带图纸,网页内容里面会有图纸预览,若没有图纸预览就没有图纸。
4. 未经权益所有人同意不得将文件中的内容挪作商业或盈利用途。
5. 装配图网仅提供信息存储空间,仅对用户上传内容的表现方式做保护处理,对用户上传分享的文档内容本身不做任何修改或编辑,并不能对任何下载内容负责。
6. 下载文件中如有侵权或不适当内容,请与我们联系,我们立即纠正。
7. 本站不保证下载资源的准确性、安全性和完整性, 同时也不承担用户因使用这些下载资源对自己和他人造成任何形式的伤害或损失。
最新文档
- 2025年水电工程运行维护管理合同示范文本.docx
- 2025年工程勘测设计合同模板.docx
- 2025年区域产品销售代理合同.docx
- 2025年经销商授权合同样本.docx
- 2025年员工住房资金借贷合同.docx
- 2025年轻钢建筑施工合同示例.docx
- 2025年网络推广托管合同.docx
- 2025年简明个人借款正式合同范例.docx
- 2025年房产按揭贷款合同范例.docx
- 2025年技术合同争议调解.docx
- 2025年电子版城市住宅租赁合同范本.docx
- 2025年简易转让合同协议书样本.docx
- 2025年投资顾问服务合同实例.docx
- 2025年经销合同模板.docx
- 2025年工业项目设计合同样本.docx