数控车加工薄壁零件工艺分析与编程方案
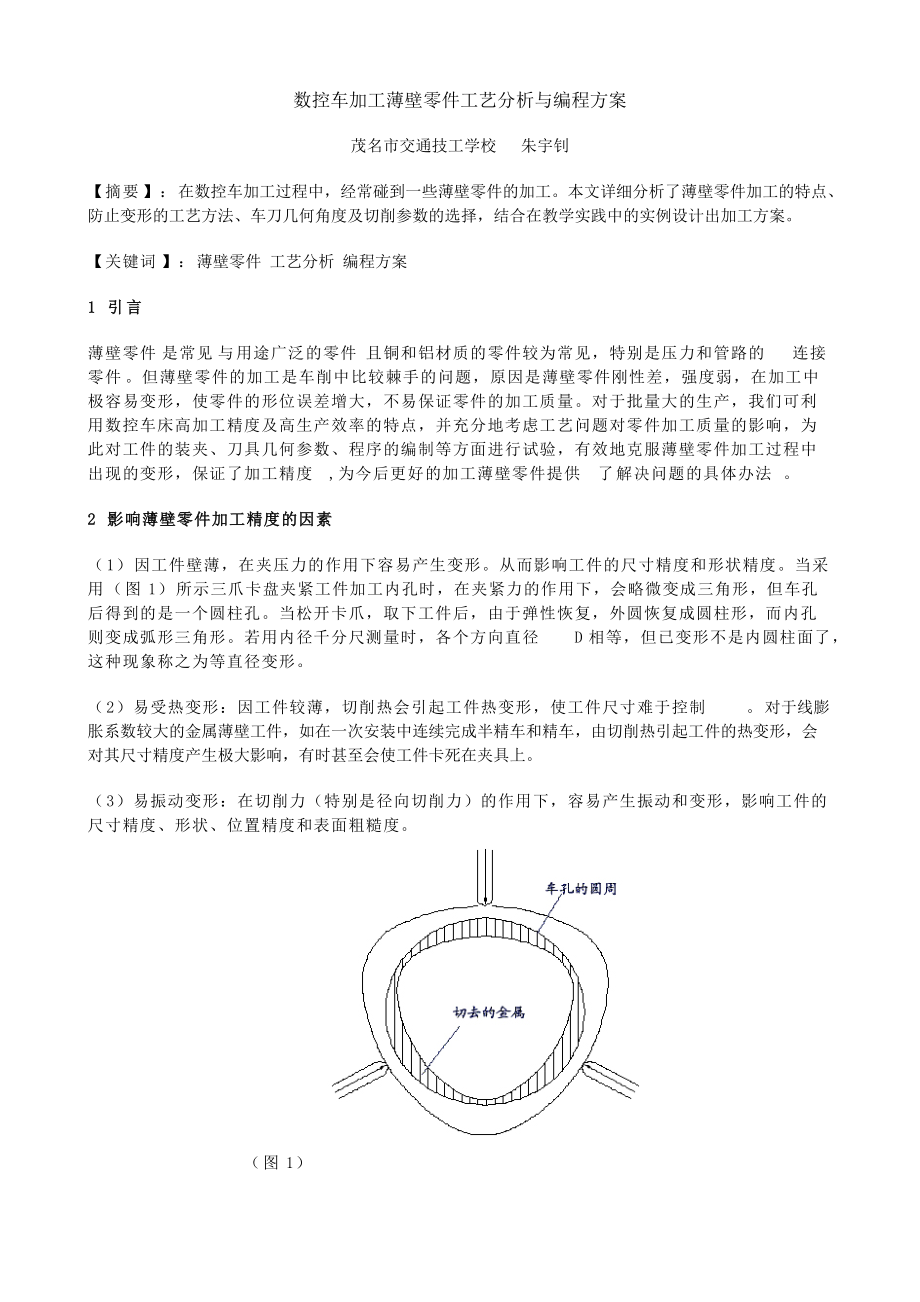


《数控车加工薄壁零件工艺分析与编程方案》由会员分享,可在线阅读,更多相关《数控车加工薄壁零件工艺分析与编程方案(5页珍藏版)》请在装配图网上搜索。
1、数控车加工薄壁零件工艺分析与编程方案 茂名市交通技工学校 朱宇钊 【摘要】:在数控车加工过程中,经常碰到一些薄壁零件的加工。本文详细分析了薄壁零件加工的特点、防止变形的工艺方法、车刀几何角度及切削参数的选择,结合在教学实践中的实例设计出加工方案。 【关键词】:薄壁零件工艺分析编程方案 1 引言 薄壁零件是常见与用途广泛的零件且铜和铝材质的零件较为常见,特别是压力和管路的连接零件。但薄壁零件的加工是车削中比较棘手的问题,原因是薄壁零件刚性差,强度弱,在加工中极容易变形,使零件的形位误差增大,不易保证零件的加工质量。对于批量大的生产,我们可利用数控车床高加工精度及高生产效率的特点,并
2、充分地考虑工艺问题对零件加工质量的影响,为此对工件的装夹、刀具几何参数、程序的编制等方面进行试验,有效地克服薄壁零件加工过程中出现的变形,保证了加工精度,为今后更好的加工薄壁零件提供了解决问题的具体办法。 2 影响薄壁零件加工精度的因素 (1)因工件壁薄,在夹压力的作用下容易产生变形。从而影响工件的尺寸精度和形状精度。当采用(图1)所示三爪卡盘夹紧工件加工内孔时,在夹紧力的作用下,会略微变成三角形,但车孔后得到的是一个圆柱孔。当松开卡爪,取下工件后,由于弹性恢复,外圆恢复成圆柱形,而内孔则变成弧形三角形。若用内径千分尺测量时,各个方向直径D相等,但已变形不是内圆柱面了,这种现象称之为等直径
3、变形。 (2)易受热变形:因工件较薄,切削热会引起工件热变形,使工件尺寸难于控制。对于线膨胀系数较大的金属薄壁工件,如在一次安装中连续完成半精车和精车,由切削热引起工件的热变形,会对其尺寸精度产生极大影响,有时甚至会使工件卡死在夹具上。 (3)易振动变形:在切削力(特别是径向切削力)的作用下,容易产生振动和变形,影响工件的尺寸精度、形状、位置精度和表面粗糙度。 (图1) 3 提高薄壁零件加工精度的工艺分析 (图2)所示的薄壁零件,是我校用数控车床对外加工产品中难度较大的零件,为了提高产品的合格率,我们从工
4、件的装夹、刀具几何参数、程序的编制等方面进行综合考虑,实践证明,有效提高了零件的精度,保证了产品的质量。 图 2 3.1 分析工件特点 从零件图样要求及材料来看,加工此零件的难度主要有两点: (1)主要因为是薄壁零件,螺纹部分厚度仅有4mm,材料为45号钢,批量较大,既要考虑如何保证工件在加工时的定位精度,又要考虑装夹方便、可靠,而我们通常都是用三爪卡盘夹持外圆或撑内孔的装夹方法来加工,但此零件较薄,车削受力点与加紧力作用点相对较远,还需车削M24螺纹,受力很大,刚性不足,容易引起晃动,因此要充分考虑如何装夹定位的问题。 (2) 螺纹加工部分厚度只有4mm,而且精度要求较高。
5、广州数控系统GSK980TD螺纹编程指令有G32、G92、G76。采用G92、G76混用进行编程,即先用G76(图4)进行螺纹粗加工,再用G92(图3)进精加工,在薄壁螺纹加工中,将有两大优点:一方面可以避免因切削量大而产生薄壁变形,另一方面能够保证螺纹加工工的精度。 (图3) G92直进式加工 (图4) G76斜进式加工 3.2 夹具设计 由于工件较薄,刚性较差,如果采用常规方法装夹工件及切削加工,将会受到轴向切削力和热变形的影响,工件会出现弯曲变形,很难达到技术要求。因此,需要设计出一套适合上面零件的专用夹具,如图
6、5所示。 (图5) 3.3 合理选择刀具 具体的刀具角度如下: (1)外圆精车刀(采用机夹刀)Kr=90~93,Kr’=15α0=14~16,α0’=15,γ0适当增大,刀具材料为YW1硬质合金。 (2)内孔精车刀(采用机夹刀)Kr=60,Kr’=30,γ0=35α0=14~16,α0’=6~8,λs=5~6,刀具材料为YW1硬质合金。 3.4 工艺过程 (1) 装夹毛坯15mm长,平端面至加工要求; (2) 用Φ18钻头钻通孔,粗、精加工Φ21通孔; (3) 粗、精加工Φ48外圆,加工长度大于3mm至尺寸要求; (4) 调头,利用夹具如图2所示装夹,控制总长尺寸35
7、mm平端面; (5) 加工螺纹外圆尺寸至Φ23.805; (6) 利用G76、G92混合编程进行螺纹加工; (7) 拆卸工件,完成加工。 3.5切削用量 (1) 内孔粗车时,主轴转速每分钟500-600转,进给速度F100-F150,留精车余量0.2-0.3mm。 (2) 内孔精车时,主轴转速每分钟1100-1200转,为取得较好的表面粗糙度选用较低的进给速度F30-F45,采用一次走刀加工完成。 (3) 外圆粗车时,主轴转速每分钟1100-1200转,进给速度F100-F150,留精车余量0.3-0.5mm。 (4) 外圆精车时,主轴转速每分钟1100-1200转,进给速度F
8、30-F45,采用一次走刀加工完成。 4 编程方案 (数控系统采用GSK980TD) 程序内容 程序说明 O1234 命名O G00 X200 Z50 定位至起刀点 M3 S550 启动主轴,转速550转/分 T0101 调用1#内孔刀 G00 X16 Z5 定位至(16,5) G71 U0.8 R0.3 G71外圆车削循环, 对内孔Φ21进行粗加工 G71 P1 Q2 U-0.5 W0 F100 N1 G0 X21.4 G1 Z0 F40 X21 Z-0.2 N2 Z-37 G0 X200 Z50 M5
9、 回至起刀点,主轴停止 M0 程序停止 M3 S550 主轴启动,转速550转/分 G0 X16 Z5 定位至(16,5) G70 P1 Q2 G70 精车循环N1~N2 G0 X200 Z50 定位至起点 T0202 M3 S1150 调用2#外圆精车刀,启动主轴,转速为1150转/分 G00 X52 Z5 定位至(52,5) G90 X50 Z-6 F100 G90外圆切削循环 X48 车至Φ48 G0 X100 Z100 M5 回至起刀点,主轴停止 M0 程序停止,零件调头并装夹 T0202 调用2#外圆精车刀 M3 S1150 主轴启
10、动,转速1150转/分 G00 X50 Z2 定位至(50,2) G71 U2 R0.5 G71 外圆车削循环,对螺纹外圆进行粗加工 G71 P3 Q4 U0.5 W0 F100 N3 G0 X21.805 G1 Z0 F50 X23.805 Z-1 N4 Z-32 G0 X100 Z100 M5 回到起刀点,主轴停止 M0 程序停止 M3 S1150 主轴启动,转速1150转/分 G00 X50 Z2 定位至(50,2) G70 P3 Q4 精车N3~N4内容 G0 X100 Z100 回换刀点(100,100) T0404 调用4#螺纹刀 G
11、0 X25 Z5 定位至(25,5) G76 P010160 Q300 R0.1 G76螺纹车削循环车削M24*1.5螺纹部分 G76 X22.25 Z-28 P975 Q100 F1.5 G0 X25 Z5 定位至G76同一螺纹加工起点 G92 X22.15 Z-28 F1.5 G92精修螺纹 X22.05 X22.05 G0 X100 Z100 M5 返回起点、停主轴 M30 程序结束 5结束语 本文阐述了薄壁工件的加工特点,减少和防止加工变形的方法,加工难点分析以及数控车削薄壁件参数的选择,确定了薄壁零件加工方案。经生产实践证明,该加工方案切实可行,能保证薄壁零件的尺寸精度、形状精度、位置精度、表面粗糙度和装配质量都满足图纸要求,减少了装夹校正的时间,减轻了操作者的劳动强度,经济效益十分明显。可为类似零件和产品的机械加工提供一定的借鉴。 : [1]GSK980TD系统说明书.编程手册.广州:广州数控设备厂.2004.6.. [2]职业技能鉴定教材编审委员会.车工.北京:劳动社会保障出版社.2004.7. [3]刘立.数控车床编程与操作.北京:北京理工大学出版社.2006.8. [4]穆国岩.数控加工编程与操作.北京:机械出版社.2008.8.转 [5]郑文纬 吴克坚.机械原理.北京:高等教育出版社2003.5.
- 温馨提示:
1: 本站所有资源如无特殊说明,都需要本地电脑安装OFFICE2007和PDF阅读器。图纸软件为CAD,CAXA,PROE,UG,SolidWorks等.压缩文件请下载最新的WinRAR软件解压。
2: 本站的文档不包含任何第三方提供的附件图纸等,如果需要附件,请联系上传者。文件的所有权益归上传用户所有。
3.本站RAR压缩包中若带图纸,网页内容里面会有图纸预览,若没有图纸预览就没有图纸。
4. 未经权益所有人同意不得将文件中的内容挪作商业或盈利用途。
5. 装配图网仅提供信息存储空间,仅对用户上传内容的表现方式做保护处理,对用户上传分享的文档内容本身不做任何修改或编辑,并不能对任何下载内容负责。
6. 下载文件中如有侵权或不适当内容,请与我们联系,我们立即纠正。
7. 本站不保证下载资源的准确性、安全性和完整性, 同时也不承担用户因使用这些下载资源对自己和他人造成任何形式的伤害或损失。
最新文档
- 36个关键词详解2025政府工作报告
- 学习2025年政府工作报告中的八大科技关键词
- 2025年政府工作报告要点速览接续奋斗共谱新篇
- 学习2025政府工作报告里的加减乘除
- 深化农村改革党课ppt课件(20250305)
- 弘扬雷锋精神凝聚奋进力量学习雷锋精神的丰富内涵和时代价值
- 深化农村改革推进乡村全面振兴心得体会范文(三篇)
- 2025年民营企业座谈会深度解读PPT课件
- 领导干部2024年述职述廉述责述学述法个人报告范文(四篇)
- 读懂2025中央一号党课ppt课件
- 2025年道路运输企业主要负责人安全考试练习题[含答案]
- 2024四川省雅安市中考英语真题[含答案]
- 2024湖南省中考英语真题[含答案]
- 2024宁夏中考英语真题[含答案]
- 2024四川省内江市中考英语真题[含答案]