毕业设计论文壳体零件加工工艺及夹具设计全套图纸三维
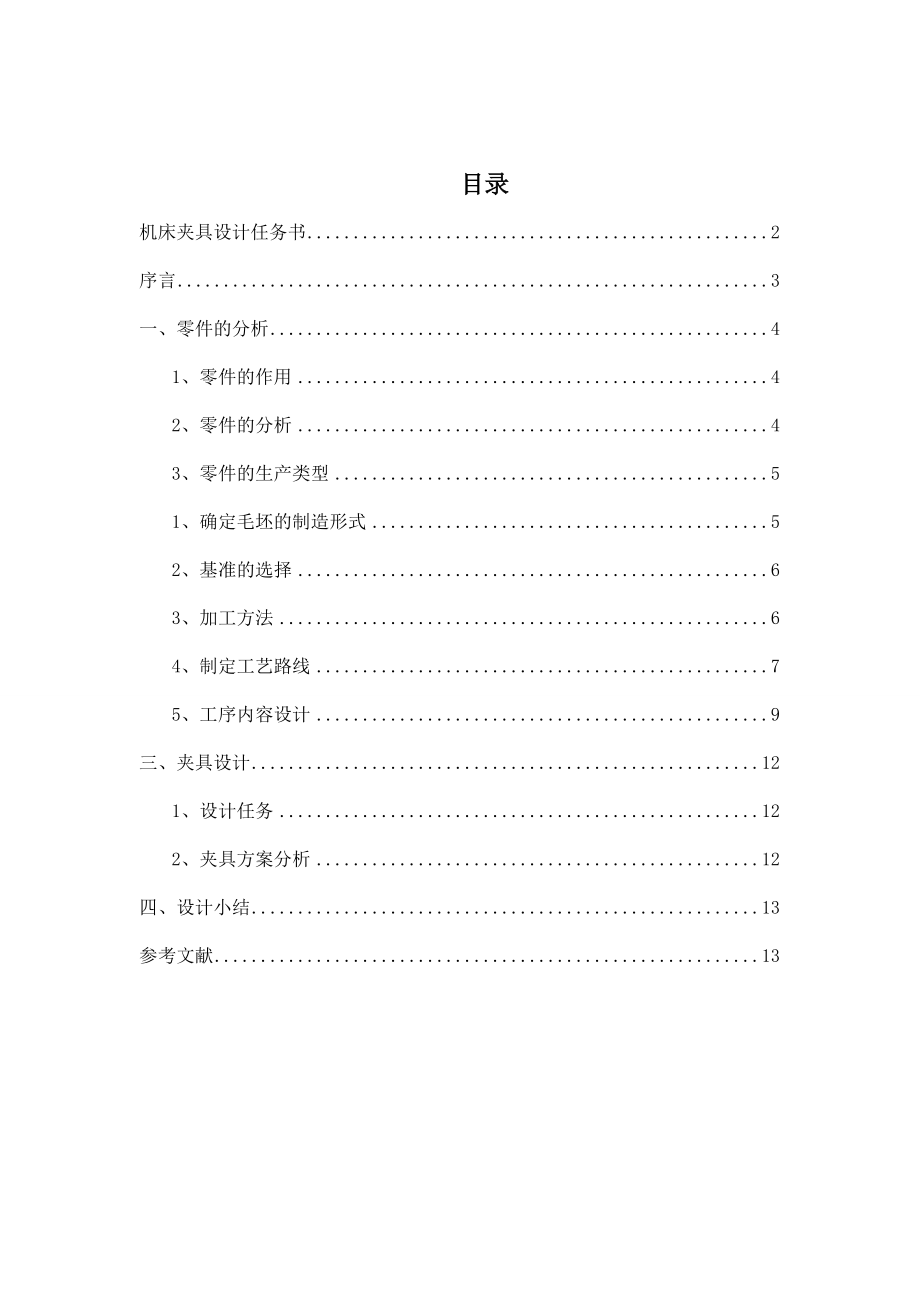


《毕业设计论文壳体零件加工工艺及夹具设计全套图纸三维》由会员分享,可在线阅读,更多相关《毕业设计论文壳体零件加工工艺及夹具设计全套图纸三维(33页珍藏版)》请在装配图网上搜索。
1、 目录 机床夹具设计任务书 2 序言 3 一、零件的分析 4 1、零件的作用 4 2、零件的分析 4 3、零件的生产类型 5 1、确定毛坯的制造形式 5 2、基准的选择 6 3、加工方法 6 4、制定工艺路线 7 5、工序内容设计 9 三、夹具设计 12 1、设计任务 12 2、夹具方案分析 12 四、设计小结 13 参考文献 13 机床夹具设计任务书 全套图纸加153893706 设计题目: 设计“壳体”某一工序专用夹具设计(生产纲领:中批) 设计要求:(上交电子文件和纸资文件) 零件图
2、 1张 工序图 1张 专用夹具装配图 1张 夹具体零件图 1张 设计说明书 1份 三、时间:一周(2010~2011学年度第一学期的第七周) 四、设计步骤及要求: ⑴计算年生产纲领,确定生产类型。 ⑵对零件进行工艺分析,画零件图。〔采用新国标〕 ⑶选定某一工序,画工序简图。(工
3、序尺寸、工序公差及技术要求) ⑷依据工序要求设计专用夹具,其主要工作是:确定定位方案,选择定位基准和定位元件;确定夹紧方式,进行定位误差分析和夹紧力计算。 (5)画夹具装配图、夹具体零件图 五、编写设计说明书 主要参考吴拓、方琼珊主编的《机械制造工艺与机床夹具设计指导》中的设计实例 序言 本设计是在学完了机械制造工艺及机床夹具和大部分专业课的基础上进行的。 本设计是根据学生的实际能力以及结合现代技术的发展趋势综合考虑而做的,主要培养学生综合运用学过的知识,独立地分析和拟定一个零件的合理工艺路线,初步具备设计一个中等复杂程度零件的
4、工艺规程的能力,能根据被加工零件的技术要求,运用夹具设计的基本原理和方法。学会拟定夹具设计方案,完成夹具结构设计,提高结构设计能力,培养学生熟悉和应用各种手册、图片、设计表格等技术资料,以便掌握从事工艺文件的方法和步骤,培养学生解决工艺问题的能力。 由于能力所限,设计尚有许多不足之处,恳请老师给予指教。 一、零件的分析 1、零件的作用 壳体是一种起支撑、连接其他零件和承受负荷的零件。通过底面孔和上端面的孔、螺纹孔,侧面的螺纹孔来与管道、其他壳体等零件连接在一起,并使这些零件之间保持正确的位置关系;通过壳体的孔进行液体或气体的传输。 2、零件的分析 图1.壳体零件图 该壳体
5、可以分成三组加工表面,且三者之间和其各内部之间存在有一定的位置关系,现分述如下: (1) 底面,F7、F30孔和F48沉孔 这一组加工表面包括:底面,4个F7的孔,加工F30的孔和F48的沉孔 (2) 上端面,M6螺纹孔,F7孔和F12盲孔, 这一组加工表面包括:上端面,M6-7H的螺纹孔,6个F7孔,F12的盲孔 (3) 侧面宽28的凹槽,M6的螺纹孔,F8的孔,F24的沉孔,F30的端面,F12的孔,F20的沉孔 这一组加工表面包括:侧面宽28的开口槽,2XM6-H7的螺纹孔,F8的孔并加工F24的沉孔,F30的端面,F12的孔并加工F20的沉孔。 3、零件的生产类型 零件
6、的生产纲领:根据机械设计制作工艺与机床夹具公式: N零 = QN(1+a)(1+B) 公式2.1 说明:式中N零 :零件生产纲领。 Q:产品的生产纲领 n :每一产品包含该零件的数量 a : 零件的备用率一般情况下a = 4 %。 B : 零件的平均废品率:取B=1%。 所以,4000 = Q1(1+4%)(1+1%) Q=3808件 根据机械制造工艺与机床夹具表1-3,可查得此零件生产为中批生产。 二、工艺规程设计 该零件形状特殊,结构一般复杂,属壳体类零件。其表面加工精度均较低,不需要高精度机床加工,通过铣削
7、、钻床的粗加工就可以达到加工要求,而主要加工表面虽然加工精度相对较高,但也可以再正常的生产条件下,采用较经济的方法保质保量地加工出来。由此可见,该零件的工艺性较好。 该零件的主要加工表面为两端面、中心孔,前端面孔,在设计工艺规程时应重点予以保证。 1.3确定零件的生产类型 按照教学要求,该零件生产类型为大批量生产。 2确定毛胚类型绘制毛胚简图 2.1选择毛胚 根据零件材料为ZL102,零件结构一般复杂,生产类型为大批量生产,确定毛胚为铸件。毛胚的铸造方法选用砂型机器造型,由于孔需铸出,故还应安放型芯,此外,为消除残余应力,铸造后应安排人工时效。 2.2确定毛胚尺寸和机加工余量
8、1. 铸件尺寸公差等级 2. 根据铸件采用砂型机器造型,材料为可锻黑铸铁,其加工表面的铸造尺寸精度等级由《机械制造技术基础设计(高等教育版)》(以下简称参考一)表2.3铸件毛胚图 3. 零件毛胚图一般包括铸造毛胚形状、尺寸及公差、加工余量与工艺余量、铸造斜度及圆角、分型面、浇冒口残根位置、工艺基准及其他有关技术要求等。根据主要毛胚尺寸,该铸件毛胚图如下图(一)图(二)所示 各表面加工方案 加工表面 尺寸及偏差/mm 尺寸精度等级 表面粗糙度/ 加工方案 底面 IT12 12.5 铣 上表面 IT12 12.5 铣 F30孔 F30+0.0250 I
9、T6 6.3 扩-粗铰-精铰 F48沉孔 F48 IT12 12.5 扩孔 F7孔 F7 IT10 25 钻 F12盲孔 F12 IT12 25 钻 M6-H7 F6 IT7 25 钻-攻丝 左侧面凹槽 IT12 12.5 粗铣 F8孔 F8 IT10 25 钻 F12沉孔 F12 IT10 25 扩 F30端面 F30 IT12 12.5 粗铣 侧面F12孔 F12 IT10 25 钻 F20沉孔 F20 IT12 12.5 扩 1、确定毛坯的制造形式 考虑到
10、零件的结构,生产年产量,经济成本,选用沙型铸造方法,材料选用ZL102。查《实用机械加工工艺手册》表6-20,表6-30,单边余量Zb=2.5,孔直径为F28、F46。 2、基准的选择 工件在最初加工时,只能以毛坯上未加工的表面作为定位基准,这个是粗基准,该零件应选用上端面作为粗基准来加工底面。以上选择符合粗基准的选择原则中的(如果必须保证零件某些重要表面的加工余量分布均匀,就应该选择该表面做为粗基准,应该用毛坯的尺寸和位置可靠表面,而且平整具有足够大的面积做基准)在以后的工序中,则使用经过加工的表面作为定位基准,底面和F30+0.025 0作为定位基准,这个基准就是精基准。在选精基准时
11、采用有基准重合,基准统一,自为基准、便于装夹。这样定位比较简单可靠,为以后加工重要表面做好准备。 3、加工方法 在市场经济的前提下,一切都是为能创造出更多的财富和提高劳动率为目的,同样的加工方法的选择一般考虑的是在保证工件加工要求的前提下,译稿工件的加工效率和经济性,而在具体的选择上,一般根据机械加工资料和工人的经验来确定。由于方法的多种多样,工人在选择时一般结合具体的工件和现场的加工条件来确定最佳的加工方案。 同样在该零件的加工方法的选择中,我们考虑了工件的具体情况与我们学校的具体加工条件是我们按加工顺序来阐述的加工方案,参考《机械制造手册》表10-33、表10-34其加工方法选择如下
12、: (1)、底面: 公差等级为自由公差,表面粗糙度为Ra12.5um,需要经过粗铣-半精铣 (2)、Φ30-0.025 0孔: 公差等级为IT7~8,表面粗糙度为Ra6.3um,毛坯铸件有孔,故采用扩-粗铰-精铰 (3)、 F48沉孔: 公差等级为自由公差、表面粗糙度达到Ra6.3,故采用扩。 (4)、两处倒角 公差等级为自由公差、表面粗糙度达到Ra25,故采用铣。 (5)、F7孔: 公差等级为自由公差、表面粗糙度达到Ra25,故采用钻。 (6)、上表面: 公差等级为自由公差,表面粗糙度为Ra12.5um,故采用粗铣-半精铣。 (7)、Φ12盲孔: 公差等级为自由公
13、差,表面粗糙度为Ra25um,故采用钻。 (8)、M6-H7的螺纹孔: 中径公差等级为IT7,故采用钻-攻丝。 (9)、左侧面凹槽: 公差等级为自由公差,壁、底面表面粗糙度都为Ra12.5um,,故采用粗铣-半精铣。 (10)、F8孔: 公差等级为自由公差,表面粗糙度为Ra25um,,故采用钻 (11)、F12沉孔: 公差等级为自由公差,壁、底面表面粗糙度为Ra25um,,故采用扩。 (12)、F30端面: 公差等级为自由公差,壁、底面表面粗糙度为Ra12.5um,,故采用粗铣-半精铣。 (13)、侧面F12孔: 公差等级为自由公差,表面粗糙度为Ra25um,,故采用钻
14、。 (14)、F20沉孔: 公差等级为自由公差,内孔表面的表面粗糙度为Ra12.5um、底面表面粗糙度为Ra25um,故采用扩。 4、制定工艺路线 制定工艺路线的出发点,应当是使零件的几何形状、尺寸精度及位置精度等技术要求能得到合理的保证。 4.1工艺路线方案一 工序10:粗、精铣上下表面。 工序20:车 粗车F40,F30孔 。 工序30:车 半精车F40,F30孔。 工序40:铣左端面槽。 工序50:钻孔及攻螺纹M6。 工序60:钻左端面阶梯孔攻2XM6-H7螺纹。 工序70:铣前端面。 工序80:钻前端面阶梯孔。 工序90:钻顶面孔、锪孔。 工序100:钻
15、底面孔、锪孔。 工序110:车 精车F40,F30孔。 工序120:终检。 4.2工艺路线方案二: 工序10:粗、精铣上下表面 工序20:钻、扩、铰孔,倒1x45角 工序30:铣前端面 工序40:钻前端阶梯孔。 工序50:钻顶面孔、锪孔。 工序60:钻底面孔、锪孔。 工序70:铣左端面面槽。 工序80:钻各螺纹孔、攻螺纹。 工序90:扩铰孔。 工序100 :终检。 4.3工艺方案的比较与分析 上述两个方案中,方案2主要按照外表面逐次加工完成后进行空的加工,但会带来一个不利的因素,不利于限制零件自由度,其次虽两方案都是按照孔定位进行加工,但方案2中有部分工序的公布
16、不在同一平面上,会给加工带来额外的不便。 另外,根据机床各种因素综合考虑,选择方案1的工艺路线进行加工。 5、工序内容设计 5.1加工设备选择 根据机床的精度与工序要求的加工精度相适应,机床的工作区域尺寸应与零件的外形尺寸相适应,机床的功率,刚度和工作参数最合理的切屑用量相适应,机床的效率与产品生产类型相适应等关键需求的综合分析后选用下列设备。 万能回转头铣床x62w 工作台面积:1600x400mm 快进速度:2300m/min 工作台进给范围:30-1500 主轴孔径:29mm 进给量级数:16级 主轴转速级数:16级 功率:10kw 外形尺寸:2
17、556x2/59x1770mm 立式钻床Z5140 最大钻孔直径:40mm 进给级数:9级 主轴转速级数:12级 主轴转速范围:31.5-1400r/min 主轴行程:250mm 机床外形尺寸:1105x880x2508mm 工作台面积:480x560mm 立式钻床Z5163A 最大钻孔直径:63mm 进给级数:9级 主轴转速级数:12级 主轴转速范围:22-10000r/min 主轴行程:315mm 机床外形尺寸:1200x970x2790mm 工作台面积:550x650mm 3.5确立切
18、削用量及基本工时 1.工序10——粗铣上下表面 该工序分两个公步,公步1是以下表面定位,粗铣上端面;工步2是以上端面定位,粗铣下端面,它们所选用的背吃刀量、切削速度和进给量是一样的。 (1)背吃刀量 由于切削量较小,故选择 ==2mm。一次走刀即可完成。 (2)进给量 X51型立式铣床功率为4.5KW,查参考一表5.8高速钢套式面铣刀粗铣平面进给量,按机床、工件、夹具系统刚度为中等条件选取,该工序的每齿进给量取为0.08mm/z。 (3)铣削速度 由本工序采用高速钢整体铣刀、=40mm,齿数=12。查参考一表5.8高速钢整体铣刀铣削速度,确定铣
19、削速度=44.9m/min,则 ==357.3r/min 由本工序采用X51型立式铣床,查参考一表3.6,取转速=380r/min,故实际切削速度 ==47.7m/min 当=380r/min时,工作台的每分钟进给量==364.8mm/min 也可根据参考一表3.7查得机床的进给量为300mm/min。 (4)基本工时 由于该工序包括两个工步,每个工步的基本加工时间计算查参考一表5.41铣削基本时间计算,。确定=14mm,=2mm,=24mm;则该工序的基本时间为 , 则该工序基本工时为16s。 工序20——车 粗车F40,F30孔 由参考文献
20、[3]表1.1-47查得f=1.4mm/rb.由参[3]表1.1-46查得νc=80m/min由此算出转速为n=1000νc/πD=106.157r/min按车床的实际转速取n=350r/min 则实际切削速度νc=πDn/1000=263.76m/min 工序30——车 半精车F40,F30孔 由参考文献[3]表1.1-47查得f=1.4mm/r由参[3]表1.1-46查得νc=80m/min 由此算出转速为n=1000νc/πD=110.77r/min 按车床的实际转速取n=350r/min则实际切削速度 νc=πDn/1000=252.77m/min 加工时间 T=
21、 = =1.56min 工序40——铣左端面槽 所选用的背吃刀量、切削速度和进给量是一样的。 (1)背吃刀量 由于切削量较小,故选择 ==2mm。一次走刀即可完成。 (2)进给量 X51型立式铣床功率为4.5KW,查参考一表5.8高速钢套式面铣刀粗铣平面进给量,按机床、工件、夹具系统刚度为中等条件选取,该工序的每齿进给量取为0.08mm/z。 (3)铣削速度 由本工序采用高速钢整体铣刀、=40mm,齿数=12。查参考一表5.8高速钢整体铣刀铣削速度,确定铣削速度=44.9m/min,则 ==357.3r/min 由本工序采用X
22、51型立式铣床,查参考一表3.6,取转速=380r/min,故实际切削速度 ==47.7m/min 当=380r/min时,工作台的每分钟进给量==364.8mm/min 也可根据参考一表3.7查得机床的进给量为300mm/min。 (4)基本工时 由于该工序包括两个工步,每个工步的基本加工时间计算查参考一表5.41铣削基本时间计算,,确定=14mm,=2mm,=62mm;则该工步的基本时间为,该工序基本工时为32s。 工序50——钻F12孔及攻螺纹M6 该工序分两个公步,公步1是钻F12孔;工步2是攻螺纹M6, 背吃刀量的确定ap=20mm 进
23、给量的确定:取每转进给量f=0.20mm/r3).切削速度的计算工件材料ZL102条件选取,切削速度v=15m/min,得n=100015/3.1420=238.73r/min。选取Z550立式钻床主轴转速n=250r/min。可求实际钻削速度v=πdn/1000=π20250/1000=15.71m/min.4).根钻孔的基本时间可由tj=(l+l1+l2)/fn求的。式中l=80㎜l2=1㎜,L1=D/2cotKr+1=20/2cot54+1=100.72+1=8.18㎜,f=0.20㎜/r,n=250r/min,所以基本时间:tj=(l+l1+l2)/fn=(80+8.18+1)/0.2
24、250=1.78min=107.2s(2)扩孔 背吃刀量的确定ap=2mm 进给量的确定取每转进给量f=0.7mm/r3).切削速度的计算选取切削速度v=92.9m/min 得n=100092.9/3.1422=1344.14r/min,选取Z550立式钻床主轴转速n=1400r/min。再将此转速代入公式(5-1)可求实际切削速度v=πdn/1000=π221400/1000=96.76m/min. (3)基本工时 由于该工序包括两个工步,它们所选用的背吃刀量、切削速度和进给量是一样的,所以两工步基本工时也相同。偏角,查参考一表5.41铣削基本时间计算,,,确定=1
25、4mm,=2mm,=15mm;则每个工步工序的基本时间为 ,该工序基本工时为16s。 工序60钻左端面阶梯孔攻2XM6-H7螺纹 (1)切削用量 由工件材料为ZL102、孔F8mm、查参考二表10-22麻花钻,选定直径F8的麻花钻,查参考一表5.19高速钢麻花钻钻削碳钢的切削用量得,切削速度=20m/min,进给量=0.20mm/r,取=8.7mm,则 =r/min=732.1r/min 由本工序采用Z525型立式钻床,由表3.17得,转速=680r/min,故实际切削速度为 ==18.58m/min (2)基本工时 由参考一表5.39,工步,则该工序的
26、基本时间为 工序70铣前端面 该面精度要求不太高,可直接由高速钢铣刀一次铣完 根据金属机械加工工艺人员手册第三版表12-2查得 ZL102材料铸件总加工余量为6mm,故工序尺寸及公差为,由表14-69可查得铣削进给量=0.3mm/z;由表14-76查得铣削时切削速度V=40m/min,由此可算出转速: n==250r/min 根据机床的主轴变速级数可取实际转速为263r/min,则实际线速度为r===41.4m/min 由表8-55可查得x62w主轴转速范围为30-1500r/min;机床功率为10kw, 由表14-67可得切削功率为: =4.76kw<10kw,
27、所以所选机床适用。 工序80钻前端面阶梯孔 该工序分为两个工步:1.先钻F12 2.钻F20 该孔由高速钢扩钻钻头扩钻后再铰刀铰。由机械加工工艺手册表13-16查得铰孔时加工余量为0.4mm,故扩钻加工余量为Z=6-0.4=5.6mm 钻孔的工序尺寸为12mm 扩孔的工序尺寸为20mm 由表14-37查得扩孔进给量=0.8mm/r,由表14-41查得扩孔时切削速度r=20.1m/min,所以计算得到转速 n= ==134.4r/min 根据机床实际变速级数取实际转速n=178r/min,则实际切削速度: V= =26.6m/min 扭矩M=222.75N/mm
28、 由表8-26查得此机床最大扭矩为1200x10N/mm,所以所选机床适用。 (4)基本工时 由参考一表5.37孔基本时间的计算 ,因此基本工时为11s,半 精镗工步基本工时为46s。 工序90钻顶面6X7孔、锪孔 此孔由高速钢钻头一次钻出,由机械加工工艺人员手册表14-34可查得钻孔进给量=0.15mm/r,钻孔余量为7mm,钻孔尺寸及公差为,由表14-36可查得钻孔时的切削速度r=21m/min,由此可计算得到转速n: n==954.9r/min 由机床实际转速可取实际转速为n=990r/min,则实际速度: V= =21.8m/min 由表14-30可
29、查得 =1113N M=3265N.mm 由表8-26查得此机床最大进给力为16000N,最大扭矩为400xN.mm,此机床适用。 工序100 底面4-7孔 此孔由高速钢钻头一次钻出,由机械加工工艺人员手册表14-34可查得钻孔进给量=0.15mm/r,钻孔余量为7mm,钻孔尺寸及公差为,由表14-36可查得钻孔时的切削速度r=21m/min,由此可计算得到转速n: n==954.9r/min 由机床实际转速可取实际转速为n=990r/min,则实际速度: V= =21.8m/min 由表14-30可查得 =1113N M=3265N.mm 由表8-26查得此机床最
30、大进给力为16000N,最大扭矩为400xN.mm,此机床适用。 3)基本工时 由于该工序包括两个工步,它们所选用的背吃刀量、切削速度和进给量是一样的,所以两工步基本工时也相同。偏角,查参考一表5.41铣削基本时间计算,,,确定=14mm,=2mm,=6mm;则每个工步工序的基本时间为 ,该工序基本工时为10s。 工序110 车 精车F40,F30孔 根据《工艺手册》中表3-19,查得=1mm,f=0.4mm/z。根据表3-30,查得v=0.5m/s 加工转速 = = =6.29r/s 取n=6.3r/s,则 切削速度 v= = =1.50m/s 1. 确定
31、车削时间 T= = =82.14s 工序120去毛刺,终检。 5.3工装夹具 (1)、工装夹具: 第一次装夹:即加工底面、43F7,以上表面作为粗基准,采用压板压住。 第二次装夹:即加工上表面,63F7,F12盲孔等,以底面定位,采用带螺纹圆柱销夹紧。 第三次装夹:即加工内孔F30+0.025 0表面与F48沉孔等,以上表面作为精基准,用带螺纹圆柱销夹紧。 第四次装夹:即倒内孔F30+0.025 0的倒角,以底面定位,采用带螺纹圆柱销夹紧。 (2)、刀具: ①粗铣平面:刀具号T0101,可转位面铣刀,刀具直径为F100,刀片型号为SNKN1204ENN,刀
32、具型号为FM75-100SD08ALML200-Z5 ②钻中心孔:刀具号T0202,高速钢中心钻,d=3.15,d 1=8.0,l=50,l 1=3.9 ③钻F7孔:刀具号T0303,高速钢直柄短麻花钻,d=7, l=74,l 1=34 ④钻螺纹孔底孔F5:刀具号T0404,攻螺纹前钻孔用直柄阶梯麻花钻,d=5, l=62,l 1=26 ⑤钻F12盲孔:刀具号T0505,高速钢直柄麻花钻,d=12, l=151,l 1=101 ⑥扩F30孔:刀具号T0606,莫氏锥柄扩孔钻,d=29.8, l=296,l 1=175 ⑦扩F48孔:刀具号T0707,莫氏锥柄扩孔钻,d=48, l=
33、369,l 1=220 ⑧粗铰F30孔:刀具号T0808,莫氏锥柄长刃机用铰刀,d=29.93, L=251,l=124 ⑨精铰F30孔:刀具号T0909,莫氏锥柄长刃机用铰刀,d=30, L=251,l=124 ⑩倒角:刀具号T1010,直柄燕尾槽铣刀,d=20, L=67,θ=45Z=8 5.5工序尺寸及公差 由机械加工工艺人员手册12-5查得该种铸件的尺寸公差等级为9级,机械加工余量等级为6-8级,故取为8级,最大为7级。 由表12-4可查得铸件的主要尺寸的公差,由表12-2可查得各表面的总余量,但由于用查表法确定的总余量与生产实际情况有些差距,故做相应调整,现将调整后的主要
34、毛坯尺寸及公差列入下表: 主要尺寸 零件尺寸 总余量 毛坯尺寸 公差 30前端面 36 6 42 48孔 48 5.6+0.4 42 底面4-7孔 7 7 三、铣床夹具设计 1、设计任务 此次设计主要分为两部分,一是对零件的机加工进行工艺规程设计,二是对工序进行专用夹具设计。 此次夹具设计选择壳体前端面加工进行专用夹具设计。 2、夹具方案分析 2.1工件的定位方案分析 零件下表面有足够的宽度且下表面的宽度宽于待加工平面,若以上表面为定位面,则不利于前端面的铣削,所以选择下表面为主要定位基准面,限制两个旋转自由
35、度和一个移动自由度,根据零件前端的设计基准为孔轴线,所以以孔进行定位,作为导向定位基准面限制工件的另外两个移动自由度,再采用一个菱形定位销在工件的底面进行定位,限制工件的另外一个旋转自由度。 2.2夹紧方案分析 因为采用限制工件的自由度,所以可以将定位心轴的长度尺寸加长,在末端攻上螺纹,采用开口垫片与螺母相互结合的方式夹紧,不仅方便简单而且可保证工件的快捷安装。 (1)定位元件尺寸及公差确定。 夹具的主要定位元件为一圆孔和一面,孔与面隙配合。 (2)工件的工序基准为孔心,当工件孔径为最大,定位孔的孔径为最小时,孔心在任意方向上的最大变动量等于孔与其配合的最大间隙量
36、。本夹具是用来在立式钻床上加工,所以工件上圆柱与夹具上的定位孔保持固定接触。此时可求出孔心在接触点与圆柱中心连线方向上的最大变动量为孔径公差多一半。工件的定位基准为孔心。工序尺寸方向与固定接触点和圆柱中心连线方向相同,则其定位误差为:Td=Dmax-Dmin 本工序采用一孔,一圆柱端面定位,工件始终靠近定位孔的一面,而圆柱的偏角会使工件自重带来一定的平行于夹具体底版的水平力,因此,工件不在定位圆柱正上方,进而使加工位置有一定转角误差。但是,由于加工是自由公差,故应当能满足定位要求。 钻床专用夹具的设计 2.2.1. 设计前的准备工作 (1)明确工件的年
37、生产纲领 机床夹具是在机床上装加工件的一种装置,其作用是使工件相对机床和刀具有一个正确的位置,并在加工过程中保持不变。它是夹具总体方案确定的依据之一,它决定了夹具的复杂程度和自动化程度。本次加工的工件需大批量生产,此时,一般选择机动、多工件同时加工,自动化程度高的方案,结构也随之复杂,成本也提高较多。 (2)熟悉工件零件图和工序图 零件图给出了工件的尺寸、形状和位置、表面粗糙度等精度的总体要求,工序图则给出了夹具所在工序的零件的工序基准、工序尺寸、已加工表面、待加工表面、以及本工序的定位、夹紧原理方案,这是夹具设计的直接依据。 已知待加工工件如图2-1所示,加工φ35H7的孔(前工序已
38、将各部尺寸加工完成)。 2.2.2. 加工方法 了解工艺规程中本工序的加工内容,机床、刀具、切削用量、工步安排、工时定额,同时加工零件数。这些是在考虑夹具总体方案、操作、估算夹紧力等方面必不可少的,根据零件图可知,本道工序的内容是钻、扩、铰φ35H7的孔。 2.3. 总体方案的确定 2.3.1. 定位方案 工件在机床上的定位实际上包括工件在夹具上的定位和夹具在机床上的定位两个方面。工序图只是给出了原理方案,此时应仔细分析本工序的工序内容 2.3.3. 加紧机构的选择 (1)对工件加紧装置的要求 ① 在加紧过程中应保持工件定位时所获得的正确位置
39、 。 ② 在切削过程中,切削力不应破坏工件的正确位置,并使平衡切削力所需的夹紧力最小。 ③ 在切削过程中,应避免工件产生不能允许的振动。 ④ 加紧装置应操作方便、省力、安全。 ⑤ 夹紧装置的复杂程度和制动化程度应与生产批量和生产方式相适应。 (2)夹紧力的方向 夹紧力的方向要有利于工件的定位,并注意工件的刚性方向,不能使工件有脱离定位表面的趋势,防止工件在夹紧力的作用下产生变形。 (3)夹紧力的作用点 夹紧力的作用点应选择在定位元件支承点的作用范围内,以及工作刚度高的位置,确保工件定位准确、不变形。 (4)选择夹紧机构 在确定夹紧力的方向、作用点的同时,要确定相应的夹紧
40、机构。确定夹紧机构要注意以下几方面的问题: ① 安全性。夹紧机构应具备足够的强度和夹紧力,以防止以外伤及夹具操作人员。 ② 手动夹具夹紧机构的操作力不应过大,以减轻操作人员的劳动强度。 ③ 夹紧机构的行程不宜过长,以提高夹具的工作效率。 夹紧机构的原理是用固定扳手拧开上方螺母,这个过程中螺母下方的夹紧体在弹簧作用下自动升起,从而达到松开工件的作用。原理简单,操作简单 2.3.4选择导向装置 刀具的导向是为了保证孔的位置精度,增加钻头的支撑以提高其刚度,减少刀具的变形,保证孔加工的位置精度,常用的几种钻套如下图所示。 图2-5快换钻套 夹具装配图上的尺
41、寸和技术条件 夹具装配图上应标注必要的尺寸和技术要求,主要目的是为了检验本工序零件加工表面的形状,位置和尺寸精度在夹具中是否可以达到,为了设计夹具零件图,也为了夹具装配和装配精度的检测。 3.1. 夹具装配图上标注的尺寸 1)夹具总体外形轮廓尺寸,总长200mm,总宽180mm,总高164mm。 2)夹具与钻模套导向的配合关系,如钻模套对衬套所需要的配合尺寸为Φ20F7/k6,夹具与衬套所需的配合为Φ26H7/n6。 4)各定位元件之间,定位元件与工件之间,与卡具体之间装配后的位置尺寸及公差,如心轴与孔配合为Φ30H7/r6,,定位大平面与夹
42、具体基准平面间的平行度为0.03mm。 上述联系尺寸和位置尺寸的公差,一般取工件的相应公差的1/3~1/5,最常用的是1/3。 3.2. 夹具装配图上应标注的技术要求 应标注的技术要求包括:相关元件表面间的位置精度,主要表面形状精度,保证装配精度和检测的特殊要求,以及调整、操作等必要的说明。通常有以下几方面: 1)定位元件的定位表面间相互位置精度。 2)定位元件的定位表面与夹具安装基面、定向基面间的相互位置精度。 3)导向元件工作面与安装基面间的相互位置精度。 4)写明需要钳工配作的元件。 对于不同的机床夹具,对于夹具的具体结构和使用
43、要求,应进行具体分析,订出该夹具的具体的技术要求。设计中可以参考机床夹具设计手册以及同类夹具的图样资料。 夹具零件图上的尺寸和技术条件 零件图上应标注必要的尺寸和技术要求,标注的主要目的是保证夹具体各个零件之间的尺寸要求和安装配合后的精度要求,也是为了各夹具零件加工后进行安装配合能满足制造工件的要求,本设计所画夹具零件图为夹具体。 4.1夹具零件图上标注的尺寸 1)夹具体的外形尺寸,总长为200mm,总宽180mm,总高164mm。 2)夹具体上各螺纹孔之间的位置尺寸要求,定位销的配做精度要求。 4.2夹具零件图上应标注的技术要求 1)零件图中必须用规
44、定的代号、数字和文字简明地表示出在制造和检验时所应达到的技术要求。 方案设计论证 (1)根据所给工件的需要,选择加工机床,选用立式钻床加工比较合理。 (2)然后工件主要定位部分为平面、两个销,分析所要加工φ12的孔必须完全定位,设想用一面两销定位,正好满足六点定位原理且结构简单,所以这里就是选择一面两销的优点。 (3)最后将一面两销先固定在大平面上,以平面、心轴和菱形销进行定位。一面两销把工件定位后,可利用螺旋夹紧机构来对工件进行夹紧,工件的夹紧力的方向应和工件待加工孔的轴线方向一致,并保证该轴线和夹具体底面有一定的垂直度要求。 5.1设计方法与结果 (
45、1)对工件的加工要进行分析,已知工件上待加工φ12H7的孔,根据工件的形状和加工要求和批量,采用立式摇臂钻床比较合理。 (2)根据六点定位原理,选用一面、一短圆柱销和一菱形销定位,由于限制了六个自由度,所以只需要将工件夹紧就可以进行加工了,在工件加工方向上进行夹紧,可以螺旋夹紧机构,因为他们可以对工件快速加紧,且夹紧力的方向要有利于工件的定位。 (3)最后,对整个夹紧方案分析得出,定位符合六点定位原理,夹紧工件稳定,所以此夹具设计可行。 四、设计小结 此次机械设计制造工艺及机床夹具设计主要是对壳体加工工艺规程与夹具设计,在设计过程中要通过对零件进行分析,选择基准,拟定合理
46、的工艺路线,再次选择加工设备及切削用量,即而确定主要表面不同加工时的工序尺寸及公差,填写过程卡,工序卡,通过相关文献手册的查阅,拟定合理的工件定位方案,并分析夹具方案,对刀方案的确定,设计出一套工件定位专用夹具,并完成对夹具体装配图,零件图的绘制。 通过这次设计,使我对机械装备有了更进一步的了解。装备在现在工业中有着重要的作用,当然,我们现在对机械设计只不过时一个初步的了解,这门还有更多的知识等着我们去学习,在这两周短暂的设计里,我学会了一些机械设计的最基本的理论,同时也对机械装备产生了浓厚的兴趣。 在这次设计过程中,我发现自己还有很多不足之处,在设计和计算过程中也出现了各种各样的错误,在
47、同学和老师的帮助下也都尽量改正了,虽然还存在或多或少的问题,这也是我今后努力的方向,我会继续努力学习,来丰富自己的知识。 在这段时间的不懈努力下,我了解了在设计中应注意的问题: 1)注意与工艺规程的衔接,夹具设计应和工序设计统一 所需设计的夹具绝大多数用于零件加工的某一特定工序。在工艺设计环节中,对该工序的设计已要求设计其定位与夹紧方案,因此夹具设计的具体内容应与工序设计保持一致,不能相互冲突。 2)设计时要有整体观念 夹具设计有其自身的特点:定位、夹紧等各种装置在设计前是分开考虑的,设计后期通过夹具体的设计将各种元件联系为一个整体。 3)设计中应学习正确运用标准与规范 对于国家
48、标准的规范要严格要求和执行。夹具设计过程中选择各种功能元件时应注意尽可能选用标准件,减少非标准件的设计制造工作量,降低夹具成本。 另外我学到的理论知识,应用于实践,学以致用,从中受益匪浅,使我明白了对零件加工时的流程,并大致了解了对相关标准件的查找及绘制,我更从此次设计中学到一丝不苟的工作作风,严谨,细致的工作态度。 在此要感谢在我设计过程中给我关心和帮助的老师同学们,谢谢! 参考文献 [1]李旦等.机床专用夹具图册.哈尔滨.哈尔滨工业大学出版社.2005. [2]孙己德.机床夹具图册.北京.机械工业出版社.1984. [3]王启平.机床夹具设计.哈尔滨.哈尔滨工业大学出版社.2005. [4]吴拓等.机械制造工艺与机床夹具设计指导.北京.机械工业出版社.2005. [5]孙丽媛.机械制造工艺及专用夹具设计指导.北京.冶金工业出版社.2002.
- 温馨提示:
1: 本站所有资源如无特殊说明,都需要本地电脑安装OFFICE2007和PDF阅读器。图纸软件为CAD,CAXA,PROE,UG,SolidWorks等.压缩文件请下载最新的WinRAR软件解压。
2: 本站的文档不包含任何第三方提供的附件图纸等,如果需要附件,请联系上传者。文件的所有权益归上传用户所有。
3.本站RAR压缩包中若带图纸,网页内容里面会有图纸预览,若没有图纸预览就没有图纸。
4. 未经权益所有人同意不得将文件中的内容挪作商业或盈利用途。
5. 装配图网仅提供信息存储空间,仅对用户上传内容的表现方式做保护处理,对用户上传分享的文档内容本身不做任何修改或编辑,并不能对任何下载内容负责。
6. 下载文件中如有侵权或不适当内容,请与我们联系,我们立即纠正。
7. 本站不保证下载资源的准确性、安全性和完整性, 同时也不承担用户因使用这些下载资源对自己和他人造成任何形式的伤害或损失。
最新文档
- 36个关键词详解2025政府工作报告
- 学习2025年政府工作报告中的八大科技关键词
- 2025年政府工作报告要点速览接续奋斗共谱新篇
- 学习2025政府工作报告里的加减乘除
- 深化农村改革党课ppt课件(20250305)
- 弘扬雷锋精神凝聚奋进力量学习雷锋精神的丰富内涵和时代价值
- 深化农村改革推进乡村全面振兴心得体会范文(三篇)
- 2025年民营企业座谈会深度解读PPT课件
- 领导干部2024年述职述廉述责述学述法个人报告范文(四篇)
- 读懂2025中央一号党课ppt课件
- 2025年道路运输企业主要负责人安全考试练习题[含答案]
- 2024四川省雅安市中考英语真题[含答案]
- 2024湖南省中考英语真题[含答案]
- 2024宁夏中考英语真题[含答案]
- 2024四川省内江市中考英语真题[含答案]