冶金工程课程设计转炉炉型设计及物料平衡计算
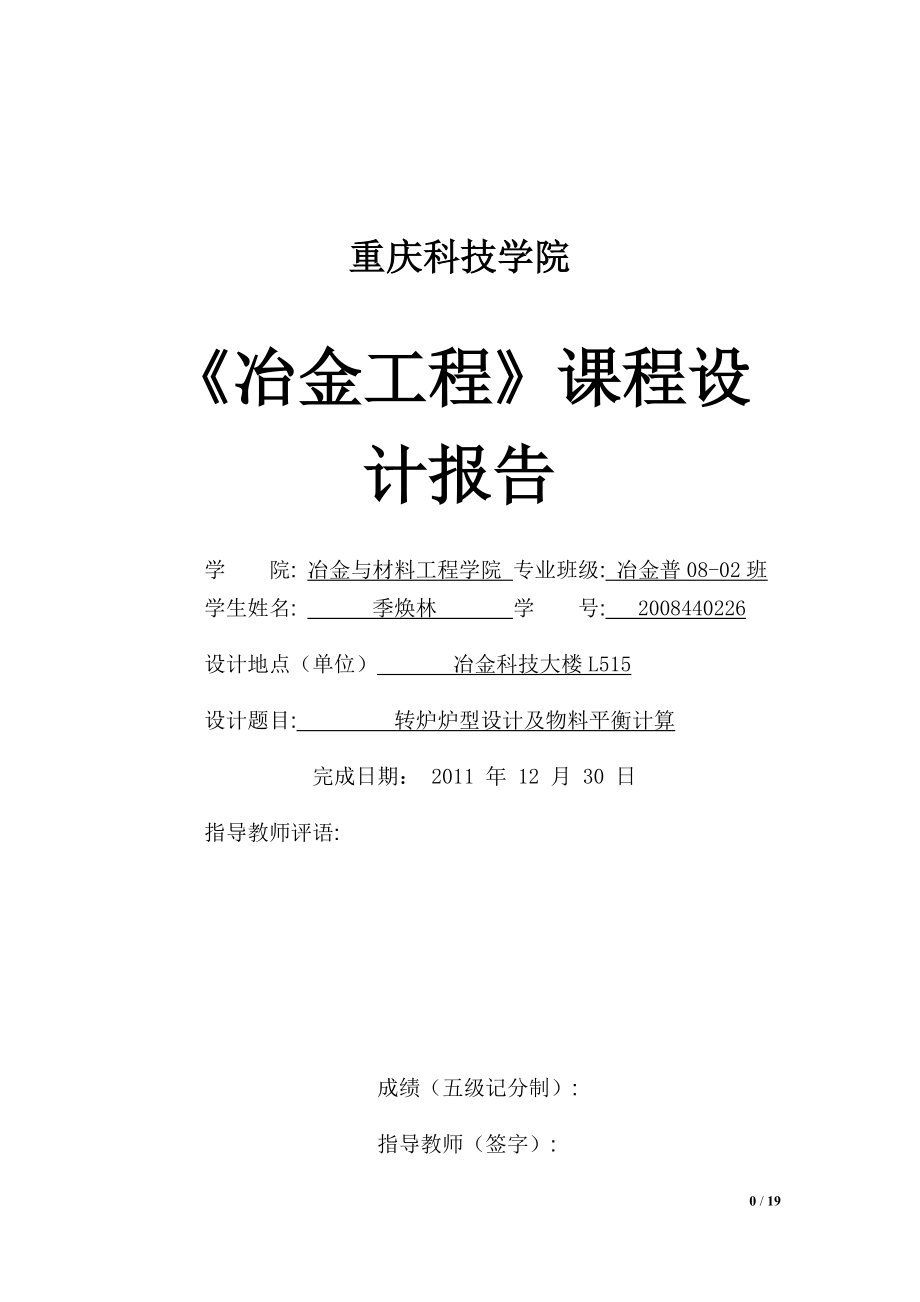


《冶金工程课程设计转炉炉型设计及物料平衡计算》由会员分享,可在线阅读,更多相关《冶金工程课程设计转炉炉型设计及物料平衡计算(19页珍藏版)》请在装配图网上搜索。
1、 重庆科技学院 《冶金工程》课程设计报告 学 院: 冶金与材料工程学院 专业班级: 冶金普08-02班 学生姓名: 季焕林 学 号: 2008440226 设计地点(单位) 冶金科技大楼L515 设计题目: 转炉炉型设计及物料平衡计算 完成日期: 2011 年 12 月 30 日 指导教师评语:
2、 成绩(五级记分制): 指导教师(签字): 目 录 1 50t氧气顶吹转炉炉型设计3 1.1转炉炉型及其选择 3 1.2 转炉炉型各部分
3、尺寸的确定 3 1.2.1 熔池尺寸 3 1.2.2 炉身尺寸 4 1.2.3 炉帽尺寸 5 1.2.4 出钢口尺寸 6 1.2.5 高径比 6 1.3 绘制转炉炉型图 6 2 氧气顶吹转炉炼钢物料平衡和热平衡计算7 2.1 物料平衡计算 7 2.1.1 计算原始数据 7 2.1.2 物料平衡基本项目 8 2.1.3 计算步骤 8 第一步:计算脱氧和合金化前的总渣量及其成分 8 第二步:计算氧气消耗量 9 第三步:计算炉气量及其成分 10 第四步:计算脱氧和合金化前的钢水量 11 第五步:计算加入废钢的物料平衡 11 第六步:计算脱氧合金化后的物料平衡 1
4、2 2.2 热平衡计算 14 2.2.1 计算所需原始数据 14 2.2.2 计算步骤 15 第一步:计算热收入Qs 15 第二步:计算热支出Qz 16 第三步:列出热平衡表 17 参考文献 18 附 50t氧气顶吹转炉炉型图 冶金工程课程设计任务书 1 50t氧气顶吹转炉炉型设计说明书 1.1 转炉炉型及其选择[1] 转炉的炉型是指由炉帽、炉身、炉底三部分组成的炉衬内部空间的几何形状。由于炉帽和炉身的形状没有变化,所以通常按熔池形状将转炉炉型分为筒球型、锥球型和截锥型等三种。炉型的选择往往与转炉的容量有关。 转炉公称容量:50t,根据我国中小型转炉普遍采用的炉
5、型,选择锥球型熔池(熔池由球缺体和倒截锥体两部分组成)。 1.2 转炉炉型各部分尺寸的确定[1] 1.2.1 熔池尺寸 (1)熔池直径D。熔池直径是指转炉熔池在平静状态时金属液面的直径。转炉吹氧时间t与金属装入量G成正比,而与单位时间供氧量Q成反比,即: (1-1) 在供氧增大的情况下,若要避免喷溅趋于严重,就必须扩大熔池面积。也就是说,单位时间供氧量Q与熔池直径D的平方根成正比,即: (1-2) 将式(1-1)与式(1-2)合并,得:
6、 (1-3) 上式可写为: (1-4) 式中 D——熔池直径,m; K——系数,参见表1-1,取K=1.85; G——新炉金属装入量,t,可取公称容量; t——平均每炉钢吹氧时间,min,参见表1-2,取t=14min。 表1-1 系数K的推荐值 转炉容量/t <30 30~100 >100 备注 K 1.85~2.10 1.75~1.85 1.50~1.75 大容量去下限,小容量取上限 表1-2 平均每炉钢冶炼时间推荐值 转炉容量/t <30 30~100 >10
7、0 备注 冶炼时间/min 28~32 32~38 38~45 结合供氧强度、铁水成分和所炼钢种等具体条件确定 吹氧时间/min 12~16 14~18 16~20 代入数值计算得: (1-5) (2)熔池深度h。熔池深度指转炉熔池在平静状态时,从金属液面到炉底的深度。对于一定容量的转炉,炉型和熔池直径确定之后,可利用几何公式计算熔池深度h。 锥球型熔池:倒锥度一般为12~30,当球缺体半径R=1.1D时,球缺体高h1=0.09D的设计较多。熔池体积和熔池直径及熔池深度h有如下关系: ,其中ρ为钢液的密度,取ρ=7.0 t/m3
8、 (1-6) 因而 (1-7) 代入数值计算得: 取倒锥度β=15 球缺体半径R= 1.1D = 1.13.496 = 3.846m 球缺体高h1 = 0.09D = 0.093.496 = 0.315m 1.2.2 炉身尺寸 转炉炉帽以下,熔池面以上的圆柱体部分称为炉身。其直径与熔池直径是一致的,故需确定的尺寸高度H身。 (1-8) 式中 ,,——分别是炉帽、炉身、熔池的容积; —
9、—转炉的有效容积,为,,三者之和,取决于炉容量和炉容比。 炉容比系指转炉有效容积与公称容量G之比值/G (m3/t)。近20年投产的大型氧气转炉,其炉容比都在0.9~1.05之间。据此取炉容比。计算得: 1.2.3 炉帽尺寸 (1)炉帽倾角θ。倾角过小,炉帽内衬不稳定,容易倒塌;过大则出钢时容易钢渣混出和从炉口大量流渣。倾角为55~63,小炉子上限,大炉子取下限,这是因为大炉子的炉口直径相对小些。据此: 取θ=60 (2)炉口直径d。在满足顺利兑铁水和加废钢的前提下,应适当减小炉口直径,以减少热损失。一般炉口直径为熔池直径的43%~53%较为适宜。小炉子取上限,大炉子取下限。据此:
10、 d=0.52D=0.523.496=1.818m。 (3)炉帽高度H帽。为了维护炉口的正常形状,防止因转衬蚀损而使其迅速扩大,在炉口上部设有高度为H口=300~400mm的直线段。因此炉帽高度H帽为: (1-9) 取H口=350mm,代入数值得: 炉帽总容积V帽为: (1-10) 代入数值得: 所以 由式(1-8)得: 1.2.4 出钢口尺寸 出钢口内口一般都设在炉帽与炉身交界处,以使转炉出钢时其位置最低,便于钢水全部出净。 (1)出钢口中心线水平倾角θ1。为了缩短
11、出钢口长度,以利于维修和减少钢液二次氧化及热损失,大型转炉的θ1趋于减小。国外不少转炉采用0一般为15~20。据此:取θ1=15 (2)出钢口直径d出。出钢口直径决定着出钢时间,因此随炉子容量而异。出钢时间通常为2~8min。时间过短(即出钢口大),难于控制下渣,且钢包内钢液静压力增长过快,脱氧产物不易上浮。时间过长(即出钢口过小),钢液容易二次氧化和吸气,散热也过大。通常d出(cm)按下面的经验公式确定: (1-11) 代入数值计算得: 1.2.5 高径比 高径比指转炉的炉壳总高H总和炉壳外径D壳之比值。随着转炉大型化和顶
12、底复吹技术的采用,转炉由细高型趋于矮胖型,即高宽比趋于减小。转炉高径比推荐值为1.35~1.65。 由上知: 1.3 绘制转炉炉型图[1] 根据以上计算所得数据绘制50t氧气顶吹转炉炉型图。 设计熔池为截锥型,设计草图附后。 2 氧气顶吹转炉炼钢物料平衡和热平衡计算说明书 2.1 物料平衡计算[1] 2.1.1 计算原始数据 基本原始数据有:冶炼钢种及其成分、铁水和废钢的成分、终点钢水成分(表2-1);造渣用溶剂及炉衬等原材料的成分(表2-2);脱氧和合金化用铁合金的成分及其回收率(表2-3);其他工艺参数(表2-4)。 表2-1 钢种、铁水、废钢和
13、终点钢水的成分设定值 成分含量/% 类别 C Si Mn P S 钢种Q235设定值① 0.18 0.25 0.55 ≤0.045 ≤0.050 铁水设定值 4.10 0.60 0.40 0.120 0.060 废钢设定值 0.18 0.25 0.55 0.030 0.030 终点钢水设定值② 0.10 痕迹 0.12 0.012 0.042 ①本计算设定的钢种为Q235。 ②[C]和[Si]按实际生产情况选取;[Mn]、[P]和[S]分别按铁水中相应成分含量的30%、10%和70%留在钢水中设定。 表2-2
14、原材料成分 成分含量/% 类别 CaO SiO2 MgO Al2O3 Fe2O3 CaF2 P2O5 S CO2 H2O C 灰分 挥发分 石灰 88.00 2.50 2.60 1.50 0.50 0.10 0.06 4.64 0.10 萤石 0.30 5.50 0.60 1.60 1.50 88.00 0.90 0.10 1.50 生白云石 36.40 0.80 25.60 1.00 36.20 炉衬 1.20 3.00 78.80 1.
15、40 1.60 14.00 焦炭 0.58 81.50 12.40 5.52 表2-3 铁合金成分(分子)及其回收率(分母) 成分含量/回收率% 类别 C Si Mn Ai P S Fe 硅铁 — 73.00/75 0.50/80 2.50/0 0.05/100 0.03/100 23.92/100 锰铁 6.60/90① 0.50/75 67.8/80 — 0.22/100 0.13/100 24.74/100 ①10 %与氧生成CO2。 表2-4 其他工
16、艺参数设定 名称 参数 名称 参数 终渣碱度 萤石加入量 生白云石加入量 炉衬损失量 终渣含量∑ω(FeO)含量(按向钢中传氧量ω(Fe2O3)=1.35ω(FeO)折算) 烟尘量 喷溅铁损 ω(CaO)/ω(SiO2)=3.5 为铁水量的0.5% 为铁水量的2.5% 为铁水量的0.3% 15%,而ω(Fe2O3)/ ∑ω(FeO)=1/3,ω(Fe2O3)=5% ,ω(FeO)=8.25% 为铁水量的1.5%(ω(FeO)为75%,ω(Fe2O3)为20%) 为铁水量的1% 渣中铁损(铁珠) 氧气浓度 炉气中自由氧的含量 气化去硫量 金
17、属中[C]的氧化产物 废钢量 为渣量的6% 99%,余者为N2 0.5%(体积比) 占总去硫量的1/3 90%C氧化成CO,10%C氧化成CO2 由热平衡计算确定,本次计算结果为铁水量的12.08%,即废钢比为10.78% 2.1.2 物料平衡基本项目 收入项目:铁水、废钢、溶剂(石灰、萤石、轻烧白云石)、氧气、炉衬蚀损、铁合金。 支出项目:钢水、炉渣、烟尘、渣中铁珠、炉气、喷溅。 2.1.3 计算步骤 (以100kg铁水为基础进行计算) 第一步:计算脱氧和合金化前的总渣量及其成分。 总渣量包括铁水中元素氧化,炉衬蚀损和加入熔剂的成渣量。其各项成渣量分别列于表
18、2-5~表2-7。总渣量及其成分如表2-8所示。 表2-5 铁水中元素的氧化产物及成渣量 元素 反应产物 元素氧化量/kg 耗氧量/kg 产物量/kg 备注 C Si Mn P S Fe [C]→{CO} [C] →{CO2} [Si] →(SiO2) [Mn] →(MnO) [P] →(P2O5) [S]→{SO2} [S]+(CaO)→(CaS)+(O) [Fe] →(FeO) [Fe] →(Fe2O3) 4.0090%=3.600 4.0010%=0.400 0.600 0.280 0.108 0.0181/3=0.00
19、6 0.0182/3=0.012 0.86856/72=0.675 0.487112/160=0.341 4.800 1.067 0.686 0.081 0.139 0.006 -0.006① 0.193 0.146 8.400 1.467 1.286 0.361 0.247 0.012 0.027 0.868 0.487 入渣 入渣 入渣 入渣 入渣(见表) 入渣(见表) 合计 6.022 7.112 成渣量 3.276(入渣组分之和) ①由CaO还原出的氧量;消耗的CaO量=0.01256/32=
20、0.021kg。 第二步:计算氧气消耗量。 氧气实际消耗量系消耗项目与供入项目之差。见表2-9 表2-6 炉衬损失成渣量 炉衬损失量/kg 成渣组分/kg 气态产物/kg 耗氧量/kg CaO SiO2 Mg Al2O3 Fe2O3 C→CO C→CO2 C→CO、CO2 0.3(据表2-4 ) 0.004 0.009 0.236 0.004 0.005 0.314%90% 28/12=0.088 0.314%10% 44/12=0.015 0.314%(90% 16/12+10%32/12) =0.062 合计 0.258 0.1
21、03 0.062 表2-7 加入溶剂的成渣量 类别 加入量/kg 成渣组分/kg 气态产物/kg CaO MgO SiO2 Al2O3 Fe2O3 P2O5 CaS CaF2 H2O CO2 O2 萤石 0.5(据表2-4) 0.002 0.003 0.028 0.008 0.008 0.005 0.001 0.440 0.005 生白云石 2.5(据表2-4) 0.910 0.640 0.020 0.025 0.905 石灰 5.16① 4.520② 0.134 0.129
22、0.077 0.026 0.005 0.007 0.005 0.239 0.002③ 合计 5.432 0.777 0.177 0.110 0.034 0.010 0.008 0.440 0.010 1.144 0.002 成渣量 6.988 ①石灰的加入量计算如下:由表2-5~表2-7可知,渣中以含有(CaO)= -0.021+0.004+0.002+0.910=0.895kg;渣中已含(SiO2)=1.286+0.009+0.028+0.020=1.424kg。因设定碱度R=3.5,故石灰加入量为:[R∑ω(SiO2)-∑ω(CaO
23、)]/[ ω(CaO石灰)-Rω(SiO2石灰)]=4.089/(88.0%-3.52.50%)=5.16kg。 ②(石灰中CaO含量) -(石灰中S→CaS自耗的CaO量)。 ③石灰中的S与CaO反应还原出来的氧量,计算方法同表2-5的标注。 表2-8 总渣量及其成分 炉渣成分 CaO SiO2 MgO Al2O3 MnO FeO Fe2O3 CaF2 P2O5 CaS 合计 元素氧化成渣量/kg 石灰成渣量/kg 炉衬损失成渣量/kg 生白云石成渣量/kg 萤石成渣量/kg 4.520 0.004 0.910 0.002 1.286
24、0.129 0.009 0.020 0.028 0.134 0.236 0.640 0.003 0.077 0.004 0.025 0.008 0.361 0.868② 0.487③ 0.026 0.005 0.008 0.440 0.247 0.005 0.005 0.027 0.007 0.001 3.276 4.898 0.258 1.595 0.495 总渣量/kg 5.436 1.472 1.013 0.114 0.361 0.868
25、0.526 0.440 0.257 0.035 10.522 质量分数/% 51.66 14.00 9.63 1.08 3.43 8.25 5.00 4.18 2.44 0.33 100 ①总渣量计算如下:因表中除了(FeO)和(Fe2O3)以外的渣量为: 5.436+1.472+1.103+0.114+0.361+0.440+0.257+0.035=9.128kg。而终渣∑ω(FeO)=15%,所以总渣量为:9.12886.75%=10.522kg。 ②ω(FeO)=10.5228.25%=0.868kg。 ③ω(Fe2O3)=10.5225%-0.0
26、26-0.005-0.008=0.487kg。 表2-9 实际耗氧量 耗氧量/kg 供氧量/kg 实际氧气 消耗量/kg 铁水中元素氧化耗氧量(表2-5) 7.112 炉衬中碳氧化耗氧量(表2-6) 0.062 石灰中S与CaO反应还原出的氧化量(表)0.002 烟尘中铁氧化耗氧量(表2-4) 0.34 7.573-0.002+ 0.068①=7.639 炉气自由氧含量(表2-10) 0.059 合计 7.573 合计 0.002 ①炉气N2(存在于氧气
27、中,见表2-4)的质量,详见表2-10。 第三步:计算炉气量及其成分。 炉气中含有CO、CO2、N2、SO2、和H2O。其中CO、CO2、SO2和H2O可由表2-5~2-7表查得,O2和N2则由炉气总体积来确定。现计算如下: 炉气总体积VΣ: 式中: Vg——CO、CO2、SO2和H2O各组分总体积,m3。本计算中,其值为: 8.48822.4/28+2.62622.4/44+0.01222.4/64+0.01022.4/18=8.144 m3; Gs——不计自由氧的氧气消耗量,kg。本计算中,其值为:7.112+0.062+0.34=7.514kg(见表2
28、-9); Vx——石灰中的S与CaO反应还原出的氧量(其质量为:0.002kg,见表(2-9)与铁水中的S与CaO反应还原出的氧量之和(其质量为:0.006kg),m3; 0.5% ——炉气中自由氧含量; 99 ——自由氧纯度为99%转换得来。 计算结果列于表2-10。 第四步:计算脱氧和合金化前的钢水量。 钢水量Qg = 铁水量―铁水中元素的氧化量―烟尘、喷溅和渣中的铁损=100-6.022-[1.50(75%56/72+20%112/160)+1+10.5226%]=91.262kg 据此可以编制出未加废钢、脱氧与合金化前的物料平衡表2-11。 表2-10 炉气量及其成分
29、 炉气成分 炉气量/kg 体积/m3 体积分数/% CO CO2 SO2 H2O O2 N2 8.488 2.626 0.012 0.010 0.059① 0.068② 8.48822.24/28=6.790 2.62622.24/44=1.377 0.01222.24/64=0.004 0.01022.24/18=0.013 0.041① 0.054② 82.01 16.63 0.05 0.16 0.50 0.65 合计 11.263 8.279 100.00 ①炉气中O2的体积为8.1440.5%=0.041 m3;质量为0.
30、04132/22.4=0.059kg。 ②炉气中N2的体积系炉气总体积与其他成分的体积之差;质量为0.05428/22.4=0.068kg。 表2-11 未加废钢时的物料平衡表 收入 支出 项目 质量/kg % 项目 质量/kg % 铁水 石灰 萤石 生白云石 炉衬 氧气 100.00 5.16 0.50 2.50 0.30 7.64 86.13 4.45 0.43 2.15 0.26 6.58 钢水 炉渣 炉气 喷溅 烟尘 渣中铁珠 91.26 10.52 11.26 1.00 1.50 0.63 78.56
31、 9.06 9.69 0.86 1.29 0.54 合计 116.10 100.00 合计 116.17 100.00 注:计算误差为(116.10-116.17)/116.10100%=-0.06%。 第五步:计算加入废钢的物料平衡。(先进行热平衡计算确定废钢加入量) 如同“第一步”计算铁水中元素氧化量一样,利用表2-1的数据先确定废钢中元素的氧化量及其耗氧量和成渣量(表2-12),再将其与表2-11归类合并,遂得加入废钢后的物料平衡表2-13和表2-14。 表2-12 废钢中元素的氧化产物及其成渣量 元素 反应产物 元素氧化量/kg 耗氧量/kg 产物
32、量/kg 进入钢中的量/kg C Si Mn P S [C]→{CO} [C] →{CO2} [Si] →(SiO2) [Mn] →(MnO) [P] →(P2O5) [S] →{SO2} [S]+(CaO)→(CaS)+(O) 12.080.08%90%=0.009 12.080.08%10%=0.001 12.080.25%=0.030 12.080.43%=0.052 12.080.018%=0.002 12.08(-0.012%)1/3=0.000 12.08(-0.012%)2/3=0.000 0.012 0.003 0.034
33、 0.015 0.003 0.000 0.000 0.021(入气) 0.004(入气) 0.064 0.067 0.005 0.000 0.000 合计 0.094 0.067 12.08-0.094=11.986 成渣量(kg) 0.161 表2-13 加入废钢的物料平衡表(以100kg铁水为基础) 收入 支出 项目 质量/kg % 项目 质量/kg % 铁水 废钢 石灰 萤石 轻烧生白云石 炉衬 氧气 100.00 12.08 5.16 0.50 2.50 0.30 7.64+0.067
34、=7.707 77.98 9.42 4.02 0.39 1.95 0.23 6.01 钢水 炉渣 炉气 喷溅 烟尘 渣中铁珠 91.26+11.986=103.246 10.52+0.161=10.681 11.26+0.025=11.285 1.00 1.50 0.63 80.45 8.32 8.79 0.78 1.17 0.49 合计 128.247 100.00 合计 128.342 100.00 注:计算误差为(128.247-128.342)/128.247=-0.07%。 表2-14 加入废钢的物料平衡表(以100k
35、g(铁水+废钢)为基础) 收入 支出 项目 质量/kg % 项目 质量/kg % 铁水 废钢 石灰 萤石 生白云石 炉衬 氧气 89.22 10.79 4.60 0.44 2.23 0.26 6.88 77.98 9.42 4.02 0.39 1.95 0.23 6.01 钢水 炉渣 炉气 喷溅 烟尘 渣中铁珠 92.12 9.53 10.07 0.89 1.34 0.56 80.45 8.32 8.79 0.78 1.17 0.49 合计 114.42 100.00 合计 11
36、4.51 100.00 第六步:计算脱氧和合金化后的物料平衡。 先根据钢种成分设定值(表2-1)和铁合金成分及其回收率(表2-3锰铁和硅铁的加入量,再计算其元素的烧损量。将所有结果与表2-14,即得冶炼一炉钢的总物料平衡表。 锰铁加入量WMn为: 硅铁加入量WSi为: 铁合金中元素的烧损量和产物量列于表2-15。 表2-15 铁合金元素烧损量及其产物量 类别 元素 烧损量/kg 脱氧量/kg 成渣量/kg 炉气量/kg 入钢量/kg 锰 铁 C Mn Si P S Fe 合计 0.636.60%10%=0.004 0.6
37、367.80%20%=0.085 0.630.50%25%=0.001 0.090 0.010 0.024 0.001 0.035 0.109 0.002 0.111 0.015(CO2) 0.015 0.636.60%90%=0.037 0.6367.80%80%=0.342 0.630.50%75%=0.002 0.630.23%=0.001 0.630.13%=0.001 0.6324.74%=0.156 0.539 硅 铁 Al Mn Si P S Fe 合计 0.422
38、.50%100%=0.011 0.420.50%20%=0.0004 0.4273.00%25%=0.077 0.088 0.010 0.0001① 0.088 0.098 0.006 0.0005 0.165 0.172 0.420.50%80%=0.002 0.4273.00%75%=0.230 0.420.05%=0.0002① 0.420.03%=0.0001① 0.4223.92%=0.100 0.332 总计 0.178 0.133 0.283 0.015 0.871 ① 可以忽略不计。
39、脱氧和合金化后的钢水成分如下: w(C)=0.10%+0.037/92.99100%=0.14% w(Si) = (0.002+0.230)/92.99100%=0.25% w(Mn)=0.120%+(0.342+0.002)/92.99100%=0.49% w(P)=0.012%+0.001/92.99100%=0.013% w(S)=0.042%+0.001/92.99100%=0.043% 可见,含碳量尚未达到设定值。为此需在钢包内加焦粉增碳。其加入量W1为: 焦粉生成的产物如下: 碳烧损量/kg 耗氧量/kg 气体量/kg① 成渣量/kg 碳入钢量/kg
40、0.0681.50%25% =0.012 0.032 0.044+0.06(0.58+5.52)% =0.047 0.0612.40% =0.007 0.0681.50%75% =0.037 ① H2O、CO2和挥发分的总和(未计算挥发分燃烧的影响)。 由此可得冶炼过程(即脱氧和合金化后)的总物料平衡表2-16 。 表2-16 总物料平衡表 收入 支出 项目 质量/kg % 项目 质量/kg % 铁水 废钢 石灰 萤石 生白云石 炉衬 氧气 锰铁 硅铁 焦粉 89.22 10.79 4.60 0.44 2.23 0.26
41、7.05① 0.63 0.42 0.06 77.11 9.33 3.98 0.38 1.93 0.22 6.09 0.55 0.36 0.05 钢水 炉渣 炉气 喷溅 烟尘 渣中铁珠 93.03(92.12+0.871+0.037) 9.82(9.53+0.283+0.007) 10.13(10.07+0.015+0.047) 0.88 1.33 0.40 80.48 8.50 8.76 0.76 1.15 0.35 合计 115.70 100.00 合计 115.59 1
42、00.00 ①7.05=6.88+0.133+0.032,可以近似的认为(0.133+0.032)的氧量系出钢水二次氧化带入。 注:计算误差为(115.70-115.59)/115.70100%=0.10%。 2.2 热平衡计算[1] [2] [3] 2.2.1 计算所需原始数据 计算所需基本原始数据有:各种入炉料及产物(表 );物料平均热容(表 );反应热效应(表 );溶入铁水中的元素对铁熔点的影响(表 )。其他数据参照物料平衡选取。 表2-17 入炉物料及产物的温度设定值 名称 入炉物料 产物 铁水 废钢 其他原料 炉渣 炉气 烟尘 温度/℃ 1310
43、 25 25 与钢水相同 1450 1450 ①纯铁熔点为1536℃。 表2-18 物料平均热容 物料名称 生铁 钢 炉渣 矿石 烟尘 炉气 固态平均热容/KJ(kgK)-1 0.745 0.699 — 1.047 0.996 — 溶化潜热/KJkg-1 218 272 209 209 209 — 液态或气态平均热容/KJ(kgK)-1 0.837 0.837 1.248 — — 1.137 表2-19 炼钢温度下的反应热效应 组元 化学反应 △H/KJkmol-1 △H/KJkg-1 C C Si Mn
44、 P Fe Fe SiO2 P2O5 CaCO3 MgCO3 [C]+1/2{O2}={CO} 氧化反应 [C]+{O2}={CO2} 氧化反应 [Si]+{O2}=(SiO2) 氧化反应 [Mn]+1/2{O2}=(MnO) 氧化反应 2[P]+5/2{O2}=(P2O5) 氧化反应 [Fe]+1/2{O2}=(FeO) 氧化反应 2[Fe]+3/2{O2} =(Fe2O3) 氧化反应 (SiO2)+2(CaO)=(
45、2CaOSiO2) 成渣反应 (P2O5)+4(CaO)=(4CaOP2O5) 成渣反应 CaCO3=(CaO)+{CO2} 分解反应 MgCO3=(MgO)+{CO2} 分解反应 -139420 -418072 -817682 -361740 -1176563 -238229 -722432 -97133 -693054 169050 118020 -11639 -34834 -29202 -6954 -18980 -4250 -6460 -1620 -4880 1690 1405 表2-20
46、 溶入铁水中元素对铁水熔点的降低值 元素 C Si Mn P S Al Cr N、H、O 在铁中的极限溶解度/% 5.41 618.5 无限 2.8 0.18 35.0 无限 溶入1%元素使铁熔点降低值/℃ 65 70 75 80 85 90 100 8 5 30 25 3 1.5 氦、氮、氧溶入使铁熔点降低值/℃ ∑=6 使用含量范围.% <1 1.0 2.0 2.5 3.0 3.5 4.0 ≤3 ≤15 ≤0.7 ≤0.08 ≤1 18
47、 2.2.2 计算步骤 以100kg铁水为基础 第一步:计算热收入Qs。 热收入项包括:铁水物理热;元素氧化热及成渣热;烟尘氧化热;炉衬中碳的氧化热。 (1)铁水物理热Qw;现根据表纯铁熔点、铁水成分以及溶入元素对铁熔点的降低值(表2-17、表2-1和表2-20)计算铁水熔点Tt,然后由铁水温度和生铁热容(表2-17和表2-18)确定Qw。 Tt =1536-(4.1100+0.68+0.45+0.1230+0.0625)-6=1108.1℃ Qw =100[0.745(1108.1-25)+218+0.837(1310-1108.1)]=119389.98kJ (2)元素
48、氧化热及成渣热Qy:由铁水中元素氧化量和反应热效应(表2-19 )可以算出,其结果列于表2-21。 表2-21 元素氧化热和成渣热 反应产物 氧化热或成渣热/kJ 反应产物 氧化热或成渣热/kJ C→CO 3.60011639=41900.40 Fe→Fe2O3 0.3416460=2202.86 C→CO2 0.40034834=13933.60 P→P2O5 0.10818980=2049.84 Si→SiO 0.60029202=17521.20 P2O5→4CaOP2O5 0.2574880=1254.16 Mn→MnO 0.2806594=184
49、6.32 SiO2→2CaOSiO2 1.4721620=2384.64 Fe→FeO 0.6754250=2868.75 合计Qy 85961.77 (3)烟尘氧化热Qc:由表2-4中给出的烟尘量参数和反应热效应计算可得。 Qc=1.5(75%56/724250+20%112/1606460)=5075.35kJ (4)炉衬中碳的氧化热Q1:根据炉衬蚀损量及其含碳量确定。 Q1=0.314%90%11639+0.314%10%34834=586.25kJ 故热收入总值为: Qs= Qw +Qy+Qc+ Q1=211013.35kJ 第二步:计算热支出Qz。 热
50、支出项包括:钢水物理热、炉渣物理热、烟尘物理热、炉气物理热、渣中铁珠物理热、喷溅物(金属)物理热、轻烧白云石分解热、热损失、废钢吸热。 (1)钢水物理热Qg: 钢水熔点Tg=1536-(0.1065+0.185+0.02030+0.04225 )-6=1521℃ 式中,0.10、0.18、0.020和0.042分别为终点钢水C、Mn、P、S的含量。 出钢温度Tz=1521+50+50+70=1691℃ 式中,50、50和70分别为出钢过程中温降、镇静及炉后处理过程中的温降和过热度。 Qg=91.26[0.699(1521-25)+272+0.837(1691-1521)]=1332
51、39.05kJ (2)炉渣物理热Qr:令终渣温度与钢水温度相同,则得: Qr=10.522[1.248(1691-25)+209]=24076.10kJ (3)炉气、烟尘、铁珠和喷溅金属的物理热Qx。根据其数量、相应的温度和热容确定。详见表2-22。 表2-22 某些物料的物理热 项目 参数/kJ 备注 炉气物理热 11.263[1.137(1450-25)]=18248.59 1450℃系炉气和烟尘的温度 烟尘物理热 1.5[0.996(1450-25)+209]=2442.45 渣中铁珠物理热 0.63[0.699(1521-25)+272+0.837(16
52、91-1521)] =919.80 1521℃系钢水熔点 喷溅金属物理热 1[0.699(1521-25)+272+0.837(1691-1521)] =1459.99 合计 Qx =23070.83 (4)轻烧白云石分解热Qb:根据其用量、成分和表2-19所示的热效应计算。 Qb = 2.5(36.40%1690+25.60%1405) = 2437.10 kJ (5)热损失Qq:其他热损失带走的热量一般占总热收入的3%~8%。本计算取5%,则得: Qq =211013.355% = 10550.67 kJ (6)废钢吸热Qf:用于加热废钢的热量系声誉热量
53、,即: Qf = Qs―Qg―Qr―Qx―Qb―Qq = 17639.60 kJ 故废钢加入量Wf为: Wf =17639.60{1[0.699(1521-25)+272+0.837(1691-1521)]} =12.08kg 即废钢比为: 若不计算炉渣带走的热量时: 第三步:列出热平衡表(表2-23)。 表2-23 热平衡表 收入 支出 项目 热量/KJ % 项目 热量/KJ % 铁水物理热 元素氧化和成渣热 其中C氧化 Si氧化 Mn氧化 P氧化 Fe氧化 P2O5 成渣 SiO2 成渣 烟尘氧化热 炉衬中
54、碳的氧化热 119389.98 85961.77 55834.00 17521.20 1846.32 2049.84 5071.61 1254.16 2384.64 5075.35 586.25 56.58 40.74 26.46 8.30 0.88 0.97 2.40 0.60 1.13 2.40 0.28 钢水物理热 炉渣物理热 废钢吸热 炉气物理热 烟尘物理热 渣中铁珠物理热 喷溅金属物理热 轻烧白云石分解热 热损失 133239.05 24076.10 17639.60 18248.59 2442.45 919.
55、80 1459.99 2437.10 10550.67 63.14 11.41 8.36 8.65 1.16 0.44 0.69 1.15 5.00 合计 21101.35 100.00 合计 21101.35 100.00 应当指出,加入铁合金进行脱氧和合金化,会对热平衡数据产生一定的影响。对转炉用一般生铁冶炼低碳钢来说,所用铁合金种类有限,数量也不多。经济计算,其热收入部分约占总热收入的0.8%~1.0%,热支出部分约占0.5%~0.8%,二者基本持平。 参考文献: [1] 王令福. 钢铁厂设计原理[M].北京:冶金工业出版社,2009. [2] 李传薪. 钢铁厂设计原理[M].北京:冶金工业出版社,1995. [3] 贾凌云. 转炉—连铸工艺设计与程序.北京:冶金工业出版社,2005. 18 / 19
- 温馨提示:
1: 本站所有资源如无特殊说明,都需要本地电脑安装OFFICE2007和PDF阅读器。图纸软件为CAD,CAXA,PROE,UG,SolidWorks等.压缩文件请下载最新的WinRAR软件解压。
2: 本站的文档不包含任何第三方提供的附件图纸等,如果需要附件,请联系上传者。文件的所有权益归上传用户所有。
3.本站RAR压缩包中若带图纸,网页内容里面会有图纸预览,若没有图纸预览就没有图纸。
4. 未经权益所有人同意不得将文件中的内容挪作商业或盈利用途。
5. 装配图网仅提供信息存储空间,仅对用户上传内容的表现方式做保护处理,对用户上传分享的文档内容本身不做任何修改或编辑,并不能对任何下载内容负责。
6. 下载文件中如有侵权或不适当内容,请与我们联系,我们立即纠正。
7. 本站不保证下载资源的准确性、安全性和完整性, 同时也不承担用户因使用这些下载资源对自己和他人造成任何形式的伤害或损失。
最新文档
- 36个关键词详解2025政府工作报告
- 学习2025年政府工作报告中的八大科技关键词
- 2025年政府工作报告要点速览接续奋斗共谱新篇
- 学习2025政府工作报告里的加减乘除
- 深化农村改革党课ppt课件(20250305)
- 弘扬雷锋精神凝聚奋进力量学习雷锋精神的丰富内涵和时代价值
- 深化农村改革推进乡村全面振兴心得体会范文(三篇)
- 2025年民营企业座谈会深度解读PPT课件
- 领导干部2024年述职述廉述责述学述法个人报告范文(四篇)
- 读懂2025中央一号党课ppt课件
- 2025年道路运输企业主要负责人安全考试练习题[含答案]
- 2024四川省雅安市中考英语真题[含答案]
- 2024湖南省中考英语真题[含答案]
- 2024宁夏中考英语真题[含答案]
- 2024四川省内江市中考英语真题[含答案]