制动盘铸造工艺分析及工装设计
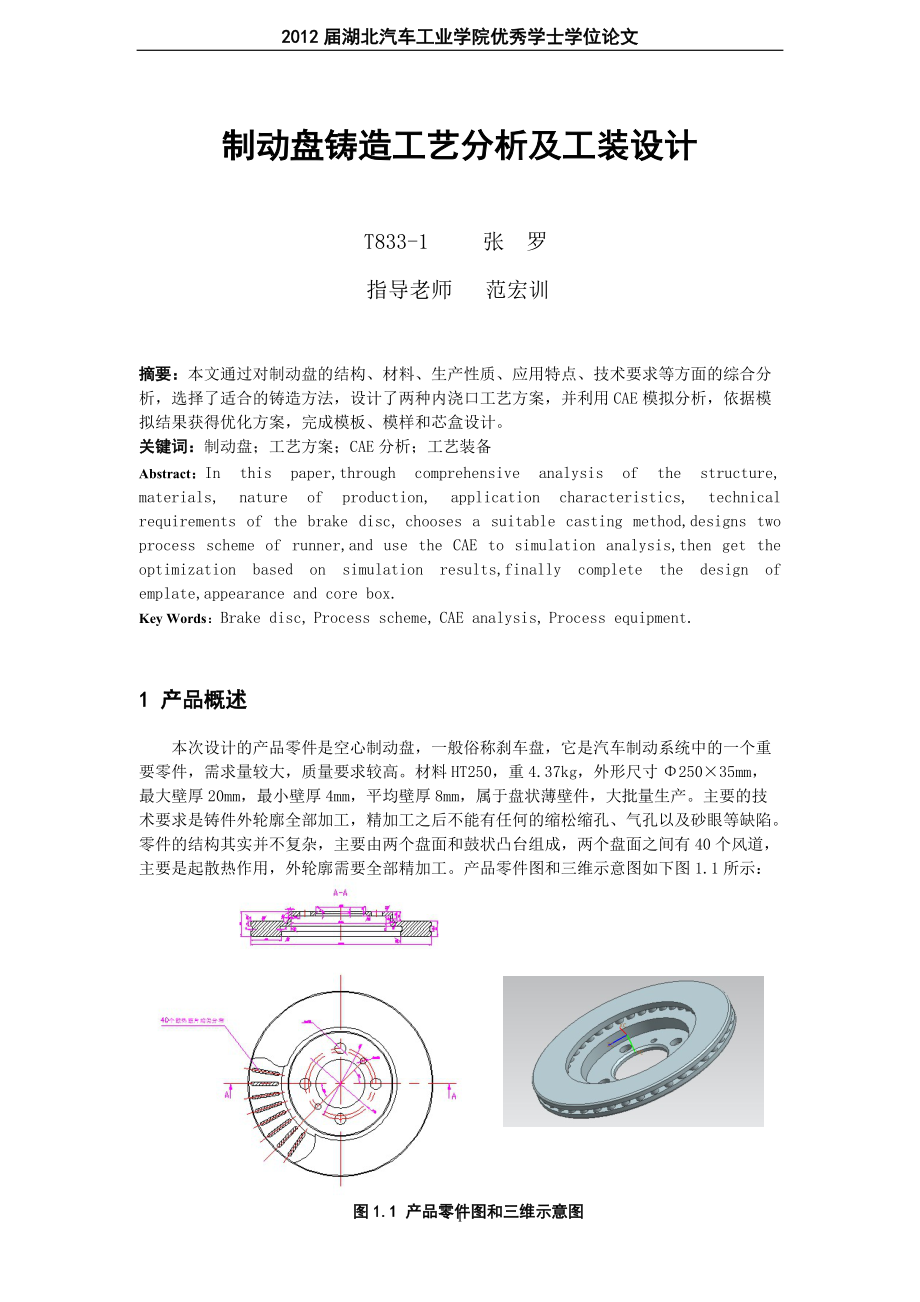


《制动盘铸造工艺分析及工装设计》由会员分享,可在线阅读,更多相关《制动盘铸造工艺分析及工装设计(10页珍藏版)》请在装配图网上搜索。
1、2012届湖北汽车工业学院优秀学士学位论文 制动盘铸造工艺分析及工装设计 T833-1 张 罗 指导老师 范宏训 摘要:本文通过对制动盘的结构、材料、生产性质、应用特点、技术要求等方面的综合分析,选择了适合的铸造方法,设计了两种内浇口工艺方案,并利用CAE模拟分析,依据模拟结果获得优化方案,完成模板、模样和芯盒设计。 关键词:制动盘;工艺方案;CAE分析;工艺装备 Abstract:In this paper,through comprehensive analysis of the structure, materials, nature of prod
2、uction, application characteristics, technical requirements of the brake disc, chooses a suitable casting method,designs two process scheme of runner,and use the CAE to simulation analysis,then get the optimization based on simulation results,finally complete the design of emplate,appearance and cor
3、e box. Key Words:Brake disc, Process scheme, CAE analysis, Process equipment. 1 产品概述 图1.1 产品零件图和三维示意图 本次设计的产品零件是空心制动盘,一般俗称刹车盘,它是汽车制动系统中的一个重要零件,需求量较大,质量要求较高。材料HT250,重4.37kg,外形尺寸Φ25035mm,最大壁厚20mm,最小壁厚4mm,平均壁厚8mm,属于盘状薄壁件,大批量生产。主要的技术要求是铸件外轮廓全部加工,精加工之后不能有任何的缩松缩孔、气孔以及砂眼等缺陷。零件的结构其实并不复杂,主要由两个盘面和鼓状凸台
4、组成,两个盘面之间有40个风道,主要是起散热作用,外轮廓需要全部精加工。产品零件图和三维示意图如下图1.1所示: 10 2 铸造工艺方案的拟定 2.1 铸造方法及设备的选择 对于此类大批量生产的薄壁盘式铸件,选择粘土湿型砂,由零件的结构特点、凝固技术以及便于下芯等方面考虑吧,水平分型优于垂直分型,终上所述,我们选择水平分型高压自动生产线,铸件的风道和内腔由砂芯成形,且采用整体式砂芯结构,使用热芯盒法,覆膜砂成形[1]。 2.2 分型面的选择 在分型面的选择上,提出了以下三种方案,如下图2.1所示:第一种方案保证了大部分铸件
5、位于下箱,但是这时候还有三分之一的铸件位于上面,而且位于上箱的铸件部分属于薄壁,增加了铸件产生缺陷的可能性;第二种方案可以减少加工量,因为风道是没有精度要求的,但是这样金属液从下腔通过砂芯充填上腔,阻力较大;第三种方案,我们可以将所有的铸件位于下箱,降低出现缺陷的可能性,但是这样增加了内浇口的设计开设难度,但是这种方案还有一个优点,就是减少了由于分型面上铁液渗透所产生的毛边,减少后期精整量,这在大批量生产中极为重要。综合考虑,我们选择方案Ⅲ。 图2.1 分型面方案示意图 2.3铸件浇注位置的确定 分型面选择方案Ⅲ,此时较好的选择就是将全部铸件位于下箱,这也是较合理
6、的方法。将内浇口位置选择在第一个盘面的边缘,为了减少砂芯的结构和便于工人快速下芯,采用压边式内浇口设计[2]。如下图2.2所示: 内浇口位置 图2.2 浇注系统和内浇口位置 2.4 砂芯设计 考虑到铸件的结构特点和生产效率,采用整体式砂芯设计,覆膜砂成形,为了使砂芯在型腔内有准确的定位和稳固的固定,该砂芯设计了两个垂直芯头,用来支撑和固定整个砂芯。砂芯内部采用空心结构,不仅可以减少材料的使用量,且便于砂芯散热[3],砂芯壁厚取10mm。其结构和尺寸如图2.3所示。 2.5 铸造工艺参数的选择 按照铸造工艺手册选取铸造工艺参数,机械加工余量全部取2
7、.5mm;拔模斜度1;铸造收缩率取1%;铸件上有很多孔,考虑到精度和表面粗糙度的要求,故4个Φ15的通孔和2个Φ8通孔采用机械加工的方法成形,其余通孔和风道直接铸出[2]。 图2.3 砂芯结构尺寸示意图 3 浇注系统初步设计 3.1 浇注系统的类型选择及结构设计 本铸件属于薄壁小件,根据上述浇注位置和分型面的选择,在此采用顶注式、封闭式浇注系统,封闭式浇注系统组元截面积比取∑A内:∑A横:A直=1:1.2:1.4。在浇注系统结构设计方面,为了简化砂芯结构并提高下芯速度,将内浇口开设在上箱,采用压边式内浇口设计,并设计了两种内浇口方案。方案一采
8、用1个铸件1个内浇口引入,方案二使用1个铸件2个内浇口引入。方案一和方案二结构示意图如下图3.1所示: 方案一 1个铸件1个内浇口 方案二 1个铸件2个内浇口 图3.1 内浇口设计方案示意图 3.2 浇注系统的计算 浇注系统最小阻流截面积的计算,参照水力学计算公式进行计算: [4] 其中:∑F内为内浇道截面积,G件=6.24kg,μ=0.5,τ=5.5s,Hp=H0=250mm。求出: ∑F内= ==1.46cm2 最后取∑F内=1.6cm2,算出横浇道截面积为:∑A横=∑A内1.2=1.61.2=1.92cm2。取∑A横
9、=2 cm2,直浇道截面积为:A直=∑A横1.4=1.61.4=2.24cm2,取A直=2.4 cm2。最后根据铸造工艺手册查出方案一和方案二浇注系统各组员结构和尺寸,如下表3.2所示: 表3.2 方案一和方案二浇注系统各组元截面尺寸 内浇道 横浇道 直浇道 方案一 (1个铸件1个内浇口引入) 方案二 (1个铸件2个内浇口引入) 3.3 冒口的设计 此铸件材料为HT250,灰铸铁的结晶范围窄,更接近于层状凝固,凝固时的膨胀和液态收缩趋于互相补偿,所以灰铸铁补缩需要的铁水量少,铸型刚度要求较低,一般的
10、灰铸铁可不设置冒口。本铸件的体积为607.5cm3,表面积为1954.7cm2,平均模数为0.31cm,模数较小,且在实际生产中也常使用无冒口铸造。 本次设计的两种方案均采用无冒口设计,下面通过CAE模拟来分析方案的合理性并根据分析结果对其进行优化。 4 CAE模拟与优化 对于浇注系统方案一(1个铸件1个内浇口引入)与方案二(1个铸件2个内浇口引入),均采用ProCAST进行CAE模拟分析。本次模拟所设置的参数主要有:浇注温度1400℃,浇注速度4.88 in/s,传热系数500 W/m2/K,重力加速度9.8m/s2,型砂初始温度25℃,最后采用空冷的方式进行冷却[5]。 针
11、对两种方案的模拟结果,就充型过程、凝固过程、缩松缩孔预测和裹气等方面进行了比较和分析。如下图4.1、图4.2、图4.3和图4.4所示: 方案一 方案二 图4.1 两种方案的金属液充型过程 图4.3 两种方案的缩松缩孔预测 图4.2 两种方案的凝固时间分布 图4.4 两种方案的裹气充气分布 根据以上模拟的结果,对方案一和方案二进行了对比,发现方案二在充型能力、充型时间、凝固时间和缩松缩孔等方面都要优于方案一,但是方案二在充气裹气方面仍然存在很大
12、的不足,很容易出现气孔等缺陷,且无法消除缩松缩孔缺陷。前面已经提到,此铸件应用于汽车制动系统中,性能要求和质量要求极其严格,不允许出现气孔、缩松缩孔等缺陷,因此,在分析和综合了两种方案之后,提出了浇注系统的优化方案。 优化方案主要是在方案二的基础上加以优化和改进,仍采用1个铸件2个内浇口引入,主要的改变即是在内浇口和横浇道之间增加了一个冒口,使由横浇道引入的金属液先进入冒口,再经冒口引入内浇道,最后引入型腔。 本次冒口的设计采用模数法计算,并通过ε(V件+V冒)+Ve≦V冒η 验算公式进行验证,最终验证此次设计的冒口具有足够的补缩能力。最后根据铸造工艺设计手册,查出冒口和冒口颈的尺寸,冒口
13、直径D=Φ60mm,高度H=70mm,冒口颈截面积尺寸2aa(矩形)=2412mm。 针对优化方案,进行了与方案一和方案二同样的ProCAST模拟,参数设置一致,最终得到了优化方案的模拟结果,如下图4.5、图4.6、图4.7和图4.8所示: 图4.6 优化方案凝固时间分布 图4.5 优化方案金属液充型过程 图4.7 优化方案缩松缩孔预测 图4.8 优化方案裹气充气分布 由上图所示,可以看出,方案三充型过程和方案二并不差别,且增加冒口之后,基本上消除了缩松缩孔缺陷,同时大幅度降低了铸件出现充气裹气的范围,有效地降
14、低了出现气孔的可能性,达到了预期的效果。综上所述,方案三是最优方案,本次设计采用方案三。 5 模板的设计 该铸件属于成批大量生产的小件,选用HT200做模板材料,采用普通单面顶箱式模板。采用水平分型自动生产线的模底板尺寸与结构,采用的模板基本尺寸为1200mm690mm,砂箱内框尺寸为920mm610mm250mm[6]。 一箱放置3件,模样对称分布在下模板上,同时直浇道窝以及与直浇道相连的一段横浇道布置在下模板,其余浇注系统以及冒口等布置在上模板,浇注系统与模底板的固定,采用六角螺钉和沉头螺钉固定。上下模板如下图5.1、图5.2所示: 图5.1 上模板二维及三维示意图
15、 图5.2 下模板二维及三维示意图 6 模样的设计 由于采用大批量生产,选择金属模样,根据各金属模样材料的性能和适用范围,选用灰铸铁作为模样材料,牌号为HT150。 图6.1 下摸样二维和三维示意图 下模样的结构较简单,主要由几个圆形凸台形成,由于模样整体高度不大,故采用实心模样。模样最大平面边缘由芯头形成了宽25,高15.5的延伸圆台,刚好可以用来固定模样。1个模样使用4个沉头圆柱头螺钉固定,螺钉穿过模样装配在模底板上,对称分布,螺钉尺寸为M10;此外,使用2个定位销定位,也是穿过模样装配在模底板上,定位销尺寸d(定位
16、销直径)为10mm。下模样如图6.1所示: 7 芯盒的设计 此次设计的砂芯由覆膜砂成形,采用热覆膜法生产工艺[7],为节约成本和提高生产效率,一次生产4件。芯盒各部分的材料,大部分采用HT250,例如芯盒本体、顶芯板、底框等,另外还有45刚,例如定位销,顶芯杆等。 7.1 热芯盒本体设计 为加工制造方便,提高生产率,将分盒面选在砂芯最大平面处,由于边缘的圆形凹槽无法取出,故在凹槽处采用折线分盒,如图7.1所示。为了便于制造,芯盒采用类似于正方体的形状,4个型芯腔均匀分布,如图7.2所示。将射砂口选择在芯头部位和最大断面处,一个砂芯使用12个射
17、砂口,12个射砂口均匀对此分布,为了降低射砂口的磨损,便于更换,故增设衬套,如图7.3所示。 图7.1 分盒面示意图 图7.3 射砂孔及衬套示意图 图7.2上、下芯盒三维示意图 7.2 热芯盒定位及排气设计 上、下芯盒使用压板紧固式热芯盒定位销(套)定位,整个芯盒使用4个定位销和定位销套来实现定位,如图7.4所示。排气方面,由于芯头处有间隙,则只在型芯较深部位开设了6个排气塞进行排气,如图7.5所示。 图7.5排气塞分布及结构示意图 图7.4定位销分布及定位销(套)结构示意图 7
18、.3取芯方式的确定及其结构设计 根据芯盒和型芯的结构特点,这里选用顶杆取芯法进行取芯,一个型芯使用9个顶芯杆,顶芯杆分布在型芯厚大部位和受阻力最大处,另外使用4个回位导杆进行复位。顶芯杆和回位导杆通过固定板与顶芯杆进行固定,顶芯板下设置8根加强筋,另外使用4个Φ40的凸台供射芯机顶芯使用。如下图7.6所示: 图7.6 顶芯杆及顶芯板结构示意图 7.4 热芯盒加热方式的选择 图7.7加热管道分布示意图 热芯盒采用电加热法进行加热,电加热法具有加热均匀、清洁、效率高且易于自动控温等优点。主要使用电加热管进行加热,因此分别在上、下芯盒
19、各设计了11个加热管道,总共是22个。如图7.7所示: 7.5 底框的设计 为了减少加热板的热量传到运输小车的工作台,在芯盒与运输小车工作台之间设置一个过渡零件--底框。这里为了节约材料,减轻芯盒整体重量,采用较为简单的底框结构设计,材料选用HT250,底框主要是通过6个凸台与下芯盒进行固定和定位,如图7.8所示: 图7.8 底框三维示意图及与固定方式 参考文献 [1] 叶荣茂、吴维冈、高景艳 《铸造工艺课程设计手册》[M] 哈尔滨:哈尔滨工业大学出版社,1988.5 [2] 中国铸造协会 《铸造工程师手册》[M] 北
20、京:机械工业出版社,2010.10 [3] 周述积、侯英玮、茅鹏 《材料成型工艺》[M] 北京:机械工业出版社, 2005.7 [4] 董选普 李继强 《铸造工艺学》[M] 北京:化学工业出版社,2009.8 [5] 李日 《铸造工艺仿真PrOCAST从入门到精通》[M] 北京:中国水利水电出版社,2010.9 [6] 朱广华、马强、钱绍嵩等 《铸造工艺装备设计手册》[M] 北京:机械工业出版社,1989.5 [7] 石德全、康福伟 《造型材料》[M] 北京:北京大学出版社,2009.9 [8] 大连理工大学工程图学教研室 《机械制图(第六版)》 北京:高等教育出版社,2007.7 [9] 甘永立 《几何量公差与检测(第八版)》[M] 上海:上海科学技术出版社,2008.1 [10] 盛龙海、杨彬、杨英栋等 《垂直造型和水平造型生产刹车盘经济技术比较分析》[J] 金属加工 2009,1:64-66 [11] 袁森、王武孝 《汽车刹车盘铸件生产工艺、缺陷分析与对策》[J] 铸造技术 2000,5(49):301-304 [12] 盛龙海、杨彬、谢庆智等 《一种汽车刹车盘铸件缩松缩孔缺陷的解决方法》[J] 铸造技术 2009,2(30):148-150
- 温馨提示:
1: 本站所有资源如无特殊说明,都需要本地电脑安装OFFICE2007和PDF阅读器。图纸软件为CAD,CAXA,PROE,UG,SolidWorks等.压缩文件请下载最新的WinRAR软件解压。
2: 本站的文档不包含任何第三方提供的附件图纸等,如果需要附件,请联系上传者。文件的所有权益归上传用户所有。
3.本站RAR压缩包中若带图纸,网页内容里面会有图纸预览,若没有图纸预览就没有图纸。
4. 未经权益所有人同意不得将文件中的内容挪作商业或盈利用途。
5. 装配图网仅提供信息存储空间,仅对用户上传内容的表现方式做保护处理,对用户上传分享的文档内容本身不做任何修改或编辑,并不能对任何下载内容负责。
6. 下载文件中如有侵权或不适当内容,请与我们联系,我们立即纠正。
7. 本站不保证下载资源的准确性、安全性和完整性, 同时也不承担用户因使用这些下载资源对自己和他人造成任何形式的伤害或损失。
最新文档
- 2025年水电工程运行维护管理合同示范文本.docx
- 2025年工程勘测设计合同模板.docx
- 2025年区域产品销售代理合同.docx
- 2025年经销商授权合同样本.docx
- 2025年员工住房资金借贷合同.docx
- 2025年轻钢建筑施工合同示例.docx
- 2025年网络推广托管合同.docx
- 2025年简明个人借款正式合同范例.docx
- 2025年房产按揭贷款合同范例.docx
- 2025年技术合同争议调解.docx
- 2025年电子版城市住宅租赁合同范本.docx
- 2025年简易转让合同协议书样本.docx
- 2025年投资顾问服务合同实例.docx
- 2025年经销合同模板.docx
- 2025年工业项目设计合同样本.docx