卧式单面多轴钻孔组合机床动力滑台液压系统课程设计
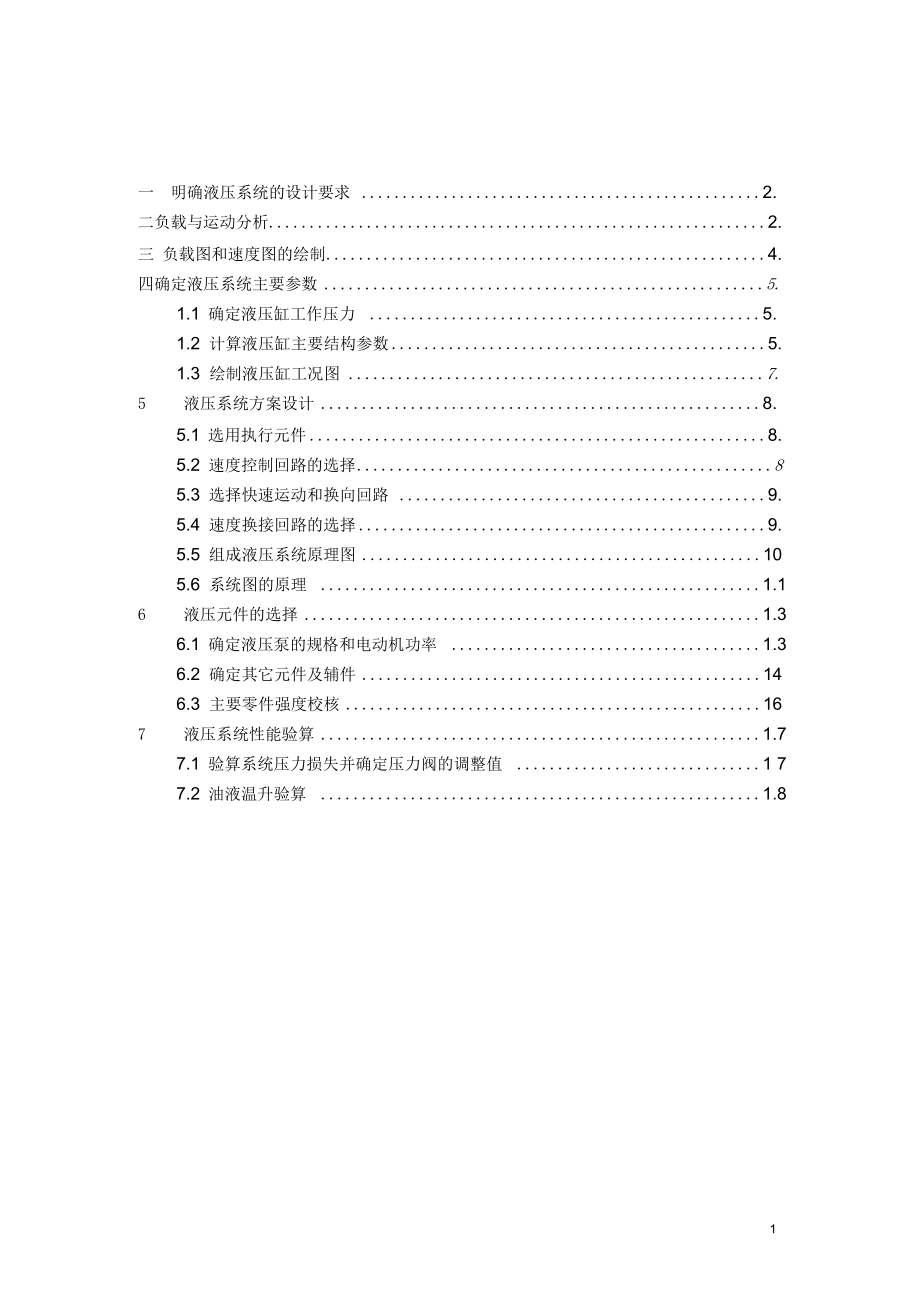


《卧式单面多轴钻孔组合机床动力滑台液压系统课程设计》由会员分享,可在线阅读,更多相关《卧式单面多轴钻孔组合机床动力滑台液压系统课程设计(22页珍藏版)》请在装配图网上搜索。
1、一 明确液压系统的设计要求 2. 二负载与运动分析 2. 三 负载图和速度图的绘制 4. 四确定液压系统主要参数 5. 1.1 确定液压缸工作压力 5. 1.2 计算液压缸主要结构参数 5. 1.3 绘制液压缸工况图 7. 5 液压系统方案设计 8. 5.1 选用执行元件 8. 5.2 速度控制回路的选择 8 5.3 选择快速运动和换向回路 9. 5.4 速度换接回路的选择 9. 5.5 组成液压系统原理图 10 5.6 系统图的原理 1.1 6 液压元件的选择 1.3 6.1 确定液压泵的规格和电动机功率 1.3 6.2 确定其它元件及辅件 14
2、 6.3 主要零件强度校核 16 7 液压系统性能验算 1.7 7.1 验算系统压力损失并确定压力阀的调整值 1 7 7.2 油液温升验算 1.8 22 明确液压系统的设计要求 要求设计一台卧式单面多轴钻孔组合机床动力滑台的液压系统。要求实现 的动作顺序为:启动一加速一快进一减速一工进一快退一停止。液压系统的主要 参数与性能要求如下:轴向切削力总和 Fg=12700N,移动部件总重量 G = 20000N;行程长度400mm (其中工进行程100mm)快进、快退的速度为7m/min, 工进速度(20~1000) mm/min,其中20mm/min为粗加工,1000mm/m
3、in为精加 工;启动换向时间△ t<0.15s;该动力滑台采用水平放置的平导轨;静摩擦系数 fs= 0.2;动摩擦系数fd=0.1。液压系统的执行元件使用液压缸。 负载与运动分析 负载分析中,暂不考虑回油腔的背压力,液压缸的密封装置产生的摩擦阻力 在机械效率中加以考虑。因工作部件是卧式放置,重力的水平分力为零,这样需 要考虑的力有:夹紧力,导轨摩擦力,惯性力。 在对液压系统进行工况分析时,本设计实例只考虑组合机床动力滑台所受到 的工作负载、惯性负载和机械摩擦阻力负载,其他负载可忽略。 (1)工作负载Fw 工作负载是在工作过程中由于机器特定的工作情况而产生的负载, 对于金属 切削机床
4、液压系统来说,沿液压缸轴线方向的切削力即为工作负载,即 Ft =12700 N (2)阻力负载Ff 阻力负载主要是工作台的机械摩擦阻力,分为静摩擦阻力和动摩擦阻力两部 分。导轨的正压力等于动力部件的重力,设导轨的静摩擦力为 Ff,则 静摩擦阻力 Ffs =0.2 20000 -4000N 动摩擦阻力 Ffd =0/20000 -2000N (3)惯性负载 最大惯性负载取决于移动部件的质量和最大加速度,其中最大加速度可通过 工作台最大移动速度和加速时间进行计算。已知启动换向时间为 0.05s ,工作台 最大移动速度, 20000 7 9.81 60 0.15 即快进、快退
5、速度为 4.5m/min ,因此惯性负载可表示为 N =1585.68N 如果忽略切削力引起的颠覆力矩对导轨摩擦力的影响,并设液压缸的机械 效率“W =0.9,根据上述负载力计算结果,可得出液压缸在各个工况下所受到的 负载力和液压缸所需推力情况,如表 1所示 表1液压缸总运动阶段负载表(单位: N) 工况 负载组成 负载值F/N 推力F/ w /N 启动 F =Ffs 4000 4444.44 加速 F =Ffd +Fm 3585.68 3984.08 快进 F =Ffd 2000 2222.22 工进 F =Ffd +Ft 14700 16
6、333.33 反向启动 F =Ffs 4000 4444.44 加速 F =Ffd +Fm 3585.68 3984.08 快退 F =Ffd 2000 2222.22 制动 F =Ffd - Fm 414.32 460.36 三 负载图和速度图的绘制 根据负载计算结果和已知的个阶段的速度, 可绘制出工作循环图如图1 (a) 所示,所设计组合机床动力滑台液压系统的速度循环图可根据已知的设计参数进 行绘制,已知快进和快退速度 M=v3=7m/min、快进行程L1=400-100=300mm、 工进行程L2=100mm、快退行程L3=400mm,工进速度v2
7、 =50mm/min。 快进、工进和快退的时间可由下式分析求出。 快进 ti Li 300 10与 7 =2.57s 工进 t2 L2 V2 60 一一 一 3 100 10 0.05 二 120s 60 快退 t「k工迎咨.臾* s^ V1 V3 |l_7 1000 7 1000 根据上述已知数据绘制组合机床动力滑台液压系统绘制负载图( F-t )如图 1(b),速度循环图如图1 (c)所示。 快进 工进 快进 停止 b a)工作循环图 b 速度负载循环图 )负载速度图 c)负载速度图 四确定液压系统主要参数 4.1 确定
8、液压缸工作压力 由表2和表3可知,组合机床液压系统在最大负载约为17000 N时宜取3MP 表2按负载选择工作压力 ^ KN <5 5~10 10~20 20~30 30~50 >50 工作压力 /MPa < 0.8~1 1.5~2 2.5~3 3~4 4~5 >5 表3各种机械常用的系统工作压力 机械类型 机床 农业机械 小型工程机械 建筑机械 液压凿岩机 液压机 大中型挖掘机 重型机械 起重运输机械 磨床 组合 机床 龙门 刨床 拉床 工作压力/MPa 0.8~2 3~5 2~8 8~10 10~1
9、8 20~32 4.2 计算液压缸主要结构参数 由于工作进给速度与快速运动速度差别较大,且快进、快退速度要求相等, 从降低总流量需求考虑,应确定采用单杆双作用液压缸的差动连接方式。通常利 用差动液压缸活塞杆较粗、可以在活塞杆中设置通油孔的有利条件,最好采用活 塞杆固定,而液压缸缸体随滑台运动的常用典型安装形式。这种情况下,应把液 压缸设计成无杆腔工作面积 人是有杆腔工作面积A2两倍的形式,即活塞杆直径 d与缸筒直径D呈d = 0.707 D的关系。 工进过程中,当孔被钻通时,由于负载突然消失,液压缸有可能会发生前 冲的现象,因此液压缸的回油腔应设置一定的背压(通过设置背压阀的方式)
10、,选 取此背压值为P2=0.8MPa 快进时液压缸虽然作差动连接(即有杆腔与无杆腔均与液压泵的来油连接), 但连接管路中不可避免地存在着压降 Ap,且有杆腔的压力必须大于无杆腔,估 算时取 p 0.5MPa快退时回油腔中也是有背压的,这时选取被压值 p2 =0.6MPa 工进时液压缸的推力计算公式为 F / "m = APl — A2 P2 = Ai Pl - (Ai / 2) P2 , 式中:F ——负载力 nm — —液压缸机械效率 Ai——液压缸无杆腔的有效作用面积 A2——液压缸有杆腔的有效作用面积 Pi——液压缸无杆腔压力 P2 液压有无杆腔压力 因此,根据已知参
11、数,液压缸无杆腔的有效作用面积可计算为 Ai = 16333.33 106 Pi - P2 3- 0.8 2 = 0.006282 m 液压缸缸筒直径为 D = . 4Ai* -89.46mm mm 由于有前述差动液压缸缸筒和活塞杆直径之间的关系, d = 0.707D,因此活 塞杆直径为d=0.707)89.46=63.32mm,根据GB/T2348 —1993对液压缸缸筒内径 尺寸和液压缸活塞杆外径尺寸的规定,圆整后取液压缸缸筒直径为 D=110mm, 活塞杆直径为d=80mm。 此时液压缸两腔的实际有效面积分别为: A1 = D2.4 =63.
12、585 104m2 A23.D2-d2 4 =32.43 10“m2 工作台在快进过程中,液压缸采用差动连接,此时系统所需要的流量为 q快进=(A1 —A2 v1 = 23.07 L/min 工作台在快退过程中所需要的流量为 q快退=A2 乂 v 3 = 22.7 L/ min 工作台在工进过程中所需要的流量为 q 工进=A1XV1=0.318 L/min 根据上述液压缸直径及流量计算结果,进一步计算液压缸在各个工作阶段中 的压力、流量和功率值,如表 4所示。 表4各工况下的主要参数值 工况 F /N 回油腔 压力 PVMPa 进油腔 压力 P1/ MPa
13、输入流里 “-1 q/L.min 输入功 率 F/Kw 计算公式 快 进 启动 5556 0 1.54 P1 =(F +A2Ap“A1-A2 q =(A1 -A2 v1 p = p1q P2 = P1 +Ap 加速 6949 2.31 1.81 快速 2778 1.49 0.99 22.73 0.375 工进 27788 0.8 3.29 0.95 0.052 P1 =(F+p2A2 yA q = A1v2 p = p1q 快 退 起动 2180 0 0.49 P1 =(F+p2A )A2
14、 q = A2v3 P = P1 + q 加速 6949 0.6 2.84 快退 2778 0.6 1.82 20.02 0.607 制动 414.3 0.6 1.3 汪:F = F /nm o 4.3 绘制液压缸工况图 并据表4可绘制出液压缸的工况图,如图2所示。 23. 07 3, 078 1, 81 L 67 0. 448 0, 016 T /rim C. 7037 QPP L86 .37 L41 22.7 图2组合机床液压缸工况图 五 液压系统方案设计 5.1 选用执行元件
15、 因系统运动循环要求正向快进和工进,反向快退,且快进,快退速度相等,因 此选用单活塞杆液压缸,快进时差动连接,无杆腔面积 Ai等于有杆腔面积 A2 的两倍。 5.2 速度控制回路的选择 工况图表明,所设计组合机床液压系统在整个工作循环过程中所需要的功 率较小,系统的效率和发热问题并不突出,因此考虑采用节流调速回路即可。虽 然节流调速回路效率低,但适合于小功率场合,而且结构简单、成本低。该机床 的进给运动要求有较好的低速稳定性和速度-负载特性,因此有三种速度控制方 案可以选择,即进口节流调速、出口节流调速、限压式变量泵加调速阀的容积节 流调速。 钻链加工属于连续切削加工,加工过程中切削力
16、变化不大,因此钻削过程 中负载变化不大,采用节流阀的节流调速回路即可。但由于在钻头钻入铸件表面 及孔被钻通时的瞬间,存在负载突变的可能,因此考虑在工作进给过程中采用具 有压差补偿的进口调速阀的调速方式,且在回油路上设置背压阀。 由于选定了节流调速方案,所以油路采用开式循环回路,以提高散热效率, 防止油液温升过高。 从工况图中可以清楚地看到,在这个液压系统的工作循环内,液压要求油源 交替地提供低压大流量和高压小流量的油液。 而快进快退所需的时间ti和工进所 需的时间t2分别为 ti = li,vi I3.. V3 =〔60 300 7 1000 C60 400 7 1000 S-6s t
17、2 =l2 v2 =!60 100 0.05 1000 S-120S 亦即是殳=20因此从提高系统效率、节省能量角度来看,如果选用单个定量 t1 泵作为整个系统的油源,液压系统会长时间处于大流量溢流状态, 从而造成能量 的大量损失,这样的设计显然是不合理的。 如果采用一个大流量定量泵和一个小流量定量泵双泵串联的供油方式, 由双 联泵组成的油源在工进和快进过程中所输出的流量是不同的, 此时液压系统在整 个工作循环过程中所需要消耗的功率估大, 除采用双联泵作为油源外,也可选用 限压式变量泵作油源。但限压式变量泵结构复杂、成本高,且流量突变时液压冲 击较大,工作平稳性差,最后确定选用双联液压泵
18、供油方案, 有利于降低能耗和 生产成本,如图3所示。 图3双泵供油油源 5.3 选择快速运动和换向回路 根据本设计的运动方式和要求,采用差动连接与双泵供油两种快速运动回路 来实现快速运动。即快进时,由大小泵同时供油,液压缸实现差动连接。 本设计采用二位二通电磁阀的速度换接回路,控制由快进转为工进。与采 用行程阀相比,电磁阀可直接安装在液压站上,由工作台的行程开关控制,管路 较简单,行程大小也容易调整,另外采用液控顺序阀与单向阀来切断差动油路。 因此速度换接回路为行程与压力联合控制形式。 5.4 速度换接回路的选择 所设计多轴钻床液压系统对换向平稳性的要求不高,流量不大,压力不
19、高, 所以选用价格较低的电磁换向阀控制换向回路即可。 为便于实现差动连接,选用 三位五通电磁换向阀。为了调整方便和便于增设液压夹紧支路,应考虑选用 Y 型中位机能。 由前述计算可知,当工作台从快进转为工进时,进入液压缸的流量由 23.07 L/min降0.318 L/min ,可选二位二通行程换向阀来进行速度换接,以减少速度 换接过程中的液压冲击,如图4所示。由于工作压力较低,控制阀均用普通滑阀 式结构即可。由工进转为快退时,在回路上并联了一个单向阀以实现速度换接。 为了控制轴向加工尺寸,提高换向位置精度,采用死挡块加压力继电器的行程终 点转换控制。 a.换向回路 b. 速度换接回
20、路 图4换向和速度切换回路的选择 参考同类组合机床,选用双作用叶片泵双泵供油,调速阀进油节流阀调速的 开式回路,溢流阀做定压阀。为了换速以及液压缸快退时运动的平稳性,回油路 上设置背压阀,初定背压值Pb=0.8MPa。 5.5 组成液压系统原理图 选定调速方案和液压基本回路后,再增添一些必要的元件和配置一些辅助性 油路,如控制油路、润滑油路、测压油路等,并对回路进行归并和整理,就可将 液压回路合成为液压系统,即组成如图 5所示的液压系统图。 为便于观察调整压力,在液压泵的进口处,背压阀和液压腔进口处设置测压 点,并设置多点压力表开关,这样只需一个压力表即能观察各压力。 要实现系统
21、的动作,即要求实现的动作顺序为:启动一加速一快进一减速一 工进一快退一停止。则可得出液压系统中各电磁铁的动作顺序如表 5所示。表中 “+”号表示电磁铁通电或行程阀压下;“一”号表示电磁铁断电或行程阀复位。 表5电磁铁的动作顺序表 1YA 2YA 3YA 行程阀 快进「 + 减速] + ,— ,—= + X 进 + — 十 + 死档铁停留 + + + 快退 — + — + 原位停止 — — — — 图5液压系统图 5.5系统图的原理 1 .快进 快进如图所示,按下启动按钮,电磁铁 1YA通电
22、,由泵输出地压力油经 2 三位五通换向阀的左侧,这时的主油路为: 进油路:泵一向阀10一三位五通换向阀2 (1YA得电)一行程阀3一液压 缸左腔 回油路:液压缸右腔-三位五通换向阀 2 (1YA得电)f单向阀6f行程阀 3f液压缸左腔。 由此形成液压缸两腔连通,实现差动快进,由于快进负载压力小,系统压力 低,变量泵输出最大流量。 2 .减速 当滑台快到预定位置时,此时要减速。挡块压下行程阀 3,切断了该通路, 电磁阀继续通电,这时,压力油只能经过调速阀 4,电磁换向阀16进入液压缸 的左腔。由于减速时系统压力升高,变量泵的输出油量便自动减小,且与调速阀 4开口向适应,此时液控顺序
23、7打开,单向阀6关闭,切断了液压缸的差动连接 油路,液压缸右腔的回油经背压阀8流回油箱,这样经过调速阀就实现了液压油 的速度下降,从而实现减速,其主油路为: 进油路:泵 -向阀10-三位五通换向阀2 (1YA得电)-调速阀4-电磁 换向阀16―液压缸左腔。 回油路:液压缸右腔-三位五通换向阀2f背压阀8-液控顺序阀7f油箱。 3 .工进 减速终了时,挡块还是压下,行程开关使3YA通电,二位二通换向阀将通路 切断,这时油必须经调速阀4和15才能进入液压缸左腔,回油路和减速回油完 全相同,此时变量泵输出地流量自动与工进调速阀 15的开口相适应,故进给量 大小由调速阀15调节,其主油路为:
24、 进油路:泵 ―向阀10-三位五通换向阀2 (1YA得电)-调速阀4f调速 阀15―液压缸左腔。 回油路:液压缸右腔-三位五通换向阀2f背压阀8-液控顺序阀7f油箱。 4 .死挡铁停留 当滑台完成工进进给碰到死铁时,滑台即停留在死挡铁处,此时液压缸左 腔的压力升高,使压力继电器14发出信号给时间继电器,滑台停留时间由时间 继电器调定。 5 .快退 滑台停留时间结束后,时间继电器发出信号,使电磁铁 1YA 3YA断电,2YA 通电,这时三位五通换向阀2接通右位,,因滑台返回时的负载小,系统压力下 降,变量泵输出流量又自动恢复到最大,滑快速退回,其主油路为: 进油路:泵 -向阀10
25、-三位五通换向阀2 (2YA得电)-液压缸右腔。 回油路:液压缸左腔-单向阀5-三位五通换向阀2 (右位)-油箱。 6 .原位停止 当滑台退回到原位时,挡块压下原位行程开关,发出信号,使 2YA断电,换 向阀处于中位,液压两腔油路封闭,滑台停止运动。这时液压泵输出的油液经换 向2直接回油箱,泵在低压下卸荷。 系统图的动作顺序表如表5所示。 六液压元件的选择 6.1 确定液压泵的规格和电动机功率 (1)计算液压泵的最大工作压力 根据液压泵的最大工作压力计算方法,液压泵的最大工作压力可表示为液 压缸最大工作压力与液压泵到液压缸之间压力损失之和。 对于调速阀进口节流调速回路,选取进
26、油路上的总压力损失 △ p = 0.8MPa,同时考虑到压力继电器的可靠动作要求压力继电器动作压力 与最大工作压力的压差为0.5MPa,则小流量泵的最高工作压力可估算为 Pp1 = 2.97 0.8 0.5 MPa =4.27MPa 大流量泵只在快进和快退时向液压缸供油, 图4表明,快退时液压缸中的工 作压力比快进时大,如取进油路上的压力损失为 0.5MPa,则大流量泵的最高工 作压力为: Pp2 = 1.86 0.5 MPa =2.36MPa (2)计算总流量 表3表明,在整个工作循环过程中,液压油源应向液压缸提供的最大流量出 现在快进工作阶段,为23.07 L/min,若整个回路
27、中总的泄漏量按液压缸输入流 量的10%计算,则液压油源所需提供的总流量为: q =1.1 23.07 L min =30.97 L/min p 工作进给时,液压缸所需流量约为 0.318 L/min ,但由于要考虑溢流阀的最 小稳定溢流量3 L/min ,故小流量泵的供油量最少应为 3.318L/min。 据据以上液压油源最大工作压力和总流量的计算数值,因此选取 PV2R126/26型双联叶片泵,其中小泵的排量为 6mL/r,大泵的排量为26mL/r, 若取液压泵的容积效率 1=0.9,则当泵的转速np=940r/min时,液压泵的实际 输出流量为 qp =16+ 26产960 M0.
28、9/1000 】L/min =(5.1+22) =27.072L/min 由于液压缸在快退时输入功率最大, 这时液压泵工作压力为2.36MPa流量 为27.072r/min。取泵的总效率"=0.75,则液压泵驱动电动机所需的功率为: p P—制W5 p 根据上述功率计算数据,此系统选取 Y100L-6型电动机,具额定功率 Pn =1.5kW ,额定转速 nn =960r/min。 6.2 确定其它元件及辅件 (1)确定阀类元件及辅件 根据系统的最高工作压力和通过各阀类元件及辅件的实际流量, 查阅产品样 本,选出的阀类元件和辅件规格如 表6所列。 表6液压元件规格及型号
29、 序号 元件名称 通过的最 大流里 q/L/min 规格 型号 额定流量 qn/L/min 额定压力 Pn/MPa 额定压降 ?Pn/MPa 1 双联叶片泵 一 PV2R12-6/26 (5.1+22) 16/14 一 2 三位五通电 液换向阀 50 35DYF3— E10B 80 16 < 0.5 3 行程阀 60 AXQF- E10B 63 16 < 0.3 4 调速阀 <1 AXQF- E10B 6 16 一 5 单向阀 60 AXQF- E10B 63 16 0.2 6 单向阀 25
30、 AF3-Ea10B 63 16 0.2 7 液控顺序阀 22 XF3— E10B 63 16 0.3 8 背压阀 0.3 YF3— E10B 63 16 一 9 溢流阀 5.1 YF3— E10B 63 16 一 10 单向阀 22 AF3-Ea10B 63 16 < 0.02 11 滤油器 30 XUH 63 X 80-J 63 一 < 0.02 12 压力表开关 一 KF3-E3B 3 测点 一 16 一 13 单向阀 60 AF3-Fa10B 100 6.3 0.2 14 压力继
31、电器 一 PF— B8L 一 0 一 *注:此为电动机额定转速为 940r/min时的流量。 (2)确定油管 在选定了液压泵后,液压缸在实际快进、工进和快退运动阶段的运动速度、 时间以及进入和流出液压缸的流量,与原定数值不同,重新计算的结果如表 7 所列。 表7各工况实际运动速度、时间和流量 流量、速度 快进 工进 快退 输入流里 Aqp q1 _ A1 — A2 /(L/min ) _ 63.59x27.1 63.59-32.43 = 55.3 q1 =0.318 q1 = qp = 27.1 排出流量 Azq A2CI1
32、 A。 q2 — q2 — q2 — A1 A A2 /(L/min ) 32.43X55.3 ccc 0.38K32.43 27.1m 63.59 = =28.2 63.59 63.59 = 0.194 32.43 = 53.13 运动速度 qp _q1 _ q1 v1 —.. V2 - V3 —— A1 -A2 A1 A2 /(L/min ) 27.1 黑10 _0.381父10 27.1x10 ―63.59-32.43 63.59 32.43 = 8.22 = 0.0
33、5 = 8.35 由表可以看出,液压缸在各阶段的实际运动速度符合设计要求 根据表中数值,当油液在压力管中流速取 3m/s时,可算得与液压缸无杆腔 和有杆腔相连的油管内径分别为: d =2 q 二v =2 63.59 106 二 3 103 60mm=19.78mm 取标准值20mm; d =2 q -V =2 27.1 106 二 3 103 60 mm = 13.85mm 取标准值15mm。 因此与液压缸相连的两根油管可以按照标准选用公称通径为 420和巾15的 无缝钢管或高压软管。如果液压缸采用缸筒固定式,则两根连接管采用无缝钢管 连接在液压缸缸筒上即可。如果液压缸采用
34、活塞杆固定式,则与液压缸相连的两 根油管可以采用无缝钢管连接在液压缸活塞杆上或采用高压软管连接在缸筒上。 (3)油箱的设计 油箱的主要用途是贮存油液,同时也起到散热的作用,参考相关文献及设 计资料,油箱的设计可先根据液压泵的额定流量按照经验计算方法计算油箱的体 积,然后再根据散热要求对油箱的容积进行校核。 油箱中能够容纳的油液容积按 JB/T7938 —1999标准估算,取,=7时,求得 其容积为 V = qp =7 27.1 L =189.7L p 按JB/T7938—1999规定,取标准值 V=250L 6.3 主要零件强度校核 ①缸筒壁厚& =4 nlm 因为方案是低压
35、系统,校核公式 、一毕,…0.1D 2 ।-. 1 式中:6-缸筒壁厚(m) Pe-实验压力 Pe =(1.25~1.5)P,其中pi是液压缸的额定工作压力 D- 缸筒内径D=0.11M ,n为 5】-缸筒材料的许用应力。[Q]=Ob/n,j为材料抗拉强度(A 安全系数,取n=5。 对于R<16MPa材料选45号调质钢,对于低压系统 PeD 2[二] 1.5 4 106 0.11 cc 6——=3.3mm 2 100 10 因此才两足要求。 ②缸底厚度5 =11 mm 对于平缸底,厚度 储 有两种情况: a.缸底有孔时: a >0.433D2j—Pe— =0
36、.433〃 103.4mJ 1.5父4 = 23.069mm 1 。[二] 0.226 100 其中d D2 一 d0 D2 103.4 -80 103.4 =0.226 mm b.缸底无孔时,用于液压缸快进和快退; P 1 -0.433D2=0.433 103.4 1.5 4 106 10.97mm , 100 106 其中 D2 = D -2、. =110 -2 3.3 = 103.4mm ③杆径d 由公式: 式中:F是杆承受的负载(N) , F=12700N 61是杆材料的许用应力,= ]=100MPa 4 12700 6 =0.0127
37、2mm 3.14 100 106 d1. 5.2KF ,二 z[二] ④缸盖和缸筒联接螺栓的底径di 5.2 1.5 12700 6 : 0.00725mm 3.14 6 100 106 式中K------ 拧紧系数,一般取K=1.25~1.5; F—— 缸筒承受的最大负载(N); z 螺栓个数; 卜]-- 螺栓材料的许用应力,kL^s/n,仃s为螺栓材料的屈服点(MPa, 安全系数n=1.2~2.5 七液压系统性能验算 7.1验算系统压力损失并确定压力阀的调整值 ①快进 滑台快进时,液压缸差动连接,由表3和表4可知,进油路上油液通过单向 阀10的流量是22L/mi
38、n ,通过电液换向阀2的流量是27.1L/min ,然后与液压缸 有杆腔的回油汇合,以流量55.3L/min通过行程阀3并进入无杆腔。因此进油路 上的总压降为 .,2122 J 巨1+0.3 1MPa L 回, I 80 J I 63 人 =0.024 0.057 0.231 =0.2796MPa 此值不大,不会使压力阀开启,故能确保两个泵的流量全部进入液压缸。 回油路上,液压缸有杆腔中的油液通过电液换向阀 2和单向阀6的流量都是 28.2L/min ,然后与液压泵的供油合并,经行程阀 3流入无杆腔。由此可算出快 进时有杆腔压力 出与无杆腔压力P1之差 - P1」0.5M
39、 ’28.2 ;2 < 80 二「MPa < 63 J =0.0621 0.04 0.231 =0.3331MPa 此值小于原估计值0.5MPa (见表2),所以是偏安全的 ②工进 工进时,油液在进油路上通过电液换向阀 2的流量为0.318L/min ,在调速 阀4处的压力损失为 0.5MPa;油液在回油路上通过换向阀 2的流量是 0.0162L/min ,在背压阀8处的压力损失为 0.5MPa,通过顺序阀 7的流量为 (0162+22) L/min=22.162L/min ,因此这时液压缸回油腔的压力为 .为 「 『0 162 9 /22 162 121 p2= 0
40、.5父 土* i1 +0.5+0.3X । MPa =0.53712MPa I < 80 ) < 63 ) 可见此值小于原估计值0.8MP3故可按表2中公式重新计算工进时液压缸进油 腔压力口,即 MPa 2.84 M P a 16333.33 0.537 106 32.43 10工 63.59 10-4 106 此值与表3中数值2.976MPa相近。 考虑到压力继电器可靠动作需要压差 Ape=0.5MPa,故溢流阀9的调压Ppia 应为 Pp1 > Pi +&Pi +Ape = 1.84 +0.5M 0 - ] +0.5+0.5 M P a3.84M Pa L 180 J
41、J ③快退 快退时,油液在进油路上通过单向阀 10的流量为22L/min,通过换向阀2 的流量为27.1L/min ;油液在回油路上通过单向阀5、换向阀2和单向阀13的流 量都是53.13L/min。因此进油路上总压降为 k & 「22 y 「27 1 弋 । Apv2= 0.2父 —I +0.5父 I MPa=0.082MPa 2 - <63 J 180 J J 此值较小,所以液压泵驱动电动机的功率是足够的。回油路上总压降为 一 CC ’53.13 ’53.132 上cc ’53.132 Lc 八〜八一c 乙 &P2 = 0.2 父 । +0.5父 । +0.2父 ।
42、MPa =0.616MPa L < 63 J 8 80 ) < 63 J J 此值与表3的估计值相近,故不必重算。所以,快退时液压泵的最大工作压力 Pp应为 Pp = P1 " Q = 2.41 0.082 M P a=2.492M P a 因此大流量液压泵卸荷的顺序阀 7的调压应大于2.492MPa 7.2油液温升验算 液压传动系统在工作时,有压力损失、容积损失和机械损失,这些损失所消 耗的能量多数转化为热能,使油温升高,导致油的粘度下降、油液变质、机器零 件变形等,影响正常工作。为此,必须控制温升 AT在允许的范围内,如一般机 床△= 25 ~ 30 C ;数控机床25 C ;
43、粗加工机械、工程机械和机车车辆A= 35〜 40 C。 液压系统的功率损失使系统发热,单位时间的发热量 小(kW可表示为 二 Pl 一 P2 式中 P ——系统的输入功率(即泵的输入功率)(kW; P2 ——系统的输出功率(即液压缸的输出功率) (kW 若在一个工作循环中有几个工作阶段,则可根据各阶段的发热量求出系统的 平均发热量 对于本次设计的组合机床液压系统, 比例达95% 其工进过程在整个工作循环中所占时间 t2 120 二=——= =95.23% t1 t2 120 6 因此系统发热和油液温升可用工进时的发热情况来计算。 工进时液压缸的有效功率(即系统输
44、出功率)为 14700 0.05 P0 -Fv 3 kW-0.01225kW 103 60 这时大流量泵通过顺序阀10卸荷,小流量泵在高压下供油,所以两泵的总 输出功率(即系统输入功率)为: Pp1qp1 - Pp2qp2 0.3 106 2 Jj)嚼“10F84"06福"10, 3 0.75 10 kW = 0.432kW 由此得液压系统的发热量为 Hi = P -P0 =:。432 -0.01225 kW =0.42kW 即可得油液温升近似值: △T =(0.42黑103 /3A25070c =11.45% 温开小于普通机床允许的温升范围,因此液压系统中不需设置冷却器
- 温馨提示:
1: 本站所有资源如无特殊说明,都需要本地电脑安装OFFICE2007和PDF阅读器。图纸软件为CAD,CAXA,PROE,UG,SolidWorks等.压缩文件请下载最新的WinRAR软件解压。
2: 本站的文档不包含任何第三方提供的附件图纸等,如果需要附件,请联系上传者。文件的所有权益归上传用户所有。
3.本站RAR压缩包中若带图纸,网页内容里面会有图纸预览,若没有图纸预览就没有图纸。
4. 未经权益所有人同意不得将文件中的内容挪作商业或盈利用途。
5. 装配图网仅提供信息存储空间,仅对用户上传内容的表现方式做保护处理,对用户上传分享的文档内容本身不做任何修改或编辑,并不能对任何下载内容负责。
6. 下载文件中如有侵权或不适当内容,请与我们联系,我们立即纠正。
7. 本站不保证下载资源的准确性、安全性和完整性, 同时也不承担用户因使用这些下载资源对自己和他人造成任何形式的伤害或损失。
最新文档
- 2025年水电工程运行维护管理合同示范文本.docx
- 2025年工程勘测设计合同模板.docx
- 2025年区域产品销售代理合同.docx
- 2025年经销商授权合同样本.docx
- 2025年员工住房资金借贷合同.docx
- 2025年轻钢建筑施工合同示例.docx
- 2025年网络推广托管合同.docx
- 2025年简明个人借款正式合同范例.docx
- 2025年房产按揭贷款合同范例.docx
- 2025年技术合同争议调解.docx
- 2025年电子版城市住宅租赁合同范本.docx
- 2025年简易转让合同协议书样本.docx
- 2025年投资顾问服务合同实例.docx
- 2025年经销合同模板.docx
- 2025年工业项目设计合同样本.docx