MINITAB图表分析工具
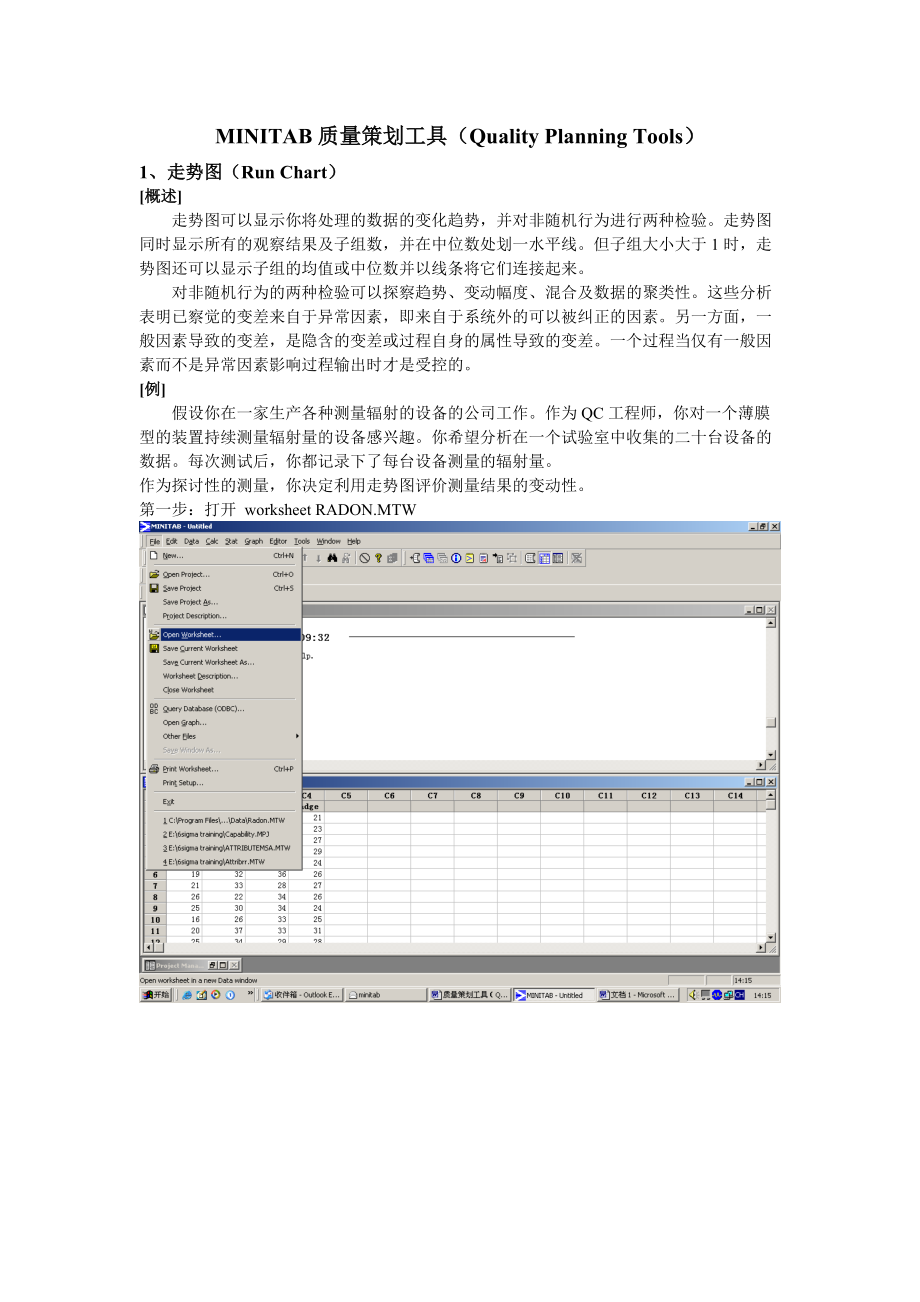


《MINITAB图表分析工具》由会员分享,可在线阅读,更多相关《MINITAB图表分析工具(49页珍藏版)》请在装配图网上搜索。
1、MINITAB质量策划工具(Quality Planning Tools) 1、走势图(Run Chart) [概述] 走势图可以显示你将处理的数据的变化趋势,并对非随机行为进行两种检验。走势图同时显示所有的观察结果及子组数,并在中位数处划一水平线。但子组大小大于1时,走势图还可以显示子组的均值或中位数并以线条将它们连接起来。 对非随机行为的两种检验可以探察趋势、变动幅度、混合及数据的聚类性。这些分析表明已察觉的变差来自于异常因素,即来自于系统外的可以被纠正的因素。另一方面,一般因素导致的变差,是隐含的变差或过程自身的属性导致的变差。一个过程当仅有一般因素而不是异常因素影响过程输出时才
2、是受控的。 [例] 假设你在一家生产各种测量辐射的设备的公司工作。作为QC工程师,你对一个薄膜型的装置持续测量辐射量的设备感兴趣。你希望分析在一个试验室中收集的二十台设备的数据。每次测试后,你都记录下了每台设备测量的辐射量。 作为探讨性的测量,你决定利用走势图评价测量结果的变动性。 第一步:打开 worksheet RADON.MTW 第二步:选择 Stat > Quality Tools > Run Chart. 第三步:在Single column栏输入Membrane,在Subgroup size栏输入 2. ,然后按 OK. 聚类检验在0.05的水平
3、上是显著的。既然聚类检验的概率(p=0.02)比0.05小,你可以得出结论存在异因影响你的过程,你应该调查可能的来源。聚类可能意味着取样或测量有问题。 注:在这里选择0.05的显著性水平进行说明。因为在许多应用中它都适用。你可以选择任何显著性水平对非随机现象进行检验显著性评估。当显示的p值比选择的显著性水平低时,你应拒绝虚拟假设—数据随机排列—支持另一个选择。参见对随机性检验的更完整的研讨。 2、排列图(Pareto Chart) [概述] 排列图是一种条图,其横轴表示研究对象的类别,而不是连续的刻度。横轴的分类通常是缺陷。通过按最大到最小顺序排列的条形,排列图可以帮助你判断缺陷中有哪些
4、是关键的少数以及次要的多数。一个累积百分比的连线可以帮助你判断每个类别的累加效果。排列图可以将改善努力的重点放在可以取得最大成果的因素上。 排列图可以为所有的数据画一张图,或数据内部的分组对应的几个独立的图形。 [例1] 使用Raw Data 你所工作的公司制造金属书架。在最终检查中,一定数量的书架因为划伤、裂片、弯曲或花边等原因被拒收。你希望通过排列图了解是什么缺陷导致了主要问题。首先,你计算每个缺陷发生的次数,接着你在每次发生时将缺陷的名称输入到叫“Damage”的工作表列中。 第一步:打开worksheet EXH_QC.MTW。 第二步:选择Stat > Qual
5、ity Tools > Pareto Chart 第三步:在Chart defects data in栏输入Damage,按OK [结果分析1] 75%的损失是划伤和裂片造成的,因此你应该将改善的重点放在这两个方面。 [例2] 使用 Count Data 假设你在一家制造摩托车的公司工作。你希望减少因为速度计不良导致的质量成本。在检查中,一定数量的速度计被拒收,缺陷的类型也被记录了下来。你在“Defects”中输入缺陷的名称,在“Count”中输入相应的计数。你知道你可以将重点放在导致大多数的拒收的缺陷上而省下许多钱。一个排列图可以帮助你识别哪些缺陷导致了多数的问题。
6、第一步:打开worksheet EXH_QC.MTW 第二步:选择Stat > Quality Tools > Pareto Chart 第三步:选择Chart defects table图表,在Labels in栏输入Defects,在Frequencies in栏输入Counts,然后按OK [结果分析2] 一半以上的速度计是因为无螺钉而拒收,因此你应将重点放在这个问题上。 [例3] 使用 "By" Variable 假想你在生产洋娃娃的公司工作。最近你注意到,在工厂最终检查中,因为划伤、剥落、脏污而被拒收的洋娃娃数量在上升。你想了解是否在类型和缺陷数量以及生产洋娃娃的班
7、次之间存在某个关系。 第一步:打开worksheet EXH_QC.MTW 第二步:选择Stat > Quality Tools > Pareto Chart 第三步:在Chart defects data in栏中输入Flaws,在BY variable in栏中输入Period [结果分析3] 夜班生产的缺陷品较多。大多数的问题是划伤和剥落引起的。如果你检查夜班生产的过程细节的话,你可能会了解到很多与问题相关的信息。 3、因果图(Cause-and-Effect Diagram) [概述] 利用因果图(鱼骨图)来组织头脑风暴法获得的关于问题的潜在原因,它可以帮助你识别
8、潜在原因之间的关系。你可以画一张空图,或在图中添加任何你想添加的信息。 [例] 画一张因果图 利用排列图,你发现你的零件主要是因为表面缺陷而被拒收。今天下午,你将与不同部门的成员利用头脑风暴法寻找这些缺陷的潜在原因。你需要提前打印出一张因果图帮你组织会议中的信息。你可以: 画一张空白图 第一步:选择Choose Stat > Quality Tools > Cause-and-Effect 第二步:选择Do not label the branches栏,然后点OK 画一个完整的图 第一步:打开EXH_QC.MTW 第二步:选择Choose Stat > Quali
9、ty Tools > Cause-and-Effect 第三步:将In Colum选择为Constan,然后在Personnel栏输入:培训 态度 技能,在Machine, Material, Method, Measure, and Enviro栏以此类推,填入你要输入的内容即可。 4、多变量图(Multi-Vari Chart) [概述] Minitab可以显示最多含四个因子的多变量图(Shainin multi-vari charts)。多变量图以图形表示变差分析的结果从而为变差分析提供了又一种可视化的选择。这些图还可用于数据的初步分析以纵览数据。该图同时为每个因子
10、的不同水平显示平均值。 [例] 你负责评价三种不同金属的烧结时间对耐压强度的影响。在每个烧结时间下各取5个金属样本测量耐压强度:100分钟, 150分钟,和200分钟,在进行全面的数据分析前,你希望通过多变量图观察数据是否有可察觉的趋势或交互作用。 第一步:打开工作表SINTER.MTW. 第二步:选择Stat > Quality Tools > Multi-Vari Chart 第三步:在Response输入Strength,在Factor1,输入SinterTime.在Factor2输入MetalType,然后点击OK [结果分析] 多变量图表明在金属类
11、型和烧结时间长短之间存在着交互作用。烧结100Min时,金属1获得最大耐压强度,金属2烧结150Min,金属3烧结200Min。 为量化分析交互作用,你可以进一步地使用变差分析或通用线性模型。 5、对称图(Symmetry Plot) [概述] 对称图可以用来评价样本数据是否来自于对称分布。许多统计过程假设数据来自于正态分布。然而,许多过程不服从正态分布,因此数据来自于一个对称分布通常是必要的。其它统计过程,比如非参数方法,假设数据来自于对称分布而不是正态分布。因此,对称图在许多情况都是一个很有用的工具。 [例] 在做进一步的分析之前,你想判断是否样本数据来自于对称分布。 第一步
12、:打开工作表EXH_QC.MTW 第二步,选择Stat > Quality Tools > Symmetry Plot 第三步:在Variables栏输入Faults,点OK [结果分析] 注意在线的右上部的点,这些点表明分布向左边倾斜。你还可从条形图中看到这一点。 MINITAB测量系统分析(Measurement System Analysis) 1、量具走势图(Gage Run Chart) [概述] 量具走势图是一张观察结果随观察者和零件号而变化的图形。在均值处划了一条水平线,该均值可由数据计算得出或根据过程以往的检验得出。你可以利用该图快速地评价不同的操
13、作者和零件之间的差异。一个稳定的过程会显示一张随机的散布的点;存在操作者或零件影响则会显示一张具有某种规律的图形。 [例]1 变差占了所观察到的总体变差的一大部分(GAGE2.MTW)。 为了比较,以同样的数据分别以ANOVA方法或Xbar-R方法进行Gage R&R研究。 对GAGEAIAG表中的数据, 选择10个零件代表过程变差的预期范围。三个操作者以随机顺序测量10个零件,每个零件测量两次。对GAGE2表中的数据,选择3个零件代表过程变差的预期范围。三个操作者以随机顺序测量三个零件,每个零件测量3次。 第一步:打开工作表GAGEAIAG.MTW 第二步:选择Stat > Qua
14、lity Tools > Gage Study> Gage Run Chart 第三步:在Part numbers输入C1,在Operators输入C2,在Measurement data输入C3,然后点OK [结果分析1] Gage Run Chart Example —GAGEAIAG.MTW 对每个零件,你可以比较每个操作者的测量变差,以及操作者之间的测量差异。 你还可以观察测量结果与水平参考线的关系。默认情况下,参考线是所有观察结果的均值。 大多数的变差是零件之间的差异。一些小的规律可以观察出来。举例来说,操作者2的第二个测量比第一次测量较小(10次当中有7次);操
15、作者2的测量结果比操作者1测量的结果小(10次当中有8次)。 [例]2: 第一步:打开工作表GAGE2.MTW 第二步:选择Stat > Quality Tools > Gage Study> Gage Run Chart 第三步:在Operators输入C2,在Measurement data输入C3,然后点OK [结果分析2] Gage Run Chart Example—GAGE2.MTW 对每个零件,你可以比较每个操作者的测量结果之间的变差,以及不同操作者的测量结果之间的差异。 你还可以观察测量结果与水平参考线之间的关系。默认情况下,参考线是所有观察结果的均
16、值。本例中的主要因素是再现性——当同一个操作者测量同一零件时测量结果之间的巨大差异。这种变动表明操作者需要调整他们测量的方式。 2、量具线性和准确性研究(Gage Linearity and Accuracy Study) [概述] 量具线性研究通过预期的测量结果的范围告诉你测量结果的准确程度。它回答了你的量具是否对各种尺寸的测量对象具有相同的准确度。 量具准确度研究检查观察到的测量结果的平均值和参考值之间的差异。它回答了与参考值相比量具的准确性问题。量具准确性还可以作为偏差的参考。通过使用ANOVA方法进行的量具R &R研究以获得过程偏差-所有数据的5.15SIGMA-本例中为14.1
17、941 [例] 一个工厂领班选择5个零件代表测量结果的预期偏差。每个零件都进行检查以判断其参考值。于是,1个操作者随机测量每个零件12次。通过使用ANOVA方法进行的量具R &R研究以获得过程偏差。 第一步:打开工作表GAGELIN.MTW 第二步:选择Stat > Quality Tools > Gage study> Gage Linearity and Bias Study %Linearity是13.2,意味着该量具的变差占总的过程偏差的13%; %Bias是0.4,意味着该量具的变差占总的过程偏差的1%以下。 3、量具R&R研究(交互)(Gage R&R Stud
18、y (Crossed)) [概述] 量具重复性和再现性研究分析你观察到的过程变差多大程度上是量测系统变差所致。Minitab提供两种方法进行交互Gage R&R研究:Xbar and R,或 ANOVA。Xbar-R方法将总体变差分成三个部分:part-to-part, 重复性和再现性;ANOVA方法更进一步将再现性分成操作者、操作者*零件。 ANOVA方法比Xbar-R方法更准确,因为它考虑了操作者和零件的交互作用。 [例1] Example of Gage R&R Study (ANOVA method) 在本例中,我们对数据进行量具R&R研究:量测系统变差占总体观察到的变差较
19、大 (GAGE2.MTW)。为分析,我们使用ANOVA和Xbar-R方法分析数据。你还可以在量具走势图上观察同样的数据。 在GAGE2中,选择三个零件代表过程变差的预期变差。三个操作者以随机顺序测量3个零件,每个零件测量3次。 使用ANOVA方法分析GAGE2数据 第一步:打开工作表GAGE2.MTW 第二步:选择Stat > Quality Tools > Gage study> Gage R&R Study (Crossed) 第三步:在Part numbers栏输入Part,在 In Operators栏输入Operator,在Measurement data栏输入Resp
20、onse,在Method of Analysis下面选择ANOVA,然后点击OK 观察ANOVA表中Operator*Part交互作用的p值。当 Operator by Part的p值 > 0.25时,Minitab 适合于无交互作用的模型,并使用减少的模型定义Gage R&R统计量。 观察Gage R&R中%Contribution列。总的Gage R&R占的比例(84.36)远大于零件之间的差异(15.64)。所以,多数的变差是测量系统引起的,零件之间的变差对总变差的影响则较小。 ① 在Components of Variation图中(位于左上角),量具R&R对总变差
21、的贡献比零件之间的差异大得多,表明变差主要是测量系统引起的(主要是重复性),较小部分是由于零件之间差异所致㈩②在By Part图中(位于右上角),零件之间的差异较小,几乎在一条直线上㈩③在Xbar Chart by Operator (位于左下部),大多数的点在控制线以内,表明观察到的变差主要是测量系统所致。 ④在By Operator图(位于右列中部),操作者之间没有差异,几乎在一条直线上。⑤Operator*Interaction图是 Oper*Part 交互作用p值(0.48352)的再现,表明每个操作者/零件结合之间的差异相对于总的变差而言是不显著的。 [例2] Example of
22、 a Gage R&R Study (Crossed) ?(Xbar and R方法) 在本例中,我们对两组数据进行量具R&R研究:一组量测系统变差占总体观察到的变差的比例较低 (GAGEAIAG.MTW),另一组量测系统变差占总体观察到的变差较大 (GAGE2.MTW)。为分析,我们使用ANOVA和Xbar-R方法分析数据。你还可以在量具走势图上观察同样的数据。 在GAGEAIAG中,选择了10个数据来代表预期的过程变差的范围。三个操作者以随机顺序测量10个零件,每个零件测量2次。在GAGE2中,选择三个零件代表过程变差的预期变差。三个操作者以随机顺序测量3个零件,每个零件测量3次。 使
23、用Xbar and R 方法分析数据 GAGEAIAG 第一步:打开工作表GAGEAIAG.MTW 第二步:Stat > Quality Tools > Gage study> Gage R&R Study (Crossed) 第三步:第三步:在Part numbers栏输入Part,在 In Operators栏输入Operator,在Measurement data栏输入Measurement,在Method of Analysis下面选择Xbar and R,然后点击OK 观察Gage R&R表的%Contribution列。 测量系统的变差(Total Gage R&R)
24、比对相同数据ANOVA分析的结果小得多。这是因为Xbar-R方法未考虑操作者与零件的相互作用而它们还比较大。因而你会对测量系统导致的变差所占的百分比得出错误的估计。 按照AIAG, 当区分号为4时,测量系统是足够的。然而,如上所述,对这些数据利用ANOVA方法更合适。 图形分析:①在变差构成图中,小部分是测量系统造成的,较高比例的变差是零件之间差异所致。②在Xbar Chart by Operator图中,虽然Xbar-R方法未考虑操作者与零件之间的交互作用,该图显示这种交互是显著的。这里,Xbar-R方法高估了量具的能力。你应该利用考虑到操作者和零件的交互作用的ANOVA方法。③当变
25、差主要是零件之间的差异造成时,Xbar图中大多数的点在控制线之外。 使用Xbar and R 方法分析数据 GAGE2 第一步:打开工作表GAGE2.MTW 第二步:Stat > Quality Tools > Gage study> Gage R&R Study (Crossed) 第三步:第三步:在Part numbers栏输入Part,在 In Operators栏输入Operator,在Measurement data栏输入Response,在Method of Analysis下面选择Xbar and R,然后点击OK 观察量具R&R中的 %Contribution列,
26、测量系统导致的变差(Gage R&R)占了较大的比例(78.111%); 较小比例是零件之间的差异所致(21.889%)。 数字 1表示测量系统能力不够,它不能区分零件之间的差异。 图形分析: ① 在变差构成图中,测量系统的导致的变差(Gage R&R)占了较高的比例(主要是重复性)。零件之间的差异导致的变差占的比例较低。②当观察到的变差主要是测量系统所致时,Xbar图中的多数点在控制线内。 4、量具R&R研究(嵌套)(Gage R&R Study (Nested)) [概述] 量具重复性和再现性研究分析你观察到的过程变差多大程度上是量测系统变差所致。Gage R&R Study
27、 (Nested)用于每个零件仅被一个操作者测量时,如破坏性试验。在破坏性试验中,所测量的特性在测量过程以后与其初始值是不同的。跌落试验便是破坏性试验的一个例子。 Gage R&R Study (Nested)利用ANOVA方法评价重复性和再现性。 ANOVA 方法更进一步地将再现性分成操作者和操作者与零件的交互作用。 如果你进行破坏性试验,你必须假设某个批次所有的零件都具有足够的相似性以至于可以认为它们是相同的零件。如果你不能做如此假设,那么某个批次零件之间的差异将掩盖测量系统的变差。如果你可以做以上假设,是选择交互式还是嵌套式量具R&R 研究依赖于你的测量过程是如何建立的。如果
28、所有的操作者测量来自于不同批次的零件,那么应使用交互式。如果每个批次仅仅被某个操作者测量,应使用嵌套式。事实上,只要操作者测量特定的零件,就是嵌套式设计。 [例] 在这个例子中,三个操作者每人测量五个不同的零件各两次,一共有30个测量结果。每个零件对操作者来说都是独特的,没有任何两个操作者测量相同的零件。因此,你决定进行嵌套式量具R&R研究来决定你所观察到的过程变差在多大程度上是测量系统变差所致。 第一步:打开工作表GAGENEST.MTW 第二步:选择Stat > Quality Tools > Gage study> Gage R&R Study(Nested) 第三步:在In
29、 Part or batch numbers栏输入Part,在 In Operators栏输入Operator,在Measurement data栏输入Response,在Method of Analysis下面选择Xbar and R,然后点击OK [结果分析] 观察%Contribution列中的Total Gage R&R和Part-to-Part.。零件之间的差异占的百分比(Part-To-Part = 17.54)比测量系统变差占的百分比小得多(Total Gage R&R = 82.46)。这表明变差主要是由于测量系统引起的,极少部分是零件之间的差异引起。
30、在区分域中的数字表明测量系统不能区分零件之间的差异。 观察位于左上角的变差构成图。变差主要是由于测量系统所致,而零件之间的差异造成的变差占的比重很低。观察位于左下方的Xbar图。当变差主要是由于测量系统误差造成时,图中多数点在控制线以内。 过程能力概述(Process Capability Overview) 在过程处于统计控制状态之后,即生产比较稳定时,你很可能希望知道过程能力,也即满足规格界限和生产良品的能力。你可以将过程变差的宽度与规格界限的差距进行对比来片段过程能力。在评价其能力之前,过程应该处于控制状态,否则,你得出的过程能力的估计是不正确的。 你可以画能力条形图和能力
31、点图来评价过程能力,这些图形可以帮助你评价数据的分布并验证过程是否受控。你还可以计算过程指数,即规范公差与自然过程变差的比值。过程指数是评价过程能力的一个简单方法。因为它们无单位,你可以用能力统计量来比较不同的过程。 一、选择能力命令(Choosing a capability command) Minitab提供了许多不同的能力分析命令,你可以根据数据的属性及其分布来选择适当的命令。你可以为以下几个方面进行能力分析: n 正态或Weibull概率模型(适合于测量数据) n 很可能来源于具有明显组间变差的总体的正态数据 n 二项分布或泊松概率分布模型 (适合于属性数据或计数数据)
32、注:如果你的数据倾斜严重,你可以利用Box-Cox转换或使用Weibull 概率模型。 在进行能力分析时,选择正确的分布是必要的。例如:Minitab提供基于正态和Weibull概率模型的能力分析。使用正态概率模型的命令提供更完整的一系列的统计量,但是你的数据必须近似服从正态分布以保证统计量适合于这些数据。举例来说,Analysis (Normal) 利用正态概率模型来估计期望的PPM。这些统计量的结实依赖于两个假设:数据来自于稳定的过程,且近似服从的正态分布。类似地,Capability Analysis (Weibull) 利用Weibull 分布模型计算PPM。在两种情况下,统计的有效
33、性依赖于假设的分布的有效性。 如果数据倾斜严重,基于正态分布的概率会提供对实际的超出规格的概率做比较差的统计。这种情况下,转化数据使其更近似于正态分布,或为数据选择不同的概率模型。在Minitab中,你可以用“Box-Cox power transformation”或Weibull概率模型。Non-normal data 对这两个模型进行了比较。 如果你怀疑过程具有较明显的组间变差,使用Capability Analysis (Between/Within)或 Capability Sixpack (Between/Within)。子组内部的随机误差之上,子组数据可能还有子组之间的随机变
34、差。对子组变差的两个来源的理解可以为过程潜在能力提供更实际的估计。Capability Analysis (Between/Within)和Capability Sixpack (Between/Within) 计算了组间和组内标准差,然后再估计长期的标准差。 Minitab还为属性数据和计数数据进行能力分析,基于二项分布和泊松概率模型。例如:产品可以根据标准判定为合格和不合格(使用 Capability Analysis (Binomial)).。你还可以根据缺陷的数量进行分类(使用Capability Analysis (Poisson)). 二、能力分析命令概况 Capabilit
35、y Analysis (Normal)为单个测量结果画一张能力条形图,图上包含基于过程均值和标准差的正态曲线。这可以帮助你对正态性假设进行视觉上的评价。报告还包括一张过程能力统计量的表,包括组内和组间统计量。 Capability Analysis (Between/Within) 为单个测量结果画一张能力条形图,图上包含基于过程均值和标准差的正态曲线。这可以帮助你对正态性假设进行视觉上的评价。报告还包括一张组间/组内和长期过程能力统计量的列表。 Capability Sixpack (Normal) 同时显示以下图形,以及能力统计量的子集: 一张Xbar (or Individual
36、s), R or S (or Moving Range), 和 run chart, 可用来验证过程是否处于控制状态; 一个能力条形图和正态概率图,可以帮助验证数据是否服从正态分布; 一个能力图,显示过程变差与规范界限的相对性。 Capability Sixpack (Between/Within)适合于组间变差比较明显的子组数据。Capability Sixpack (Between/Within) 同时显示以下图形,以及能力统计量的子集: 一张Individuals Chart, Moving Range Chart, and R Chart or S Chart,可用来验证
37、过程是否处于控制状态; 一个能力条形图和正态概率图,可以帮助验证数据是否服从正态分布; 一个能力图,显示过程变差与规范界限的相对性。 Capability Sixpack (Weibull) 同时显示以下图形,以及能力统计量的子集: 一张Individuals, R- (or Moving Range), and run chart, 可用来验证过程是否处于控制状态; 一个能力条形图和Weibull概率图,可以帮助验证数据是否服从Weibull分布; 一个能力图,显示过程变差与规范界限的相对性。 Capability Analysis (Weibull) 为单个测量结果
38、画一张能力条形图,图上包含基于过程形状和大小的Weibull曲线。这可以帮助你对Weibull分布的假设进行直观的评价。报告还包括一张长期过程能力统计量的表。 Capability Analysis (Binomial) 适合于数据由不合格品的数量相对于抽取的全部样本数组成时。报告画了一张P图,可以帮助你验证过程是否处于控制状态,以及一张不合格品率的累积图,不合格品率的条形图,以及不合格品率图。 Capability Analysis (Poisson)适用于数据为单位缺陷数。报告画了一张 U图,可以帮助你可以帮助你验证过程是否处于控制状态,还包括一张累积DPU (defects per
39、 unit)图,DPU条形图和缺陷率图。 MINITAB过程能力分析(Process Capability Analysis) 1、Capability Analysis (Normal) [概述] Capability Analysis (Normal)用于对来自于正态分布的数据或Box-Cox转换后的数据进行能力分析。分析报告包括一张带两条正态曲线的能力条形图,一张长期和组内能力统计量的列表。两条正态曲线分别与过程均值和组内标准差、过程均值和长期标准差相对应。 报告还包括过程数据的统计量,如过程均值,目标,组内和长期标准差,过程规范,观察到的能力,以及期望的组内和长期能力。因此,该
40、报告可用于直观评价过程是否服从正态分布,是否以目标值为中心,是否具备持续满足过程规范要求的能力。 [例] 假设你在一个汽车制造厂的机器组装部门工作。某个零件,凸轮轴的长度的工程规范为600+-2mm。长期以来,该轴的长度均超出规范的要求,导致生产线上装配性性、高废弃和重工率。 在对记录清单检查后,你发现该零件有两个供应商。Xbar-R图告诉你供应商2的零件失控,因此你决定停止接受供应商2的零件直至产品受控为止。 在去除供应商2后,不良装配的数量明显减少,但问题并未完全消除。你决定通过能力研究来观察供应商1是否具备满足工程规范的能力。 第一步:打开工作表CAMSHAFT.MTW.
41、第二步:选择Stat > Quality Tools > Capability Analysis>Normal 第三步:在Single column栏输入Supp1,在Subgroup size栏输入5,在Lower spec栏输入598,在Upper spec栏输入602。 第四步:点击Options键,在Target (adds Cpm to table)栏输入600,然后按OK [结果分析] 如果你想解释过程能力统计量,数据应该近似服从正态分布。这个要求得到了满足,这点可以从带正态曲线的条形图上看出来。 但是你可以发现过程均值(599.548)比目标值低,切分布
42、的左边落在了下规范界限之外。这个均值意味着你有些时候可以看到不符合最低规范(598mm)的零件。 Cpk指数表明过程是否可以生产在公差界限内的产品。供应商1的CPK为0.90,表明他们需要通过减少变差和向目标值靠拢来改善其过程。 同样,Likewise, PPM < LSL—每百万零件中质量特性值低于下规范界限的零件数—是3621.06.。这意味着大约3621个零件不满足下规范界限(598mm)。 既然供应商1是你最好的供应商,你应该与它们一起共同改善其过程,从而改善自己的过程。 2、Capability Analysis (Weibull Distribution) [概述] C
43、apability Analysis (Weibull)命令用于对来自于Weibull分布的数据进行过程能力分析。分析报告包括:一个带Weibull曲线的能力条形图,一张长期能力统计表。Weibull曲线是根据过程形状和规模(大小)构造的。 报告还包括过程数据的统计量,如均值,形状,目标,过程规范,实际的长期能力,以及观察到的和期望的长期能力。因此报告可直观地评价过程相对于目标的分布,数据是否服从Weibull分布,过程是否具备持续满足过程规范的能力。 在Weibull模型中,Minitab计算长期过程统计量,Pp, Ppk, PPU, and PPL。计算是基于形状的最大可能估计和规模参
44、数,而不是象正态分布中的均值和变差。如果数据不服从正态分布,你可以选择Box-Cox转换来应用Capability Analysis (Normal Distribution)命令来计算组内统计量,Cp和Cpk。 [例] 假设你在生产地板瓷砖的公司工作,你对瓷砖表面的翘曲比较关心。为保证产品质量,你每个工作日测量10个瓷砖的翘曲量,连续测量了10天。 你决定基于Weibull概率模型进行能力分析。 第一步:打开工作表TILES.MTW 第二步:选择Stat > Quality Tools > Capability Analysis>Nonnormal 第三步:在Single
45、column栏输入Warping,在Upper spec栏输入8,然后点OK. [结果分析] 能力条形图没有显示在假想的模型和数据之间存在严重的差异。但你可以看出分布的右边超出了上规范界限,这意味着你有时会发现翘曲超过上规范界限(8mm)。 Ppk和PPU 指数表明过程是否能生产在允差范围内的瓷砖。两个指数均为0.77,均在1.33之下,因此,过程能力是不够的。 同样,PPM > USL—每百万产品中质量特性值高于上规范界限的产品数—为20000.00。这意味着1,000,000个瓷砖中有20000个的翘曲量将超出上规范界限(8mm)。 3、Capability Sixpac
46、k (Normal) [概述] Capability Sixpack (Normal) 命令用来数据服从正态分布或转换数据时评价过程能力。 Capability Sixpack同时显示以下信息: 一张Xbar图 (或Individuals chart for individual observations) 一张R图或S图 (or MR chart for individual observations) 一张最近25个子组的趋势图 (或最近25个观察结果) 一个过程数据的条形图 一个正态概率图 一个过程能力图 短期和长期能力统计量:Cp, Cpk, 和swit
47、hin; Pp, Ppk, and soverall Xbar, R, 和趋势图可用于验证过程是否处于受控状态。条形图和正态概率图可用于验证数据服从正态分布。最后,能力图以图形显示相对于规范的过程能力。与能力统计量一起,这些信息可以帮助你评价过程是否受控以及产品是否符合规范。 假设数据来自于正态分布的模型适合于多数过程数据。 [例] 假设你在一个汽车制造厂的机器组装部门工作。某个零件,凸轮轴的长度的工程规范为600+-2mm。长期以来,该轴的长度均超出规范的要求,导致生产线上装配性差、高废弃和重工率。 在对记录清单检查后,你发现该零件有两个供应商。Xbar-R图告诉你供应商2的零件失
48、控,因此你决定停止接受供应商2的零件直至产品受控为止。 在去除供应商2后,不良装配的数量明显减少,但问题并未完全消除。你决定通过capability sixpack来观察供应商1是否具备满足工程规范的能力。 第一步:打开工作表CAMSHAFT.MTW 第二步:选择Stat > Quality Tools > Capability Sixpack > Normal 第三步:在Single column栏输入Supp1,在Subgroup size栏输入5,在Upper spec栏输入602,在Lower spec输入598,然后按OK。 [结果分析] 在Xbar-R 图
49、上,点在控制界限之间随机分布,表明过程是稳定的。将R图上的点与Xbar上的点进行比较可发现点之间是否有相关关系。图上的点没有,表明过程稳定。 趋势图上的点随机分布,无趋势或偏移,也表明过程的稳定性。 如果你想解释过程能力统计量,数据应该近似服从正态分布。这个要求得到了满足,这点可以从正态曲线看出来。在正态概率图上,点大致在一条直线上。这些表明数据服从正态分布。 但是从能力图上,可以看出过程的允差落在了下控制界限外,表明你有时会看到不满足最低规范界限的零件。同样,Cp (1.16) and Cpk (0.90)均低于1.33,表明供应商1的过程需要改善。 4、Capability Six
50、pack (Weibull) [概述] Capability Sixpack (Normal) 命令用来数据近似服从Weibull分布时评价过程能力。 Capability Sixpack (Weibull)同时显示以下信息: 一张Xbar图 (或Individuals chart for individual observations) 一张R图(or MR chart for individual observations) 一张最近25个子组的趋势图 (或最近25个观察结果) 一个过程数据的条形图 一个正态概率图 一个过程能力图 长期过程能力统计量:Pp,
51、 Ppk, shape (b), and scale (d) Xbar, R, 和趋势图可用于验证过程是否处于受控状态。条形图和Weibull概率图可用于验证数据近似服从Weibull分布。最后,能力图以图形显示相对于规范的过程能力。与能力统计量一起,这些信息可以帮助你评价过程是否受控以及产品是否符合规范。 假设数据来自于正态分布的模型适合于多数过程数据。 在Weibull模型中,Minitab仅计算长期过程统计量,Pp, Ppk。计算是基于形状的最大可能估计和规模参数,而不是象正态分布中的均值和变差。如果数据不服从正态分布,你可以选择Box-Cox转换来应用Capability Ana
52、lysis (Normal Distribution)命令来计算组内统计量,Cp和Cpk。 [例] 假设你在生产地板瓷砖的公司工作,你对瓷砖表面的翘曲比较关心。为保证产品质量,你每个工作日测量10个瓷砖的翘曲量,连续测量了10天。 你决定基于Weibull 概率模型进行capability sixpack分析。 第一步:打开工作表TILES.MTW 第二步:选择Stat > Quality Tools > Capability Sixpack > Nonnormal 第三步:在Single column栏输入Warping,在Subgroup size栏输入10,在Upper s
53、pec栏输入8,然后按OK [结果分析] 能力条形图没有显示在假想的模型和数据之间存在严重的差异。同样,在Weibull概率图上,所有点近似在一条直线上。 Ppk和PPU 指数表明过程是否能生产在允差范围内的瓷砖。然而,能力图表明过程不能满足规范要求。Ppk为0.77,低于1.33之下,因此,过程能力是不够的。 同样,PPM > USL—每百万产品中质量特性值高于上规范界限的产品数—为20000.00。这意味着1,000,000个瓷砖中有20000个的翘曲量将超出上规范界限(8mm)。 5、Capability Analysis (Binomial) [概述] Capa
54、bility Analysis (Binomial)命令用于对来自于二项分布的数据进行过程能力分析。二项分布通常与所抽取的样本的缺陷项目的数目的记录相关。 例如,你可能使用通过/失败GAGE来判断某个特性合格与否。你应记录检查的所有的样本数和失败的数量。或者,你可以记录某天电话报告生病的人数和每天计划工作的人数。 应用Capability Analysis (Binomial) 命令时必须满足下列条件: 每个项目都是相同条件下的结果; 每个项目将导致两种可能的结果(成功/失败); 对某个项目成功的概率是常数; 项目结果之间是相互独立的。 Capability Analys
55、is (Binomial)所产生的过程能力报告包括以下内容: P图,用于验证过程是否受控; 不合格品率的累积图,用于验证你收集的样本数据是否足够以对稳定的不合格率作出估计; 不合格品率的条形图,显示搜集的样本的长期不合格品率的分布; 不合格品率图,用于验证不合格品率是否受抽取的样本数影响。 [例] 假设你负责评价电话销售部门的反应情况,也就是回答来电的能力。你记录下了20天中每天因为无效销售代表没有回的来电数(不合格)。你还记录了整个的来电数。 第一步:打开工作表BPCAPA.MTW. 第二步:选择Stat > Quality Tools > Capability Ana
56、lysis >Binomial 第三步:在Defectives栏输入Unavailable,在Use sizes in栏输入Calls,然后按OK. [结果分析] P图上有一个点失控。累积不合格品率图显示长期不合格品率趋于22%,但需要收集跟多的数据以证明这一点。不合格品率看起来不受样本大小的影响。过程Z值在0.75左右,比较低,过程需要进一步进行改善。 6、Capability Analysis (Poisson) [概述] Capability Analysis (Poisson)用于当数据来自于泊松分布时产生过程能力报告。泊松数据通常与在某个单位上的缺陷数相关,这个
57、单位可以是指定的时间周期或指定的空间。单位的大小可以改变,因此,你必须同时跟踪大小的变化。 例如:如果你生产电线,你可能想记录某段电线断开的数量,如果线的长度是变化的,你必须记录每段抽取的样本的大小。或者,你们生产电器,你希望记录电器表面的划伤数量。因为表面大小可能不同,你可能记录每个抽取的表面的大小,及平方英寸。 当数据满足下列条件时,应用Capability Analysis (Poisson): 单位表面或时间内的缺陷率对每个项目是相同的; 项目中缺陷数量彼此之间是相互独立的。 Capability Analysis (Poisson) 为服从泊松分布的数据产生过程能力
58、分析报告,包括: U图,验证报告时过程是否受控; 累积平均DPU (defects per unit),验证是否收集到足够数据来对均值做出稳定的估计; DPU 条形图,显示收集到的样本的单位缺陷数的整体分布; 缺陷图比率,验证DPU是否受抽取到的样本大小的影响。 [例] 假设你在电线厂工作,你对电线绝缘过程的有效性非常关心。你随机抽取一定长度的电线,以测试电压,测试绝缘上的弱点。你记录了弱点数和每段电线的长度(in feet)。 第一步:打开工作表BPCAPA.MTW 第二步:选择Stat > Quality Tools > Capability Analysis >P
59、oisson 第三步:在Defects栏输入Weak Spots,在Uses sizes in栏输入Lengths,然后点OK. [结果分析] U图上有3个点失控。累积DPU均值在0.0265上来回变动,表明样本数是足够的以对DPU均值作出较好的估计。DPU看起来不受电线长度的影响。 7、Capability Analysis (Between/Within) [概述] Capability Analysis (Between/Within)利用组间和组内变差产生一个过程能力报告。但数据为子组时,组内的随机误差可能不是唯一应考虑的变差来源。在子组之间也可能存在着随机误
60、差。在这种情况下,全部过程变差包括组内变差和组间变差。 Capability Analysis (Between/Within) 计算组内标准差和组间标准差,也可以指定历史标准差。这些将被结合起来计算全部标准差。全部标准差可用于计算工程能力,如Cp和Cpk。 报告还包括过程数据的统计量,如过程均值,目标,整体(组内和组间)标准差以及长期标准差,观察到的和期望的过程能力。 [例] 假设你对将卷纸涂上一层薄的胶片的过程能力感兴趣。你关心的是纸是否被涂上了正确厚度的胶片以及是否整卷纸都涂上了胶片。你从25个连续卷中抽取了3卷测量涂的厚度。厚度的工程规范为50+-3mm 。 第一步:打开工作
61、表BWCAPA.MTW 第二步:选择Stat > Quality Tools > Capability Analysis> Between/Within 第三步:在Single column栏输入Coating,在Subgroup size栏输入Roll,在Lower spec栏输入47,在Upper spec栏输入53,然后点OK [结果分析] 你可以看出过程均值(49.8829)与50很接近。Cpk指数表明过程是否生产在允差内的产品。Cpk指数为1.21,表明过程能力还可以,但还可以进一步改善。 期望的组内/组间能力的PPM为193.94。这意味着100万个卷中约
62、有194个不能满足规范界限。这种分析告诉你过程具备相当的过程能力。 8、Capability Sixpack (Between/Within) [概述] Capability Sixpack (Between/Within)命令适于存在组内和组间变差的时候,它允许你同时显示以下信息以评价过程能力: 一张单值图;an Individuals chart 一张移动极差图;a Moving Range chart 一张R图或S图;an R chart or S chart 一张过程数据的条形图;?a histogram of the process data 一张正态概率图
63、;?a normal probability plot 一张过程能力图;?a process capability plot 组间/组内和长期能力统计量:Cp, Cpk, Cpm (如果你指定了目标), swithin, sbetween, and s total; Pp, Ppk, and soverall。 单值图、移动极差图、R图或S图可以验证过程是否受控。条形图和正态概率图可以验证数据是否服从正态分布。最后,能力图可以直观地将过程变差与工程规范进行比较。在加上能力统计量,这些信息可以帮助你评价过程是否受控,以及产品是否满足规范要求。 [例] 假设你对将卷纸涂上一层薄的
64、胶片的过程能力感兴趣。你关心的是纸是否被涂上了正确厚度的胶片以及是否整卷纸都涂上了胶片。你从25个连续卷中抽取了3卷测量涂的厚度。厚度的工程规范为50+-3mm 。 因为你想判断是否整个卷都被喷涂,你可以用Minitab来进行Capability Sixpack (Between/Within)分析。 第一步:打开工作表BWCAPA.MTW. 第二步:选择Stat > Quality Tools > Capability Sixpack > Between/Within 第三步:在Single column栏输入Coating,在Subgroup size栏输入Roll,在Lowe
65、r spec栏输入47,在Upper spec栏输入53。 第四步:点击Tests,选择Perform all eight tests然后点OK至结束 [结果分析] 如果你想结实过程能力统计量,数据必须来自于正态分布。这一点是符合的。在能力条形图上,数据大致服从正态分布。同样,在正态概率线上,所有点大致在一条直线上。 没有点被察觉出来存在异常因素,从而表明过程受控。单值图和移动极差图上的点看起来彼此之间无明显关系,也表明过程是稳定的。 能力图显示过程符合规范要求。Cpk (1.21) and Ppk (1.14) 均比1.33低一些,因此你的过程还可以进行改善。 附录1:MINITAB指南 E:\8.27-28\Tutorials.CHM 附录2:MINITAB帮助文件 E:\8.27-28\Minitab help.pdf 附录3:
- 温馨提示:
1: 本站所有资源如无特殊说明,都需要本地电脑安装OFFICE2007和PDF阅读器。图纸软件为CAD,CAXA,PROE,UG,SolidWorks等.压缩文件请下载最新的WinRAR软件解压。
2: 本站的文档不包含任何第三方提供的附件图纸等,如果需要附件,请联系上传者。文件的所有权益归上传用户所有。
3.本站RAR压缩包中若带图纸,网页内容里面会有图纸预览,若没有图纸预览就没有图纸。
4. 未经权益所有人同意不得将文件中的内容挪作商业或盈利用途。
5. 装配图网仅提供信息存储空间,仅对用户上传内容的表现方式做保护处理,对用户上传分享的文档内容本身不做任何修改或编辑,并不能对任何下载内容负责。
6. 下载文件中如有侵权或不适当内容,请与我们联系,我们立即纠正。
7. 本站不保证下载资源的准确性、安全性和完整性, 同时也不承担用户因使用这些下载资源对自己和他人造成任何形式的伤害或损失。