张力减径机孔型设计
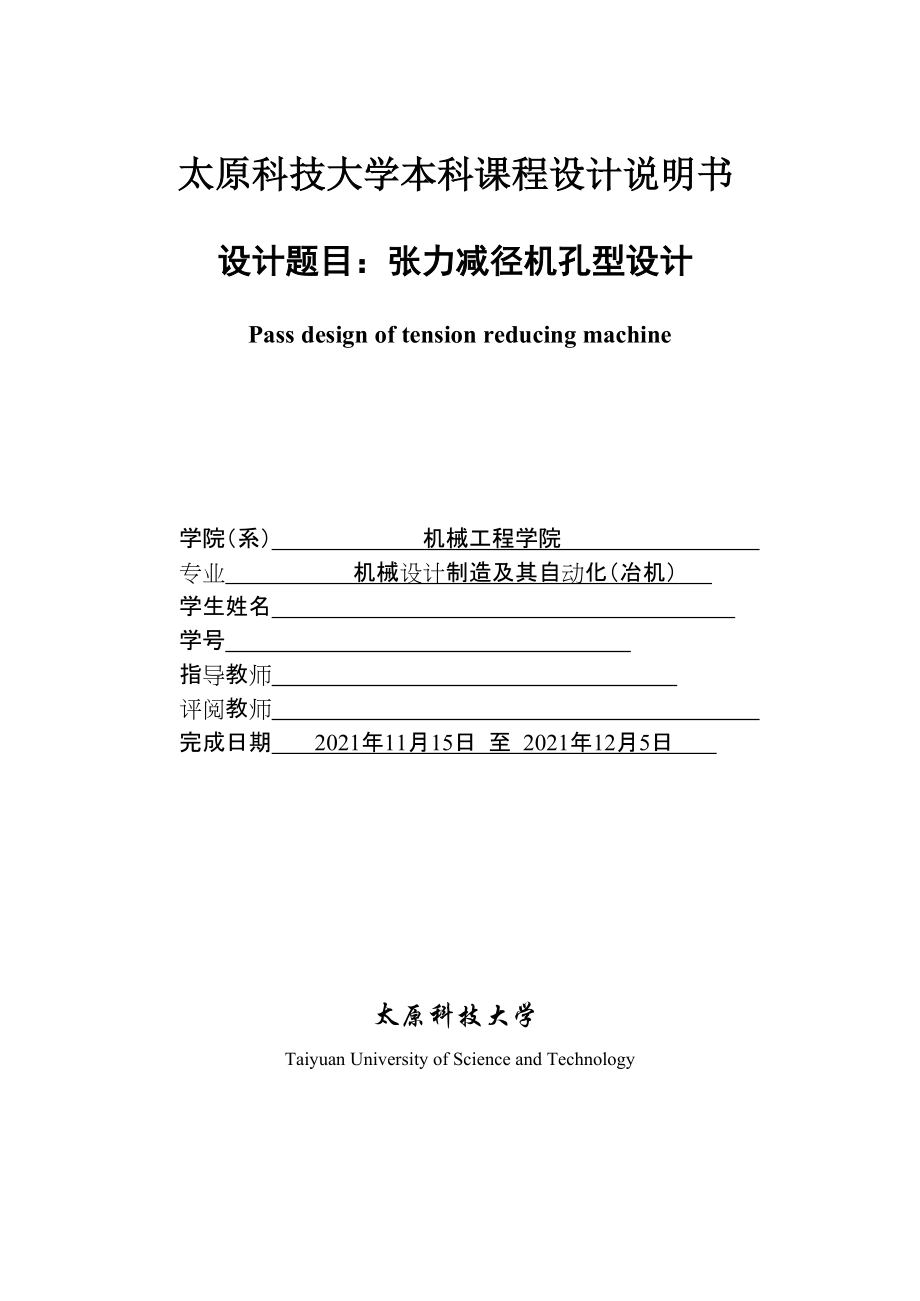


《张力减径机孔型设计》由会员分享,可在线阅读,更多相关《张力减径机孔型设计(30页珍藏版)》请在装配图网上搜索。
1、 太原科技大学本科课程设计说明书 设计题目:张力减径机孔型设计 Pass design of tension reducing machine 学院(系) 机械工程学院 专业 机械设计制造及其自动化(冶机) 学生姓名 学号 指导教师 评阅教
2、师 完成日期 2021年11月15日 至 2021年12月5日 太原科技大学 Taiyuan University of Science and Technology 太原科技大学 机械工程学院 轧 制 工 艺 学 课 程 设 计 任 务 书 专业班级 机自 181208 班 设计人 设计题目: 张力减径机孔型设计 设计参数:荒管规格:Φ 120mm,20钢;
3、 成品规格:34×5×10000mm、42×6×10000mm、48×5×10000mm、60*6×10000mm、76×8×10000mm; 入口速度:0.8m/s; 入口温度:900-950℃。 设计要求:了解张力减径机工作原理、减径机用途、不同规格产品的工艺计算及其运用范围。要求根据给定的设计内容,选定适当的参数,制定无缝钢管轧制规程以及轧
4、制温度、速度、轧制力矩等相关的计算,最后编写设计说明书并打印。 设计时间: 2021 年 11 月 15 日至 2021 年 12 月 5 日 设计人(签字) 指导教师(签字) 教研室主任(签字) 张力减径机孔型设计 摘要 张力减径作为生产无缝钢管的最后一道工序,对无缝钢管的尺寸规格和质量具有重要的影响。它使从轧机出来的荒管在张力作用下,实现减径、定径,减壁或者增壁,从而得到了多种规
5、格的成品钢管。根据张力机组中钢管减径所需要的所有工艺参数,利用以往的经验公式初步设计出各个孔型的几何尺寸和孔型加工参数,给定钢管成形所必须的初始条件。利用解析几何的方法,从实际生产需要出发,结合近现代张力减径变形机理研究成果,给出了钢管定减径过程相关工艺参数的计算方法。并应用于实际钢管张力减径生产。 本课题设计了荒管Φ120mm进行减径的张力减径机孔型参数。 关键词:无缝钢管;张力减径;孔型设计;工艺参数 I Abstract As the last procedure in the producti
6、on of seamless steel pipe, the micro-tension reducing has an important influence on the size, specification and quality of seamless steel pipe. Under the action of tension, the waste pipe from the mill can be reduced in diameter, sizing, wall reduction or wall increase, so as to obtain a variety of
7、specifications of finished steel pipe. According to all the technological parameters needed for reducing the diameter of steel tube in micro-tension unit, the geometric dimensions and machining parameters of each hole are preliminarily designed by using the previous empirical formulas, and the neces
8、sary initial conditions for steel tube forming are given. By means of analytical geometry, based on the actual production needs, and combined with the research results on the mechanism of micro-tension reducing deformation, the calculation method of related technological parameters in the process of
9、 constant reducing diameter of steel pipe is given. It is applied to the actual production of steel tube with small tension reducing diameter. In this paper, the process parameters of small expansion force reducing unit with diameter of φ 120mm are designed. Key words: Seamless steel tube; Tensi
10、on reduction; Design of grooves;The process parameters 目录 摘要 I Abstract II 第 1 章 绪论 1 1.1 我国无缝钢管的发展概述 1 1.2 无缝钢管的生产工艺和发展趋势 1 1.2.1 无缝钢管的生产工艺 1 1.2.2 无缝钢管的发展趋势 2 1.3 定(减)径机生产概述 2 1.3.1 定(减)径机 2 1.3.2 定径工艺 3 1.3.3 张力减径工艺 3 1.3.4 微张力减径工艺 3 第 2 章 确认生产方案 5 2.1 产品大纲的确定
11、5 2.1.1编制原则 5 2.1.2确定产品大纲 5 2.2 生产工艺流程 5 第 3 章 孔型设计 7 3.1 减径率分配原则 7 3.2 孔型设计的方法 7 3.3 本课题中孔型加工参数确定 11 3.3.1 基础数据 11 3.3.2 基本参数的确定 11 第 4 章 轧制力的相关计算 15 4.1 力能参数工程计算方法概述 15 4.2 各机架钢管壁厚计算 15 4.3 轧制力参数的确定 16 4.4 本课题轧制力参数的相关计算 18 4.4.1 张力系数确定 18 4.4.2 各机架孔型壁厚的确定 19 4.4.3 相关参数计算 20 第 5 章
12、 结论 21 参考文献 22 IV 板带热连轧压下规程的设定 第 1 章 绪论 1.1 我国无缝钢管的发展概述 我国无缝钢管行业起步于1952年,在新中国成立后,我国经济迈上了工业化道路,对无缝钢管需求大,但由于受到西方国家的经济封锁,无缝钢管的进口受到影响,因此我国在前苏联的帮助下开展了无缝钢管工程。 无缝管是一种具有中空截面、周边没有接缝的长条钢材。无缝钢管是一种经济断面钢材,在国民经济中具有很重要的地位,广泛应用于石油、化工、锅炉、电站、船舶、机械制造、汽车、航空、航天、能源、地质、建筑及军工等各个部门。
13、 进入20世纪以来,我国无缝管产量进入高速增长阶段。短短14年,我国无缝钢管产量从2001年年产500万吨,到2014年达到年产3000万吨以上的水平。我国已是世界钢管生产和消费大国。无缝钢管产量超过全球产量65%;出口量占我国无缝钢管产量15%;占世界无缝钢管总产量的10%。出口依存度比较高。在世界整体格局发生巨变之后,钢管行业会遇到更多的困难和不确定因素,出口面临更大压力。创新能力有待进一步提高。通过技术创新实现工艺进步,产品升级。只有拥有原创技术,才能立于行业的潮头,引领行业的发展。 1.2 无缝钢管的生产工艺和发展趋势 近年来,各国的无缝钢管生产有着飞速的发展,不仅是产量
14、的持续增加,其他如新设备、新技术以及新工艺的开发与应用也有着日新月异的进步。主要是将产品质量不断提高,将各种消耗降低,以便将经济效益最大化,提升国内(外)的市场的竞争。汽车工业、航空工业、锅炉制造、石油工业、国防工业各部门以及城市公用事业等等都需要大量的钢管,同时伴随日益激烈的国际竞争,为了达到各种经济以及技术指标,客户针对无缝钢管提出了越来越多的要求。 1.2.1 无缝钢管的生产工艺 轧管机组的类型决定无缝钢管生产工艺。热轧无缝钢管机组主要包括三辊轧管机组、连轧管机组、自动轧管机组、周期轧管机组、顶管机组和挤压管机组以及圆盘(狄塞尔)或精密轧管机组。 一般的无缝钢管生产的流程,基本上包
15、括三个主变形部分: ①将实心钢坯穿孔(轧制)成管状毛坯的“毛管”; ②将“毛管”轧制成热成品管要求壁厚的“荒管”; ③将“荒管”轧制成热成品管要求外径的“热成品管”。 无缝钢管大约是在 100 年前开始出现的。无缝钢管应用范围极为广泛,特别是用于国计民生当中。各国生产无缝钢管的工艺类似,无缝钢管工艺流程如图 1.1 所示。 图 1.1热轧无缝钢管工艺流程图 1.2.2 无缝钢管的发展趋势 我国无缝钢管行业在转型升级阶段已经取得了一定的成效,但离成为全球无缝钢管生产强国仍有一定的距离,我国无缝钢管企业仍需努力。在供给侧的改革背景下,企业应当坚持摒弃以量取胜的发展道路,而更应
16、关注产品的附加值,打造高质量产品。前瞻认为,在未来的发展趋势上,我国无缝钢管行业将往产品高端化、市场集中化、生产绿色化和智能制造化等方向发展。 ①产品高端化。在激烈的竞争环境下,无缝钢管企业将会更加关注产品质量,专注研发与技术,生产附加值更高的产品。 ②市场集中化。在行业供给侧改革的背景下,行业兼并重组也得到了国家的支持,企业强强联合趋势明显,行业市场集中度将会进一步提升。 ③生产绿色化。国家发布政策淘汰行业高耗能生产工艺设备,企业环保税越来越高。低碳环保、绿色生产将为大势所趋。 ④智能制造化。在“互联网+”背景下,无缝钢管企业将往基础自动化、生产过程可控化、制造执行化、企业管理化等智
17、能制造方向发展。 1.3 定(减)径机生产概述 1.3.1 定(减)径机 钢管定减径机是由若干对带有孔槽的轧辊组成的,轧辊排列时要使得每组轧辊所形成的孔型中心线都在一条直线上,荒管连续地经过轧辊,而孔型直径逐渐减小,因此荒管通过轧辊后由荒管的原始直径减为最终所需尺寸。相邻机架间轧辊布置互成一定角度,这样,轧辊边缘间形成的间隙沿荒管的纵向并不都在一条直线上,对于二辊定径机或张力减径机,相邻两机架的轧辊中心线互成 90°,有时也采用较小的角度。对于三辊定减径机,相邻机架的轧辊中心线互成 60°。企业中也常用四辊定减径机。在四辊式定减径机架中,每一个轧辊同将近四分之一的管子圆周相接触。 1.
18、3.2 定径工艺 由图 1.1 可以看出,定减径是热轧生产无缝钢管的最后一道工序。定(减)径工艺可分为定径、张力减径和无张力减径三大类。只减小荒管直径而不能同时减小荒管壁厚的过程一般称为定径。定径的主要目的是消除前道工序造成的外径不一,得到外径精度和真圆度都比较高的成品管。定径机的工作机架较少,一般为 3~12 架,三辊定径机组单机架的减径量在 3%~5%之间(在二辊定减径机组上,单机架的减径率在 2%~3%)。二辊式定径机和三辊式定径机的主要区别:二辊式定径机精度没有三辊式高;二辊式定径机的孔型参数可调,三辊式的孔型参数不可调;二辊式定径机设备投资少,而三辊式的则不然。 1.3.3 张力
19、减径工艺 张力减径机在轧制过程中既可以减少管子的外径也可以减少管子的壁厚。张力减径中的张力是指轧辊施加给轧件的纵向拉力。钢管在张力减径过程中,通过切向变形和径向变形来达到轴向变形的目的。张力减径机的机架数比较多,一般超过 16;由于轧制过程存在张力,使得单机架减径率也较大,在 12%~14%之间,机组总减径量可在75%~80%之间,总减壁量可以超过 40%。张力减径机可以用一种规格的荒管获得多种不同规格的成品管,因而扩大了机组的生产范围,有效地提高了机组的生产效率和产品质量。张力减径机主要用来生产中小直径薄壁管、中厚壁管。 1.3.4 微张力减径工艺 微张力减径是处于张力减径和无张力减径
20、之间的一种情况。张力系数一般小于 0.5。微张力减径的机架数通常都比较少,一般不超过 14,单机架减径率小于 3.5%,总减径率不超过 35%。张力减径和微张力减径的原理基本一样。张力减径和微张力减径的区别在于:张力减径时的张力系数一般都大于 0.5,而微张力减径时的张力系数一般都小于 0.3;张力减径时的机架数更多、减径量更大和产品规格范围更广;而微张力减径时机架数较少、减径量较小和产品规格较少。 第 2 章 确认生产方案 2.1 产品大纲的确定 2.1.1编
21、制原则 国民经济发展对产品的要求。根据国民经济各部门对产品数量、质量和品种等方案的需要情况,既考虑当前的急需,又要考虑将来发展的需要。产品的平衡。考虑全国各地生产的布局和配套加以平衡。考虑轧机生产能力的充分利用和建厂地区产品的合理分工。考虑建厂地区及资源用钢的供应条件、物资和材料等运输情况,逐步完善我国自己独立的轧钢生产体系。解决产品品种和规格老化的问题,要适应当前对外开放,对内搞活的―新经济形势的需要。需根据车间工业设备的情况,力争做到产品标准的现代化。 2.1.2确定产品大纲 表2.1产品设计大纲 产品规格 外径(mm) 厚度(mm) 长度(mm) 1 60 6
22、 10000 2 76 8 10000 3 89 7 10000 4 102 9 10000 5 114 8 10000 2.2 生产工艺流程 圆管坯→加热→穿孔→三辊斜轧、连轧或挤压→脱管→定径(或减径)→冷却→矫直→水压试验(或探伤)→标记→入库 以最大减径率计算外径120mm荒管生产出成品管所需的最大机架数目,保证定(减)径机能生产所有规格产品。当减径率较小时,多出机架数目设置为定径机机架及精整机架,生产出符合要求的成品管。
23、 第 3 章 孔型设计 3.1 减径率分配原则 微张力减径机组种的各机架减径率如何分配,主要是从管子的质量考虑。首先保证管子在孔型中轧制的稳定,易于咬入,不发生震动。其次,管子在孔型中即不可过充满,出现耳子,表面刮伤,也不能欠充满,使外圆不圆,壁厚不均。若使用较大的减径率虽然可以减少机架数目,但很容易在管子内部出现内多边形缺陷。取较小的减径率虽然可以保证管子表面质量,壁厚均匀,轧制工具寿命延长,但受总机架数目的限制。此外,减径率的分配还受张力减径机传动方式,咬入条件和轧机弹跳值对单机架减径率的限制等诸多因素有关。 根据实际经验,从轧管机出来的荒管带有一个直径比较大的端部,为了保证减径机第
24、一架顺利咬入,第一架选取计算使用的压下量比较小。工厂生产中常把第一架的压下量称为虚压下,甚至第一架的平均孔型直径比荒管直径大的情况也有出现。成品机架前的机架压下量取平均压下量的 1/2,而一般最后一架(或 2 架)为成品机架,压下量很小或几乎没有。 设各机架的直径相对压下量为η1、η2、……ηn-1、ηn(n 为工作机架数目),在生产过程中随着轧制机架数目的增加、变形程度的增加、轧制速度的加快和轧制温度的下降,都会使变形抗力和摩擦系数增大,从而使轧制力能消耗增大和工具磨损加剧。因此从均衡各机架能耗与磨损角度看,减径率递减分配方法更为合理(图 3.1)。 图3.1张力减径率分配曲线
25、 3.2 孔型设计的方法 (1)首先计算机架数量 求机架数量的公式为: n=lg(de/d0)lg(1-η平)+q (3-1) 式中 q —机架折合数(取 1-2); de —成品管直径,mm; d0 —荒管直径,mm; η平—平均减径率(取 2.5%—3%)。 (2)确定各机架减径率ηi 根据选定的平均减径率和机架数目,按照图 3.1 所示的减径量分配原则,选择出各个机架的减径率。 (3)根据公式 di=di-1(1-ηi)求得各机架的平均孔型直径 di。 (4)根据各机架的η值由ξ = ƒ(η)曲线(图
26、3.2)求出椭圆度影响系数ξ。 图3.2 ξ和ρ的关系 (5) 由η、ξ确定孔型椭圆度 ρi 。 ρi=1ξi(1-ηi) (3-2) (6) 由ρi求出 ai、 bi 。 ai=di1+1ρi (3-3) bi=di1+ρi (3-4) 图 3.3 孔型尺寸示意 其中ai、 bi 为孔型的长半轴和短半轴。 (7) 轧辊直径
27、的确定(图3.4) a. 轧辊的理想直径: Did≧∆h1-cosα (3-5) 式中 ∆h—压下量,mm; α—咬入角,型钢时区15°。 b. 在张力减径轧制的椭圆孔型辊面上,由于轧辊直径的不断变化,轧辊上每点的圆周速度是不一样的,钢管则是以同一出口速度离开轧辊: v=π⋅n60Dk (3-6) 式中 Dk—轧制直径; n—轧辊转速。 图3.4 轧制直径简图 c. 当在张即减径过程中不考虑相邻的机架间的张力时,孔型直径di 、轧辊理想直径Did以及轧制
28、直径Dk三者之间的关系的关系可用下式表示: Dk=Did-dicosθ (3-7) 式中: θ—中心角。 d. 由(3-6)可确定轧辊转速(单位:rad/min) ni=1000×6×viπDk (3-8) (8) 轧辊孔型加工刀具直径及刀具距离(图3.5) 令 X=bi-bi2Dwi-ai2+ai2Dwi 则 WDi=X+0.75ai22 (3-9) WAi=(RWi-bi)2-(RWi-RDi)2 (3-10) 式中 DWi —轧辊理想直径,mm; WDi—
29、孔型加工刀具直径,mm; WAi—孔型加工刀具距离,mm; RWi—轧 辊 理 想 半 径 ,RWi =DWi /2,mm RDi—加 工 刀 具 半 径 , RDi =WDi /2,mm。 图3.5 孔型加工示意图 (9) 张力减径机机架间的塑性变形 轧制过程体积不变。实际上,物体在塑性变形过程中体积会有微小的变化,这是由于通过塑性变 形会使物体密度增加或减小(钢锭经过轧制,组织变得致密使密度增加,热轧过的金属再进行冷却,由于晶体间及晶体内的破坏增加了疏松程度,因而密度略有减小)。此外,在弹性变形时,体积也略有减小。总之,上述体积的变化是微小的,在实际计算时是可以
30、认为不变的,用数学公式可以表示为 V1=V2。 (10) 钢管在孔型中的减径量Δd ∆d=di-12-2bi (3-11) 3.3 本课题中孔型加工参数确定 3.3.1 基础数据 基础数据是工艺设计前所给定的参数数据,它们包括荒管规格、成品管规格、入口速度、机架间距、轧辊理想直径、热膨胀系数等。本课题轧制实验中所给出的基础数据如下: 荒管规格: Φ120mm ; 成品管规格: Φ60×6×10000mm ;Φ76×8×10000mm ;Φ89×9×10000mm ;Φ102×10×10000mm ;Φ
31、114×12×10000mm 入口速度: 0.8m/s 入口温度: 900℃ 材料: 20钢 3.3.2 基本参数的确定 基本参数是工艺设计计算中首先需确定的参数,其中包括各机架减径率、椭圆度和张力系数三组数据,以成品管Φ60×6×10000mm为例。 a. 根据公式(3-1)确定机架数目 n=lg(60/120)lg(1-3%)+2≈25 b. 由图3.1确定各机架减径率 根据机架数,与选定的平均减径率,给出各机架减径率,减径率如表3.1 表3.1 各机架减径率 η1
32、 η2 η3 η4 η5 η6 η7 η8 η9 η10 1.70% 1.80% 2.00% 2.70% 3.20% 3.45% 3.41% 3.38% 3.37% 3.34% η11 η12 η13 η14 η15 η16 η17 η18 η19 η20 3.27% 3.26% 3.25% 3.18% 3.17% 3.14% 3.09% 3.07% 2.98% 2.96% η21 η22 η23 η24 η25
33、 2.90% 2.69% 1.90% 0.71% 0.35% c. 各孔型椭圆度系数 ρi 首先由图 3.2确定椭圆度影响系数ξ,设计中可根据经验对其数值做适当 调整,然后根据式(3-2)计算各孔型椭圆度系数,计算结果见表 3.2 表3.2 各孔型椭圆度系数ρi ξi ρi 第一架 0.9819 1.037 第二架 0.9772 1.044 第三架 0.9792 1.050 第四架 0.9863 1.047 第五架 0.9914 1.042 第六架 0.9924 1.044 第七架 0.9931
34、 1.042 第八架 0.9935 1.042 第九架 0.9840 1.052 第十架 0.9844 1.051 第十一架 0.9822 1.053 第十二架 0.9834 1.051 第十三架 0.9845 1.050 第十四架 0.9835 1.050 第十五架 0.9836 1.050 第十六架 0.9878 1.045 第十七架 0.9854 1.047 第十八架 0.9856 1.047 第十九架 0.9880 1.043 第二十架 0.9930 1.038 第二十一架
35、0.9912 1.039 第二十二架 0.9940 1.034 第二十三架 0.9993 1.020 第二十四架 0.9990 1.008 第二十五架 1.0000 1.004 d. 孔型几何加工参数计算 由式(3-3)、(3-4)、(3-5)、(3-7)、(3-9)、(3-10)、(3-11)确定孔型几何加工参数,计算结果见表3.3 表 3.3 孔型几何加工参数 机架序号 孔型平均直径 单架减径率 孔型长半轴 孔型短半轴 椭圆度 轧辊理论直径 轧辊工作直径 刀具直径 刀具距离 121.296 % a b α
36、DW Dk WD WA 1 119.234 1.70 60.703 58.531 1.037 360 256.743 124.529 29.884 2 117.088 1.80 59.810 57.278 1.044 360 258.602 123.349 32.555 3 114.746 2.00 58.761 55.985 1.050 360 260.630 121.694 34.384 4 111.648 2.70 57.117 54.531 1.047 360 263.313 118
37、.156 33.471 5 108.075 3.20% 55.150 52.926 1.042 360 266.407 113.691 31.318 6 104.347 3.45% 53.288 51.059 1.044 360 269.636 110.043 31.721 7 100.788 3.41% 51.443 49.346 1.042 360 272.717 106.188 31.071 8 97.382 3.38% 49.687 47.695 1.042 360 275.667
38、102.549 30.567 9 94.100 3.37% 48.236 45.864 1.052 360 278.509 100.386 33.801 10 90.957 3.34% 46.608 44.349 1.051 360 281.231 96.990 33.281 11 87.983 3.27% 45.117 42.865 1.053 360 283.807 94.055 33.530 12 85.114 3.26% 43.618 41.496 1.051 360 286.291
39、 90.868 32.793 13 82.348 3.25% 42.176 40.173 1.050 360 288.686 87.808 32.087 14 79.730 3.18% 40.840 38.889 1.050 360 290.954 85.085 31.901 15 77.202 3.17% 39.542 37.660 1.050 360 293.143 82.398 31.540 16 74.778 3.14% 38.215 36.563 1.045 360 295.242
40、 79.335 29.680 17 72.467 3.09% 37.069 35.399 1.047 360 297.243 77.115 30.059 18 70.243 3.07% 35.923 34.319 1.047 360 299.170 74.729 29.632 19 68.149 2.98% 34.796 33.354 1.043 360 300.983 72.182 28.202 20 66.132 2.96% 33.679 32.453 1.038 360 302.730
41、 69.548 26.068 21 64.214 2.90% 32.721 31.493 1.039 360 304.390 67.661 26.245 22 62.487 2.69% 31.763 30.724 1.034 360 305.886 65.393 24.190 23 61.300 1.90% 30.955 30.345 1.020 360 306.914 62.972 18.442 24 60.864 0.71% 30.556 30.309 1.008 360 307.291
42、 61.531 11.688 25 60.651 0.35% 30.379 30.273 1.004 360 307.476 60.936 7.649 e. 轧辊轧制出口速度vi 由式(3-6)及μi=(di-1-si-1)si-1(di-si)si ,当 i=1 时, v1=v0×μ1其中 v0为荒管进入第 1 机架轧辊的入口速度,μ1为第一架延伸系数。 计算结果如下表3.4 表3.4 延伸率与出口速度结果 机架号 1 2 3 4 5 6 7 8 9 μi 1.013 1.015 1.017 1.024 1.02
43、9 1.031 1.031 1.031 1.031 vi 0.810 0.822 0.836 0.856 0.881 0.908 0.936 0.965 0.994 机架号 10 11 12 13 14 15 16 17 18 μi 1.031 1.030 1.030 1.030 1.030 1.030 1.030 1.030 1.030 vi 1.025 1.056 1.088 1.121 1.154 1.189
44、 1.224 1.260 1.298 机架号 19 20 21 22 23 24 25 μi 1.029 1.029 1.028 1.027 1.017 1.006 1.002 vi 1.335 1.374 1.413 1.450 1.475 1.484 1.487 第 4 章 轧制力的相关计算 4.1 力能参数工程计算方法概述 张力减径过程中钢管通过轧辊时,一定的轧辊转速n将对应着一定秒流量体积
45、FV(其中F为轧件出口截面积,V为轧件出口的速度)。相邻的两个机架连轧时,设定两个机架的转速分别为n1和n2,当n1减少或者n2增加时,按自然轧制条件关系式有F1V1 46、
se—成品管壁厚,mm。
张力系数在中间机架一般按照相等的原则进行分配,张力系数分配曲线见(图4.1)
图4.1 张力系数分配曲线
4.2 各机架钢管壁厚计算
各孔型的平均孔型直径 di 已知,当已知 si-1 和选定 Zi 后。可利用迭代法求出经过各个机架管子的壁厚值 si。公式如下:
ri=12(sidi+si-1di-1) (4-2)
βi=2Zi(ri-1)+(1-2ri)Zi(1-ri)-(2-ri) (4-3)
Si=Si-1(di-sidi-1-si-1) 47、 (4-4)
其中
Zi—第 i 架平均张力系数;
ri—第 i 架变形区壁厚系数;
βi—第 i 架管子的壁厚和中径的对数变形比;
di —第 i 架管子轧后外径,mm;
di-1—第 i 架管子轧前外径,mm;
si—第 i 架管子轧后壁厚,mm;
si-1—第 i 架管子轧前壁厚,mm;
先以 si-1 代替式(4-2)中 si 求出 ri,再以此 ri 代入式(4-3)中求出βi,再以此βi 和 si-1 代替(4-4)中括号内的 si 用式(4-4)计算得到另一个 si 值。再以此 si 作为已知代入(4-2)-(4-4)带到新的 si 48、 值。如此不断迭代,直到前后两次所得的 si 值无明显变化(两者差小于 0.01mm)时,把最后得到的 si 值作为所求即可。然后通过这种迭代的办法求出通过所有机架轧辊钢管的壁厚值。如果求出的壁厚偏差超过公差,则要从新选择荒管壁厚或张力系数。
4.3 轧制力参数的确定
(1)轧制力的计算
Pi=2.1×si×Kf(1-Zm)Rd(di-1-di) (4-5)
Kf=1.15σs
σs=e0.126-1.750C+0.594C2+(2851+2968C-1120C2)Tk×u0.13×r0.21
u=2πni60εRidiln11-ε
r=ln11-ε 49、
ε=di-1-didi
式中
Kf—金属塑性变形抗力,MPa;
C—碳含量(质量分数),20%;
Tk—绝对温度,1173.15K;
u—变形速度;
r —变形程度,%;
ε—相对减径量。
(2) 接触弧长度和接触面积的计算(图4.2)
对于三辊微张减机接触弧长而言,计算接触弧长的公式为:
Li=(0.9~0.95)(ai-1-bi)[Dmin-(ai-1-bi)] (4-5)
式中
Dmin—轧辊孔型底部最小直径(mm),Dmin≈Dk-di;
Dk—轧辊理论直径(mm),Dk=360mm;
ai-1—第i-1架孔型长半 50、轴(mm);
bi—第i 架孔型短半轴(mm)。
图4.2 接触弧长度
(3) 接触面积公式为:
Fi=3aiLi (4-6)
(4) 轧制力矩计算:
M=RdKf[π∆disi(1-Zm)+(Fi-1Zi-1-FiZi)] (4-7)
式中—第 i 架钢管横断面面积 Fi=π(di-si)si
∆d=di-1-di
(5) 轧制功率
N=nM/9450 (4-8)
(6) 切头长度
Lc=2Cdu (4-9)
η=s0(d0-s0)se( 51、de-se)
式中
Cd —机架间距,mm;
η —总延伸率。
4.4 本课题轧制力参数的相关计算
4.4.1 张力系数确定
确定张力系数要先由式(4-1)确定最大张力系数。本次轧制实验所确定的最大张力系数算法如下,其中可确定的条件:
荒管规格:d0=120mm ;s0=5.5mm
成品管规格:de=60mm ;se=6mm
最大张力系数Zm为:
c=0.5(s0d0+sede)=0.5(5.5120+660)=0.0729
A=ln(s0/se)ln[(d0-s0)/(de-se)]=ln(5.5/6)ln[(120-5.5)/(60-6)]=-0.11 52、58
Zm=1-2C-AC+2A2+2C-AC+A=0.3096
如图4.1的张力分配原则所示方式,各张力系数选择如表 4.1
表4.1 各张力系数选取
Z1
Z2
Z3
Z4
Z5
Z6
Z7
Z8
Z9
Z10
0.180
0.260
0.300
0.310
0.310
0.310
0.310
0.310
0.310
0.310
Z11
Z12
Z13
Z14
Z15
Z16
Z17
Z18
Z19
Z20
0.310
0.310
0.310 53、
0.310
0.310
0.310
0.310
0.310
0.310
0.310
Z21
Z22
Z23
Z24
Z25
0.310
0.310
0.220
0.180
0.000
4.4.2 各机架孔型壁厚的确定
各孔型壁厚的确定由式(4-2)至(4-4)迭代获得。
表 4.2 各机架孔型中壁厚迭代结果
s1
s2
s3
s4
s5
s6
s7
s8
s9
s10
5.591
5.617
5.6 54、41
5.671
5.708
5.747
5.786
5.825
5.863
5.901
s11
s12
s13
s14
s15
s16
s17
s18
s19
s20
5.938
5.975
6.012
6.048
6.083
6.118
6.152
6.186
6.219
6.251
s21
s22
s23
s24
s25
6.282
6.311
6.342
6.356
6.367
55、
4.4.3 相关参数计算
根据式(3-6)、(3-8)、(4-5)如轧辊转速,轧制力,轧制功率等。结果见表4.3
表4.3 参数计算结果
机架号
出口速度
轧制力
轧制力矩
轧辊转速
轧制功率
1
0.810
147.374
-2.6784
60.260
-17.079
2
0.822
153.681
-2.1712
60.710
-13.949
3
0.836
166.410
-0.7071
61.282
-4.585
4
0.856
210.029
0.6743
62 56、.107
4.432
5
0.881
238.738
1.2716
63.140
8.496
6
0.908
251.336
1.3710
64.320
9.331
7
0.936
246.717
1.3146
65.553
9.119
8
0.965
242.783
1.2658
66.842
8.953
9
0.994
240.075
1.2287
68.195
8.867
10
1.025
236.294
1.1835
69.606
8.717
11
1.056
230.361
1.1220
71.055 57、
8.436
12
1.088
227.909
1.0902
72.568
8.372
13
1.121
225.502
1.0596
74.149
8.314
14
1.154
219.848
1.0047
75.767
8.055
15
1.189
217.599
0.9771
77.452
8.008
16
1.224
214.307
0.9425
79.196
7.899
17
1.260
210.002
0.9015
80.987
7.726
18
1.298
207.400
0.8737
82.84 58、3
7.659
19
1.335
201.104
0.8213
84.721
7.363
20
1.374
198.669
0.7966
86.663
7.305
21
1.413
194.155
0.7588
88.643
7.118
22
1.450
181.740
0.6728
90.551
6.447
23
1.475
137.297
2.2294
91.778
6.652
24
1.484
63.350
0.7127
92.220
6.955
25
1.487
36.504
0.2987
92.393 59、
2.920
第 5 章 结论
以中厚壁钢管张力减径的金属变形理论为基础,根据张力减径的理论进行减径工艺公式的推导。然后根据相关公式,推导出每一机架孔型的相关尺寸,其中还包括减径孔型的加工问题。根据上面推导并计算的结果,进行轧辊轧制直径的计算以及进行轧辊转速的计算,根据相关公式计算钢管的壁厚等。
本设计方法中,同一变形系列的孔型所轧制钢管的壁厚范围较窄,这有利于轧机的稳定工作,同时也有效地改善了成品管质量。
在具体设计过程中设定的张力机组和成品机组各机架的延伸率以及工作机组的平均延伸率可视轧制材料、轧机负荷、钢管变形温度等实际情况做相应的调整。
60、
参考文献
[1] 王延溥.齐克敏.金属塑性加工学—轧制理论与工艺[M].北京:冶金工业出版社,2018.
[2] 帅美荣.刘光明.塑性力学与轧制原理[M].北京:冶金工业出版社,2019.
[3] 马立峰.赵春江.杨霞.轧钢机械设计[M].北京:冶金工业出版社,2021.
[4] 邹家祥.轧钢机械[M].北京:冶金工业出版社,2021.
[5] 汪建业.重型机械标准[M].昆明:云南科技出版社,2007.
[6] 周研.钢管微张力减径工艺参数研究及软件开发[D].太原:太原科技大学材料科学与工程学院,2008.
[7] 刘鹏.钢管张力减径工艺研究及应用软件开发[D].太原:太原科技大学材料科学与工程学院,2011.
[8] 王琦.无缝钢管微张力减径工艺参数的研究[D].太原:太原科技大学材料科学与工程学院,2016.
[9] 马辉.微张力减径机孔型设计和轧制表计算方法[N].鞍钢技术,2004年第6期
22
- 温馨提示:
1: 本站所有资源如无特殊说明,都需要本地电脑安装OFFICE2007和PDF阅读器。图纸软件为CAD,CAXA,PROE,UG,SolidWorks等.压缩文件请下载最新的WinRAR软件解压。
2: 本站的文档不包含任何第三方提供的附件图纸等,如果需要附件,请联系上传者。文件的所有权益归上传用户所有。
3.本站RAR压缩包中若带图纸,网页内容里面会有图纸预览,若没有图纸预览就没有图纸。
4. 未经权益所有人同意不得将文件中的内容挪作商业或盈利用途。
5. 装配图网仅提供信息存储空间,仅对用户上传内容的表现方式做保护处理,对用户上传分享的文档内容本身不做任何修改或编辑,并不能对任何下载内容负责。
6. 下载文件中如有侵权或不适当内容,请与我们联系,我们立即纠正。
7. 本站不保证下载资源的准确性、安全性和完整性, 同时也不承担用户因使用这些下载资源对自己和他人造成任何形式的伤害或损失。