毕业设计(论文)-垄作玉米机械除草装置的设计
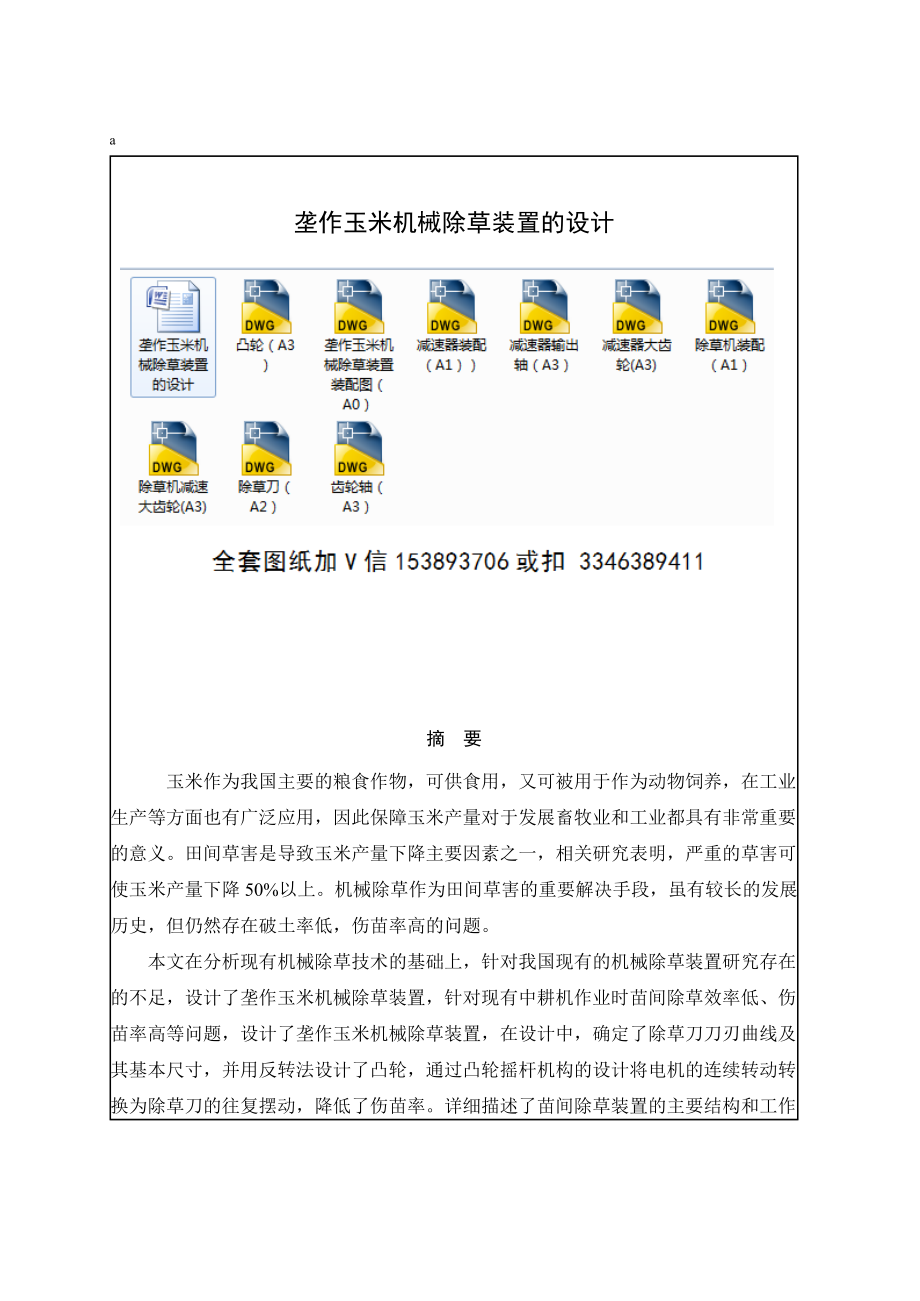


《毕业设计(论文)-垄作玉米机械除草装置的设计》由会员分享,可在线阅读,更多相关《毕业设计(论文)-垄作玉米机械除草装置的设计(40页珍藏版)》请在装配图网上搜索。
1、a 垄作玉米机械除草装置的设计 摘 要 玉米作为我国主要的粮食作物,可供食用,又可被用于作为动物饲养,在工业生产等方面也有广泛应用,因此保障玉米产量对于发展畜牧业和工业都具有非常重要的意义。田间草害是导致玉米产量下降主要因素之一,相关研究表明,严重的草害可使玉米产量下降50%以上。机械除草作为田间草害的重要解决手段,虽有较长的发展历史,但仍然存在破土率低,伤苗率高的问题。 本文在分析现有机械除草技术的基础上,针对我国现有的机械除草装置研究存在的不足,设计了垄作玉米机械除草装置,针对现有中耕机作业时苗间除草效率低、伤苗率高等问题,设计了垄作玉米机械除草装置,在设计中,确
2、定了除草刀刀刃曲线及其基本尺寸,并用反转法设计了凸轮,通过凸轮摇杆机构的设计将电机的连续转动转换为除草刀的往复摆动,降低了伤苗率。详细描述了苗间除草装置的主要结构和工作原理,建立和分析了除草刀避苗运动轨迹数学模型,优化除草装置避苗运动轨迹,用反转法设计了凸轮,并在此基础上对垄作玉米机械除草装置的关键部件,如除草刀,凸轮摇杆机构和弹簧等进行了设计。对比于传统除草机械,本文拟设计的除草机将电机的旋转通过凸轮转变为除草刀的往复运动,降低了伤苗率。 关键词:凸轮摇杆;除草;伤苗率;反转法 Design on Mechanical Weeding Device of Ri
3、pple Maize Abstract Maize is one of the main food crops in China. It is not only edible for people, but also used in animal feed and industrial production. Therefore, ensuring corn production is of great significance for the development of animal husbandry and industry. Field grass damage is one o
4、f the main factors leading to the decline of corn yield. Relevant research shows that severe grass damage can reduce corn yield by more than 50%. At present, the main methods of weeding in China include manual weeding, chemical weeding, and mechanical weeding. Manual weeding is labor intensive and
5、inefficient, and only a few areas use manual weeding methods. The chemical weeding machine has high efficiency and saves manpower. It is the current mainstream weeding method, but the chemical weeding method effectively controls the weeds and also has many adverse effects. For example, repeated use
6、of herbicides makes the field weeds resistant and seriously pollutes the farmland environment. Pesticide residues threaten people's diet and health. In recent years, with the increasing awareness of environmental protection, mechanical weeding has gradually attracted people's attention. Mechanical w
7、eeding has the advantages of high herbicidal efficiency and low environmental pollution. Therefore, research on mechanical weeding is of great significance. In order to solve the problems of low weeding efficiency and high rate of seedling damage during the operation of the existing cultivator, a C
8、AM rocker swinging weeding device between seedlings was designed. Through the design of CAM rocker mechanism, the continuous rotation of the motor was converted into the reciprocating swing of the weeding cutter, so as to achieve the purpose of weeding without harming the seedlings. The main structu
9、re and working principle of the inter-seedling weeding device were described, the mathematical model of the movement track of the weeding cutter to avoid seedlings was established and analyzed, and the movement track of the weeding device to avoid seedlings was optimized. On this basis, the key comp
10、onents of the cam-rocker swinging inter-seedling weeding device, such as weeding cutter, cam-rocker mechanism and spring, were designed. Key words: rocker CAM ;weeding ;injure rate;reversal process 目 录 1 绪论 1 1.1 课题背景与意义 1 1.2 国内外研究现状 2 1.2.1 爪式株间玉米机械除草装置 2 1.2.2 刷式株间机械除草装置 3 1.
11、2.3 智能株间机械除草装置 3 2 技术任务书(JR) 5 2.1 设计依据 5 2.3 主要技术参数 5 2.4 主要研究内容 6 3 设计计算说明书(SS) 7 3.1 整机结构及工作原理 7 3.1.1 整机结构 7 3.1.2 工作原理 7 3.2 除草刀设计 7 3.2.1 除草刀基本尺寸设计 7 3.2.2 除草刀切刃曲线设计 8 3.3 凸轮摇杆机构设计 8 3.3.1 凸轮基本尺寸的设计 9 3.3.2 凸轮运动规律选择 10 3.3.3 摆杆长度设计 11 3.3.4 凸轮机构轮廓曲线的设计 11 3.4 除草刀受力分析及弹簧参数确定 12
12、 3.4.1 除草刀的运动分析 12 3.4.2 除草刀受力分析及弹簧参数 13 3.4.3 齿轮轴及齿轮设计 14 3.5 减速器设计 16 3.5.1 拟定减速器传动方案 16 3.5.2 减速器电动机选择 17 3.5.3 计算传动装置总传动比和分配各级传动比 18 3.5.4 计算减速器传动装置的运动和动力参数 18 3.5.5 带轮设计 19 3.5.6 减速器轴的设计 21 3.5.7 减速器齿轮设计 21 3.5.8 减速器轴校核 23 3.5.9 键的选择 25 3.5.10 减速器附件选择 25 4 使用说明书 27 4.1 操作说明 27
13、4.2 注意事项 27 5 标准化审查报告 28 结 论 29 参考文献 30 致 谢 32 1 绪论 1.1 课题背景与意义 近年来,我国玉米的种植面积与产量大幅增加。2021年,玉米种植面积超过3700万公顷,产量达到1.5亿至2.7亿吨,玉米的稳产对保障国家粮食战略安全起着至关重要的作用[1]。我国玉米的总产量虽然令他国羡慕,但单产却不尽人意。加强农业管理,控制杂草是提高玉米产量的有效途径;其中,人工除草、化学除草和机械除草是应用最广泛的除草方法,而其他除草方法由于成本高、适应性差,仍难以广泛应用[2-5]。田间杂草是农业生态系统的一部分,杂草会与作物竞争生
14、长资源,导致作物营养不良,无法生长,也容易使病虫害滋生,影响农作物的栽培。因此,农田杂草是制约作物高产的主要因素之一[6,7]。我国作为一个粮食消耗大国,每年因草害损失的粮食达数百亿公斤[18]。因此,除草在农业生产中的地位极高。研究和开发除草技术和设备对保证粮食的生长具有重要意义。现在世界上主要的除草方法有人工除草、化学除草、机械除草、生物除草和热电除草等[8-10]。在经济技术和社会的快速发展的今天,原本的除草方法除草效率低、人工成本高等弊端日益突出。田间最常用的除草方法是药剂除草,这种除草方法可以同时清除行间和幼苗间的杂草。药剂除草省力、省时、快捷、高效。然而,除草剂的长期使用也给农业带
15、来环境污染和杂草抗性增强等问题,威胁着人们的饮食健康[11]。随着全民环境保护意识的增强,机械除草的应用开始广泛应用,机械除草是去除田间杂草最常用的方法 [12-15]。机械除草具有工作效率高、劳动强度低、无环境污染等优点,还不会破坏土壤养分。随着现代农业技术的发展,应用伤苗率低,无环境污染的除草机已经引起人们的关注[16,17]。然而,现在的机械除草存在许多问题,首先,现阶段的除草机虽可以消除行间杂草,但由于杂草的幼苗与作物相似,故杂草幼苗难以清除;第二,在连续实施新政策后,土壤重量和粘度增加,现有的除草机在粘性土的条件下,存在除草、破碎土效果差、操作耗电等问题。因此,在重粘土条件下,设计和
16、开发一种既能控制行间苗间杂草,又能同减少运行功率消耗的新型机械除草设备具有重要意义[18]。 1.2 国内外研究现状 行间除草机械已经有了长时间的发展,并且,大量型号的除草机已经得到推广和使用。因为幼苗之间的杂草形状与幼苗相似,因此幼苗之间的除草技术更加困难。随着现代农业技术的发展,苗 (株) 间的除草机械逐渐发展起来[18]。 1.2.1 爪式株间玉米机械除草装置 胡炼等[19,20]设计了一种带有爪齿的进行余摆线运动的株间机械除草装置(见图1-1),该装置通过算法来控制爪齿进行余摆线运动以达到避苗以及除草的目的。陈勇等设计了智能除草机器人人(见图1-2)。该装置使用除草刀切割杂草,
17、并在杂草断裂处涂抹除草剂,以完全消除杂草[21-23]。吴建等[24]设计了一种自动可视除草机器人。 图1-1 爪式株间机械除草机 图1-2 智能除草机 Nerremark等人研究了多种类型的植间除草载具人。图1-3是爪式除草机。该除草机通过匹配载具的前进速度和爪齿转速,同时实现了避苗和除草[25-30]。 图1-3 爪式株间除草机构 1.2.2 刷式株间机械除草装置 奥胡斯大学的Melander等人设计了一种刷盘式作物间除草机(见图1-4)。它的原理是刷盘与地面相对旋转,去除杂草。经验证,该除草机除草除草率高,刷盘转速与载具的行进速度对除草效果基本没有影响 [31]。
18、 图1-4 刷式株间除草机构 1.2.3 智能株间机械除草装置 图1-5展示了Hortibot带有视觉检测系统和GPS导航系统的株间除草载具人,实验表明这种除草载具人具有更好的操作效果[18]。 图1-5 智能型株间除草机器人 Blasco等人设计的一种用于蔬菜地的植物间除草平台(见图1-6),其中载具视觉系统可以在幼苗之间定为杂草信息,依靠机械手末端释放的高压来达到除草的目的[19]。 图1-6 智能化株间除草机 此外,现有的苗间除草装置根据其有无电源可分为主动除草装置和被动除草装置[20],被动除草装置主要包括弹性齿、指状和刷式除草装置,其结构如图1-7所示,该
19、类除草装置的作业原理是依靠被动旋转来除草[18]。 图1-7 现有除草机构类型 近年来,随着新的农业政策实施和全民环保意识的加强,机械除草已经逐渐被重视。对于机械除草装置,我国也进行了相关研究,尽管取得了不少成果。但是,还存在一些问题: 1)我国的机械除草装置的研究主要集中于行间除草,而对株间机械除草的研究,还是在模仿和改进他国的成果。 2)中国在质量大且粘性高的土壤条件下的农机研究比起国外已然落后。仅仅是修改了传递类型。除碎土率低以外,高运行功耗已成为除草机的主要制约因素。 35 2 技术任务书(JR) 2.1 设计依据 首先,传统的除草机虽可以消除行间杂草,但由于
20、杂草的幼苗与作物相似,故杂草幼苗难以清除;第二,在连续实施新政策后,土壤重量和粘度增加,现有的除草机在粘性土的条件下,存在除草、破碎土效果差、操作耗电等问题。因此,在重粘土条件下,设计和开发一种既能控制行间苗间杂草,又能同减少运行功率消耗的新型机械除草设备具有重要意义[18]。。本文在分析了现有的机械除草技术后,结合重且黏性高的土壤环境和垄作玉米的种植特点,设计了一种由回位弹簧、凸轮、摆杆、刀轴、除草刀、一级圆柱直齿轮减速器等部件组成的垄作玉米机械除草装置。在原有装置的基础上,在除草机上方增加了减速器,增加了除草机主轴获得的扭矩,与除草刀受到的力,以满足除草作业的要求。 2.2 产品的用途及
21、适用范围 本文设计的除草机适用于土壤环境具有粘性和重质转化的农村土地,尤其适用于播种后幼苗刚刚发育的时期,因为此时,幼苗的形状与杂草形状更为接近,除草机可以准确地切割杂草,避免幼苗受伤。这样,可以大大降低农村除草作业的强度,为农民节省时间。 2.3 主要技术参数 垄作玉米机械除草机构的主要技术参数如表2-1所示。 表2-1 主要技术参数 参数项目 参数 电动机功率(KW) 4.0 自重(kg) 29 凸轮摆杆长度(m) 64.47 凸轮最大摆角(rad) π/4 弹簧刚度(N/mm) 72 除草刀厚度(mm) 7.83 除草刀刀宽(mm) 106
22、 2.4 主要研究内容 本文拟设计一种垄作型玉米机械除草装置。具体内容包括: (1) 凸轮摇杆机构的设计,具体是对凸轮轮廓,凸轮摆杆,凸轮运动角的设计,先确定除草刀刀刃曲线并通过刀刃曲线设计凸轮的运动角,根据主动件与从动件的配合确定凸轮的运动规律,通过极坐标法确定凸轮摆杆长度。 (2) 除草刀的设计,具体为除草刀基本尺寸设计,除草刀刀刃曲线和轨迹的设计,根据玉米垄台的实际宽度和除草的覆盖率确定除草刀的基本尺寸,根据玉米苗的直径驱动除草刀的切刃曲线。 (3) 减速器的设计,具体为带轮,齿轮的设计,传动比的确定,电机的选择。 3 设计计算说明书(SS) 3.1 整机结构及工作原理
23、 3.1.1 整机结构 垄作玉米机械除草机构的整机结构如图3-1[18]所示。 图3-1 凸轮摇杆式摆动型玉米苗间除草机构 3.1.2 工作原理 工作时,秧苗之间的垄作型玉米机械除草装置与智能除草机相连,使两把除草刀分别为位于作物育苗带两侧的幼苗之间,用除草刀进行植株之间的除草操作时,随着载具向前移动,除草刀靠近幼苗,智能耕作机检测系统检测出幼苗并发送信号给单片机,单片机对信号进行处理后,向电机驱动器发出指令,电机开始转动。电机的转动带动除草机的主轴转动。主轴向一对啮合齿轮提供动力,齿轮下部是两个凸轮,两个凸轮分别推动其固定有除草刀轴的摆杆,此时除草刀成开背式,随载具移动避开幼苗
24、,在除草刀避开幼苗后,除草刀在拉伸弹簧张力的作用下返回原位,完成避苗运动。这一过程可作为除草装置的一个工作流程。 3.2 除草刀设计 3.2.1 除草刀基本尺寸设计 如图3-2[18]所示,本文所描述机构的除草刀的结构尺寸主要有刀宽L1,车削中心到刀尖的距离L2,与回转中心至刀背的距离L3组成。 图3-2 除草刀结构示意图 1.玉米幼苗 2.除草刀3.玉米垄作台 在影响除草效率的诸多因素中,除草刀的宽度占据着很重要的地位,刀宽过小会降低两幼苗间的杂草的覆盖率,使除草率降低;如果宽度太大,会增加能耗。经查证,L/2一般≤l1≤l,l为玉米的垄台宽度。我国的玉米垄台宽度的平均值在1
25、79mm左右,所以统计后取L1=0.6L=106mm。合理选择除草刀回转中心的位置,就可以大幅减小摆动过程中所受到的阻力力矩,而L/4 26、+Kθ) (3-1)
式中:
r—任意点极径,mm;
r0—起点极径,mm;
K—静态滑切角正切值与极径的比例系数[18];
θ—曲线上随机点的极角,rad[18];
根据文献[38],最终确定r0为118mm,K取0.78,除草刀厚度为7.83mm。
3.3 凸轮摇杆机构设计
本文拟用反转法设计凸轮,设计思路是根据作业需求,设计出符合实际需求的凸轮运动角,确定摆杆的最大位移;选择凸轮运动规律,确定凸轮机构基本参数,最后用反转法做出凸轮基本轮廓。
3.3.1 凸轮基本尺寸的设计
(1)凸轮机构运动角以及最大行程的确定
凸轮机构的运动角分别为远休止角和近休止角 27、,其中远休止角是指:从动件停留在距凸轮回转中心最远的位置不动,这时对应的凸轮运动角是远休止角。同理,从动件在距凸轮轴心最近处停止不动时对应的凸轮转角称为近休止角。两位置摆杆的夹角为从动件的最大摆角,结合实际情况可以看出,如果要在工作过程中完成避苗除草的任务,需要在避苗过程中,除草刀张开的最大距离L>保护区直径d,经查阅后[18],得d=62mm,故想要满足要求,则需L=d,故通过作图法可知,凸轮机构从动件的最大摆角为π/4。
根据除草的要求,除草刀的运动轨迹应为“菱形”,如图3-3所示,其轨迹可以分为以下三部分:BC段是当设备接收避苗指令时,除草刀处于开背状态。CD段是除草刀保持开背,装置避 28、开玉米幼苗的过程;DE段是装置避开玉米幼苗后除草刀回到原来位置的过程。由此可知,凸轮的运动也对应三个部分:推程、远休止和回程。为了减少在运行过程中凸轮受到的冲击,故需增加近休止段以减小加速度突变;因此,凸轮的运动角度为推程运动角∅,回程运动角∅',远休止角∅s,近休止角组成∅s',如图3-4所示。
图3-3 避苗运动轨迹
图3-4 凸轮工作段示意图
图3-3与图3-4相互对应,且有:
d2 29、角速度,rad/s[18];
SCD—凸轮处于远休止段时,除草刀前进的距离,m[18];
SBF、SEF—凸轮出去近休止段1/2时,除草刀前进的距离,m[18]。
联立式3-2,3-3可得,5π/24<∅s<3π/8,∅s'<∅s,凸轮工作时应注意以下几点:尽可能增加凸轮的推程范围,以确保除草刀能稳定的完成切割,凸轮从推程缓慢回程速度应该较低,这样可以保证除草刀完整的避开玉米幼苗:凸轮从回程到推程的速度应该较大,这样可以提高除草效率。故可知,在本文设计的机构中凸轮的近休止角是11π36,推程运动角为2π3,回程运动角为 2π3,远休止角为13π36。
3.3.2 凸轮运动规律选择
为 30、了减小凸轮和摆杆之间的刚性冲击和柔性冲击,故选取正弦加速度运动的基本运动规律作为凸轮的基本运动规律,摆杆位移计算公式为:
ψm=0 0≤Φ≤11π36 ψmΦ∅-sin2πΦ∅2π 11π36<Φ≤35π36 ψm 35π36<Φ≤59π36 ψm1-Φ∅'+sin2πΦ∅'2π 59π36<Φ≤2π (3-4)
式中:
Φ—凸轮运动角,rad[18];
ψ—凸轮机构摆角,rad[18]。
由此可得到凸轮的基本参数:基圆半径Rb, 31、中心距LOA,如图3-5所示。
图3-5 凸轮机构基本参数
经查阅资料[34]可知,机架长度计算公式为:
LOA=1.33Mrmax1+dψdΦLATMr+JAd2ψd∅2ω2cosψb+ψ2 (3-5)
式中:
Mr—摆杆运行载荷,N.M;
JA—摆杆转动惯量;kg/m2。
LAT—摆杆回转中心与凸轮切点之间的距离;mm。
为保证凸轮运转时不出现失真现象,可以将先前的数据带入式3-5可得,LOA=63.37mm。根据参考文献[],本文取凸轮基圆半径Rb=36.73mm。
3.3.3 摆杆长度设计
要测定摆杆长度,则必须先得出基圆摆角:
ψb=arcsinRb 32、LOA (3-6)
由文献[34]可知,凸轮摆杆机构需满足最小杆长条件
Lmin=maxLOAcos(ψb+ψ)1+dψd∅-minLOAcos(ψb+ψ)1+dψd∅ (3-7)
式中:
LOA—机架与凸轮回转中心的距离,mm;
ψb—基圆摆角,rad;
ψ—凸轮摆角,rad。
且摆杆边缘点到凸轮回转中心的距离也有
Rmax=maxLOAcos(ψb+ψ)1+dψd∅ (3-8)
将以得出的数据带入公式3-7,3-8,即可得出,凸轮的最小杆长应该是64.47mm。
3.3.4 凸轮机构轮廓曲线的设计
凸轮为对心摆动凸轮, 33、且在3.3.1.2中已确定了从动件的运动规律以及凸轮的远近休止角,故可有摆角-位移曲线图,根据曲线图(图3-6),可利用反转法描出凸轮轮廓曲线。
图3-6 摆角-位移曲线图
最终可得凸轮的基本轮廓如图(3-7)所示。
3.4 除草刀受力分析及弹簧参数确定
3.4.1 除草刀的运动分析
在避开玉米幼苗的过程中,除草刀的运动主要是从开背位置开始。割草机的开刀,回刀运动随载具向前移动而进行,并同时将除草刀绕自身的刀轴顺时针旋转。将除草刀跨过玉米幼苗的运动过程视为具有均匀速度的直线运动。选择除草刀上离刀轴距离最远的点E作为参照物 ,以除草刀的回转中心(即刀轴的位置)为原点,智能耕耘机 34、的前进方向为Y轴的正方向。在运动过程中,除草刀有三个动作,以避免玉米幼苗受到伤害,刀尖E点的轨迹方程可看作由三部分组成,分别为:
开背过程:
y=v0t-ρsin(θ0+ω1t)x=-ρcosθ0+ω1t (3-9 )
跨过玉米幼苗过程:
y=v0t+s0-ρsinθx=-ρsinθ0 (3-10)
回刀过程:
y=s1+s0-ρsinθ1+v0t+ρ(sinθ1-ω1t)x=-ρcosθ1-ω1t 35、 (3-11)
式中:
ρ—E点极径,m;
θ0—E点与原点的连线与 Y轴正方向的初位置夹角,rad;
θ1—E点的极径与Y轴正方向的最大角,rad;
ω1—除草刀的旋转角速度,rad/s;
s0—从初始位置到完全张开过程中,除草刀转动中心的位移,mm;
s1—除草刀跨过幼苗时,除草刀回转中心的位移,mm;
t—时间,s。
从3-9,3-10,3-11可得,可从3-9,3-10,3-11开始,在除草刀的避苗过程中,应根据载具的速度,除草刀角速度和除草刀形状来确认刀尖E点的轨迹。当除草刀切刃曲线确定时,载具的前进速度和除草刀的转速都会改变智能耕耘机的刀刃切割路线,这可以 36、降低杂草不被切割的可能性。由于3-9,3-10,3-11均为与位移相关的公式,则三个公式分别对时间求导即可得到除草刀E点的速度,其中:
v1=v02+ρ2ω12-2ρω1v0cosθ0+ω1tv2=v0v3=v02+ρ2ω12-2ρω1v0cosθ0-ω1t (3-12)
式中:
v1—除草刀开背时,刀尖E点速度,m/s;
v2—除草刀跨苗时,刀尖E点速度,m/s;
v3—除草刀回位时,刀尖E点速度,m/s。
由文献[35]可知,除草刀本身的切割速度要想达到较低的伤苗率,其速度不应超过3.9m/s[35],其载体的移动速度则应处于0.75~1.0m/s,ρ取0.07m,此时与 37、Y轴正方向的夹角θ0为11π/180,且与Y轴的最大夹角θ1为13π/45,将ρ,θ0,θ1带入式3-12,可得智能中耕机的刀轴的转速为2.2~2.5r/s。
3.4.2 除草刀受力分析及弹簧参数
弹簧是除草刀回位时的主要工具,其参数对除草刀回位时的状态有很大影响,故由如图11受力分析:
由图可知,弹簧会提供一个力矩Q来使除草刀回到初始位置,则弹簧力矩的表达式为:
Q=k∆ylb (3-13)
式中:
k—弹簧刚度;
∆y—弹簧形变量,mm;
lb—摆杆长度,mm。
Qf是除草刀工作时收到的阻力力矩,经查阅得Qf=pd,其中p为其阻力,d为施加力的力臂长度:由于在实际 38、工作情况中,影响除草刀阻力的因素很多,因此,根据[36,37]得,可在一般环境中忽略一些阻力的影响因素,则有:
p=fG+abμ+εv02 (3-14)
式中:
f——除草刀与土壤的摩擦因数;
G——单个除草刀所受重力,F;
a——深度,m;
b——宽度,m;
μ——静态阻力系数;
ε——动态阻力系数。
若要及时将影响返回到原来的位置,则须弹簧提供的回位力矩大于回位时除草刀收到的阻力力矩,即:
Q≥Qf (3-15)
式中:
Q—弹簧提供的回位力矩,N.m;
Qf—阻力力矩,N.m。
将3 39、-13,3-14,3-15联立可得出的新式为:
k≥fG+abμ+εv02d∆yLb (3-16)
经查阅可以发现,在除草机的结构设计中,弹簧形变量取∆y∈0,46mm,f∈[0.33,0.61],故本文取0.4,经过验证,近年来我国粘重土壤的静态阻力系数μ为38000N/m2,动态阻力系数ε为3800N·s2/m4,深度a取0.013m,宽度b为0.11m,单个除草刀所受重力为380N,lb取0.063m,力臂长度d取0.01m,v0取0.6 m/s将以上数据带入3-16,可得出弹簧的刚度为72N/mm,经查证,得出材料选用65Mn,弹簧直径选择25mm,弹簧匝数为15。
3. 40、4.3 齿轮轴及齿轮设计
表 3-1 齿轮具体参数
参数
参数
齿数(大)
83
齿数(小)
17
分度圆直径(大)(mm)
83
分度圆直径(小)(mm)
17
模数
1
压力角(°)
20
齿宽(mm)
15
齿顶高(mm)
1
齿根高(mm)
1.25
齿全高(mm)
2.25
基圆直径(大)(mm)
78
基圆直径(小)(mm)
16
齿顶圆直径(大)(mm)
85
齿顶圆直径(小)(mm)
19
齿根圆直径(大)(mm)
80.5
齿顶圆直径(小)(mm)
14.5 41、
齿距(mm)
3.14
齿厚(mm)
1.57
中心距(mm)
50
经过之前的计算,除草刀转速是已知的,经查阅资料[18]后,电机选择4对级电机(Y100L-8),电机转速740r/min,需要转速在130~160r/min之间,则传动比暂取i=5:1,转速为148r/min,符合要求。
摇杆的旋转轴间距为140mm,凸轮的旋转轴与摇杆的转轴距离为L=63.37mm。两大齿轮之间距离在20~140mm之间选择,为防止齿轮发生根切,齿轮齿数z≧17。考虑到凸轮基圆Rb=36.73mm,假设当其与摇杆相切时为摇杆为竖直状态,此时两轴之间的距离为66mm,取模数为m=1,压力 42、角α=20°,大齿轮齿数Z1=66,小齿轮齿数为Z2=13.2,显然小于17,取小齿轮为Z1=17,大齿轮为Z2=85。中心距为a=51mm,该中心距非标准中心距,更改中心距为a=50mm,小齿轮齿数Z1=17,得Z2=83,得到减速比i=4.88,计算出转速为n=151.6r/min,满足要求。及得到齿轮的具体数据如表3-1所示。
对于该小齿轮的设计,考虑到小齿轮分度圆直径d1=17mm,为极小值,故把小齿轮做成齿轮轴,依具两固定板之间的距离确定的各位置直径和长度如下图3-7所示:
图3-7 各位置直径和长度
大齿轮设计,轴径选择Φ15方便加工和制作,键槽选择A4X8对应的键槽 43、深度和宽度即可。
对于小齿轮轴的设计,考虑到小齿轮分度圆直径d0=17mm,为最小值,故把小齿轮做成齿轮轴。材料可选择40Gr,表面选择调质处理,提高硬度,耐磨性好,不容易发生断裂。得P=0.7125kw,n=750r/min。A=110,且:
dmin≥A3Pn (3-17)
式中:
dmin——轴的最小值,mm;
A——系数;
P——电动机功率,W。
得dmin≧9.6mm,无键设计,取最小可配标准轴承d1=10mm,则d1=10mm,LⅠ-LⅡ 44、=10mm,轴肩d2应在10~17mm之间,取d2=13mm,考虑两板之间距离,取LⅡ-LⅢ=40mm,小齿轮厚度为L0=15mm,分度圆直径d0=17mm。第三段为d3=13mm,LⅢ-LⅣ=9mm。第四段与轴承配合得d4=10mm,LⅣ-LⅤ=26mm。
3.4.4齿轮轴强度校核
轴所受扭矩为T=9.55×P/n=9072.5N·mm,d0=17mm,得圆周力为Ft=2Mtd =1067.4N,径向力Fr=Ft×tan20°=388.5N,合力F1=1135.9N。一端轴承支承反力F2=812.5最大弯矩M1=F2×20.5mm=16656.2N·mm,T=9072.5N·mm,由
45、σca=M12+αT20.1d3 (3-18)
式中:
σca——轴的计算应力,MPa;
M1——轴所受的弯矩,N∙mm;
α——折合系数;
T——轴所受扭矩,N∙mm。
带入数据,得σca=35MPa<60MPa。故强度合格。大小齿轮均可选择45钢,表面选择渗碳处理,提高硬度,耐磨性好,不容易发生断裂。
3.5 减速器设计
3.5.1 拟定减速器传动方案
经过前面四个小节的运算,可以看出,除草刀的转速为2.2~2.5r/s,得到除草机构中凸 46、轮的基本轮廓,由参考文献[18]可得,选用功率为4kw,电动机的额定转速约为47r/s,可提供的转矩为15N∙m,因此,要估算总传动比的范围,以便选择合适的传动机构和传动方案,可先计算出驱动卷筒的转速Nw,即:
v=1.1ms,D=350mm
Nw=60×1000×v/(π×D)=60.0241r/min (3-19)
式中:
Nw——卷筒转速,rad/s;
v——卷筒线速度,m/s;
D——卷筒直径,mm。
故选择同步转速(Nw)为1500r/min的电动机作为动力源,故总传动比为 25。
3.5.2 减速器电动机 47、选择
(1)电动机类型和结构形式
经验证,选用Y100L-8系列电动机,卧式全自动封闭结构。
(2)电动机容量
卷筒轴的输出功率Pw
F=2800r/min
PW=F×v1000= 3.08kw (3-20)
式中:
F—卷筒轴转速,r/min;
v—卷筒轴线速度,m/s。
电动机输出功率Pd
Pd=Pwt,t=t1×t22×t3×t4×t5 (3-21)
式中:
Pw—卷筒轴的输出功率,W;
Pd —电动机的输出功率,W。
t—传动总效 48、率。
式中,t1,t2,…为从电动机到卷筒之间的各部分的效率。经查表可得:
表3-1
名称
数量
效率(%)
弹性联轴器
1个
t4=0.99
滚动轴承
2对
t2=0.99
圆柱齿轮闭式
1对
t3=0.97
V带开式传动
1幅
t1=0.95
卷筒轴滑动轴承(润滑良好)
1对
t5=0.98
则将上述数值带入式3-21可得t=0.8762 , Pd=PWt=3.515
电动机额定功率Ped
由参考文献[18]可知,带动除草机构的电动机的额定功率为Ped=4KW。
(3)电动机的转速
为了便于选择电源电压,需要先估算电动机转速的 49、范围。查表后可得,V型带传动传动比范围一般为2~4,单级圆柱齿轮传动比范围一般为3~6,则可选电动机的最大,最小转速分别为:
Nmin=Nw×6=360.1449r/min
Nmax=Nw×24=1440.6 r/min (3-22)
式中:
Nw—驱动卷筒转速,rad/s;
Nmin—电动机最小转速,rad/s;
Nmax—电动机最大转速,rad/s。
故同步转速为960r/min,选定电动机型号为Y100L-8。
(4)电动机的技术数据 50、由查表可得,Y100L-8型电动机的技术数据如表3-2所示。
表3-2
电机型号
额定功率
同步转速
满载转速
电机质量
轴颈mm
Y100L-8
4KW
960
1000
73
28
且查表得,大齿轮数z1与小齿轮数齿数z2之比为z1z2=10119=5.3158
3.5.3 计算传动装置总传动比和分配各级传动比
(1)传动装置总传动比
Nm=960r/min:
i=NmNw =96060.0241=15.9936 (3-23)
式中 51、:
Nm—同步转速;rad/min。
(2)分配各级传动比
取V带传动比i1=3,则单级圆柱齿轮减速比为:
i2=ii1 =15.99363=5.3312 (3-24)
式中:
i1 —V带传动比;
i2—单级圆柱齿轮减速比。
所得i2值符合圆柱齿轮和单级圆柱齿轮减速器传动比的常用范围。
3.5.4 计算减速器传动装置的运动和动力参数
(1)各轴转速
电动机轴为0轴,减速器高速轴为Ⅰ轴,低速轴为Ⅱ轴,各轴转速为:
n0=nm
n1=N0i1 =60.02413=320r/min
n2=n1i2=3 52、205.3312=60.0241r/min (3-25)
式中:
n0 —电动机转速,rad/s;
n1 —高速轴转速,rad/s;
n2 —低速轴转速,rad/s。
(2)各轴输入功率
按输出功率Pd计算各轴输入功率,即P0=Ped=4kw ,轴I的功率,轴II功率分别为:
P1= P0×t1=3.8kw
P2=P1×t1×t2=3.6491kw 53、 (3-26)
式中:
P0 —电动机功率,W;
P1 —轴I的功率,W;
P2 —轴II功率,W;
t1 —V带开式传动的传动效率;
t2 —滚动轴承传动效率;
t3 —圆柱齿轮闭式的传动效率。
(3)各轴转矩
T0=9550×P0n0 =39.7917 Nm
T1=9550×P1n1 =113.4063Nm
T2=9550×P2n2 =580.5878 Nm (3-27)
式中:
T0 —电动机转矩,Nm;
T1 —轴I转矩,Nm;
T2 54、—轴II转矩,Nm。
3.5.5 带轮设计
(1)功率计算
P=Ped=4Kw,一班制工作8小时,载荷平稳,原动机为笼型交流电动机经查表可得KA=1.1;
计算其功率为:
Pc=KA×P=4.4kw (3-28)
式中:
Pc—带轮工作功率,W;
P—电动机功率,W。
(2)选择普通V带型号
n0 =960r/min,根据Pc=4.4Kw,n0=960r/min,由参考资料[39]查得坐标点位于A点,则d1=80~100
(3)确定带轮的基本直径
查表得小轮直径为d1=100m 55、m大轮直径d2= d1×3.5=350mm故取标准件,则由d2=355mm。
(4)验算带速
验算带速得:
v=πd1n060000 (3-29)
式中:
d1——小轮直径,mm;
n0——电动机轴转速,rad/s。
从动轮转速
n22=n0×d1d2=270.4225rad/s
n21=n03.5=274.2857rad/s
从动轮转速误差为n22-n21n21=-0.0141
(5)V带基准长度和中心距
计算中心距
中心距的范围为:
amin=0.75×d1+d2=341.25mm
amax=0.8×d1+d2=364mm 56、
a0=350mm
计算带长
Lc=2×a0+πd1+d22+d2-d124a0=1461.2mm (3-30)
式中:
d1—小轮直径,mm;
d2—大轮直径,mm;
Lc—传动带长度,mm。
选定带的基准长度
根据参考文献[40]可得基准长度Ld=1600mm;
定中心距
a0+Ld-Lc2=419.4206mm≈420mm (3-30)
amin=a-0.015×Ld=396mm,amax=a+0.03Ld=468mm (3-31)
式中:
a0——中心距,mm;
57、amin——最小中心距,mm;
amax——最大中心距,mm。
(6)验算小带轮包角
验算包角
α1=180-d2-d1×57.3a=145.2107>120 (3-31)
故根据文献查阅可得,包角合格。
(7)求V带根数
根据之前算出的数据可得n1=960r/min,d1=120mm,查表可得P0=0.95
传动比i=d2d11+0.0141 =3.5,∆P0=0.05,且已知包角等于145.21°故可由查表得Ka=0.92,KL=0.99
故V带的根数为:z=4.40.92×0.99=3根
(8)计算作用在带上的压力
经查表可得,单根V带的初 58、始压力为:
FQ=500pczv2.5Kα-1+qv2 (3-32)
式中:
FQ——单根V带的初始压力,F;
z——V带的数量。
3.5.6 减速器轴的设计
初做轴直径:
(3-33)
式中:
d——轴的直径,mm;
c——系数;
P——轴传递的功率,W。
轴I和轴II选用45#钢,c=110,d1=110×133.8/320=25.096mm,取d1=28mm
d2=110× 59、133.65/60=43.262mm,由于d2与联轴器联接,且联轴器为标准件,由轴II扭矩,查表可知,取YL10YLd10联轴器,又由于Tn=630>580.5878Nm ,轴II直径与联轴器内孔一致,取d2=45mm
3.5.7 减速器齿轮设计
(1)齿轮强度计算
由n2=320r/min,P=3.8Kw,i=3可知,采用软齿面,小齿轮40MnB调质,齿面硬度为260HBS,大齿轮用ZG35SiMn调质齿面硬度为225HBS。因σHlim1=700MPa,σHlim2=540MPa
SH1= 60、1.1, SH2=1.1
σH1=σH1lim1SH1=636MPa
σH2=σH2lim21.1=491MPa (3-34)
式中:
SH1——小齿轮许用应力,MPa;
SH2——大齿轮许用应力,MPa;
σH1 ——小齿轮接触应力,MPa;
σH2 ——大齿轮接触应力,MPa。
因:σFlim1=240MPa,σFlim2=180MPa,SF=1.3
σF1=σFlim1SF=185MPa
61、 σF2=σFlim2SF =138MPa (3-35)
式中:
σF1 ——小齿轮弯曲应力,MPa;
σF2 ——大齿轮弯曲应力,MPa。
(2)设计接触强度设
经查证,取载荷系数K=1.5,齿宽系数σa=0.4则小齿轮上的转矩为:
T1=9550×PN=113.4063Nm
a≥μ±13335σH2KT1φa (3-36)
式中:
a——中心距,mm;
K——载荷系数;
T1——小齿轮转矩,N.m;
μ——大小齿 62、轮齿数比。
则有u=i=5.333,代入数据得:中心距a为124.2331mm,齿数z1=19,则z2=z1×5.333=101,模数m=2az1+z2=2.0667取模数m=2.5,确定中心矩a=mz1+z22 =150mm,齿宽b=φa×a=60mm,b1=70mm,b2=60mm。
(3)验算弯曲强度
齿形系数YF1=2.57,YF2=2.18,根据参考文献可知,轮齿弯曲强度:
σF1=2KT1×YF1bm2z1=122.7KN<σF1P
σF2=122.7×2.182.57=104.9KN<σF2P (3-37)
( 63、4)齿轮圆周速度
v=πd1n160×1000=0.7955<3m/s (3-38)
式中:
v—齿轮圆周速度,m/s;
σF1—小齿轮轮齿弯曲强度,KN ;
σF2—大齿轮轮齿弯曲强度,KN。
按参考文献应选9做精度,与初选一致。
3.5.8 减速器轴校核
圆周力Ft=2T/d1,径向力Fr=Ft*tan,已知=20度为标准压力角d=mz=252.5mm,Ft=2T/d1=5852.5N,Fr=5852.5×tan20=2031.9N
(1)求垂直面的支承力Fr1,Fr2
由:
Fr2×L-Fr×L2=0 64、 (3-39)
式中:
Fr1—小直径轴垂直面支承力,F;
Fr2—大直径轴垂直面支承力,F;
L—力臂长度,m。
得Fr2=Fr/2=1015.9N
(2)求水平平面的支承力
FH1=FH2=Ft2=2791.2N (3-40)
式中:
FH1—小直径轴水平平面的支承力,F;
FH2—大直径轴水平平面的支承力,F。
Ft—圆周力,F。
(3)求垂直面弯矩
L=20+20+9 65、0+10=140mm
Mav=Fr2×L2=71.11Nm (3-41)
式中:
Mav—垂直面弯矩,Nmm。
(4)求水平面弯矩
MaH=FH×L2=195.384Nm (3-42)
式中:
MaH—水平面弯矩,Nmm。
(5)求合成弯矩
Ma=Mav2+Mah2=216.16Nm (3-43)
式中:
Ma—总弯矩,Nmm。 66、
(6)求轴传递转矩
T=Ft×d2/2=2791.2×2.5×101/2=352.389Nm (3-44)
式中:
T—轴的传递转矩,Nmm;
Ft—圆周力,F;
d2—小圆直径,mm。
(7)求危险截面的当量弯矩
从图可见a-a截面是最危险截面,其当量弯矩为
(3-45)
式中:
Me—当量弯矩,Nm;
Ma—轴所受弯矩,Nm;
a—折合系数;
T—转矩,Nm。
轴的扭切应力是脉动循环应力,取折合系数a=0.6代入上式可得。
(8)计算危险截面处轴的直径
轴的材料,用45#钢,调质处理,由表14-1查得σb=650MPa,由表13-3查得许用弯曲应力,所以
d≥3Me0.1×σ-1b=25.40mm (3-46)
式中:
d——轴的最小危险直径,
- 温馨提示:
1: 本站所有资源如无特殊说明,都需要本地电脑安装OFFICE2007和PDF阅读器。图纸软件为CAD,CAXA,PROE,UG,SolidWorks等.压缩文件请下载最新的WinRAR软件解压。
2: 本站的文档不包含任何第三方提供的附件图纸等,如果需要附件,请联系上传者。文件的所有权益归上传用户所有。
3.本站RAR压缩包中若带图纸,网页内容里面会有图纸预览,若没有图纸预览就没有图纸。
4. 未经权益所有人同意不得将文件中的内容挪作商业或盈利用途。
5. 装配图网仅提供信息存储空间,仅对用户上传内容的表现方式做保护处理,对用户上传分享的文档内容本身不做任何修改或编辑,并不能对任何下载内容负责。
6. 下载文件中如有侵权或不适当内容,请与我们联系,我们立即纠正。
7. 本站不保证下载资源的准确性、安全性和完整性, 同时也不承担用户因使用这些下载资源对自己和他人造成任何形式的伤害或损失。
最新文档
- 2025年水电工程运行维护管理合同示范文本.docx
- 2025年工程勘测设计合同模板.docx
- 2025年区域产品销售代理合同.docx
- 2025年经销商授权合同样本.docx
- 2025年员工住房资金借贷合同.docx
- 2025年轻钢建筑施工合同示例.docx
- 2025年网络推广托管合同.docx
- 2025年简明个人借款正式合同范例.docx
- 2025年房产按揭贷款合同范例.docx
- 2025年技术合同争议调解.docx
- 2025年电子版城市住宅租赁合同范本.docx
- 2025年简易转让合同协议书样本.docx
- 2025年投资顾问服务合同实例.docx
- 2025年经销合同模板.docx
- 2025年工业项目设计合同样本.docx